SMART MANUFACTURING, THE REVOLUTION IS ON
The rise of Industry 4.0 has represented a real revolution for the global production system. The increasingly decisive presence of automation systems – designed to allow an increase in production and a simultaneous improvement in work conditions – has transformed the industrial world and the way we think about the entire production system. In many cases, and following a strong and steadily increasing trend, the manufacturing plants of the recent past have given way to smart factories, characterized by new technologies that bring together people, machines and tools, playing a crucial role for sustainability. Digitalization is certainly a central element in this constantly and rapidly evolving context, because it offers the supply chain a strong opportunity for evolution in terms of speed, scalability, AI, cloud, connectivity and interconnection. In recent years, a real ecosystem has been forming in which – precisely through innovative IT and technological tools – each player in the process is connected to the other in an integrated, flexible and dynamic way. Thanks to digital technologies, we are witnessing greater integration between the systems in suppliers’ and in clients’ companies, leading to improvements in processes and products to better respond to new needs expressed by the market. Also in terms of sustainability: today’s supply chain considers attention to sustainability – both environmental and economic – as one of its key factors. It is also (if not above all) by optimizing the management of these processes that we can win the challenges posed by the current competitive scenario.
THE SUPPLY CHAIN IN THE CURRENT CONTEXT
Today, the supply chain is a complex and articulated system that differs substantially from the supply chain model that could be observed only a decade ago. Although the new paradigm is based on greater sustainability, as well as flexibility and agility of the actors involved, we are far from striking out the risk that the mechanism will suffer major setbacks. In the past two years, first with the pandemic and then with the war casting its shadow over the whole world, we have exposed the vulnerability and the delicate balance in which manufacturing industries and the production sector in general operate today. Current conditions are bringing out, in some cases with dramatic clarity, the importance of developing strategic and technological solutions that allow today’s and tomorrow’s industries to overcome obstacles in an increasingly effective, rapid and sustainable way. For businesses, any interruption or slowdown in the production flow represents a major critical issue: the scarcity and cost of raw materials, logistical problems, and the absence of systems capable of connecting suppliers and customers in a fluid and efficient way are only some of the most critical factors to be addressed now and probably also in the coming years. By taking on an even more general perspective, we can see how the climate crisis, cyber threats and geopolitical tensions are creating a context in which it is extremely important to design solutions capable of ensuring that companies have the greatest possible solidity.
FROM CHAIN TO NETWORK: A SHIFT IN PERSPECTIVE
Looking at the current scenario, it is clear that the term “supply chain” – introduced by British manager Keith Oliver more than 40 years ago – has given way to a new paradigm. While the supply chain made linearity its conceptual cornerstone, today we are witnessing a more complex system in which individual players are connected in a branched and widespread network. In this sense, it would be more correct to speak of a “supply network”: a dynamic and flexible system that requires a profound rethinking of the logic underlying its correct functioning. In this new model, software plays perhaps the most decisive role. It is through advanced and constantly evolving software that it is possible to efficiently manage the huge amount of data that allows the entire network to function and meet the needs of an increasingly demanding market in terms of speed, efficiency and safety. In this context, sustainability represents one of the key factors of the modern supply chain. To meet this need, companies must equip themselves with specific tools to establish their presence within the new competitive scenario, also through the adoption of more sustainable practices and technologies that help make the entire supply chain lighter and more environmentally aware.
PREDICTIVITY AND RESILIENCE
The first step in limiting the risk factors that undermine the correct flow of new supply chains is to implement tools capable of predicting the risks themselves. Obviously, greater predictive capacity offers businesses the opportunity of avoiding dangerous and costly interruptions, starting from the production phase. Given the number of factors that come into play during this phase and the complexity of the overall context, it is essential to invest in cutting-edge software that is able not only to foresee any problems, but also to provide for their resolution. There is a lot of room for improvement in this field and it is generally accepted that predictivity is one of the issues on which all industrial organizations that strive to lead the near future will focus their efforts. Companies will increasingly need to create management infrastructures capable of guiding a proactive response to these risks. These responses could include structural changes to the supply chain, as well as the development of detailed contingency plans for exceptional high-risk events. The introduction of resilience metrics among the supply chain’s KPIs, for example, will help industries ensure the proper functioning of their supply chains by increasing efficiency and decreasing vulnerabilities. In this sense, resilience will be one of the core values for the industry of the future. The ability to adapt quickly and effectively to critical issues is a key to success for any productive business. In summary, the more companies will be able to predict risks, the more they will also be capable of designing solutions to overcome them.
