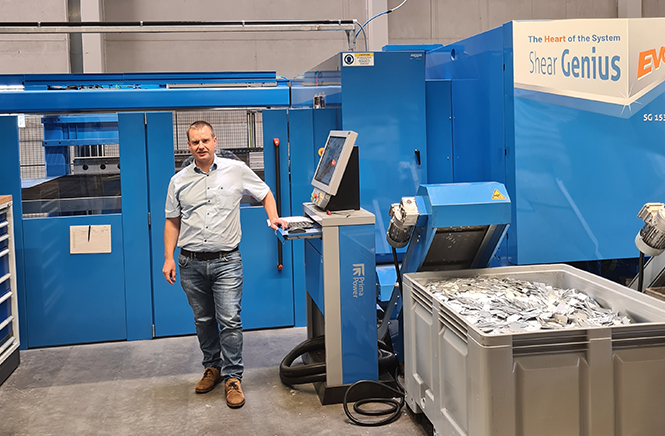
Dringenberg - Il sistema di Prima Power ha aumentato in modo significativo la nostra flessibilità e produttività
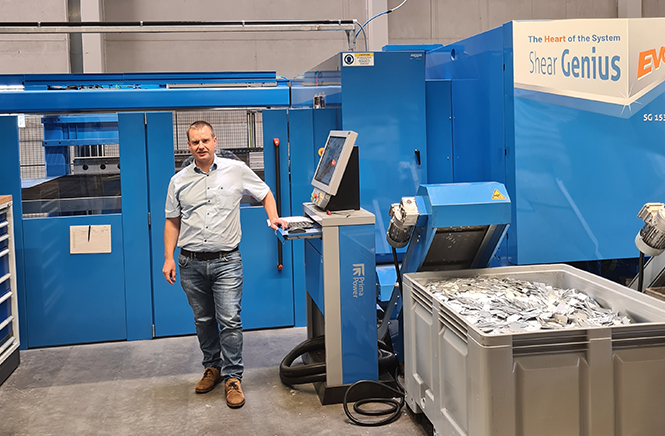
Un’importante azienda manifatturiera tedesca ha ottimizzato i propri processi e ottenuto una maggiore flessibilità grazie alla linea PSBB completamente automatizzata e integrata di Prima Power.
Dringenberg è una delle aziende in più rapida crescita nel settore della lavorazione della lamiera, affermandosi come produttore tedesco leader di attrezzature per officine e veicoli. Questa notevole crescita si basa su una strategia di produzione intelligente che combina la massima qualità con la massima flessibilità. Recentemente, l’azienda ha realizzato un investimento strategico acquistando una linea di punzonatura e piegatura di Prima Power, consolidando così il suo impegno verso una produzione all’avanguardia.
SNELLIRE LE OPERAZIONI: IL PERCORSO VERSO PRIMA POWER PER OTTIMIZZARE I PROCESSI
Dringenberg è il centro di competenza per le attrezzature per officine e veicoli del Gruppo Würth. La loro offerta comprende banchi da lavoro, armadietti, scaffalature e attrezzature mobili per officine. Dringenberg punta molto sulle soluzioni individuali e personalizzate, che costituiscono una sfida importante per la produzione, soprattutto per le apparecchiature di bordo. Dato l’elevato numero di tipi di veicoli e i requisiti speciali dei gruppi commerciali, le dimensioni degli armadietti, le configurazioni dei cassetti e le dimensioni dei vani scorrevoli variano quasi all’infinito.
“Attraverso un configuratore dedicato, ogni cliente può creare il proprio allestimento speciale”, spiega Heiko Stahl, production manager di Dringenberg. “Ciò rende quasi impossibile la preproduzione di massa per il nostro magazzino di assemblaggio. Tuttavia, è necessaria la massima velocità, perché il reparto di assemblaggio di solito ha bisogno dei singoli pezzi e moduli con un solo giorno di anticipo.”
Per ragioni di peso, viene lavorato principalmente alluminio con uno spessore compreso tra 0,8 e 2,0 mm. Poiché l’estetica gioca un ruolo fondamentale, i componenti non devono presentare graffi o striature. Il materiale viene solitamente fornito con una pellicola, che viene rimossa manualmente dopo la lavorazione.
