
Bending

Product families
More productive machines, new automation solutions and suites of user-friendly options are designed to meet your actual needs. To offer the best Prima Power technology, our team of experts will always be there to listen, assist and advise. We strongly believe in the "Next to You!" principle.
Discover how Prima Power’s Bending technology can help you optimize your production
Panel Benders
In panel benders, the bending work is done by the blades, while the sheet press holds the sheet in place during the operation. The blades can then perform different types of folds, upwards or downwards, starting with the outermost folds of a side, before automatically executing the sequence towards the innermost fold. All of these movements are controlled by electric servo drives that guarantee maximum positioning accuracy in the bending trajectory, thus ensuring an optimal result.
Choose the perfect Panel Bender for you
A wide range of bending solutions to meet all the different production requirements.Prima Power’s Panel Bender range meets offers extremely flexible solutions, with servo-electric semi-automatic or fully automatic machines configured as stand- alone cells or multi-technology lines.
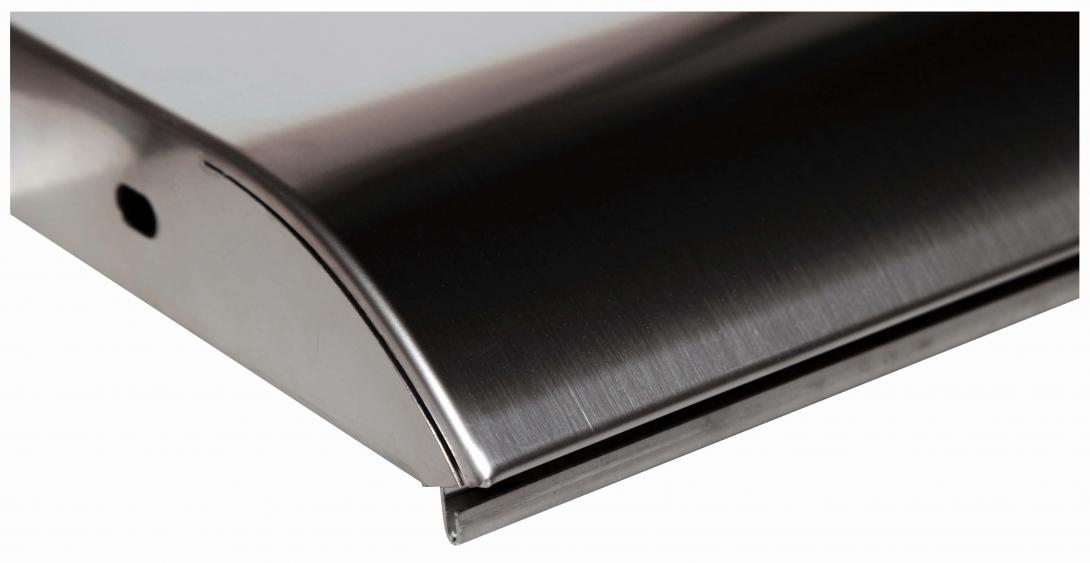
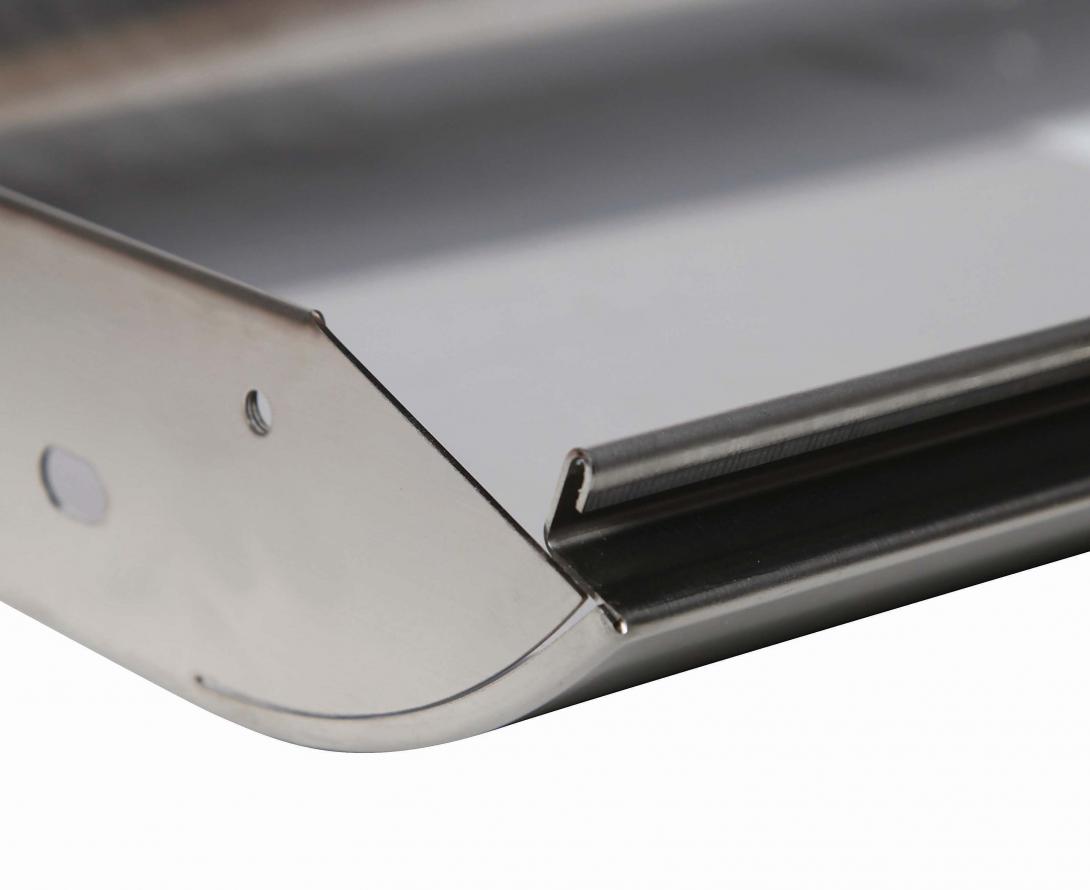
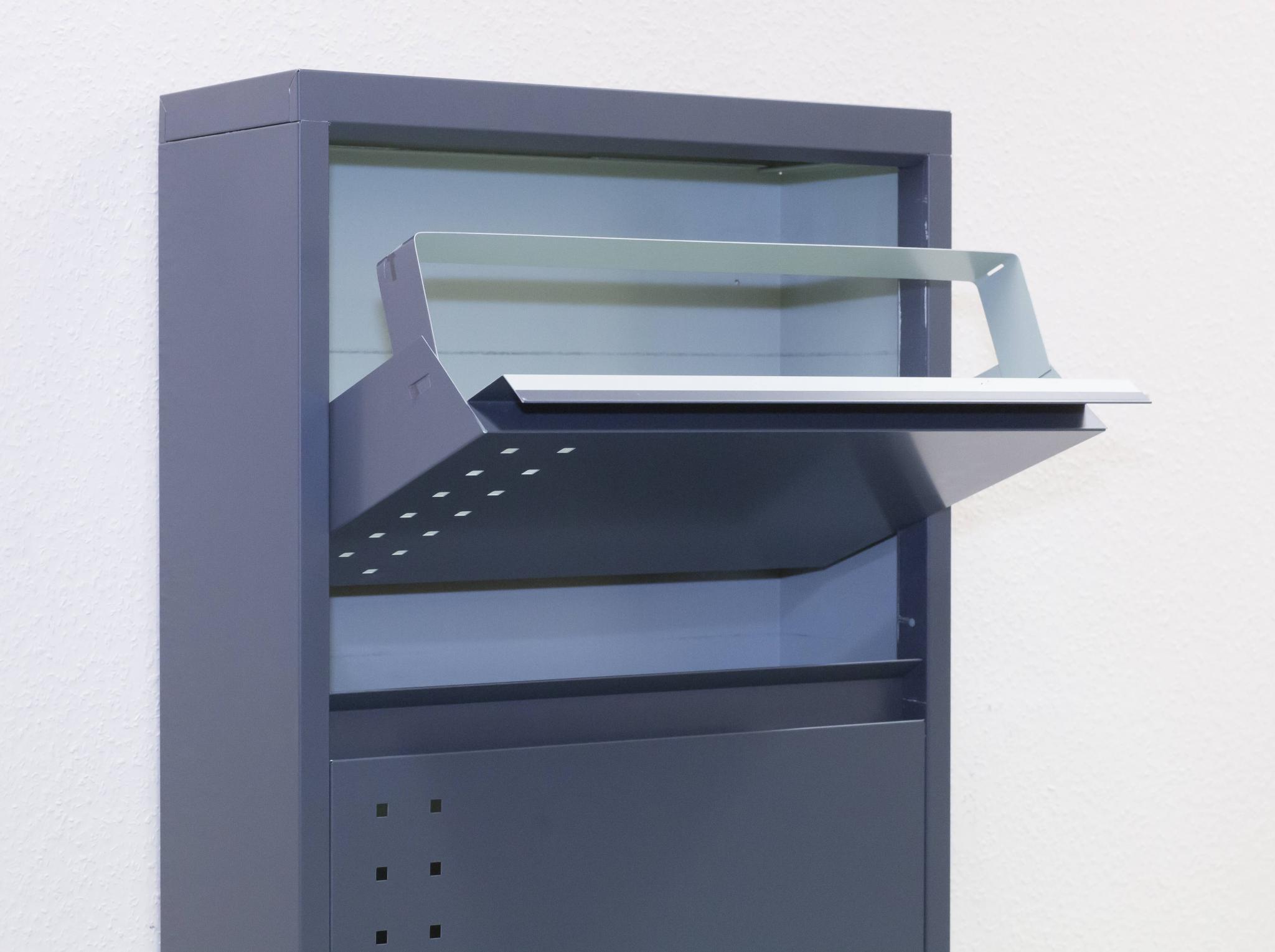
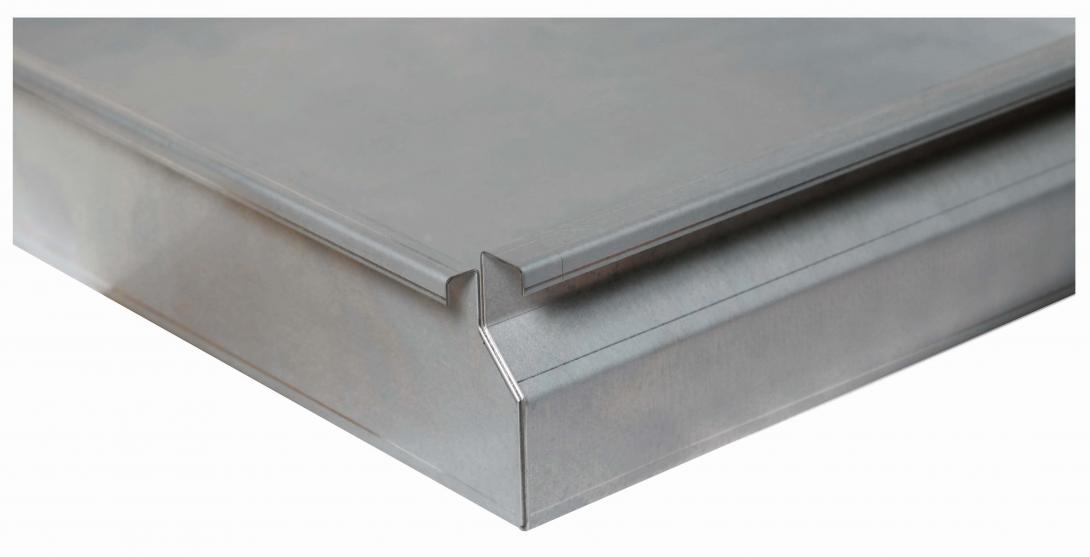
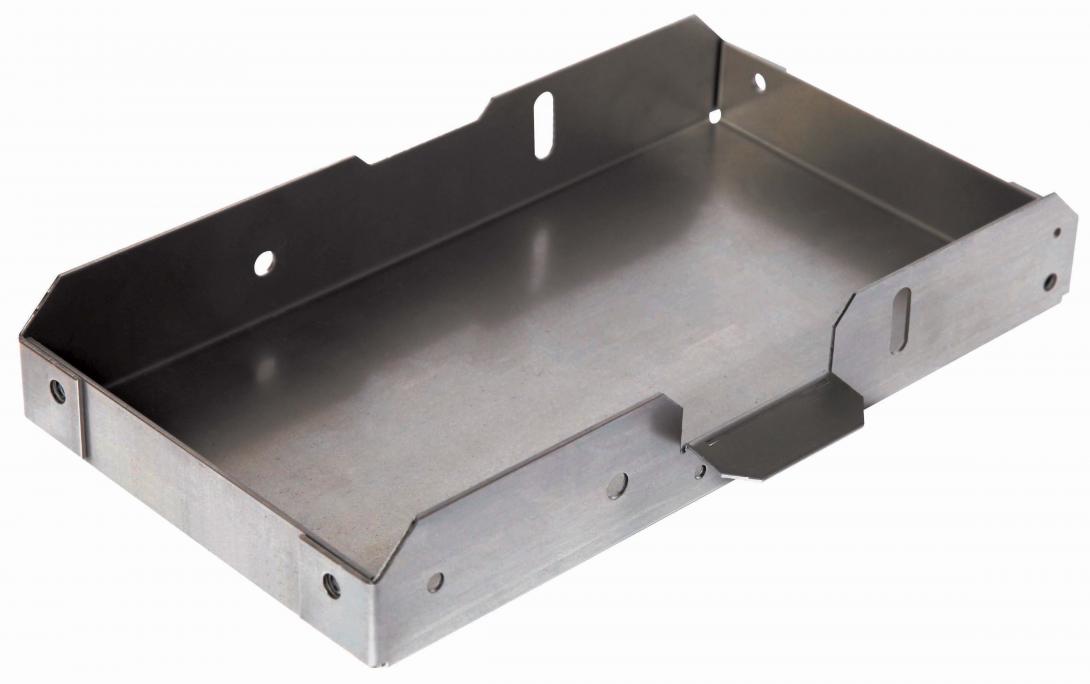
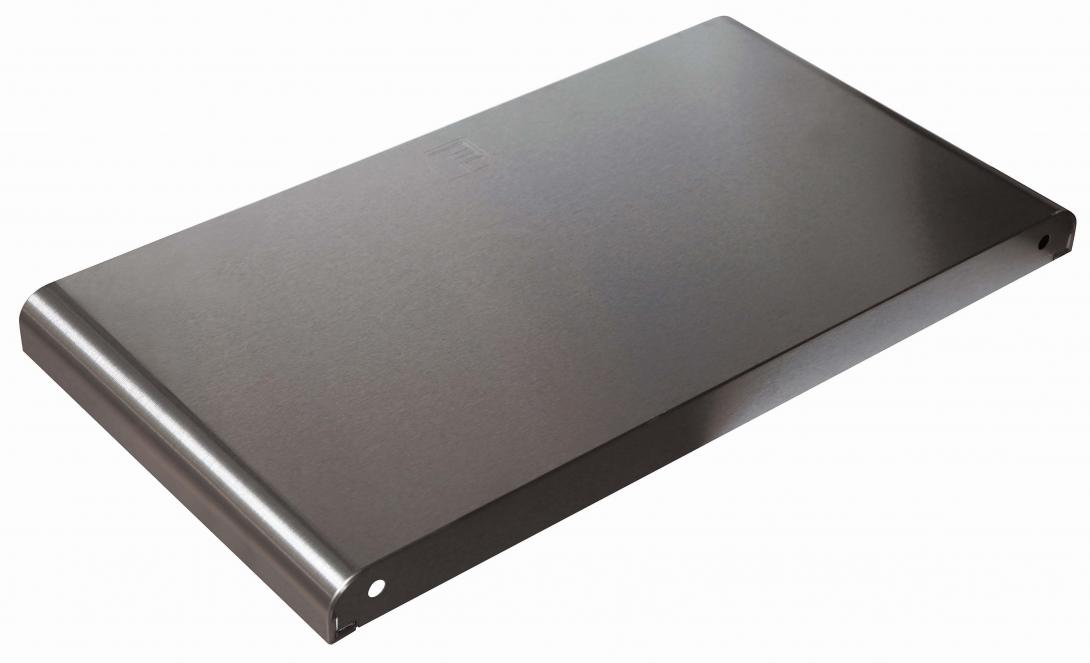
