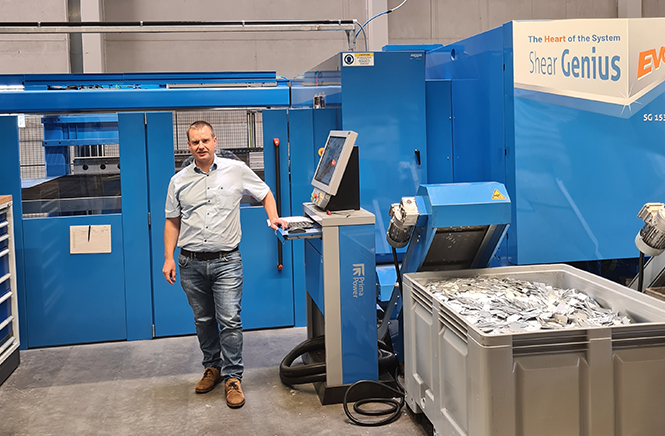
Dringenberg - Steigerung der Produktionskapazität durch Automatisierung und Integration
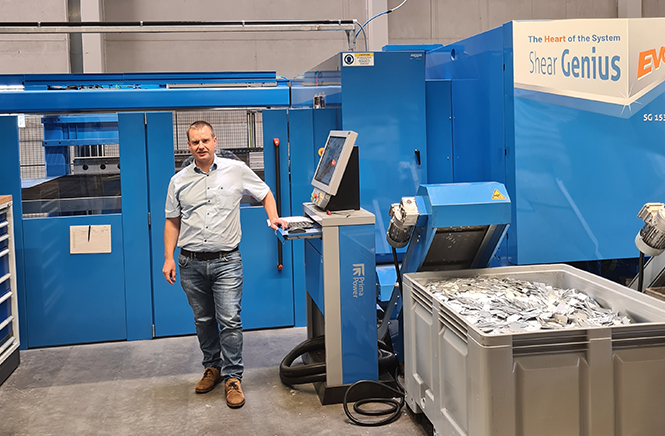
Dringenberg optimierte seine Abläufe und steigerte den Durchsatz mit Prima Power.
Dringenberg ist eines der am schnellsten wachsenden Unternehmen im Bereich der Blechbearbeitung und hat sich als führender deutscher Hersteller von Betriebs- und Fahrzeugausrüstungen etabliert. Dieses beeindruckende Wachstu basiert auf einer klugen Produktionsstrategie, die höchste Qualität mit maximaler Flexibilität verbindet. Kürzlich hat das Unternehmen eine strategische Investition in eine Stanz-Biege-Kombination von Prima Power getätigt, um sein Engagement für hochmoderne Fertigung weiter zu stärken.
RATIONALISIERUNG DER ABLÄUFE: DER WEG ZU PRIMA POWER FÜR PROZESSOPTIMIERUNG
Innerhalb der Würth-Gruppe fungiert Dringenberg als Kompetenzzentrum für intelligente Werkstatt- und Fahrzeugeinrichtungen. Ihr Sortiment umfasst Werkbänke, Schränke, Regale und mobile Werkstatteinrichtungen.
Dringenberg legt besonders großen Wert auf maßgeschneiderte Individuallösungen, die insbesondere bei der Fahrzeugausstattung eine große Herausforderung für die Produktion darstellen. Angesichts der Vielzahl von Fahrzeugtypenund den speziellen Anforderungen verschiedener Branchen sind die Dimensionen der Schränke, die Konfiguration der Schubladen und die Größe der Schiebefächer praktisch unbegrenzt.
„Mithilfe unseres eigenen Konfigurators kann jeder Kunde seine individuelle Einrichtung zusammenstellen“, erklärt Heiko Stahl, Produktionsleiter bei Dringenberg. „Die Massenvorproduktion für unser Montagelager gestaltet sich aufgrund einiger Herausforderungen als äußerst anspruchsvoll. Gleichzeitig sind schnelle Abläufe unerlässlich, da die Montageabteilung die Einzelteile und Baugruppen in der Regel nur einen Tag im Voraus benötigt.“
Hauptsächlich verarbeiten sie aus Gewichtsgründen Aluminium mit einer Dicke zwischen 0,8 und 2,0 mm. Dabei spielt die Ästhetik eine entscheidende Rolle, da die Bauteile makellos sein müssen und keine Kratzer oder Schlieren aufweisen dürfen. Das Material wird normalerweise mit einer Schutzfolie geliefert, die nach der Verarbeitung manuell entfernt wird.
