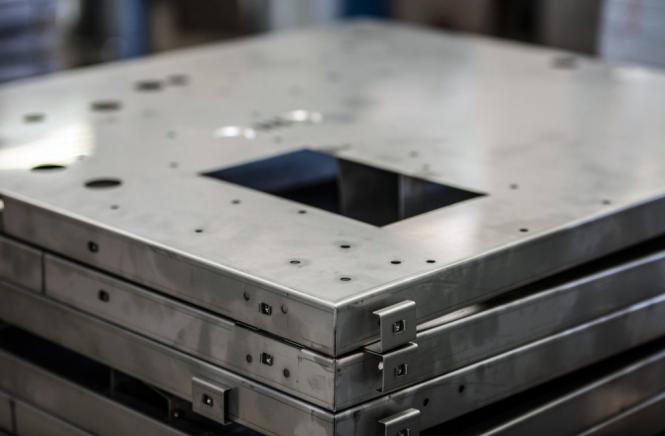
Ordine ed efficienza guidano la produttività
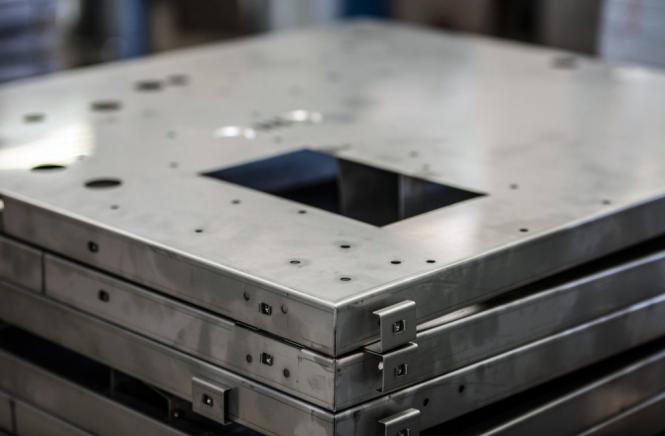
Astra nasce poco meno di trent’anni fa da un’intuizione imprenditoriale, in pochi anni dimostratasi vincente: l’acciaio inox quale materiale tecnologico del futuro.
A plasmarlo e lavorarlo è oggi un performante ed efficiente processo in cui tutte le fasi operative, dal taglio laser alla punzonatura, dalla piegatura alla pannellatura, al sistema di stoccaggio automatico (vero cuore del processo), sono state fornite da Prima Power
Astra è un’azienda specializzata nella progettazione e nella lavorazione di carpenteria metallica per la realizzazione di componentistica prevalentemente in acciaio inox, dal semilavorato al prodotto finito. Nata nel 1991, l’azienda si dimostra attenta a soddisfare i più elevati livelli di qualità di prodotto richiesti, perseguendo l’intuizione del fondatore Rudy Peruzzetto, lungimirante nell’intuire come l’acciaio inox sarebbe divenuto il materiale tecnologico del futuro. Con queste premesse, sin da subito risorse e competenze vengono orientate verso settori esigenti come l’ospedaliero e il farmaceutico, e nel 1997 si rende necessario il primo ampliamento produttivo. Nello stesso anno inizia la collaborazione anche con un importante gruppo multinazionale, Electrolux Professional, punto di riferimento globale nel settore degli elettrodomestici e delle apparecchiature per uso professionale, del quale la stessa azienda diviene peraltro fornitore certificato. Ed è proprio quest’ultimo comparto a essere servito con continuità, attraverso la produzione e la fornitura di manufatti modulari, semilavorati e prodotti finiti per grandi impianti professionali, ovvero soluzioni per il lavaggio, la cottura e la refrigerazione. Una fattiva collaborazione in cui la soddisfazione del cliente va oltre l’ottimo rapporto qualità – prezzo e che porta l’azienda a essere una realtà riconosciuta e stimata, anche nel settore della realizzazione conto terzi.
«Gli importanti risultati operativi ottenuti – afferma il titolare Rudy Peruzzetto – hanno permesso di ampliare ulteriormente la nostra capacità produttiva, per un totale che oggi si attesta su 6.000 mq coperti, più altrettanti scoperti, suddivisi in 3 stabilimenti situati a San Polo di Piave, in provincia di Treviso».
L’espansione dell’azienda è stata sempre coerente con l’intrinseca propensione all’innovazione, sostenuta nel tempo da una forte etica di sviluppo compatibile (il nuovo capannone, per esempio, viene alimentato da fonti energetiche rinnovabili, tramite un impianto fotovoltaico dedicato). L’attenzione alla cura dell’ambiente è altresì perseguita attraverso la graduale sostituzione dell’intero parco machine con modelli sempre più funzionali ed eco-sostenibili. Parco macchine che oggi assicura un performante ed efficiente processo in cui tutte le tecnologie, dal taglio laser alla punzonatura, dalla piegatura alla pannellatura, al Sistema di stoccaggio automatico, sono fornite da Prima Power, Divisione Machinery del Gruppo Prima Industrie. Tra queste, le ultime forniture in ordine cronologico sono state la nuova pannellatrice Bending Center BCe 2720 e il magazzino automatico Night Train FMS, completo di robot di carico/scarico LU6, a supporto del taglio laser (impianti installati nel corso della prima parte di quest’anno).