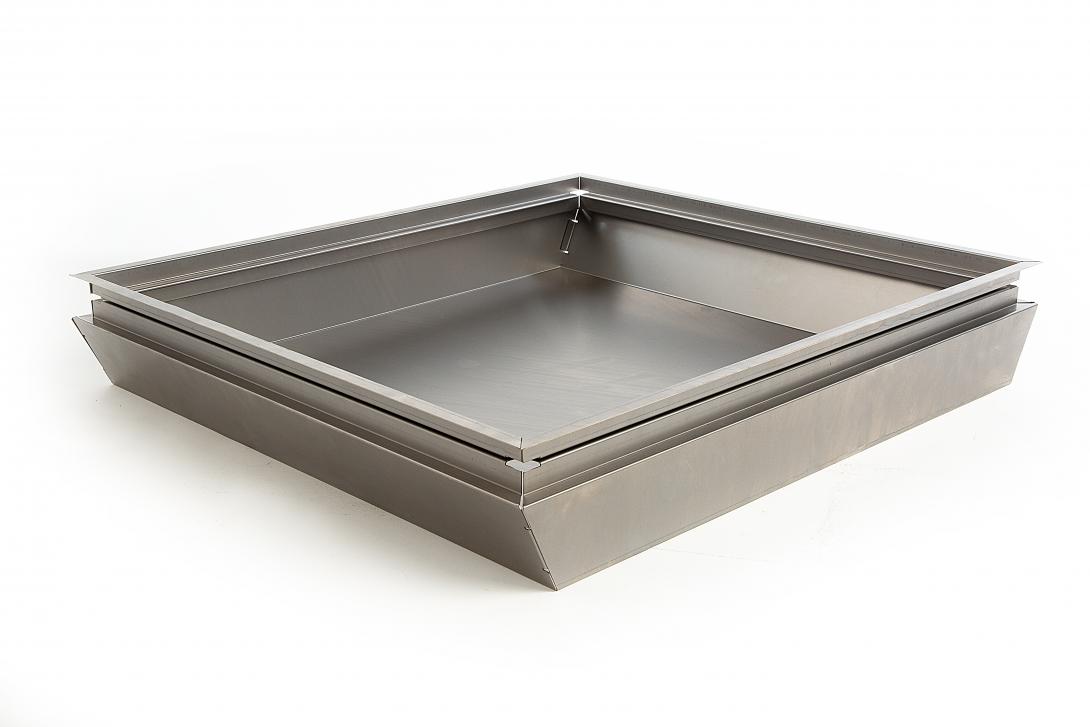
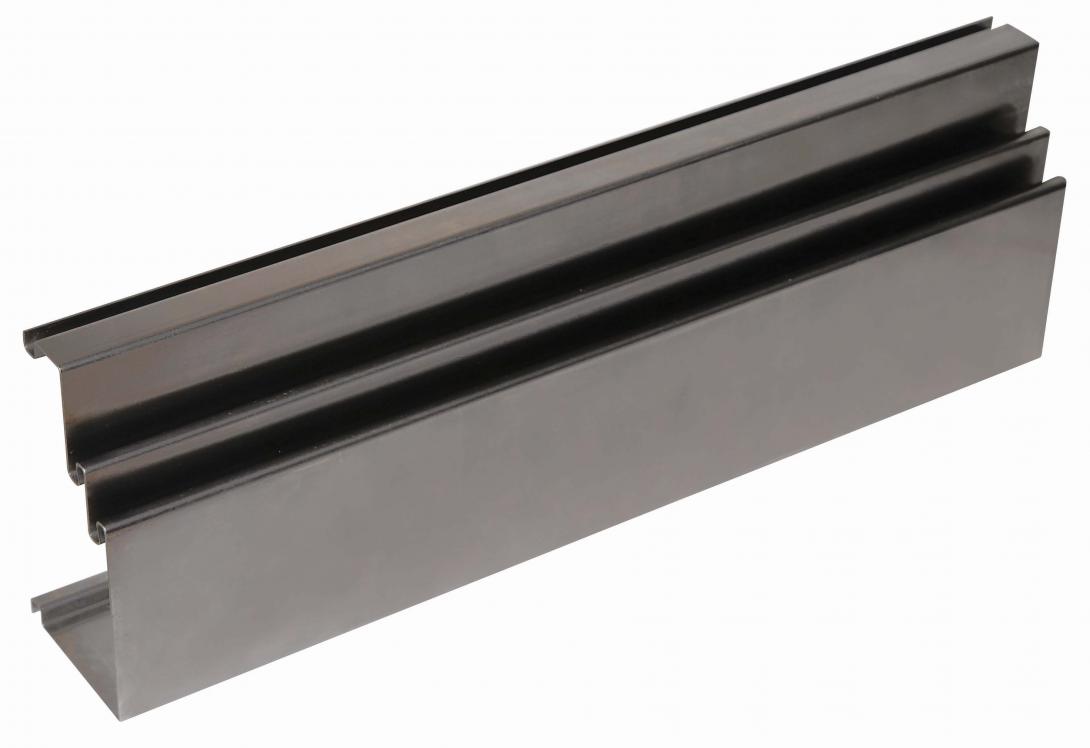
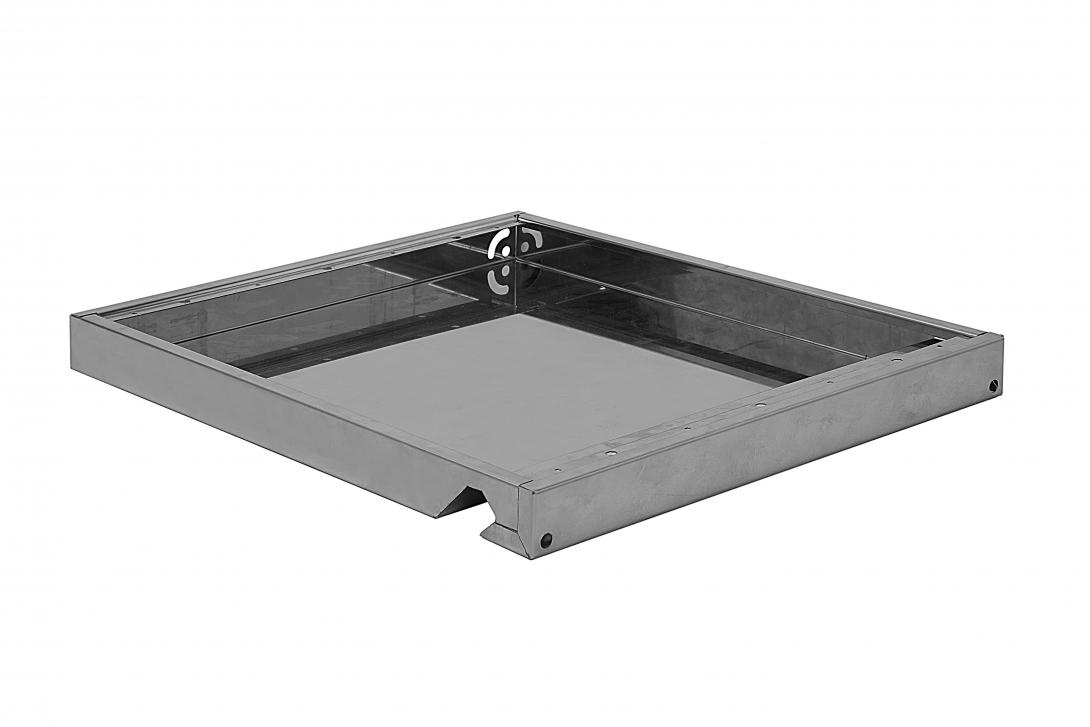
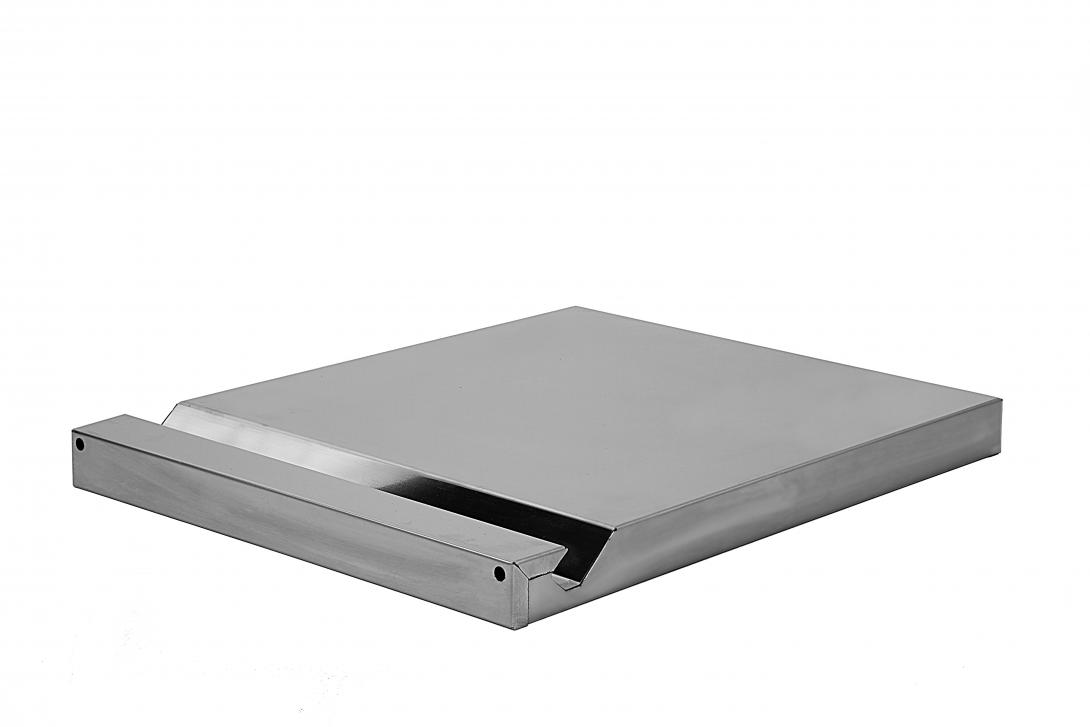
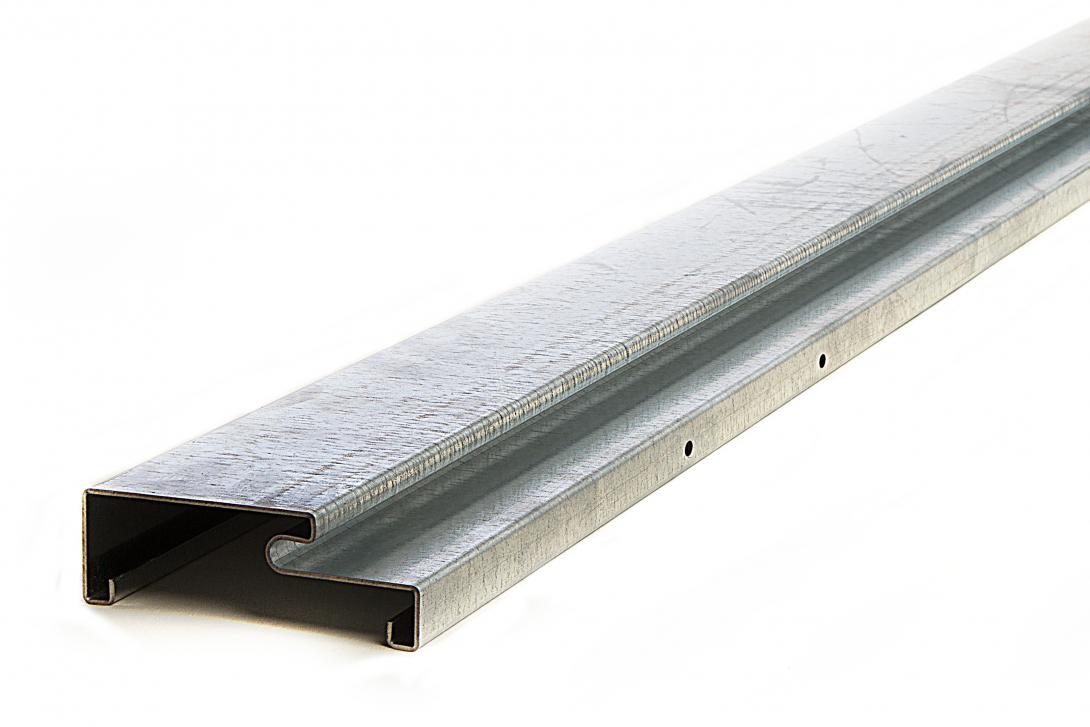
Press Brakes
In press brakes, most bending parts are produced using different bending methods: air, bottom or folding and hemming. No matter the method, they all work