Fino a pochi mesi fa, il materiale veniva punzonato da un operatore su una punzonatrice e collocato su un pallet. Un impilatore lo trasportava poi alla macchina piegatrice. Successivamente, un altro addetto collocava le lamiere punzonate nella macchina piegatrice per ottenere la forma desiderata. Infine, veniva rimossa la pellicola, preparando l’elemento per l’assemblaggio. Il team guidato da Heiko Stahl voleva migliorare questo processo e ha esplorato le varie alternative, imbattendosi rapidamente in Prima Power.
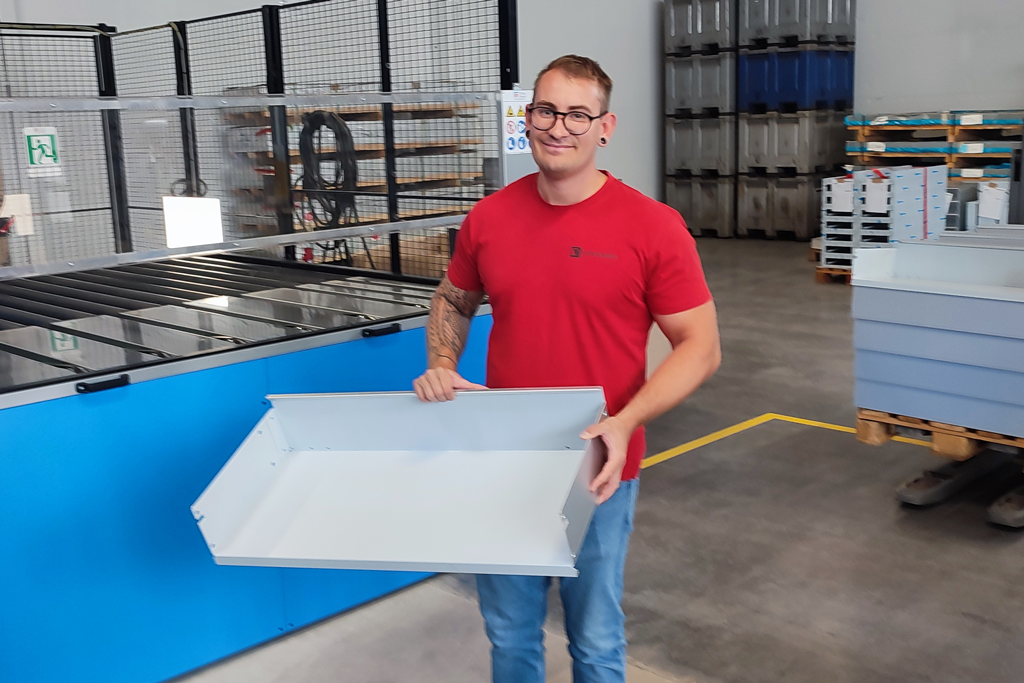
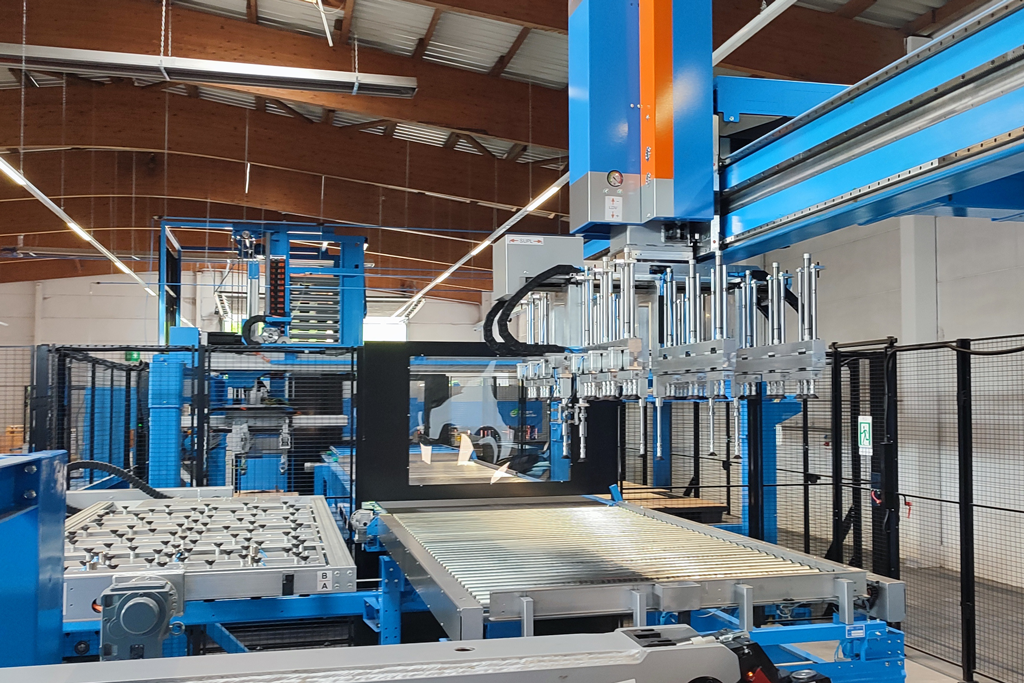
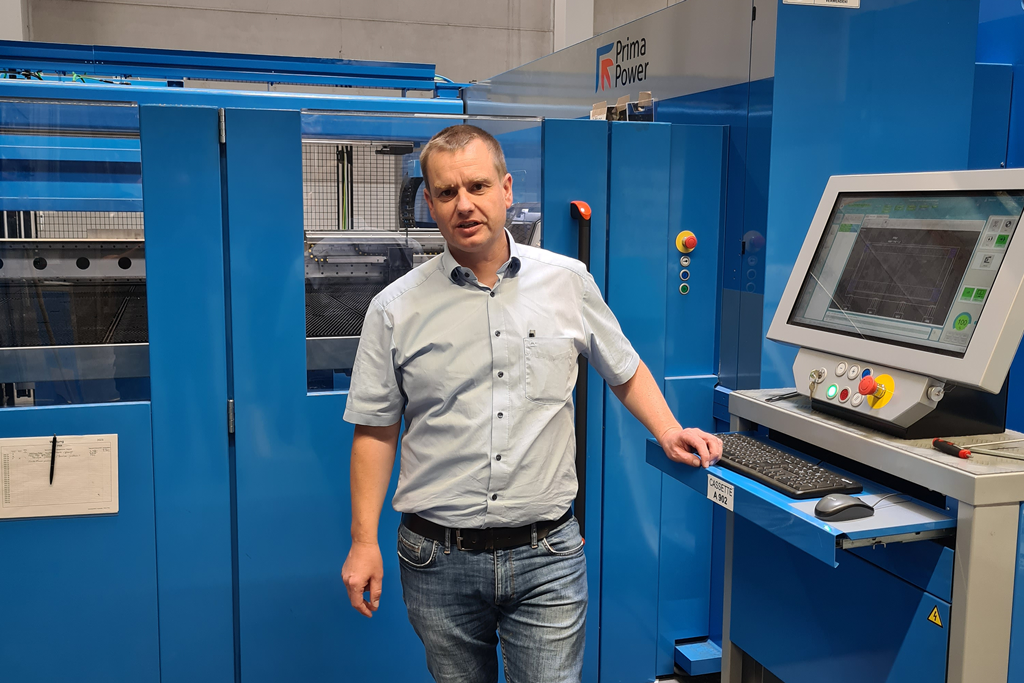
RIDUZIONE DELLA MANODOPERA E AUMENTO DELLA PRODUTTIVITÀ CON LA LINEA SERVO ELETTRICA PSBB DI PRIMA POWER
Dringenberg ha scelto Prima Power, fornitore leader di macchine laser e per la lavorazione della lamiera con la gamma di prodotti più completa del settore: macchine laser 2D e 3D, punzonatrici e macchine combinate punzonatura/laser e punzonatura/ cesoiatura, presse piegatrici, pannellatrici e sistemi di produzione flessibili. Un motivo fondamentale per la scelta di Prima Power è stata la sua capacità di supportare i clienti con soluzioni efficienti di automazione della produzione.
Avendo già collaborato in modo positivo con Prima Power in un altro sito, l’azienda ha confermato la scelta per le sue nuove esigenze produttive. L’obiettivo era quello di ridurre al minimo il lavoro manuale, massimizzare la produttività e aumentare la precisione e la qualità della superficie dei pezzi. La risposta è stata una linea servo elettrica PSBB (Punching, Shearing, Buffering, Bending) che trasforma in modo completamente automatico le lamiere grezze in elementi piegati finiti e pronti per l’installazione.
