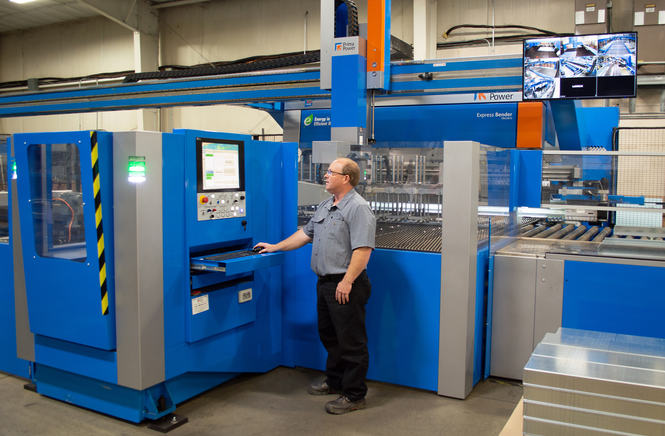
Raytec, siempre con la vista puesta en la automatización
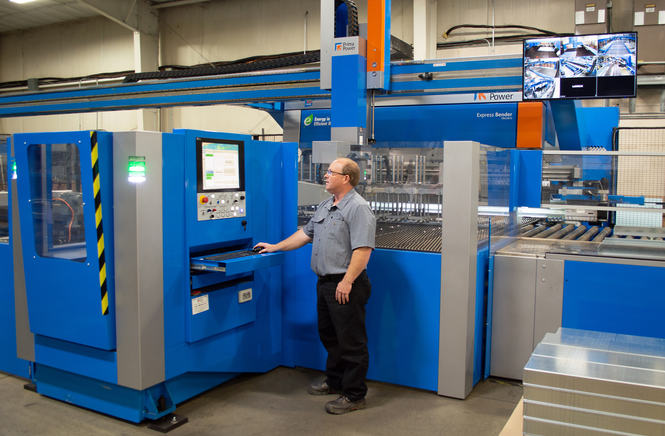
Un taller de Pennsylvania aumenta su capacidad de producción con la adición de manipulación automatizada de materiales y una plegadora de paneles a su punzonadora/cizalla
La búsqueda por parte de las empresas de fabricación de metales del encaje adecuado en sus organizaciones ha sido un reto constante a lo largo de los años. Por supuesto, se ha exacerbado recientemente con el aumento del salario por hora en otros sectores económicos, como la restauración y la hostelería, lo que hace que la competencia por los talentos de nivel inicial sea aún más acalorada. Para combatir esta tendencia en curso, los fabricantes de metal han tratado de invertir todo lo posible en la automatización de las actividades de fabricación en sus plantas de producción, liberando a los empleados para abordar trabajos más complejos. Para algunos, sin embargo, esta estrategia no es nueva. Raytec Fabricating, por ejemplo, ha tenido las idea claras durante varios años y no solo ha adquirido tecnología de fabricación más productiva a lo largo del tiempo, sino que también ha planificado un futuro automatizado con cada compra.
«Pronto vimos que teníamos que continuar este viaje [en lo que respecta a la automatización] para tener éxito», dijo Zimmerman. «Fue entonces cuando nos planteamos añadir un robot apilador [a la punzonadora/cizalla]. En aquel momento, no habíamos pensado realmente en el plegado automático de tableros, al menos hasta que tuvimos la oportunidad de que surgiera algún trabajo que encajara bien con ese tipo de máquina.»
Añadir una plegadora de paneles a su máquina combinada de punzonado y cizallado Prima Power Shear Genius SGe8, adquirida originalmente en 2015, era una extensión lógica del plan original de la empresa hacia un futuro más automatizado. Un robot apilador en la máquina combinada eliminaría las responsabilidades de manipulación del material y permitiría al operario de la máquina manejar quizás una o incluso dos máquinas más.
El robot y una plegadora de paneles conectada se tradujeron en un sistema en el que las piezas se troquelaban, perforaban y formaban sin ninguna interferencia humana. No es necesario que ninguna persona deba tocar la pieza hasta el momento de manipular la pieza acabada al salir de la paneladora (o de la punzonadora/cizalla si no se requería conformado).
