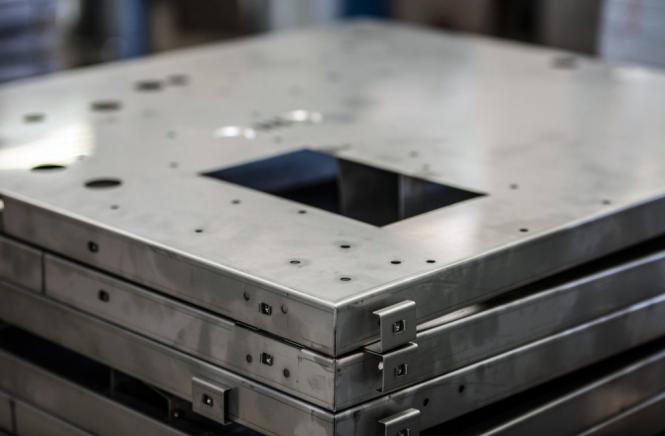
Order and efficiency drive productivity, from first cut to finished product
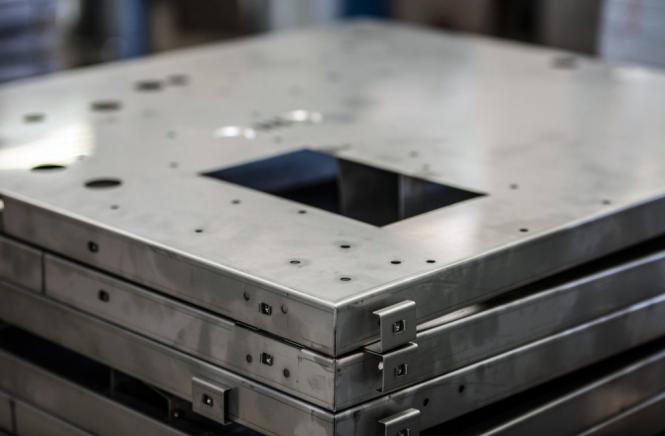
Astra was founded just short of thirty years ago as the result of an innovative instinct which proved successful in just a few years: that stainless steel would become the technological material of the future.
Today it is processed and shaped by a productive and efficient system in which each of the operational phases, from laser cutting, punching, bending, panelling, right up to its automatic storage (the heart of the process) are taken care of by Prima Power.
Astra specialises in the design and processing of metal carpentry producing mainly stainless steel components ranging from semi-finished to finished products. Established in 1991, the company has always aimed to meet the highest levels of quality required while following the foresight of founder Rudy Peruzzetto, who identified that stainless steel would become the technological material of the future. On this basis, resources and skills were immediately directed towards demanding sectors such as the hospital and pharmaceutical industry, and in 1997 production was expanded for the first time. In the same year, a partnership also began with large multinational group, Electrolux Professional, a global leader in household appliances and equipment for professional use for which Astra also became a certified supplier. And it is precisely the professional sector that it continues to serve through the production and supply of modular, semi-finished and finished products used in large professional installations, or washing, cooking and refrigeration solutions. This is an effective collaboration in which customer satisfaction goes beyond the excellent quality/price ratio and for which the company is recognized and respected, even in the area of third-party construction.
"The significant operating results we’ve achieved,” says owner Rudy Peruzzetto, “have allowed us to further expand our production capacity to a total that today stands at 6,000 indoor square meters and just as much outdoor space divided between 3 plants in San Polo di Piave, in the province of Treviso.”
Expansion of the company has always paralleled its inherent tendency towards innovation, supported over time by the strong ideal of sustainable development (for example, the new warehouse is powered by renewable energy sources via a dedicated photovoltaic system). Particular care for the environment is also seen through the gradual replacement of the entire fleet of machines with increasingly functional and eco-friendly models. This very fleet today ensures a high-performance and efficient production process in which all technologies, from laser cutting to punching, bending, panelling, right up to the automatic storage system, are all supplied by Prima Power, the Machinery Division of the Prima Industrie Group. Among these, the latest additions in chronological order were the new BCe 2720 Bending Center and the Night Train FMS automatic storage system complete with LU6 loading/unloading robot to support laser cutting (these systems were installed in early 2020).
From small batches to mass production
Today, Astra works for the hospital/pharmaceutical sector in particular, as well as for large installations and the naval sector. The labyrinth filter for Sabik industrial hoods is its own product, as well as a benchmark for ingenuity, simplicity and efficiency (ideated and created by Rudy Peruzzetto himself), which demonstrates the know-how and ability of the company to support the customer in creating a finished product, like countless other items (plate lifting cylinders and tray lifters, service trolleys, etc.) in stainless steel, as well as in galvanized steel, aluminium or copper.