Bis vor einigen Monaten erfolgte die Bearbeitung des Materials in mehreren Schritten. Ein Mitarbeiter führte das Stanzen an einer Maschine durch und legte die gestanzten Teile auf eine Palette. Ein Gabelstapler transportierte sie dann zur Biegemaschine. Dort wurden die gestanzten Bleche von einem anderen Arbeiter in die gewünschte Form gebracht. Schließlich wurde die Schutzfolie entfernt, und das Element war für die Montage bereit. Das Team unter der Leitung von Heiko Stahl suchte nach Möglichkeiten zur Verbesserung dieses Verfahrens und stieß schnell auf Prima Power.
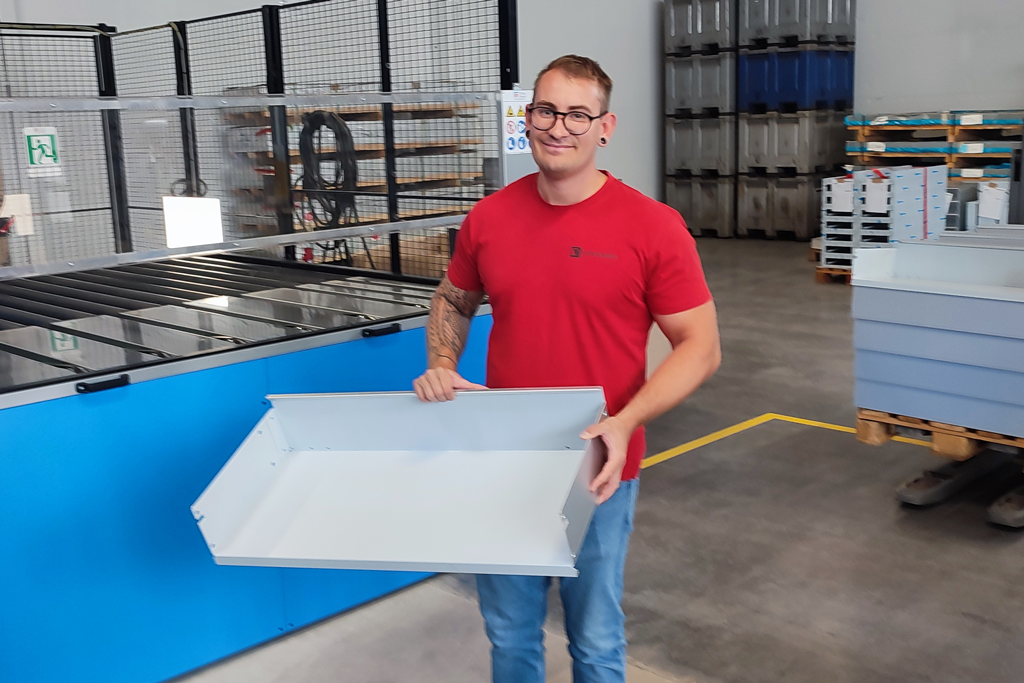
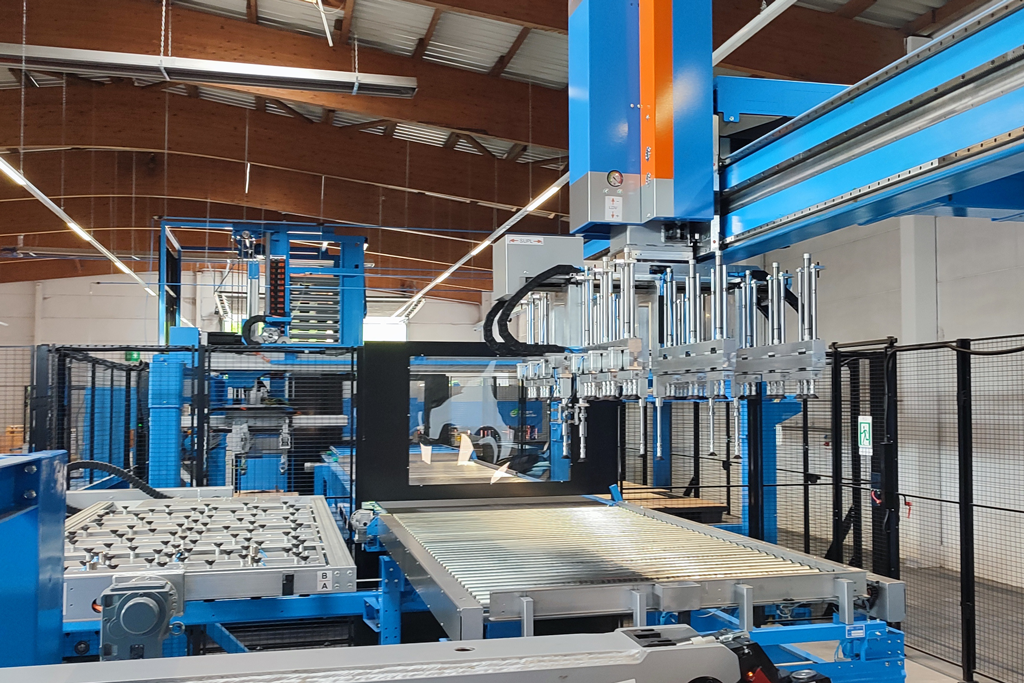
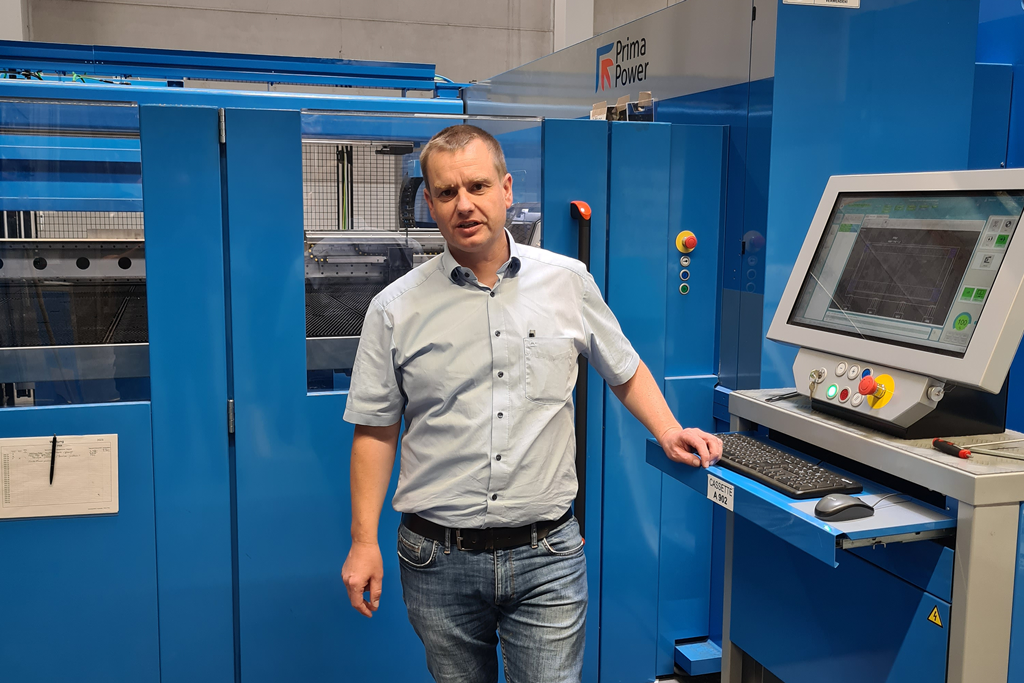
WENIGER ARBEITSAUFWAND UND HÖHERER DURCHSATZ MIT DER SERVOELEKTRISCHEN PSBB-LINIE VON PRIMA POWER
Dringenberg entschied sich für Prima Power, einen führenden Anbieter von Laser- und Blechbearbeitungsmaschinen mit der umfassendsten Produktpalette in der Branche: Dazu gehören 2D- und 3D-Lasermaschinen, Stanzmaschinen sowie kombinierte Stanz-/Laser- und Stanz-/Schermaschinen, Abkantpressen, Schwenkbiegemaschinen und flexible Fertigungssysteme. Die Wahl von Prima Power erfolgte aus einem wichtigen Grund: die Fähigkeit des Unternehmens, effiziente Produktionsautomatisierungslösungen für Kunden bereitzustellen.
Da bereits eine erfolgreiche Zusammenarbeit mit Prima Power an einem anderen Standort stattgefunden hatte, entschied sich das Unternehmen, erneut zusammenzuarbeiten, um eine optimale Lösung zu finden. Das Hauptziel bestand darin, den Arbeitsaufwand zu minimieren, den Durchsatz zu maximieren und gleichzeitig die Genauigkeit und Oberflächenqualität zu verbessern. Die Lösung bestand in einer vollautomatischen servoelektrischen PSBB-Linie (Stanzen, Scheren, Puffern, Biegen), die Rohbleche automatisch in fertige, montagebereite Biegelemente umwandelt.