En 2020, Raytec decidió apostar por la automatización total. Instaló una torre de 14 estaciones para alimentar la célula de punzonado y cizallado, que sustituyó a un sistema de carga y descarga de un solo palé; una plegadora servoeléctrica EBe Express de Prima Power; un robot de recogida y apilado para ayudar con las piezas que salen de la SGe; y una estación intermedia entre las dos células para garantizar que las piezas fluyeran sin problemas de una estación a otra.
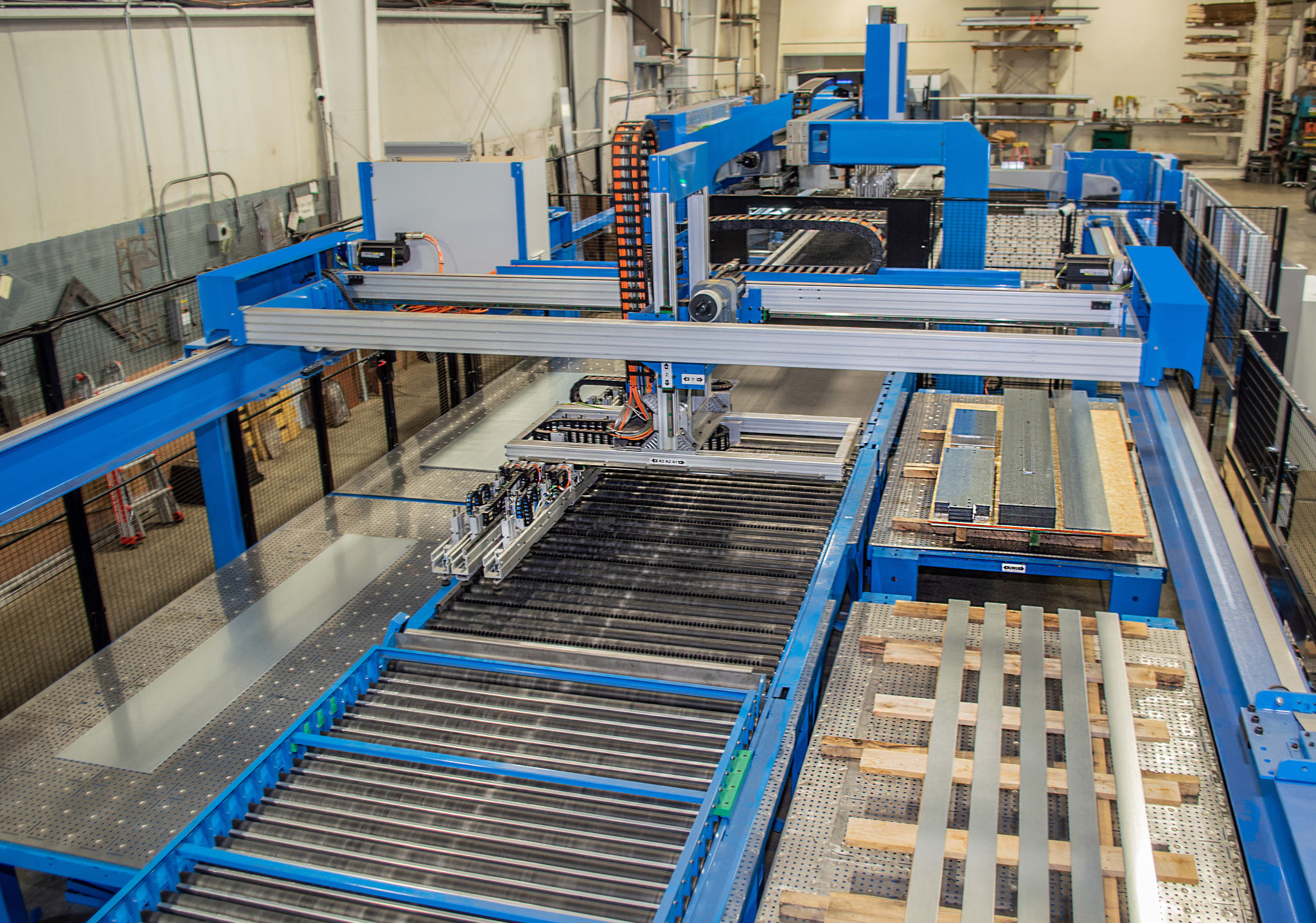
CONFIGURACIÓN DE LA NUEVA LÍNEA
A pesar de su antigüedad, la máquina combinada de punzonado y cizallado seguía siendo una candidata viable para anclar la nueva línea de fabricación automatizada. Al fin y al cabo, fue una de las primeras células instaladas en Raytec para el trabajo desatendido y sin operarios alrededor. En particular, Zimmerman afirmó que la función de clasificación de piezas de la máquina era algo que agilizaba la producción.