“About 80% of what we process is stainless steel,” specifies Peruzzetto, “and we normally work with thicknesses up to 5-6mm, although our equipment allows us to process even over 10mm, which covers the entire supply chain, from semi-finished products to the finished product. We are able to manage 1, 10 or 100 pieces with the same flexibility as thousands of pieces.”
In this regard, the first production breakthrough occurred in the company over a decade ago with the purchase of the first combined punching machine, an SG8 1530 with angle shear, from the then Finn Power. This integration more than tripled the amount of sheet metal that could be processed up to that time. A further decisive step was taken about a decade ago with the introduction of a high-performance laser cutting system, a Prima Power 2D fiber laser, a 3 kW Platino complete with LST palletising/stacking robot for automatic selection of pieces, and an EP 1030 electric panel bender. As already mentioned, the most recent installation of the BCe 2720 panel bender took place only a few months ago as an upgrade to the previous system, together with the Night Train FMS automatic storage system that includes a LU6 loading/unloading robot to support laser cutting.
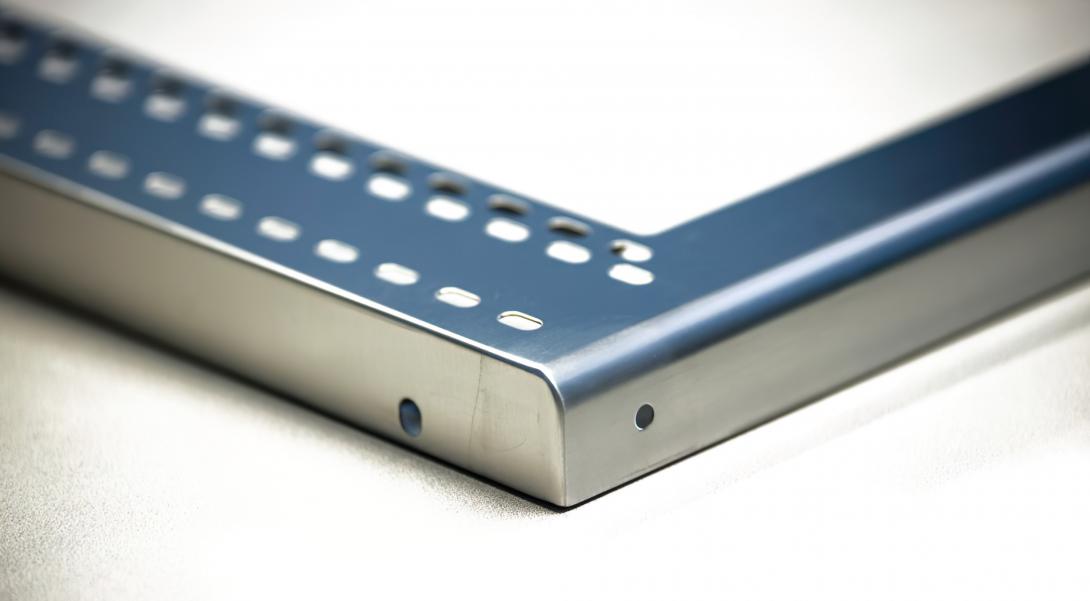
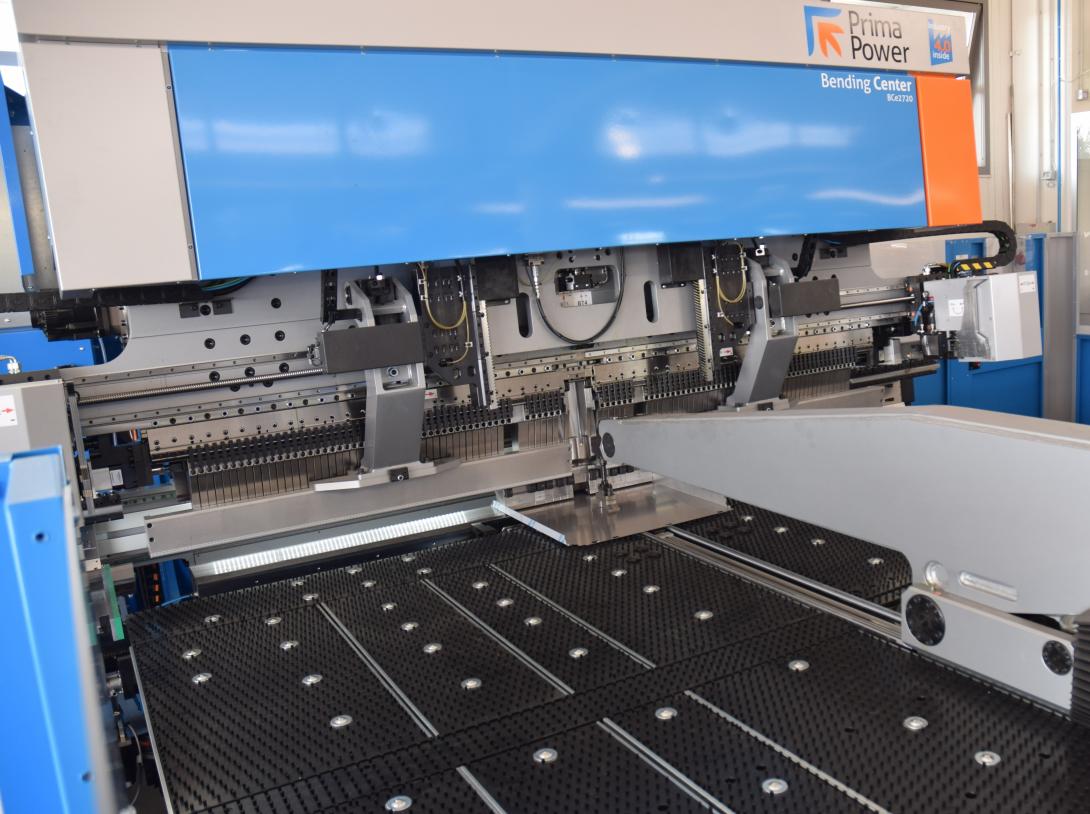
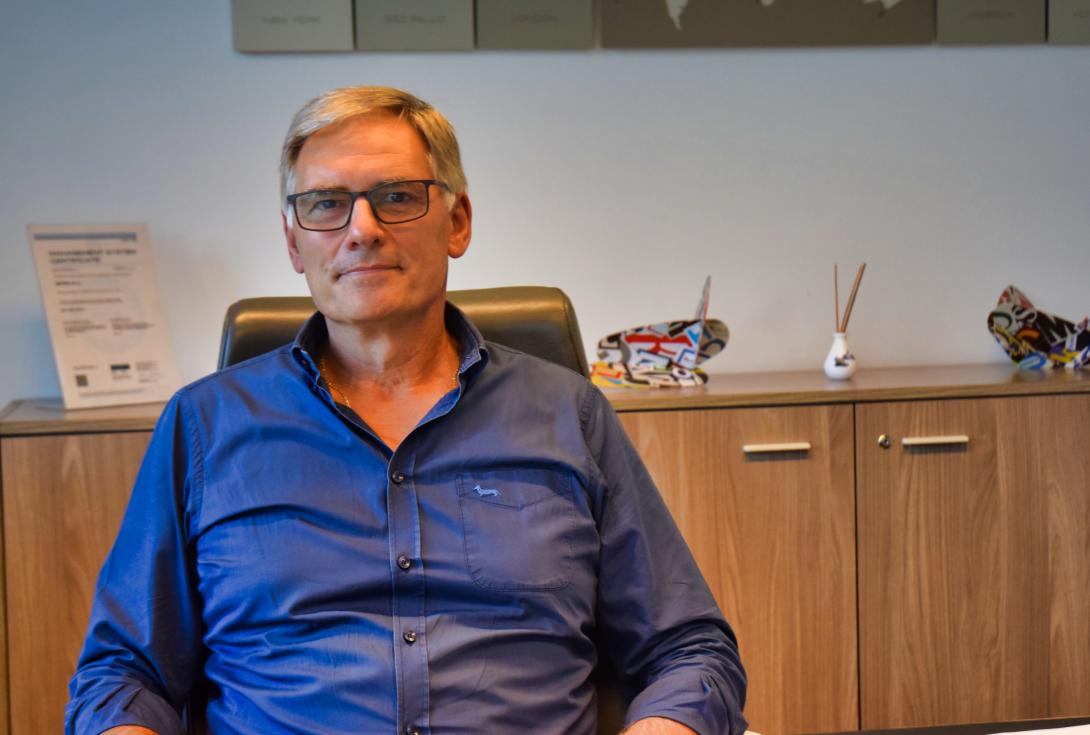
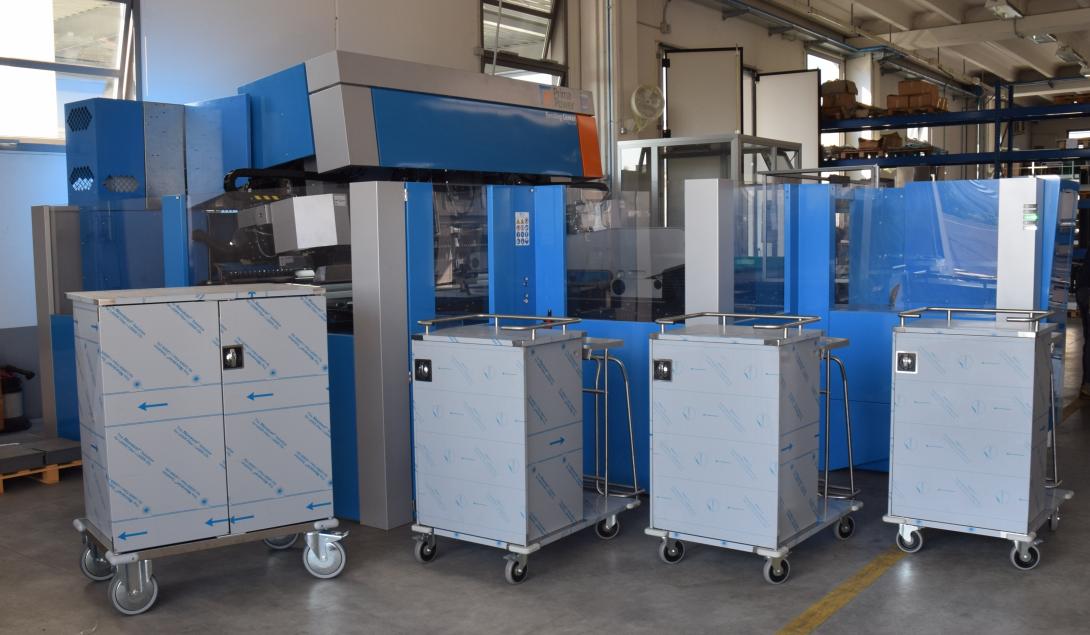
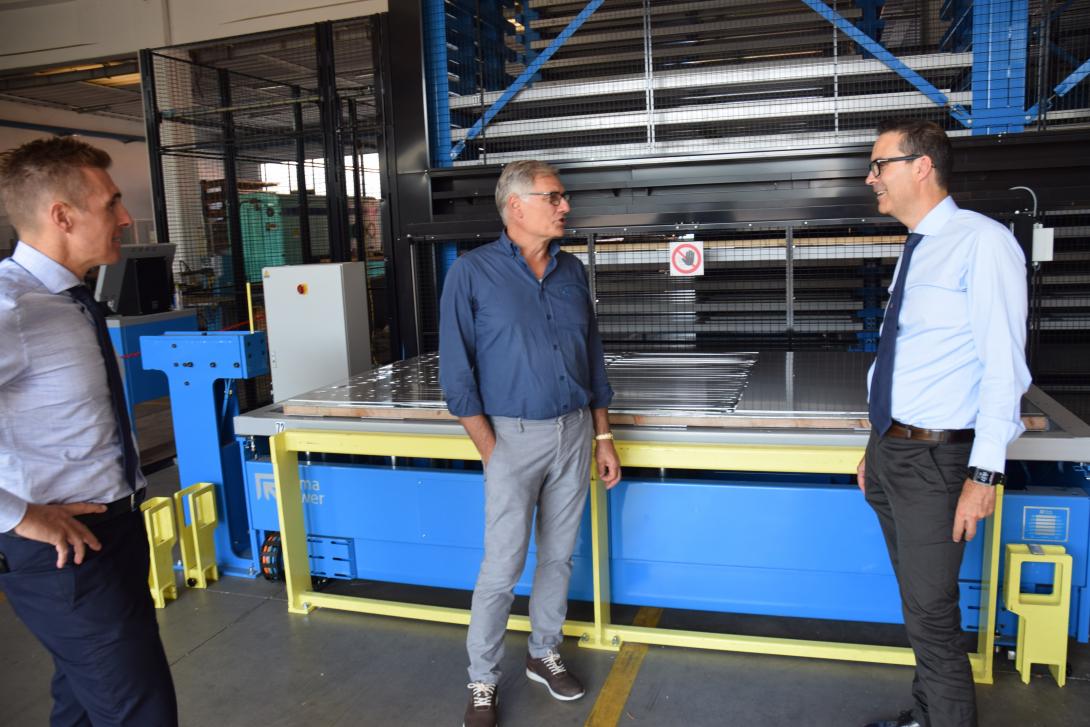
Highly flexible bending center with the same productivity
Prima Power's BCe bending center offers the ideal solution for those who, like Astra, deal with single pieces, small batches or mass production. In fact, this panel bender aims to combine the well-known benefits of the panelling product, i.e. flexibility, precision and high quality, with a semi-automatic but highly productive process where the machine is always running thanks to the LUT loading and unloading table that allows piece loading and unloading during operation. Manual feeding also allows bending of pieces that are not easily transported via automatic loading systems. The production of fully perforated pieces, long or wide shapes, or even parts that have larger inner openings thus becomes completely feasible. Servoelectric and equipped with 8 independent motors and several CNC axes, the BCe 2720 allows you to process thicknesses of 0.5 up to 3.2mm of steel (up to 2.2mm of stainless steel and up to 4mm of aluminium). This has also allowed the company to increase both the maximum bending length of the previous system from 2,250mm to the current 2,750mm, as well as to raise the level of process automation. The AUT (Auxiliary Upper Tools) system is also highly valued. This is a system of upper auxiliary tools that help perform particular bends, further demonstrating the flexibility of the machine.