THE CLOUD
Digitalization and the strengthening of IT tools play a leading role within the smart factory model. In particular, the cloud represents a crucial element to strategically manage the production and logistics chain and integrate all the steps necessary for process optimization. In recent years and at increasing speed, the cloud is becoming the ideal tool to meet the challenges of the industry of the future. While a significant share of services continues to be located in traditional data processing centers, more and more companies rely on cloud technology to manage most of their services. There are many advantages that make the cloud a tool destined to play a decisive role for the industries of the future, and the search for increasingly advanced solutions for its development is constant. The cloud favors speed, agility and scalability, and helps reduce production times and costs, also with a view to reducing waste during processing. The cloud makes companies more connected both internally and towards their suppliers and clients, and is a key ally to designing, manufacturing, and providing customized products and services, thus helping to increase customer loyalty.
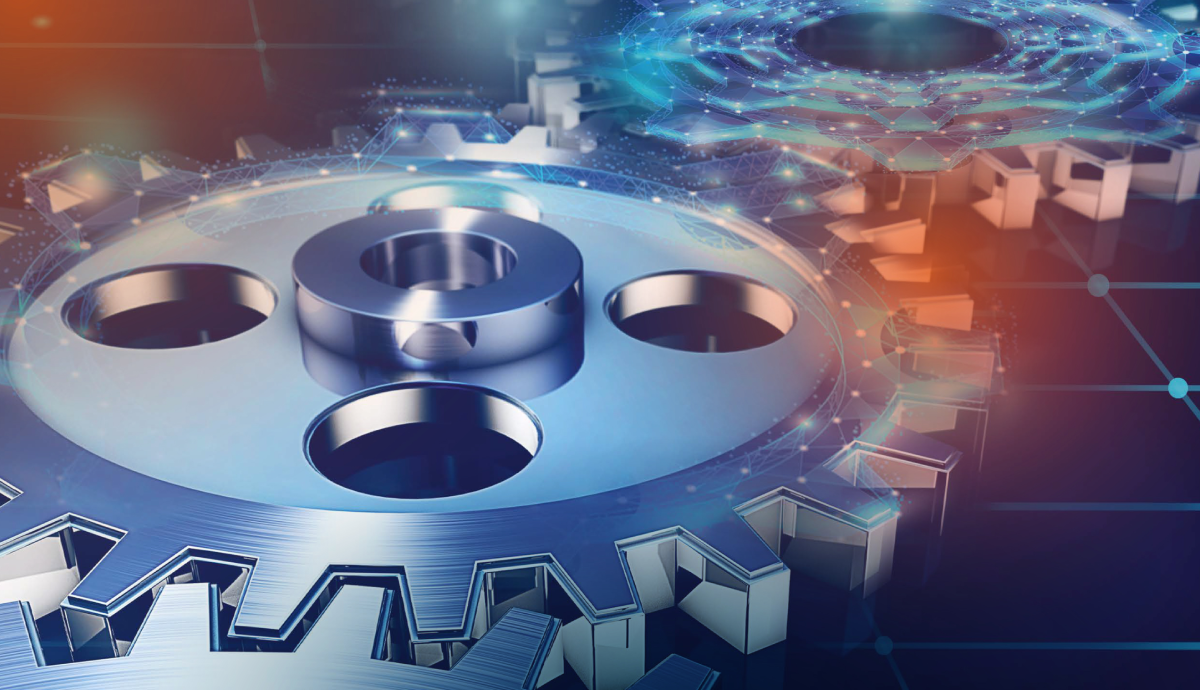
AUTOMATION AND FLEXIBILITY
Automation continues to play a central role for the industry of the future: it is thanks to automation that companies can operateminimizing errors, optimizing time and improving the quality of work for the people involved in the production process. Automation also allows for the identification and consequent resolution of critical issues, avoiding “bottlenecks”, delays and interruptions that undermine overall efficiency. While traditional supply chains aimed at achieving
stability, reliability and cost reduction, today’s model will have to be much more dynamic, agile and integrated. The ability to predict, process and respond to new market needs will play a large part in the success of any company in the ever-evolving manufacturing industry.
GRADUAL, NOT RADICAL CHANGE
It takes time to accomplish any great transformation. And only a strategic and integrated approach can truly change a process as complex as the one underlying the supply chain. Resilience, agility, flexibility are the cornerstones of a paradigm shift that is bound to affect the entire manufacturing industry sector and beyond in the coming years. Digitalization will increasingly be at the center of this transformation, but the vision of the people called to decide on the strategies to be adopted will be the factor playing the most important role. Targeted investments, careful business planning and the implementation of software solutions that can also be adapted to pre-existing management systems will allow companies to establish themselves in an increasingly global and challenging scenario. The answer for them will not be in drastic and radical changes in the supply chain, but rather in a gradual journey that, step by step, aims to achieve important goals for the future, without jeopardizing present productivity.