La SGe tiene dos zonas de caída de 30 por 60 pulgadas para piezas de tamaño medio separadas del esqueleto y un transportador transversal que captura las piezas más pequeñas y las lleva a uno de los cinco contenedores situados debajo de la mesa. Añadir la torre de almacenamiento de materias primas, que se conectaba a la máquina combinada de punzonado y cizallado, fue algo que se pudo hacer con bastante facilidad porque existía espacio para colocarla cerca del equipo. Sin embargo, toda la línea iba a tener que planificarse con precisión.
«El reto consistía en mantenerse dentro de la longitud de la fábrica, determinada por una puerta de muelle de carga», dijo Fred Cooke, director de ventas de Prima Power. «Así que suministramos componentes estándares en una configuración personalizada» La SGe8 era un formato de 14 pies.
El sistema de entrega de chapas sueltas FLS1540 conectado a la máquina y el sistema robotizado de recogida y apilado podían acomodar ese tamaño de pieza. El dispositivo del centro de recogida que alimenta la plegadora permitió también piezas de 426 mm (14 pies), abriendo la puerta a que las piezas en bruto cortadas con láser pudieran ser procesadas por el sistema de plegado. El diseño de la plegadora de paneles, sin embargo, tuvo que ser retocado. El diseño de la plegadora se amplió de 3,8 a 3,9 m (149,6 a 153,5 pulg.) para adaptarse a una pieza específica que Raytec fabricaba regularmente. Para dejar sitio a todo, Zimmerman dijo que apartaron parte de la maquinaria. Toda la línea quedaba muy justa, pero consiguieron mantener todo el equipo en el lado derecho de la puerta del muelle.
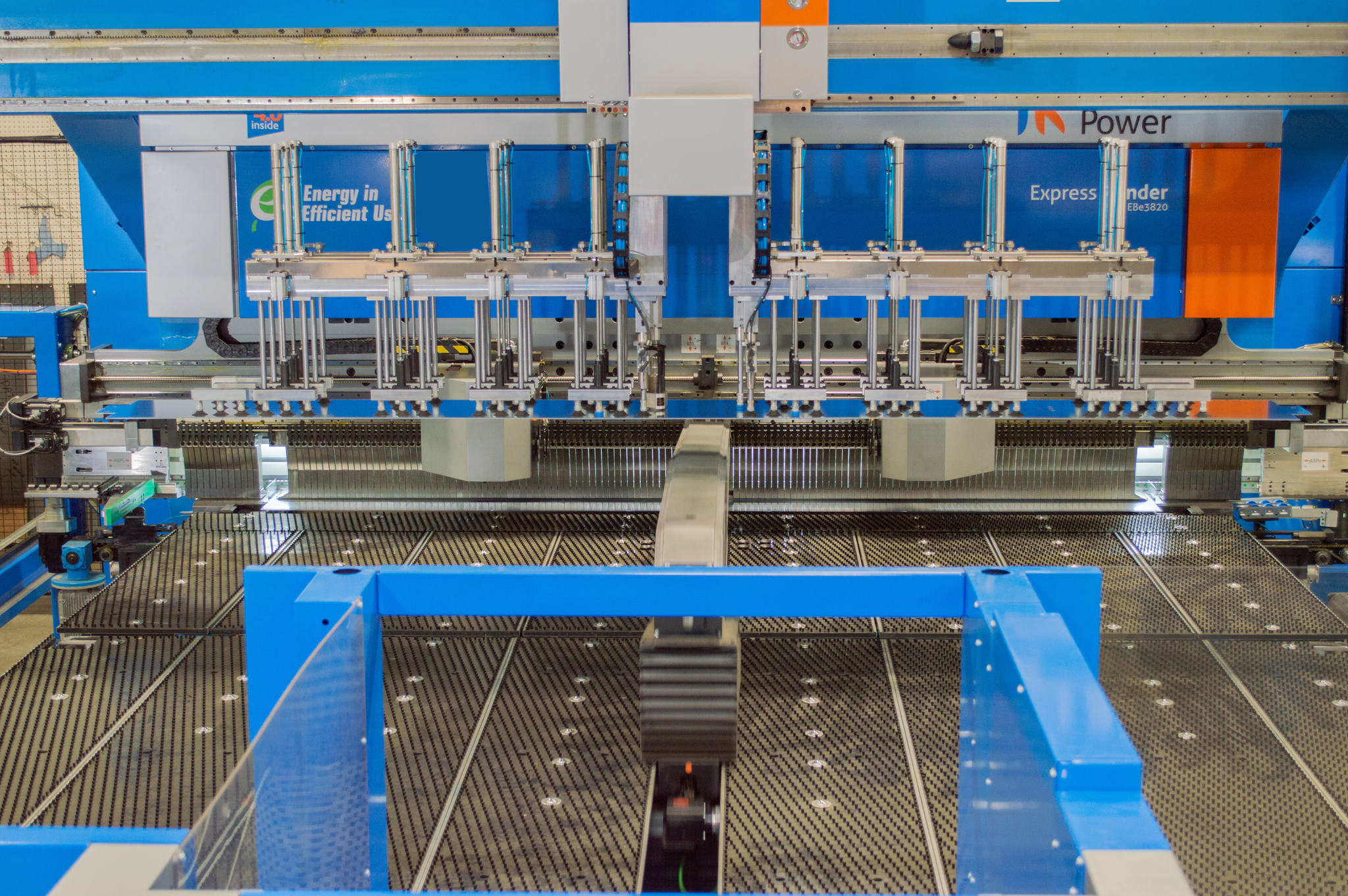
CÓMO FUNCIONA LA LÍNEA+