Dal piccolo lotto alla produzione di serie
Astra lavora oggi in particolar modo per il settore ospedaliero/farmaceutico, per i grandi impianti e per il comparto navale. È invece un prodotto di propria produzione, nonché fiore all’occhiello per genio, semplicità ed efficienza (ideato e realizzato dallo stesso Rudy Peruzzetto) il filtro a labirinto per cappe industriali Sabik, dal quale emerge tutto il know-how e la capacità dell’azienda di poter affiancare il cliente nella realizzazione di un prodotto finito, al pari di altri innumerevoli articoli (cilindri sollevatori piatti e sollevatori cesti vassoi, carrelli di servizio, ecc.) in acciaio inox, oltre che in elettrozincato, alluminio o rame.
«Processiamo per circa l’80% acciaio inox – precisa Peruzzetto – e lavoriamo spessori normalmente fino a 5-6 mm, sebbene le nostre attrezzature permettano di arrivare anche oltre i 10 mm, coprendo tutta la filiera, dal semilavorato al prodotto finito. Siamo in grado di gestire con la stessa flessibilità 1, 10, 100, piuttosto che migliaia di pezzi».
In questo contesto la prima svolta produttiva si è avuta in azienda oltre una decina d’anni fa, con l’acquisto di una prima punzonatrice combinata dell’allora Finn Power, una SG8 1530 con cesoia angolare. Un’integrazione che ha più che triplicato la quantità di lamiera lavorabile fino a quel momento. Ulteriore e decisivo step di crescita è stato poi vissuto non più di un lustro fa, con l’introduzione di un performante impianto di taglio, un laser 2D a fibra sempre Prima Power, un Platino da 3 kW, completo di robot di pallettizzazione/impilaggio LST per la selezione automatica dei pezzi, e di una piegatrice elettrica eP 1030. Come già menzionato, risale invece a qualche mese fa l’installazione della nuova pannellatrice BCe 2720, quale up-grade di un impianto precedente, e del magazzino automatico Night Train FMS, completo di robot di carico/scarico LU6, a supporto dell’impianto di taglio laser.
