SUSTAINABILITY: MORE THAN JUST A WORD
In this age of remarkable social and economic changes, one word dominates the global debate as well as the ongoing reflections by individuals, businesses and institutions: sustainability. A shared process is engaging, for different reasons, a wide range of players in the name of the same objective: to find the useful solutions we need, to guarantee a more equitable and sustainable progress. This is especially true in the manufacturing industry, which is one of the sectors most often tasked with finding effective ways to continue to ensure certain goods and services while, at the same time, avoiding harmful impacts on the environment. However, if we don’t stop to think about the complexities embedded in the very concept of sustainability, we risk suggesting easy fixes that merely cover up the problem, and do nothing but give the appearance of sustainability. The issue is so important and the dangers we face in environmental and economic terms are so great, that we must analyze with clarity the definition of sustainability. It is only by facing the issue with a practical and sensible approach that we can win this challenge in an effective and timely way.
SUSTAINABILITY AND MANUFACTURING: AN INDISSOLUBLE PAIR
“Sustainable development is not a fixed state of harmony, but rather a process of change in which the exploitation of resources, the direction of investments, the orientation of technological development, and institutional change are made consistent with future as well as present needs.”
This definition may sound perfectly current, yet is taken from the Brundtland Report presented as far back as 1987 by the World Commission on Environment and Development. Talking about sustainable development helps us highlight the key aspect in question: there can be no authentic sustainability, if we don’t consider productive activities, economic development and growth. Therefore, sustainability can exist only if it is able to ensure the needs of the present generation are met without compromising the possibility of future generations to meet their own. Excluding the issue of economic sustainability from the debate turns a just cause into a lost cause.
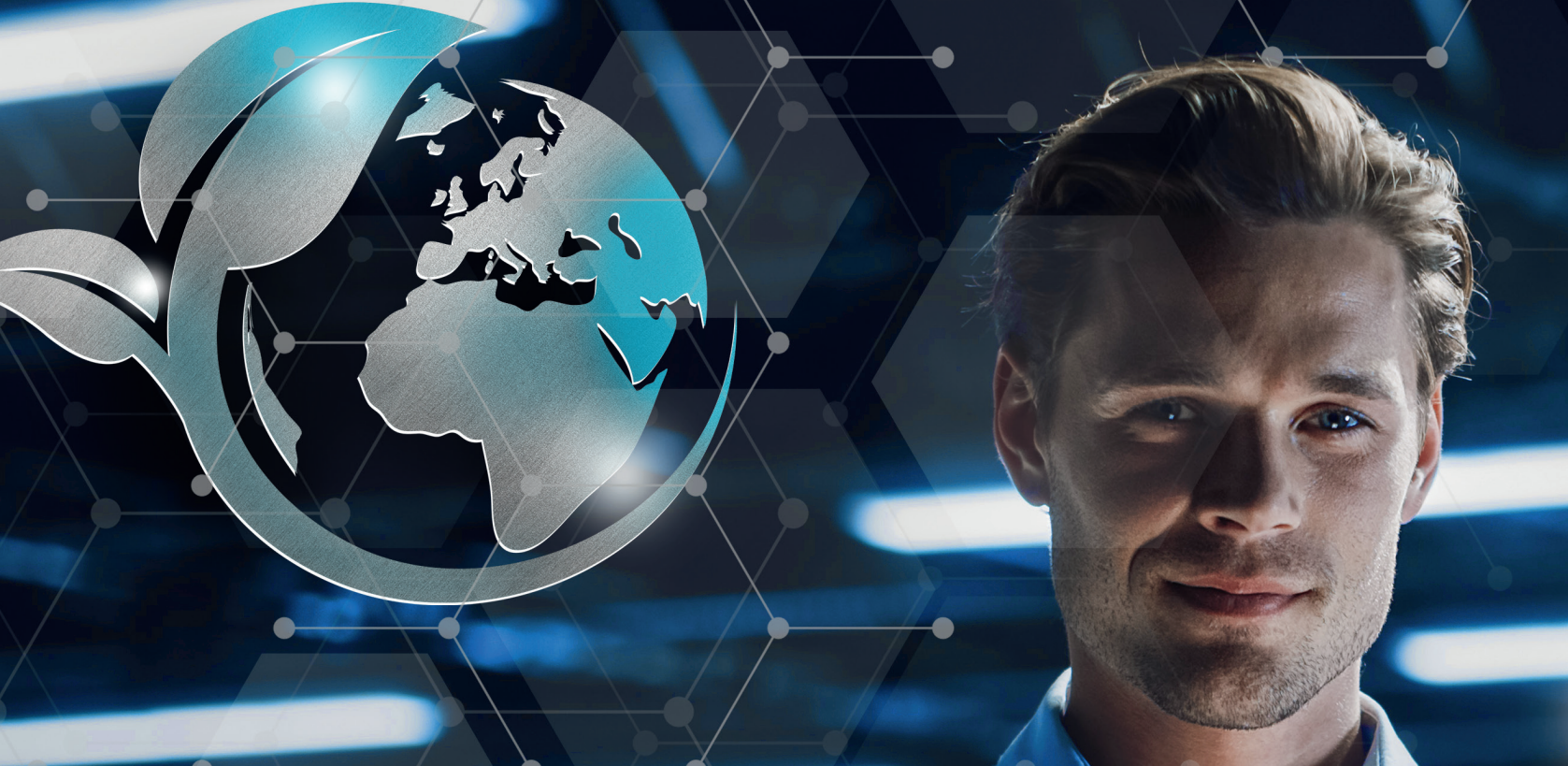
SUSTAINABLE MANUFACTURING MAKES BUSINESS SENSE