„Unsere positiven Erfahrungen mit Prima Power wurden durch dieses Projekt erneut bestätigt. Die Zusammenarbeit und die Unterstützung durch Prima Power waren hervorragend“, erklärt Stahl. Die PSBB-Linie startet mit einem 20-Paletten-Turmlager, das die Verarbeitung von Bauteilen aus verschiedenen Werkstoffen ermöglicht, die automatisch und programmgesteuert gewechselt werden können. Rene Polz, Gruppenleiter für diese Linie, behält immer Platz für schnelle Umdrehungen frei, damit auch weniger häufig verwendete Platten nahtlos eingearbeitet werden können.
Die Bleche werden zur Stanz-/Schermaschine Shear Genius mit einem Revolverkopf mit 16 Werkzeugen transportiert. Alle Werkzeuge für die Serienproduktion sind vorgerüstet, was das aufwendige Umrüsten für verschiedene Teile überflüssig macht. Die Linie bietet auch einen integrierten Reststreifenzerkleinerer und die Möglichkeit zur Parametrierung in der Steuerung. Dies erleichtert die Erstellung von Teilen, die sich lediglich in ihren Abmessungen unterscheiden, ohne aufwändige Programmierung. Die gesamte Linie zeichnet sich durch Benutzerfreundlichkeit und Effizienz aus.
Nach dem Schneiden werden die Teile automatisch in eine Pufferzone und dann in eine automatische Biegezelle weitergeleitet. Hier übernimmt ein Roboter die Aufgabe, der hohe Flexibilität bietet und das automatische Stapeln größerer Teile ermöglicht. Dadurch kann der Materialfluss so gestaltet werden, dass die unterschiedlichen Zeitanforderungen beim Stanzen und Biegen ausgeglichen werden können.
Die Bleche werden entweder direkt an die Biegemaschine übergeben, zwischengelagert oder aus dem Zwischenlager zugeführt. Die integrierte Biegemaschine legt Wert auf Produktivität, Qualität und Wiederholbarkeit. Aktuell werden Tests durchgeführt, um Bleche ohne Schutzfolie zu verarbeiten, was einen zeitaufwändigen Schritt einsparen könnte.