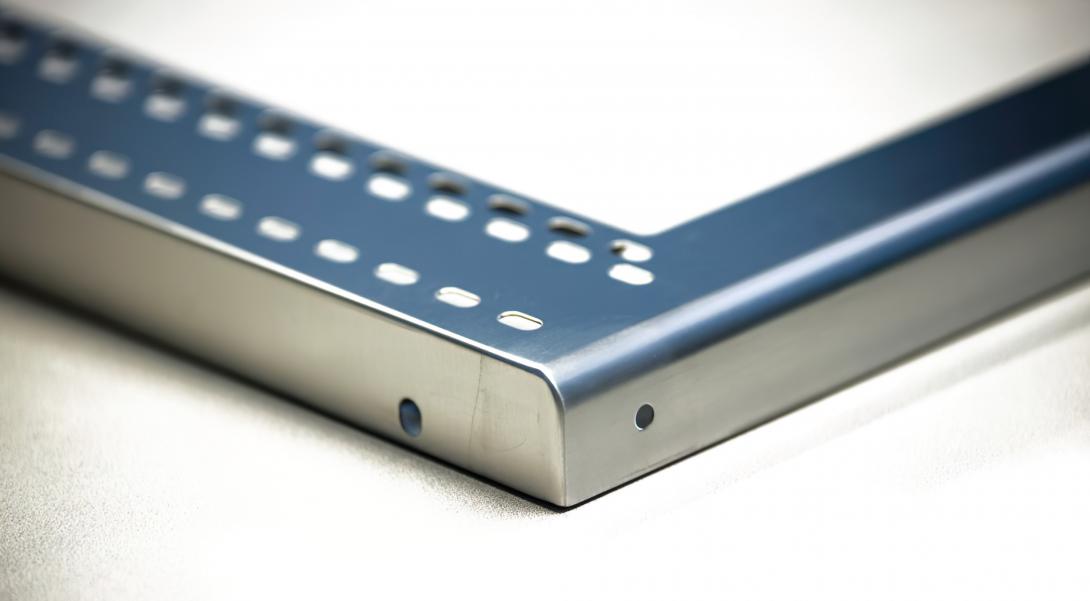
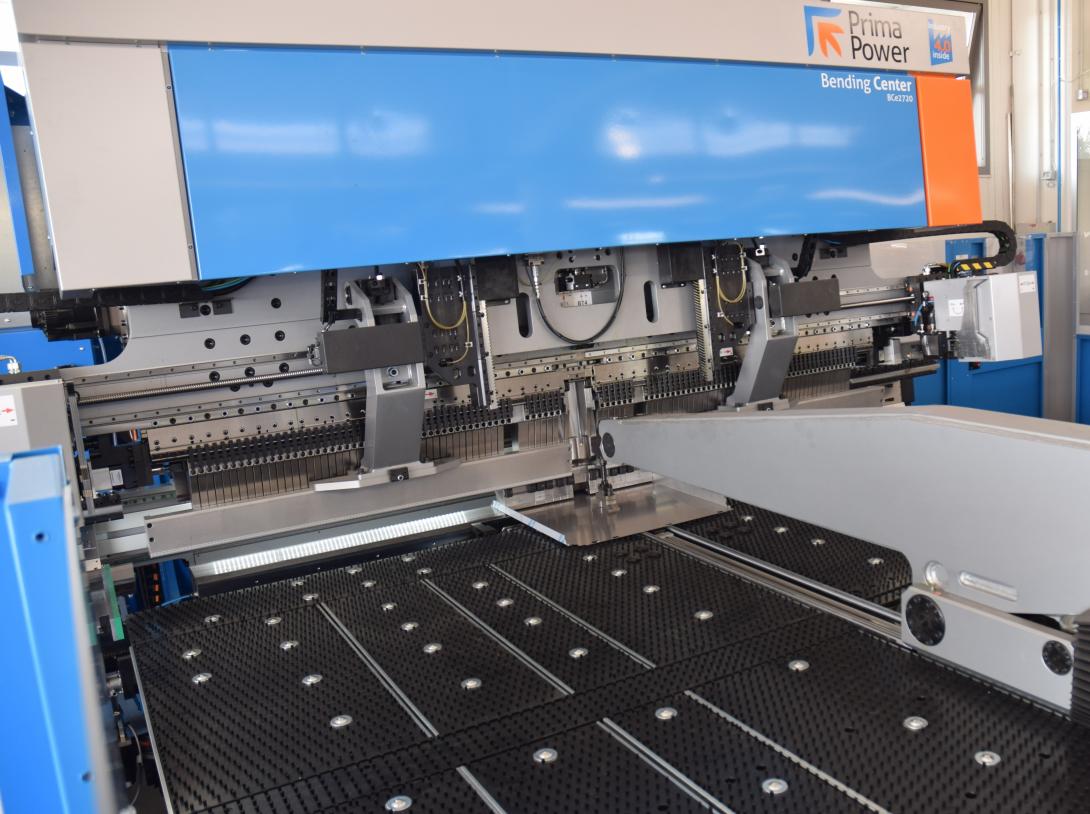
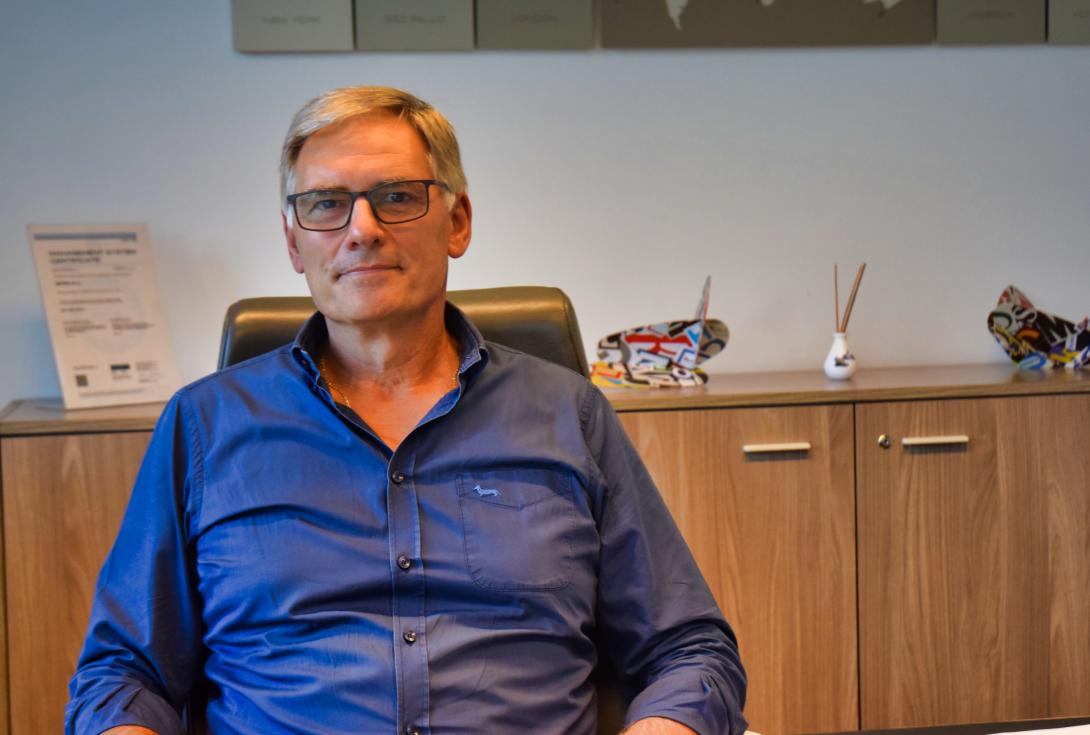
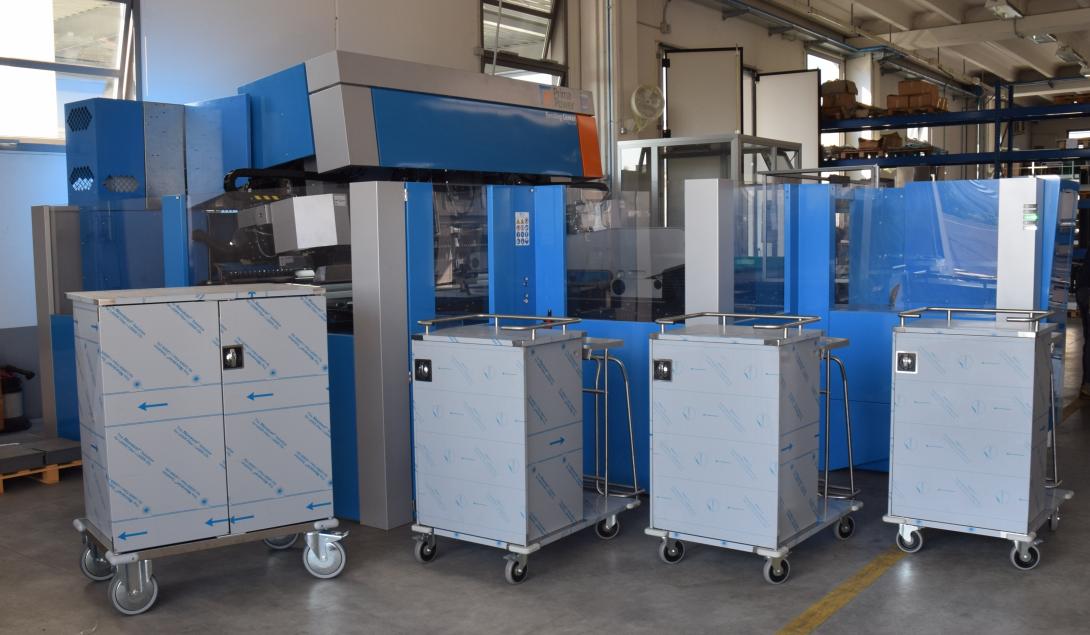
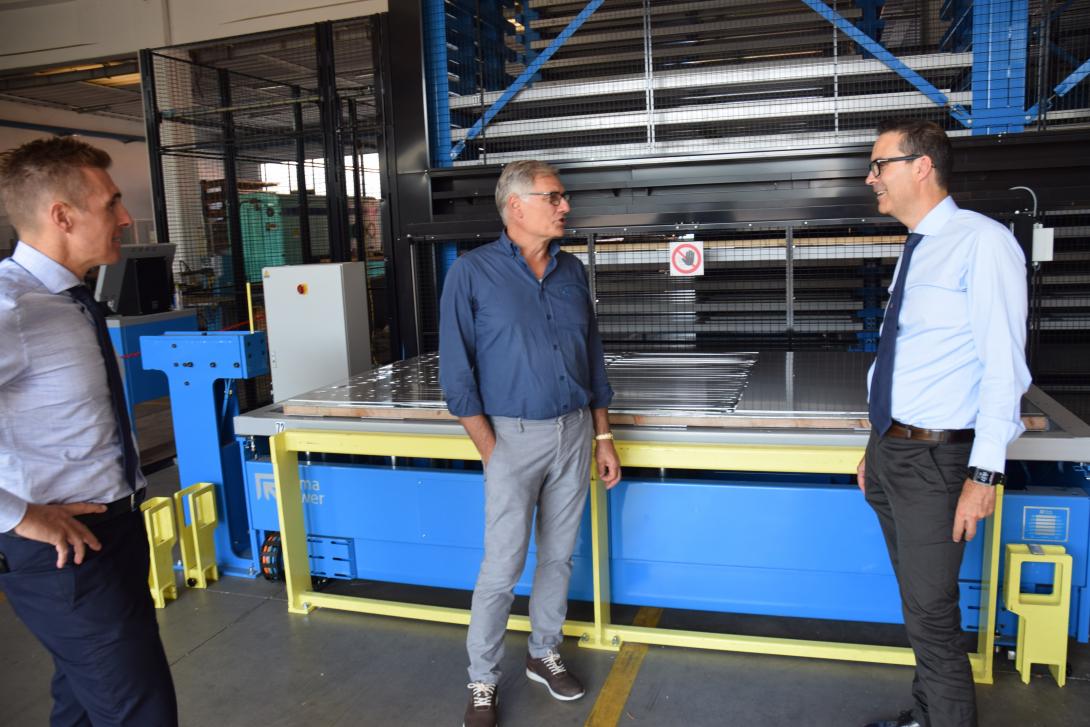
Centro di piegatura ad alta flessibilità e altrettanta produttività
Il centro di piegatura BCe di Prima Power offre la soluzione ideale per chi, come Astra, lavora pezzi singoli, piccoli lotti o produzione in serie. Questa pannellatrice si propone infatti di unire i ben noti benefici del prodotto pannellatrice, ovvero flessibilità, precisione ed elevata qualità, a un processo semi automatico ma altamente produttivo, dove la macchina è sempre in produzione grazie alla tavola di carico e scarico LUT che consente di caricare e scaricare i pezzi in tempo mascherato.L’alimentazione manuale inoltre consente la piegatura di parti non facilmente trasportabili con sistemi di carico automatici. La produzione di pezzi completamente forati, di forme lunghe o larghe, o parti che hanno aperture anche di grandi dimensioni all’interno, diventa dunque un’operazione assolutamente fattibile. Servoelettrica e dotata di 8 motori indipendenti e svariati assi a controllo numerico, la BCe 2720 permette di lavorare spessori da 0,5 a 3,2 mm di acciaio (fino a 2,2 mm di acciaio inox e fino a 4 mm di alluminio) e ha permesso all’azienda non solo di aumentare la lunghezza massima di piegatura da 2.250 mm del precedente impianto fino agli attuali 2.750 mm, ma anche di elevare il livello di automazione di processo. Molto apprezzato è anche il sistema AUT, acronimo di Auxiliary Upper Tools, ovvero un sistema di utensili ausiliari superiori che agevolano la fattibilità di pieghe particolari, dimostrando ulteriormente la flessibilità della macchina.