“La nostra precedente esperienza positiva con Prima Power è stata riconfermata da questo progetto. La collaborazione e l’assistenza di Prima Power sono state eccellenti”, dichiara Stahl. Il punto di partenza è il sistema di immagazzinamento a torre da 20 pallet, che consente la lavorazione di componenti di un’ampia gamma di materiali che possono essere cambiati automaticamente in base al programma. Rene Polz, il group leader di questa linea, riserva sempre un posto libero per le consegne rapide, il che consente di inserire senza interruzioni le lamiere meno utilizzate.
Le lamiere passano alla cella di punzonatura/cesoiatura Shear Genius con una torretta a 16 utensili. Tutti gli utensili si adattano alla produzione in serie, non necessitando di setup per le diverse parti. Un ulteriore vantaggio è la funzione di programmazione parametrica: si possono creare elementi che differiscono solo per le dimensioni, ma che per il resto sono identici, cambiando pochi parametri ed evitando così una programmazione elaborata. Facilità d’uso ed efficienza sono le caratteristiche principali dell’intera linea.
Dopo la cesoiatura, i componenti vengono trasferiti al buffering e alla successiva piegatura in una cella di piegatura automatica.
Tale operazione viene eseguita da un robot, che offre un elevato grado di flessibilità e che consente l’impilamento automatico di pezzi di grandi dimensioni. Il flusso di materiale può essere studiato per compensare i diversi tempi richiesti dalla punzonatura e dalla piegatura.
La lamiera viene trasferita direttamente alla piegatrice, immagazzinata temporaneamente o immessa dall’area di immagazzinamento intermedio. La piegatrice integrata ha come obiettivi principali la produttività, la qualità e la ripetibilità. Sono in corso dei test per la lavorazione di lamiere senza pellicola protettiva, il che potrebbe eliminare un’altra fase che richiede molto tempo.