“Our decision to opt for a new and higher performing panel bender,” Peruzzetto explains, “is based on our conscious belief and experience over the last decade of just how difficult it is to find specially qualified personnel, in this case for panel bending machines. This skills shortage can occasionally jeopardize the company's future vision or, at least, change its growth path. I therefore chose to focus on a different bending technology, where programming and automation are the basis of productivity. At first glance, the bending machine is certainly easier to program because it is a more commonly-known technology and, due to its characteristics, you can even process pieces that wouldn't be possible with a panel bender. But identifying the correct product and our design ability to adjust certain pieces to make processing them possible on this machine have allowed us to obtain great benefits in terms of execution time, as well as tooling to achieve the expected quality.”
This technological equipment has significantly expanded the production potential for the company, which can now process larger formats.
Process efficiency (also) starts from management of the raw material
As already highlighted, Astra also integrated the new Night Train FMS automatic storage system, complete with LU6 loading/unloading robot to support laser cutting, and once again this was provided by Prima Power. The owners decided on this investment in order to optimise sheet metal management, which has exceeded 100,000 kilograms per month for some time now, equalling about 200 pallets in continuous assortment and rotation.
“This is too large an amount in terms of efficiency,” says Peruzzetto, “compared to the resources required for locating and the procurement of the raw material for laser cutting, and the operational dynamics to which we have to respond with maximum flexibility.”
The new automatic storage system has been linked to the internal management software and keeps track of all movements from a 4.0 perspective. In other words, once the sheet is loaded, its availability is updated in real time, while effectively removing any errors and synchronising the actual presence each hour with management software. It should be borne in mind that the company's vast customer portfolio brings with it the need to coordinate a multitude of different sheet metal formats, many of which are not standard and entail many intricacies.
“The effectiveness and value of the investment,” observes Peruzzetto, “didn’t take long to show itself. In fact, in the first month after commissioning, laser production has already almost doubled, while also minimising downtime due to the management of raw materials. So the need to create order and keep the material under control brought with it additional indirect benefits. Last but not least, we also saved floor space that was previously occupied by the various pallets of sheet metal, either in transit, or waiting to be processed.”
Thanks to the loading/unloading robot and the stacking system, the new Prima Power FMS can also be fed with pre-cut semi-finished products, which can then be processed at a later stage, as required.
“The nesting phase has also been improved,” adds Peruzzetto, “since the new methodology allows you to include pieces to be cut in the same batch that are not strictly relevant to the order, but these can be temporarily ‘stored’ in the cassette (in whichever wagon is available), further optimising efficiency. In short, the automated storage has become the beating heart of our internal workflow. This technology allows you to rely on continuous unsupervised processes.”
Work better to produce more
The fleet of machines at Astra (which in addition to the Prima Power machines, includes other press brakes, as well as welding and cleaning cells, and shot peening) allows the entire manufacturing process to be delineated and closely monitored. Production excellence arises precisely from the close collaboration between the professionalism of qualified personnel and cutting-edge technology, allowing for reduced production times and improved operational results which can then be perfected, if necessary.