«La scelta di optare ancora per una nuova e più performante pannellatrice – motiva Peruzzetto – risiede nel fatto di aver maturato in quest’ultimo decennio la consapevole convinzione della grande difficoltà nel reperire personale qualificato, nella fattispecie piegatori. Una mancanza che pregiudica talvolta la visione futura dell’azienda o, per lo meno, ne modifica il percorso di crescita. Ho dunque scelto di puntare su una diversa tecnologia di piegatura, dove programmazione e automazione risultano la base solida della produttività.
Certamente la piegatrice al primo impatto può risultare più semplice da programmare, perché tecnologia più comune e conosciuta, e per le sue caratteristiche è in grado di processare anche pezzi che non sono fattibili in pannellatrice. Ma l’aver individuato il prodotto corretto e la nostra capacità progettuale nel modificare alcuni pezzi per renderli fattibili su questo macchinario ci hanno permesso di ottenere grossi benefici in termini di tempistica esecutiva, nonché di attrezzaggio nel rispetto della qualità attesa».
Una dotazione tecnologica che, a fronte delle più ampie geometrie lavorabili, ha ampliato per l’azienda in modo significativo il potenziale produttivo.
L’efficienza di processo parte (anche) dalla gestione della materia prima
Come già sottolineato, nel corso dell’anno la stessa Astra ha integrato al proprio interno anche il nuovo magazzino automatico Night Train FMS, completo di robot di carico/ scarico LU6, a supporto del taglio laser, sempre Prima Power. Un acquisto deciso dalla proprietà per ottimizzare la gestione della lamiera, che ormai da tempo ha superato i 1.000 quintali al mese, corrispettivi a circa 200 bancali in continuo assortimento e rotazione.