La línea se denomina oficialmente PSBB (punzonado, cizallado, almacenamiento intermedio y plegado), y el aspecto de almacenamiento intermedio ayuda a marcar el ritmo de producción para que todo fluya sin problemas a través de la línea.
Por ejemplo, para piezas que no requieren mucho punzonado o conformado en la SGe, el cizallado puede superar al robot de apilado muy rápidamente. Para evitarlo, las piezas se almacenan después de salir de la punzonadora/cizalla, y se mantienen ahí hasta que el robot puede apilar las piezas para su puesta en escena para alimentar la paneladora o para su salida si no se necesita conformado.
«El software de programación le permite ejecutar y maximizar la producción sin preocuparse por un posible cuello de botella en el sistema», dijo Zimmerman.
Una pila de piezas antes de la plegadora no es ALGO demasiado preocupante porque la EBe puede funcionar unas dos o tres veces más rápido que la punzonadora/cizalla, según Zimmerman, sobre todo si los relieves o las formas ascendentes forman parte de las actividades en la SGe.
A diferencia de una plegadora tradicional, una paneladora no requiere que un operario manipule la pieza. Un manipulador de piezas toma la chapa introducida en la mesa y la coloca entre las herramientas portapiezas, que descienden y sujetan la pieza en su lugar, con material sobresaliente por el otro lado. Con la chapa en su sitio, las cuchillas de plegado de la máquina se mueven desde arriba y desde abajo para plegar el metal.
En la mayoría de las operaciones, el movimiento de la cuchilla de plegado, y no la forma de las herramientas, determina el ángulo y el radio de plegado finales. Cuanto más sobresalga el metal del utillaje, una zona de la máquina llamada garganta, más alta será la pestaña resultante. Cuanto más profunda sea la garganta, más alta será la brida. La altura máxima de plegado en la plegadora de paneles es de unos 20 cm (8 pulg.)