The answer to what may seem like an impossible dilemma lies in the concept of sustainable manufacturing that has emerged in recent years: a type of production capable of creating products through sustainable economic processes which – thanks to research and technological innovation – are able to minimize negative environmental impacts and allow for savings in terms of both energy and raw materials. Sustainable manufacturing is characterized by a pragmatic and willing approach to do its part, proving strong awareness for environmental issues. Indeed, by investing in scientific and technological research, it strives to come up with solutions designed to optimize production cycles by focusing on process efficiency, with the aim of saving materials and energy without affecting the quality of the final output. In line with a win-win logic, it simultaneously guarantees both a lower environmental impact and a saving of resources, which in turn lead to economic savings for manufacturers. A business that strives for sustainability cannot forget the people it interacts with, both within and beyond the company. A sustainable organization will have to make all the supply, installation, assistance and consultancy actions it offers efficient and smart. Intelligent machines, linear processes, easy-to-use software, ergonomic workstations, intuitive and user-friendly interfaces are essential tools for workers’ health and psychological and physical wellbeing, while providing a more efficient and cost-effective production.
AN ACHIEVABLE GOAL
Manufacturing is one of the most energy-intensive industries and has one of the biggest impacts on the environment. Therefore, we must design and implement solutions that minimize energy impact without a decrease in production standards. Planning and optimizing processes throughout the entire production chain is crucial to achieving this goal. Performing testing phases and feasibility estimates in a virtual mode, thanks to digital twins, in order to go from design to finished piece without wasting energy and materials; constantly monitoring the various production phases to promptly correct any errors; designing simple machines made up of the fewest possible components: these are some of the practices that allow for a tangible and substantial saving of time and lower waste of material. In a nutshell, they save energy and therefore save money. One of the most efficient solutions for the optimization of production processes is the creation of systems, where several machines, each with a specific function, integrate into automated production lines to obtain the desired result by minimizing waste of material and energy. Solutions that are flexible and agile make a crucial contribution to eliminating the risk of so-called system redundancy, i.e. the overlapping of production phases that is one of the most frequent problems in the manufacturing sector. The general trend is to implement so-called energy minimalism, i.e. to try to obtain maximum production with minimum energy expenditure.