«Una mole troppo importante in ottica di efficienza – interviene Peruzzetto – rispetto alle risorse da impiegare per il reperimento e l’approvvigionamento della materia prima per il taglio laser, e alla dinamicità operativa a cui siamo chiamati a rispondere con la massima flessibilità».
Il nuovo magazzino automatico è stato collegato al software gestionale interno e, in ottica 4.0, tiene traccia di tutta la movimentazione. In altre parole, al carico della lamiera, viene aggiornata la disponibilità in tempo reale, azzerando di fatto possibili errori, sincronizzando con il gestionale ogni ora la reale presenza. Si tenga presente che il vasto portfolio clienti dell’azienda porta con sé la necessità di coordinare una gran moltitudine di formati di lamiera diversi, molti dei quali fuori standard, con tutte le difficoltà del caso.
«La bontà e il valore dell’investimento – osserva Peruzzetto – non ha tardato a palesarsi. Infatti, già dopo il primo mese di messa in servizio, la produzione del laser è quasi raddoppiata, minimizzando i tempi morti dovuti alla gestione della materia prima.
Quindi dal voler mettere ordine e tenere sotto controllo il materiale, si sono poi aggiunti dei benefici indiretti. Non ultimo il risparmio di spazio a pavimento prima occupato dai vari bancali di lamiera, in transito, oppure in attesa di essere sistemati». Grazie al robot di carico/scarico e al sistema di impilaggio, il nuovo FMS Prima Power può anche essere alimentato con semilavorati già tagliati, poi lavorabili in un secondo tempo, a seconda delle necessità.