“In this set up,” concludes Peruzzetto, “the most recent additions have brought about an increase in productivity and efficiency with the same workforce. Thanks to the new Night Train FMS, we can now plan unmanned production over 3 shifts, while sorting the pieces that are already stacked at the end of the shift and ready for further processing. My goal is to pursue automation wherever possible, to allow staff to work better while increasing our production capacity.”
This search for greater efficiency and competitiveness is reaffirmed by new projects under development which will connect other systems to the automatic storage in the future.
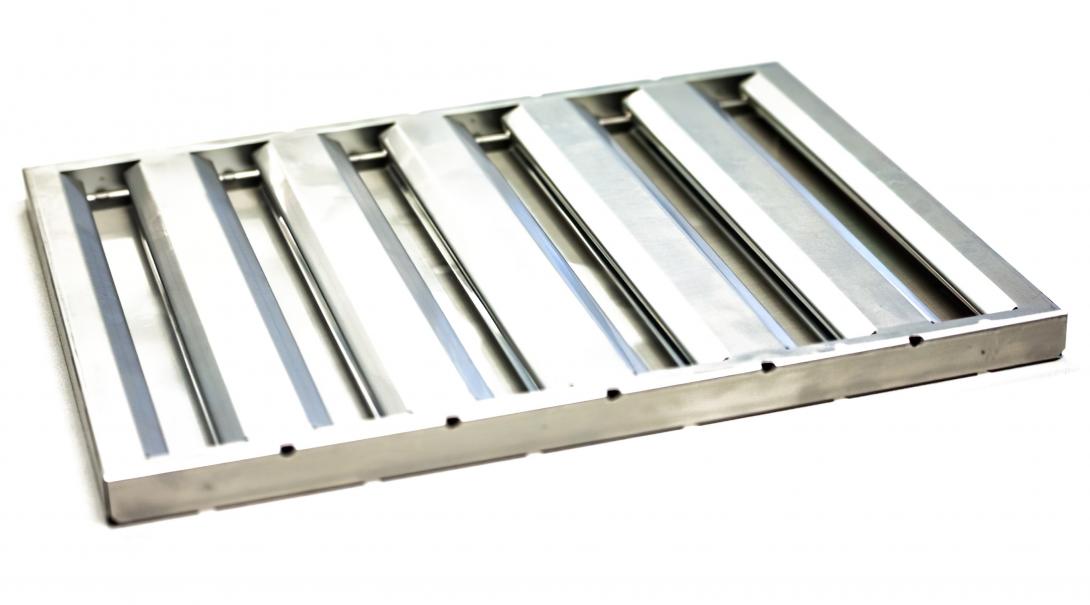
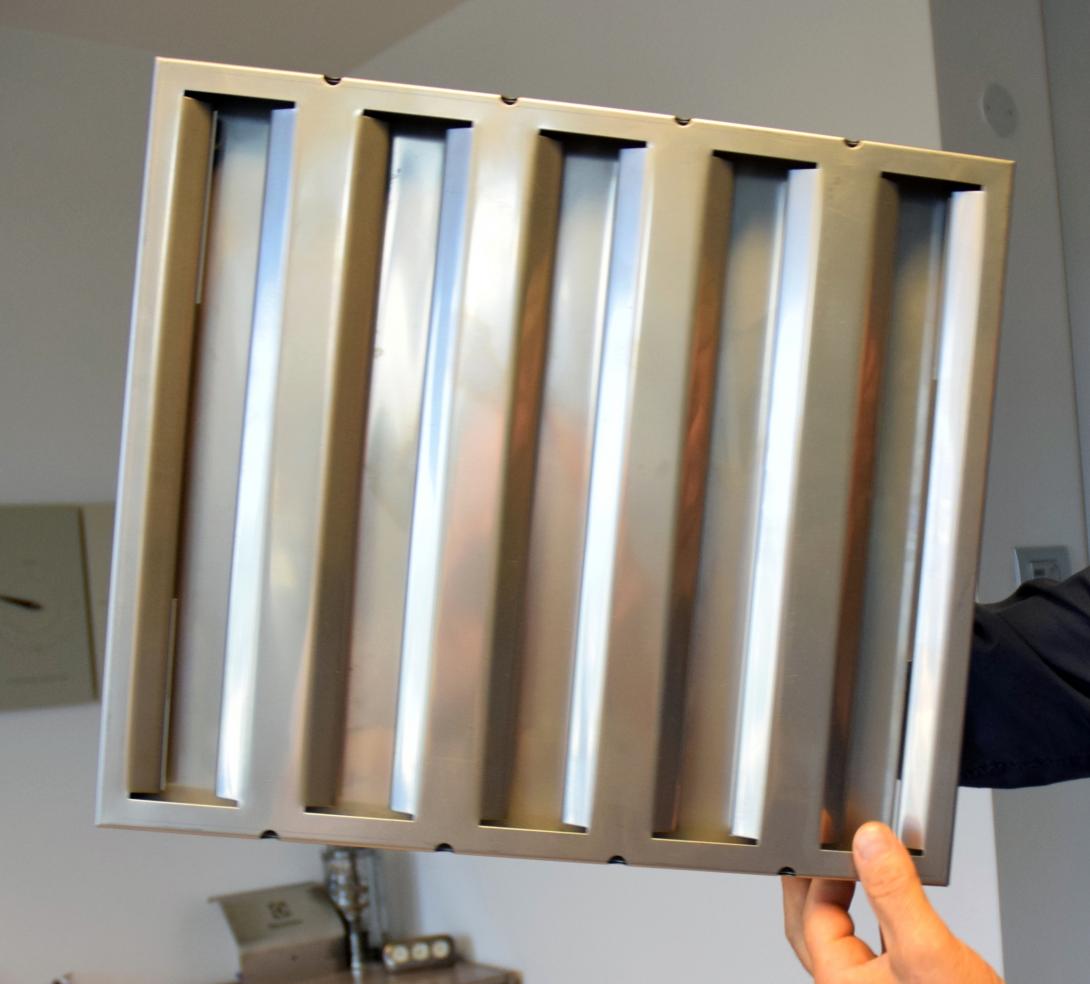
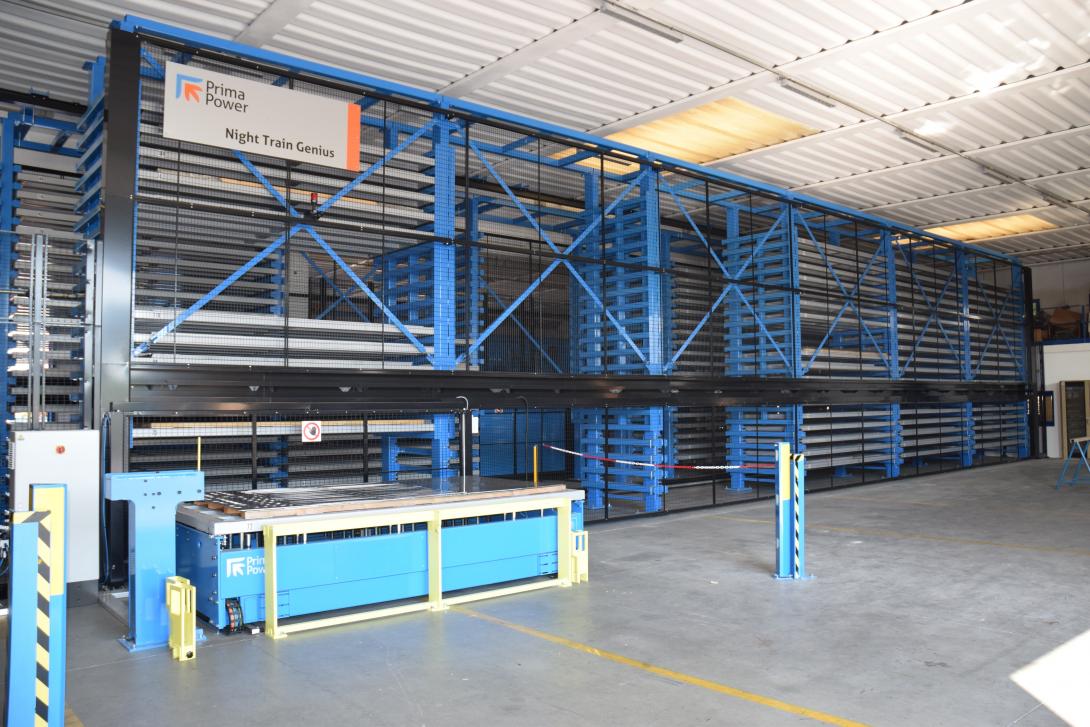
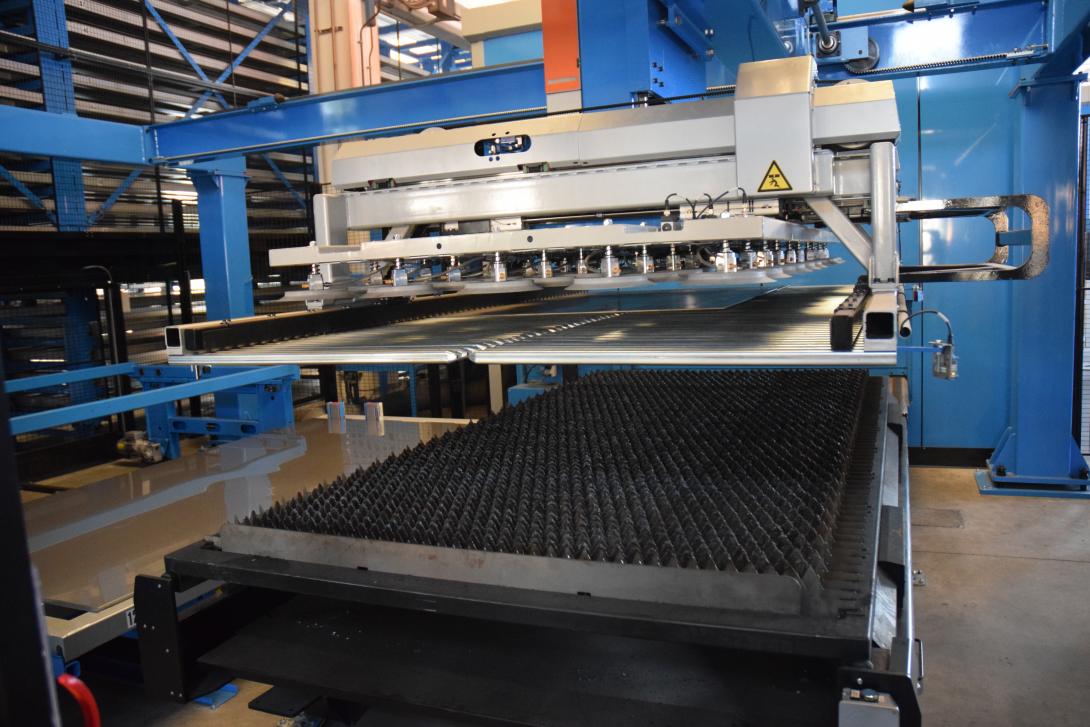
Hood filters for those with high aspirations
Sabik industrial hood filters are exclusively designed and created in pure 304 2B 6/10 stainless steel by Astra. They are characterised by finer details that allow fumes to be conveyed, condensed and expelled in the most appropriate way, while more substantial elements, such as grease, are collected. The structure of the filter has been specifically designed to minimise the use of the dust collector unit thanks to the application