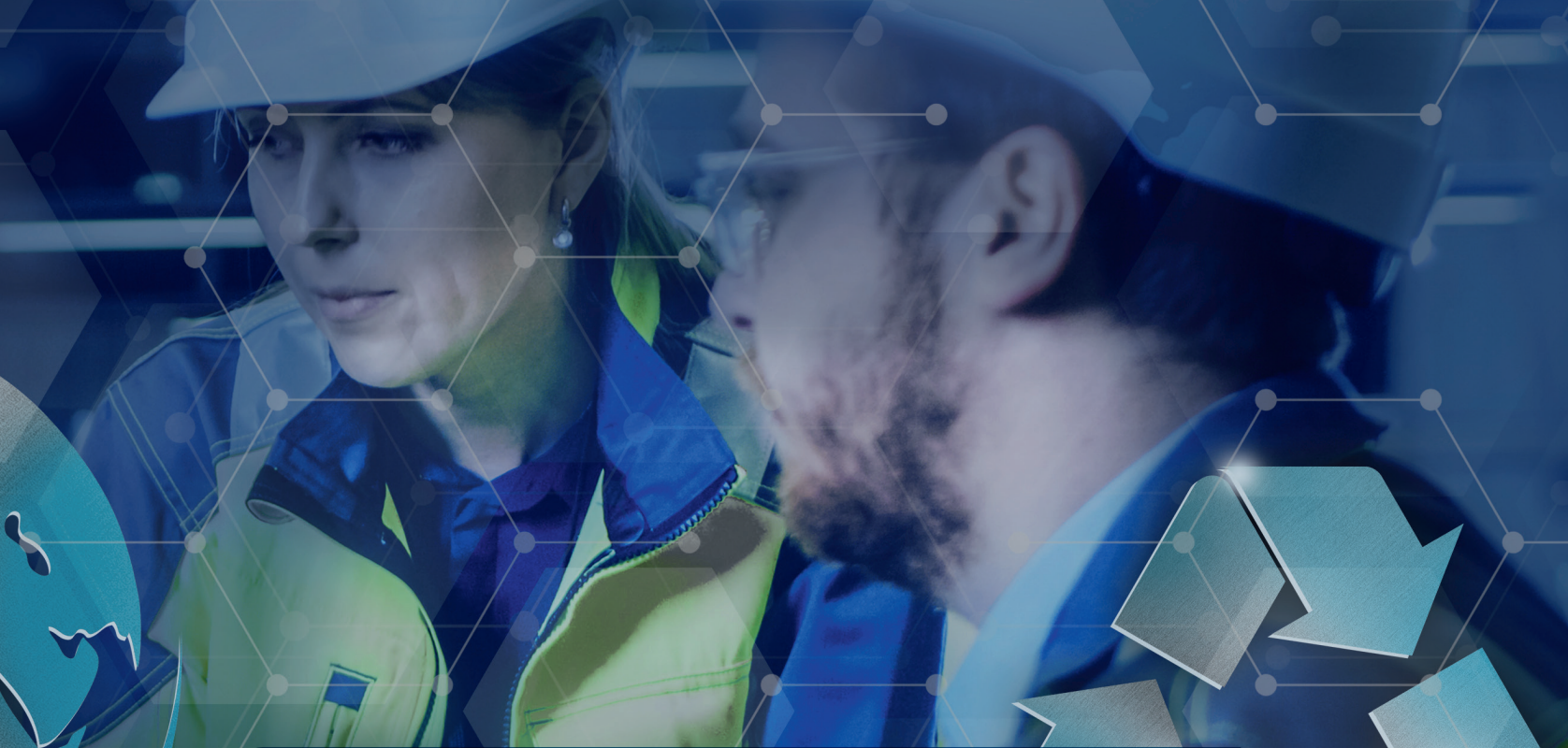
DIGITALIZATION IS AN IRREPLACEABLE ALLY
While the pursuit of the greatest possible efficiency has always been the goal of every industrial business, we must note that today, companies’ efforts to achieve it are greater than ever. Process optimization and digital transformation offer critical help in this sense. It is a widespread and shared opinion that there can be no transition towards a truly sustainable economy without a massive effort for digital transformation as well. That’s the concept of the so-called twin revolutions, which refers to the two great axes on which the entire energy transition hinges: the green transition and the digital one are the two tracks along which the new manufacturing industry must travel to reach the goals ahead, also in the light of the opportunities deriving from public resources made available to recover from the pandemic and to modernize the economy in general. The development and use of increasingly advanced software, the role of applied artificial intelligence, the collection and analysis of big data are some of the areas in which any industry must believe and invest, to really project into the future. From this point of view, the digital transformation enables the green transformation, not vice versa.
A CHALLENGE TO BE WON
Thus, to implement an authentic sustainable transformation, a crucial synergy must form between constantly evolving digital technologies, new levels of process engineering, a strong infrastructural upgrade and real care for workers. Far from empty rhetoric, sustainable manufacturing is an opportunity we cannot afford to miss in order to study and implement solutions with extremely positive repercussions. It should be seen as an excellent accelerator, capable of guiding today’s companies into a promising future from both environmental and economic perspectives. Only by understanding sustainability as a complex, organic and integrated process will we be able to find the equilibrium between production needs and the wellbeing of the planet, and win the demanding and exciting challenge that the future asks us to face.
Want to read more about sustainability? Come discover the latest issue of Power Line Magazine dedicated specifically to this topic.