«Migliorata – aggiunge Peruzzetto – è altresì la fase di nesting in quanto, in base alla nuova metodologia, è possibile inserire nello stesso job anche pezzi da tagliare non strettamente pertinenti la commessa, che possono momentaneamente essere“parcheggiati” nel cassetto (in uno dei vagoni disponibili), ottimizzando ulteriormente l’efficienza. In sintesi, il magazzino automatico è diventato cuore pulsante del flusso di lavoro al nostro interno. Una tecnologia che permette di contare anche su processi in continuo non presidiati».
Lavorare meglio per produrre di più
Il parco macchine presente in Astra (comprendente oltre agli impianti Prima Power anche alcune pressopiegatrici, oltre a celle di saldatura e celle di pulitura, compresa la pallinatura) consente di delineare e seguire l’intero processo di realizzazione del prodotto. L’eccellenza produttiva nasce proprio dalla stretta collaborazione tra professionalità del personale qualificato e l’avanguardia tecnologica, che consente di ridurre i tempi di produzione, migliorare i risultati operativi e, all’occorrenza, perfezionarli
«In questo contesto – conclude Peruzzetto – le più recenti integrazioni hanno permesso un aumento della produttività e dell’efficienza a parità di forza lavoro. Grazie al nuovo Night Train FMS possiamo oggi pianificare una produzione non presidiata su 3 turni, con