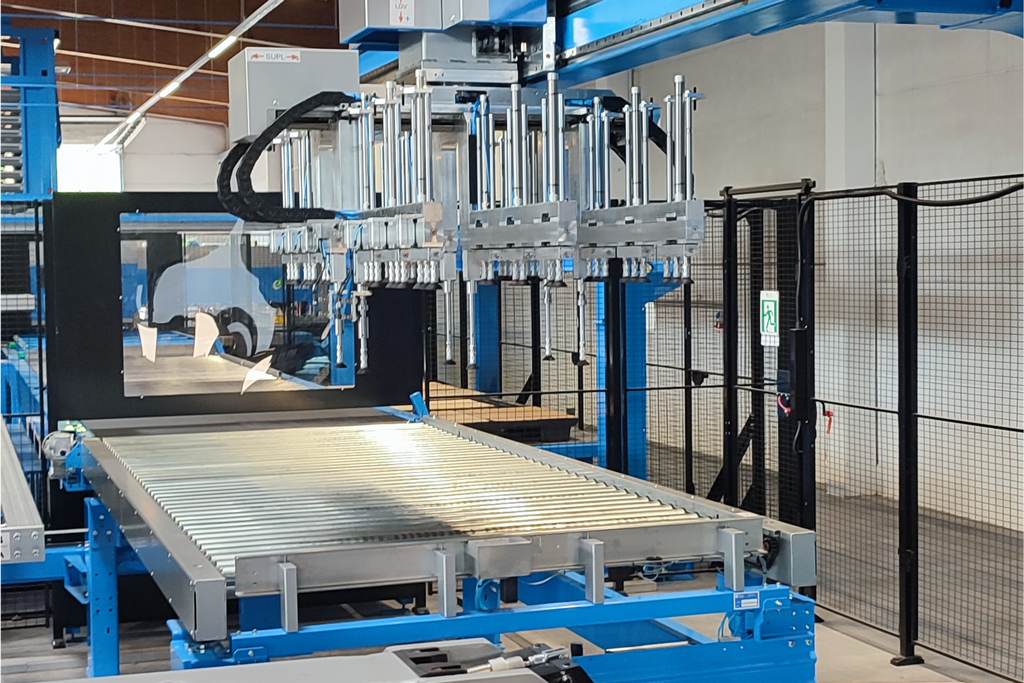
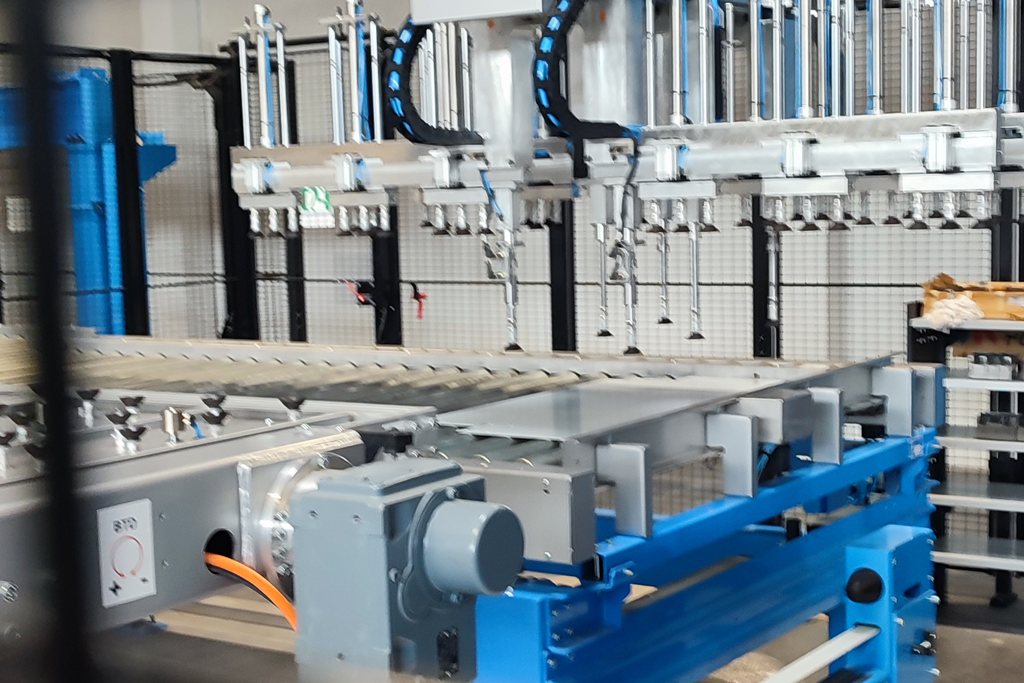
DIE STEIGERUNG DER PRODUKTIVITÄT UND FLEXIBILITÄT DURCH EINE VOLLSTÄNDIGE AUTOMATISIERUNG UND INTEGRATION
Heiko Stahl erklärt: „Mit dieser Lösung haben wir den Schritt von der manuellen Bedienung zu einem vollautomatischen Prozess gemacht.“
„Wir waren uns bewusst, dass nicht alles sofort reibungslos funktionieren würde, aber die Zusammenarbeit und Unterstützung von Prima Power waren außergewöhnlich. Dank der Integration von Stanz-Scher- und Biegemaschinen in einer Linie benötigen wir kein zusätzliches Materialhandling mehr. Das Werkstück bleibt unberührt, bis es abgeladen und gestapelt wird. Der einzige Eingriff, der in der gesamten Linie erforderlich ist, besteht darin.“
Dieser Ansatz trägt auch dazu bei, dem Mangel an Fachkräften zu begegnen. Ein einzelner Bediener steuert die gesamte Linie, die im reibungslosen Betrieb bis zu 400 Teile pro Schicht produzieren kann. Derzeit wird die Anlage im 2-Schicht-Betrieb betrieben, kann aber auch vollständig mannlos betrieben werden. Durch diese Maßnahmen wurde die Produktionskapazität von Dringenberg erheblich gesteigert. Es ermöglichte zudem eine Verringerung des Lagerbestands und erhöhte die Betriebsgeschwindigkeit und Flexibilität erheblich. Stahl fasst zusammen: „Das System von Prima Power hat unsere Flexibilität und Produktivität erheblich gesteigert.“ Basierend auf diesen positiven Erfahrungen plant Dringenberg, seinen Wachstumskurs an der Seite von Prima Power fortzusetzen.
Das System von Prima Power hat unsere Flexibilität und Produktivität erheblich gesteigert.