Zimmerman dijo que aunque la EBe no puede manejar todo, como piezas muy estrechas, que no disponen de suficiente espacio para que el manipulador de piezas las sujete y no son lo suficientemente anchas para extenderse más allá de las herramientas de soporte de piezas en bruto, ha sido una herramienta muy versátil, procesando una alta combinación de trabajos. Produce piezas cuyo tamaño varía desde puertas hasta paneles de 4 m (13 pies), de forma constante a lo largo de un turno. Toda la línea de PSBB está atendida por una sola persona.
Zimmerman añadió que, además de las mejoras en productividad y coherencia, toda la línea ha dado lugar a una operación mucho más segura porque nadie tiene que manipular el material hasta que sale de la plegadora de paneles.
«Ha requerido un nivel de experiencia diferente en la parte de programación, pero los resultados merecen la pena. Se pueden dictar los resultados de forma mucho más predecible y controlada desde la oficina que con los métodos de fabricación tradicionales», afirma Zimmerman. «No se depende de la experiencia o la habilidad de un operario.»
La plegadora de paneles no solo ha abierto la capacidad de conformado de Raytec, sino también las puertas a nuevas oportunidades de negocio.
«En lo que respecta a nuestros clientes, buscábamos formas de aprovechar las oportunidades perdidas. Una de ellas que vimos fue que había muy pocas líneas integradas de plegado de paneles, si es que había alguna, en el mercado de los talleres. Lo que eso nos permitió hacer fue abrir el mercado de volúmenes pequeños y medianos para disponer de capacidades de plegado de paneles totalmente integradas en el mercado de talleres, donde este mercado normalmente no tendría acceso a esa tecnología», dijo Zimmerman.
AÚN NO HAN TERMINADO
Con su nueva línea automatizada en funcionamiento, cabría esperar que Raytec se tomara un momento para analizar el impacto de la nueva inversión, pero no es el caso. El fabricante de metal sigue adelante con la ampliación de sus actuales instalaciones de más de 4 000 metros cuadrados. Zimmerman dijo que se espera que una adición de más de 1 600 m² esté terminada a finales de la primavera o principios del verano, a la que seguirá otra de más de 2 500 m² a finales de este verano. Raytec habrá duplicado su tamaño en otoño de este año.
«Queremos repartir un poco algunas de nuestras operaciones para que sean más eficientes», dijo.
Las dos máquinas de corte por láser se trasladarán a la primera adición. Ambas máquinas estarán conectadas a torres automatizadas de almacenamiento y recuperación de material, lo que les permitirá maximizar el corte. Con la ampliación de este último edificio, Raytec está estudiando la posibilidad de integrar un sistema de corte a medida alimentado por bobina en la línea de punzonado/cizallado/plegado de paneles.
Zimmerman añadió que el taller tiene previsto trasladar el actual sistema de punzonado/cizallado y sustituirlo por un modelo más moderno. La máquina combinada autónoma de punzonado y cizallado se acoplaría, entonces, a una torre de material para seguir funcionando sin supervisión. La célula actuaría como reserva para el troquelado y conformado de piezas pequeñas.
Los planes de automatización no acaban ahí. Gracias a la capacidad de Prima Power para integrar y construir sistemas totalmente automatizados compatibles con los anteriores, se considera que un sistema automatizado de almacenamiento y recuperación de material Night Train FMS es el último paso para unir realmente la célula de punzonado/cizallado independiente y la línea de punzonado/cizallado/plegado de paneles.
«Nuestro objetivo es poder pasar de la bobina a la chapa en cualquiera de las máquinas, pasar del almacenamiento de la chapa al punzonado en cualquiera de las máquinas y, a continuación, volver a colocar la pieza punzonada en el sistema automatizado para su almacenamiento», dijo Zimmerman.
En la actualidad, Raytec cuenta con unas 14 personas que dirigen sus operaciones de fabricación de metal. Esa cifra no cambiará drásticamente con la inversión en una mayor automatización. Zimmerman no puede predecir el futuro, pero sabe que Raytec necesita seguir mejorando su productividad y flexibilidad sin tener que añadir necesariamente mano de obra en el futuro. Ese ha sido el plan durante un tiempo y seguirá guiando a la empresa a corto plazo.