sorting dei pezzi che al termine del turno stesso sono già impilati e pronti per le successive lavorazioni. Il mio obiettivo è quello di perseguire nell’adozione laddove è possibile di automazioni, per permettere al personale di lavorare meglio aumentando nel contempo la nostra capacità produttiva».
Una ricerca di maggiore efficienza competitività confermata da nuovi progetti in via di sviluppo, che in futuro porteranno al collegamento di altri impianti al magazzino automatico.
“Un particolare ringraziamento alla mia famiglia, anch’essa presente in azienda, e all’intero staff di dipendenti e collaboratori per l’impegno profuso e per aver contribuito a mantenere alti i nostri standard qualitativi, rendendo possibili gli ottimi risultati ottenuti.”
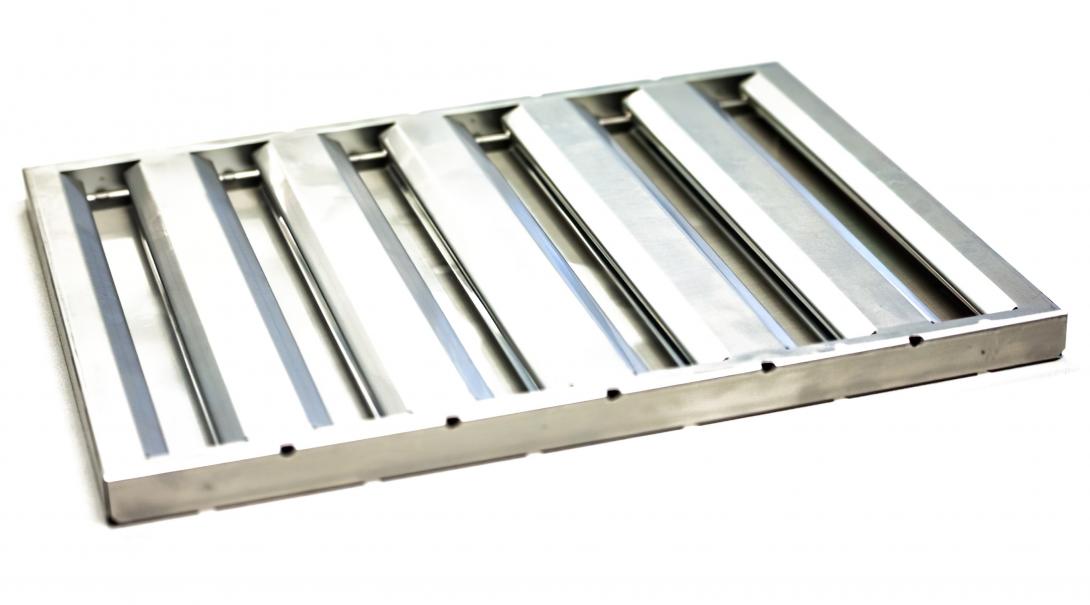
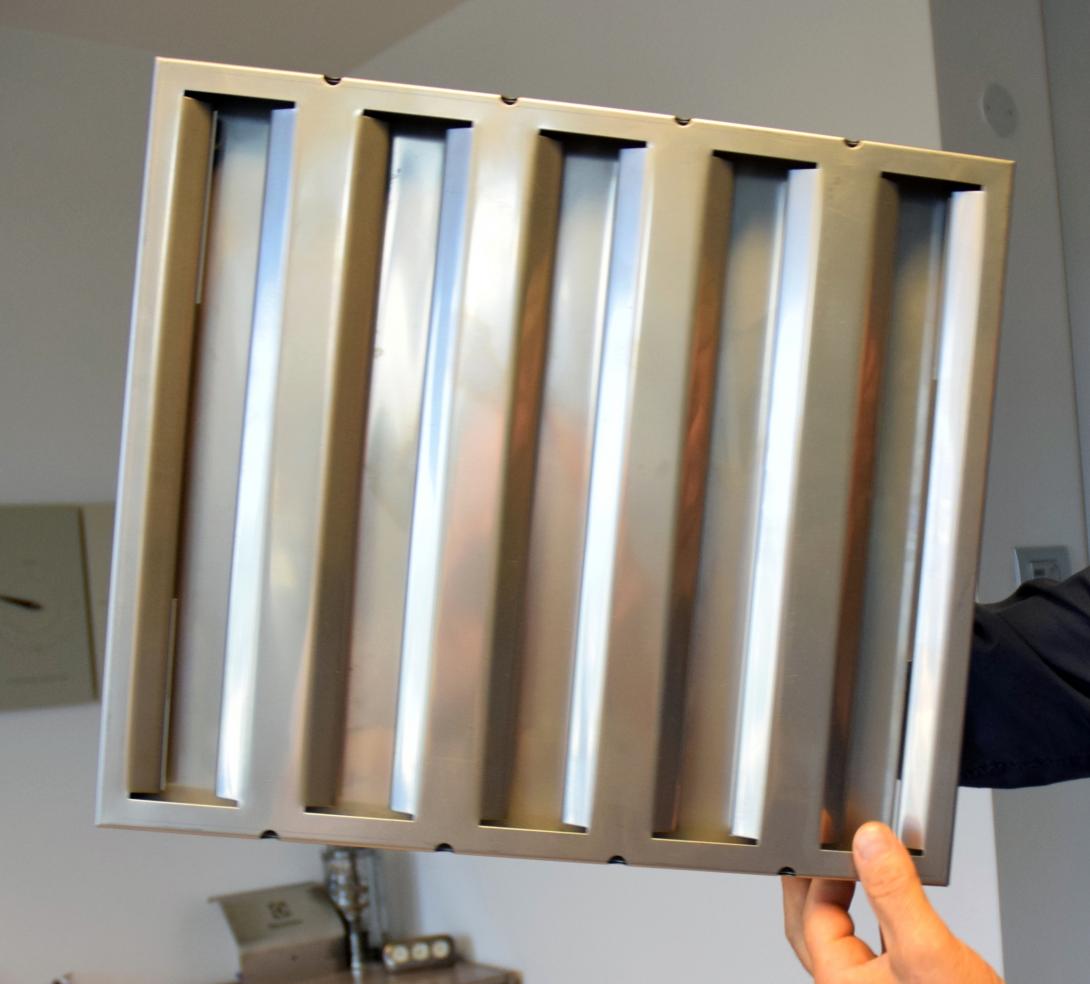
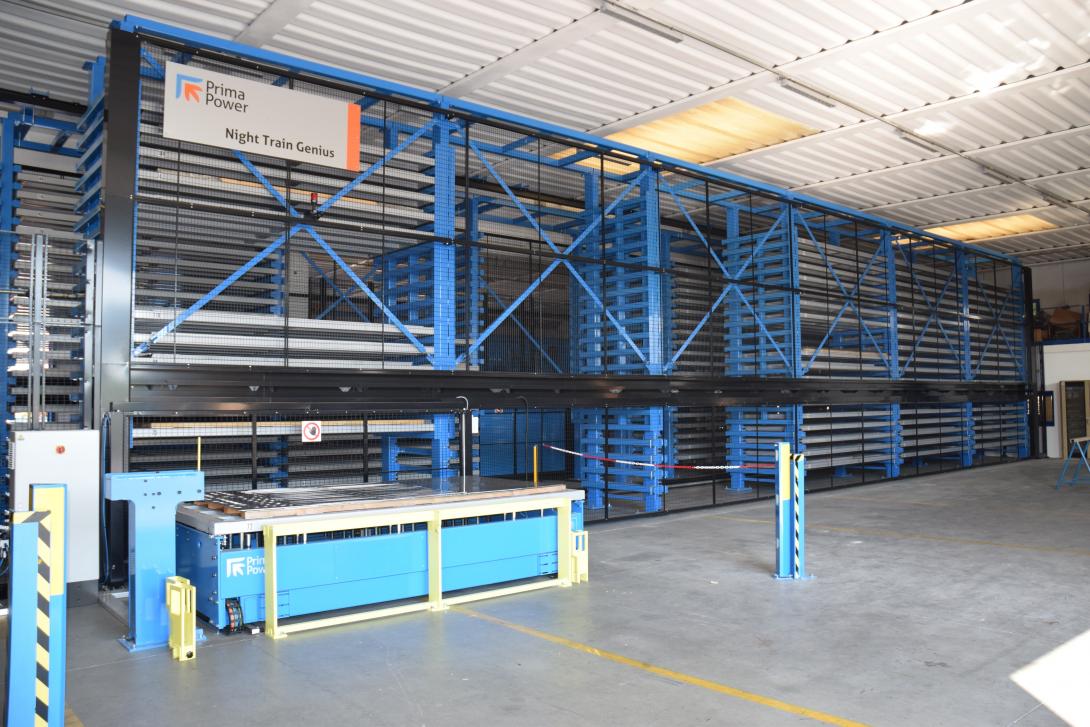
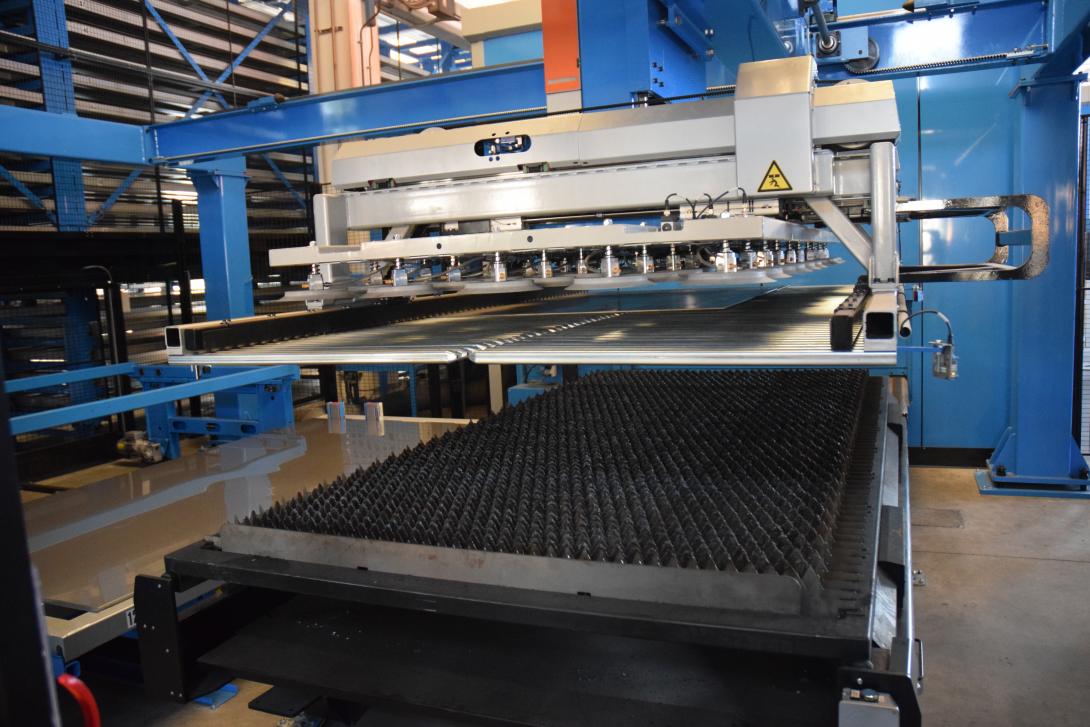
L’automazione al passo con una produzione flessibile, e viceversa
Night Train FMS di Prima Power rende automatica la gestione del materiale e delle relative informazioni, combinando singoli processi produttivi in un unico percorso flessibile. Per come è pensato e strutturato, il sistema consente di ottenere maggiore efficienza dei costi e flessibilità nella fabbricazione dei pezzi e si adatta perfettamente sia alla produzione di piccoli