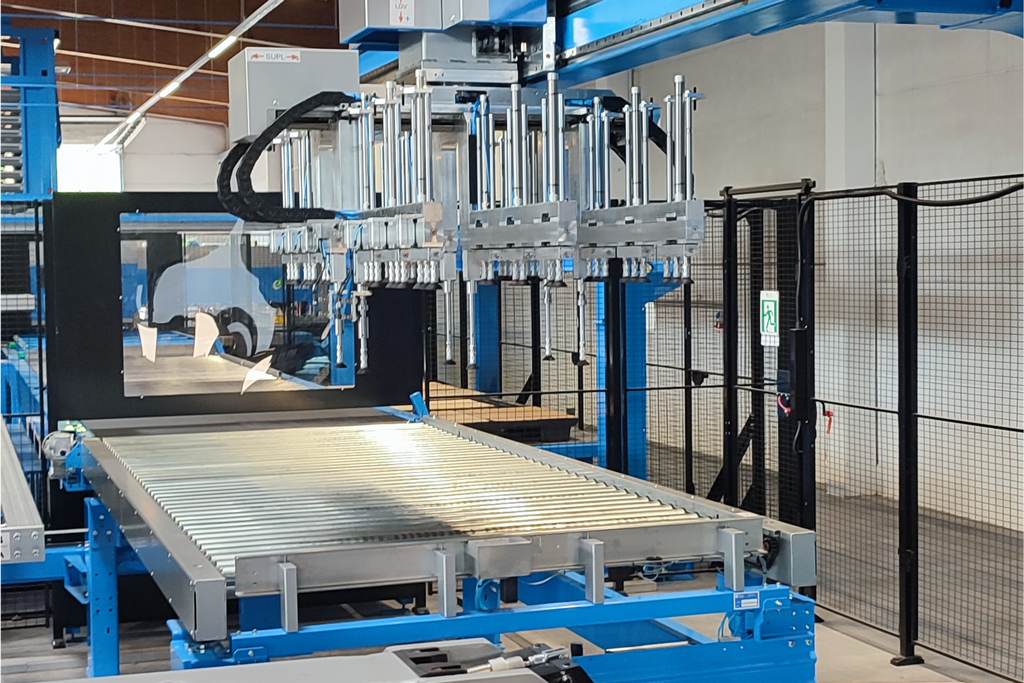
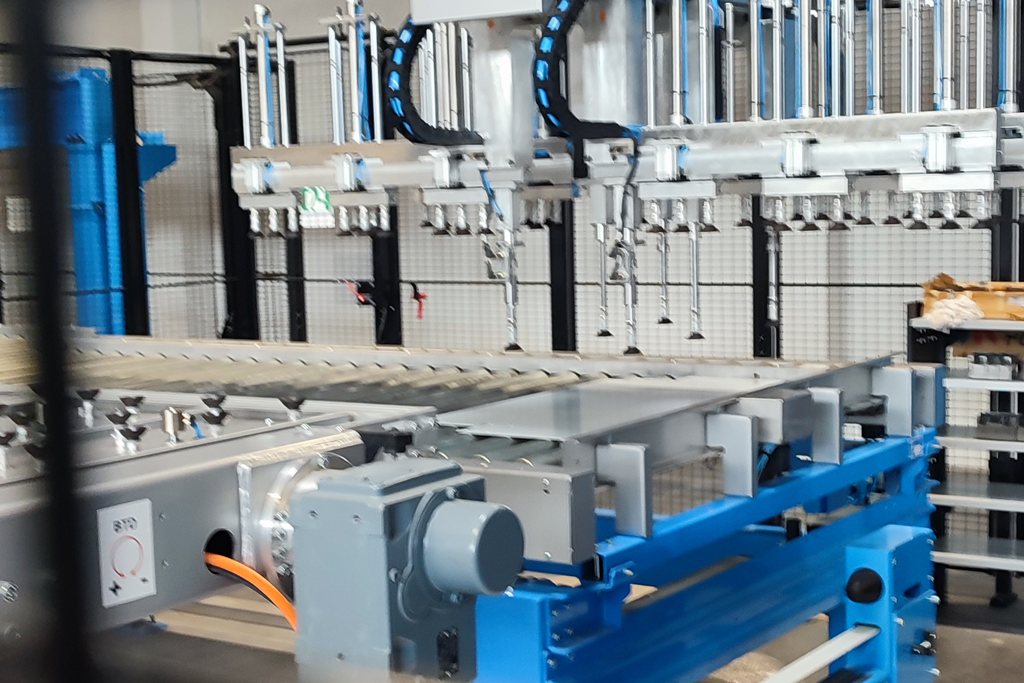
AUMENTO DELLA PRODUTTIVITÀ E DELLA FLESSIBILITÀ GRAZIE ALL’AUTOMAZIONE E ALL’INTEGRAZIONE COMPLETE
“Con questa soluzione siamo passati da un’operazione manuale a un processo completamente automatizzato”, spiega Stahl. “Eravamo consapevoli che alcuni aggiustamenti sarebbero stati necessari, ma la collaborazione e il supporto di Prima Power sono stati eccezionali. Poiché le macchine per la punzonatura-cesoiatura e la piegatura dei pannelli sono completamente automatizzate e integrate in un’unica linea, non abbiamo più bisogno di ulteriore movimentazione dei materiali. Il pezzo non viene toccato finché non lo scarichiamo e lo pallettizziamo. Questo è l’unico intervento dell’operatore richiesto in tutta la linea.”
Questo approccio risolve anche il problema della carenza di lavoratori qualificati. L’intera linea è gestita da un solo operatore, con l’obiettivo di produrre fino a 400 pezzi per turno con un funzionamento regolare. Attualmente la linea funziona su due turni, ma in seguito potrà essere gestita completamente senza personale. Questo ha aumentato in modo significativo la capacità produttiva di Dringenberg, consentendo una riduzione degli stock di magazzino e una maggiore velocità e flessibilità delle operazioni. “Il sistema di Prima Power ha aumentato in modo significativo la nostra flessibilità e produttività”, conclude Stahl. Sulla base di questa esperienza positiva, Dringenberg continuerà il suo percorso di crescita insieme a Prima Power.
Il sistema di Prima Power ha aumentato in modo significativo la nostra flessibilità e produttività.
Are you looking for a similar solution for your company? Find it here
PSBB
SISTEMI DI PRODUZIONE FLESSIBILI