of simple physics. A system of wider cups, the internal angle of 141°/90° and the structure all allow reduced suction power while also increasing the cubic meters absorbed every hour. In this way, management costs are drastically reduced. This advanced yet very simple system also makes cleaning and maintenance easier, ensuring longer service life and consistent high performance. Precision and aesthetics are both guaranteed by the quality of the process in which Prima Power technologies are used, alongside the usual operating methodology followed by Astra staff: this synergy makes the product one of a kind.
Sabik is the hoods filter exclusively designed and manufactured by Astra, in pure 304 2B 6/10 stainless steel.
Automation alongside flexible production, and vice versa
Prima Power's Night Train FMS automates the management of materials and related information, combining individual production processes in a single flexible line. The way the system is designed and structured allows for greater cost efficiency and flexibility in the manufacturing of parts and is perfectly suited to both small batch and serial production. The modular system allows you to build and structure the project according to the specific requirements of the system in which it is installed. In the case of the Veneto company, the chosen configuration to support (for the moment) the fiber laser cutting system was to opt for 12 storage units, each modular and just under 6m high with a maximum of 24 cassettes (allowing 3 tons of material or stacked components to be stored in each cassette). This gives 288 theoretical cassettes, against the 150 currently used. The main strength of the system is the ability to adapt over time to changing production needs: cells, individual machines, workstations can all be updated, changed or added, and storage capacity can be further expanded.
Prima Power's Night Train FMS has allowed Astra to structure the management of raw materials, as well as freeing up floor space and making the laser cutting process and its production line generally more efficient.
The effectiveness and value of the investment,” observes Peruzzetto, “didn’t take long to show itself. In fact, in the first month after commissioning, laser production has already almost doubled. Last but not least, we also saved floor space
Are you looking for a similar solution for your company? Find it here
BCe Bending Centre
PANEL BENDERS
Flexibility at your service semi automatic panel bender combining flexibility and productivity
Night Train FMS®
FLEXIBLE MANUFACTURING SYSTEMS