lotti, sia a quella di serie. Il concetto del sistema modulare consente di costruire e strutturare il progetto in accordo ai requisiti specifici dello stabilimento in cui viene installato. Nel caso dell’azienda veneta, la configurazione scelta, a supporto (per il momento) dell’impianto di taglio laser a fibra, è stata quella di optare per 12 unità di magazzino, ciascuna alta poco meno di 6 m e componibile con un massimo di 24 cassette (per 3 ton di materiale o componenti impilati stoccabili per ogni cassetta). Sono dunque 288 le cassette teoriche, contro le 150 attualmente impiegate. Punto di forza del sistema è infatti la possibilità di adattarsi nel tempo alle mutabili esigenze produttive: celle, singole macchine, stazioni di lavoro possono essere aggiornate, cambiate o aggiunte, e la capacità di magazzino ulteriormente espansa.
Articolo pubblicato sulla rivista LAMIERA – novembre 2020
La bontà e il valore dell’investimento non ha tardato a palesarsi. Infatti, già dopo il primo mese di messa in servizio, la produzione del laser è quasi raddoppiata, minimizzando i tempi morti dovuti alla gestione della materia prima.
Stai cercando una soluzione simile per la tua azienda? Ecco qui
Platino Fiber
CORTE A LASER 2D
Rentável para uma mistura de produção que inclui todos os materiais e espessuras
Night Train FMS®
SISTEMI DI PRODUZIONE FLESSIBILI