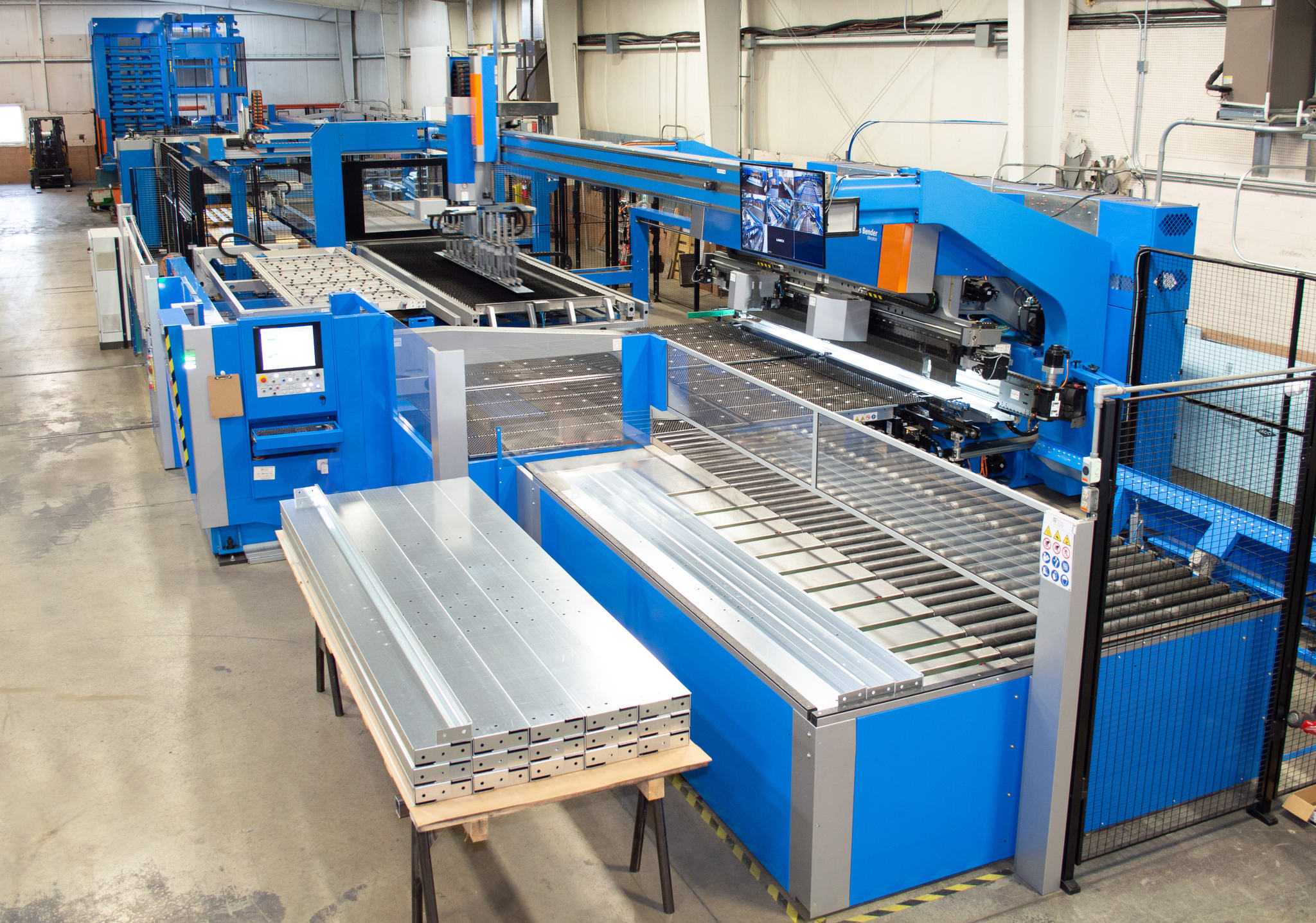
Portions of this article were used in the article that appeared in the March, 2023 issue of the FABRICATOR.
On our customer side, we were looking at ways to fulfill missed opportunities. One of them that we saw was that there were very few, if any, integrated panel bending lines in the job shop market.
Are you looking for a similar solution for your company? Find it here
Shear Genius
MÁQUINAS COMBINADAS DE PUNZONADO Y CIZALLADO
La más alta productividad con punzonado y cizallado integrado
PSBB
SISTEMAS DE MANUFACTURA FLEXIBLE