the same: a punch tool and a die are set at predetermined angles to bend or cut metal into a variety of shapes and forms.
The basic principle of press brake forming relies on force, otherwise known as tonnage. This determines the total amount of pressure that can be applied by the punch during a bend. The higher tonnage, the thicker the materials that can be bent and vice versa.
Choose the perfect Press Brake for you
Prima Power’s wide range of press brakes includes servo-electric (eP series) as well as hydraulic (hP series) bending machines.
While the eP series press brakes have the advantages of high acceleration and deceleration and fast response times of the servo-electric drive system, the hP series press brakes are the perfect combination of strength and versatility of hydraulic technology.
All our press brakes are extremely flexible and can be customized according to customer needs.
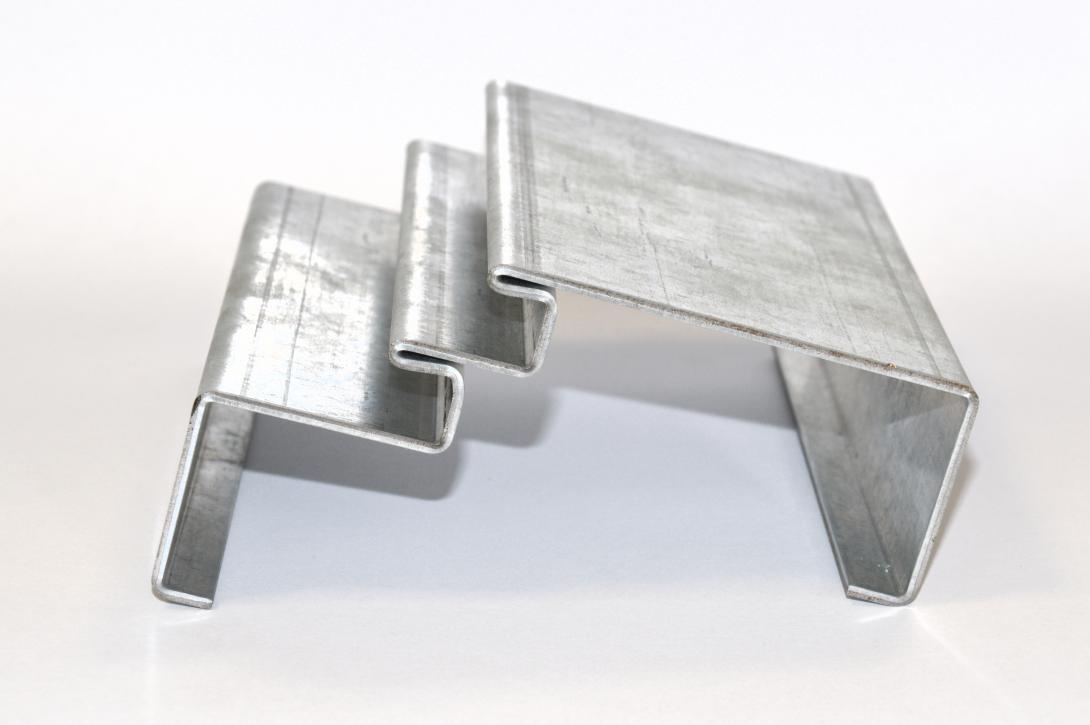
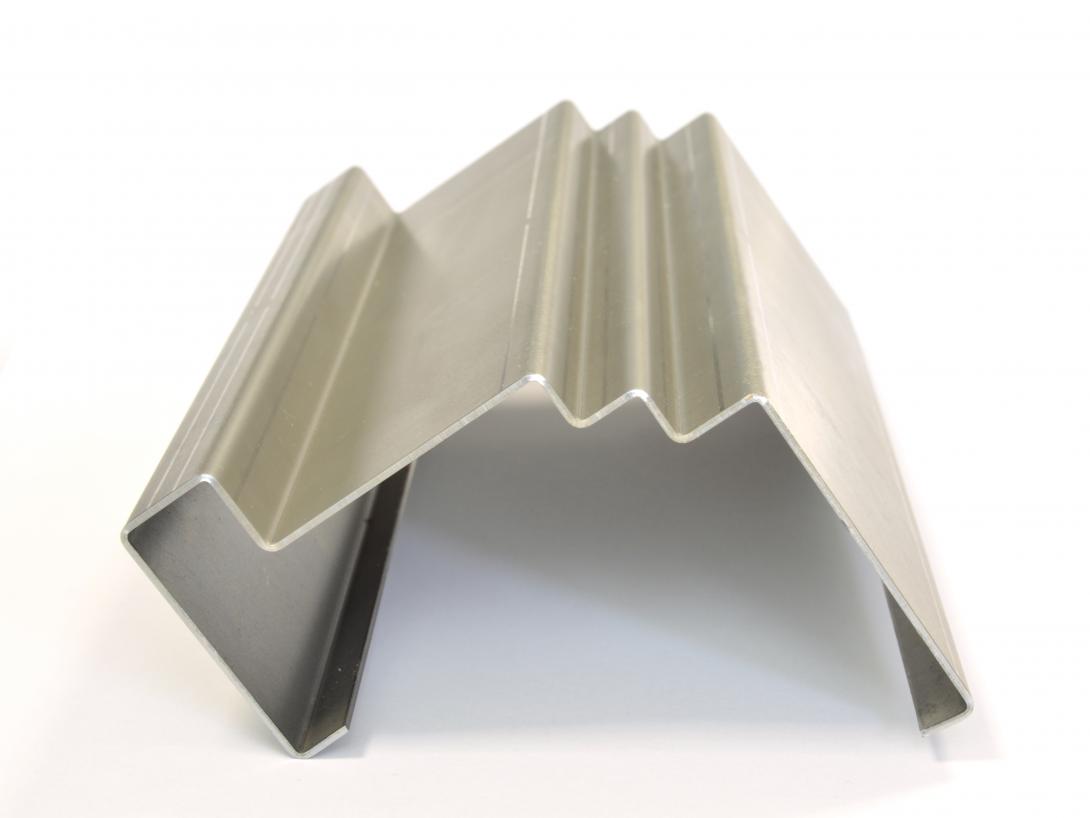
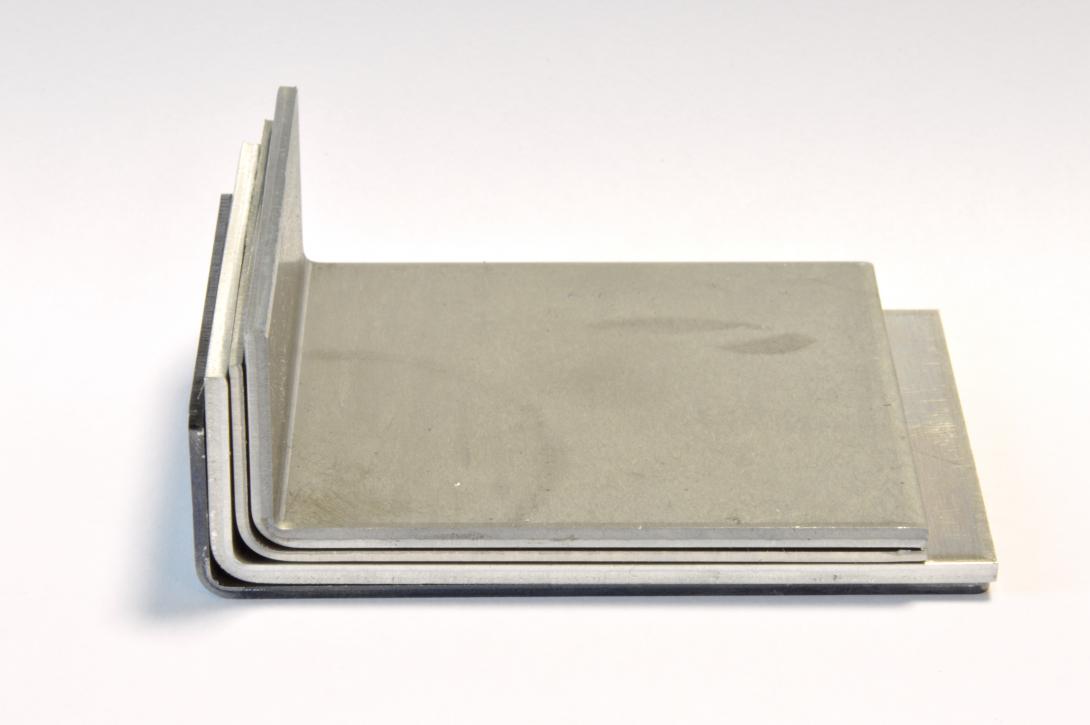
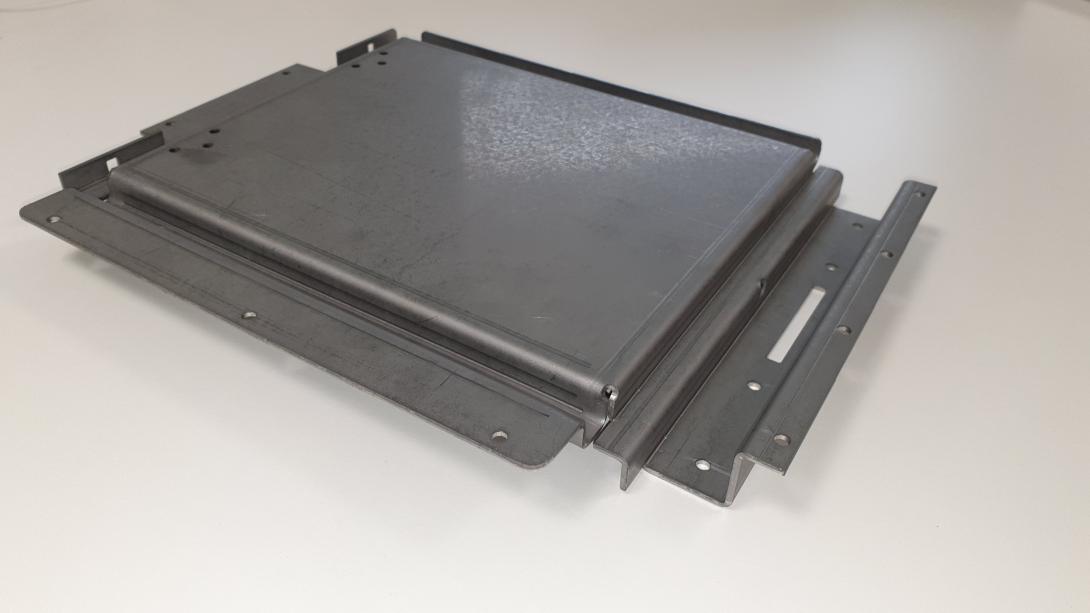
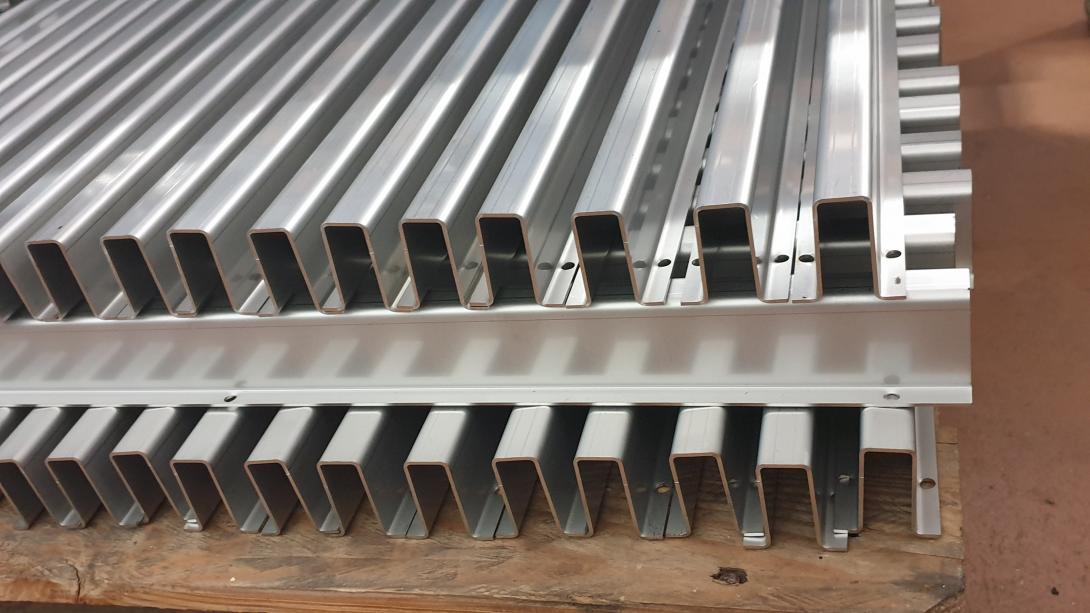
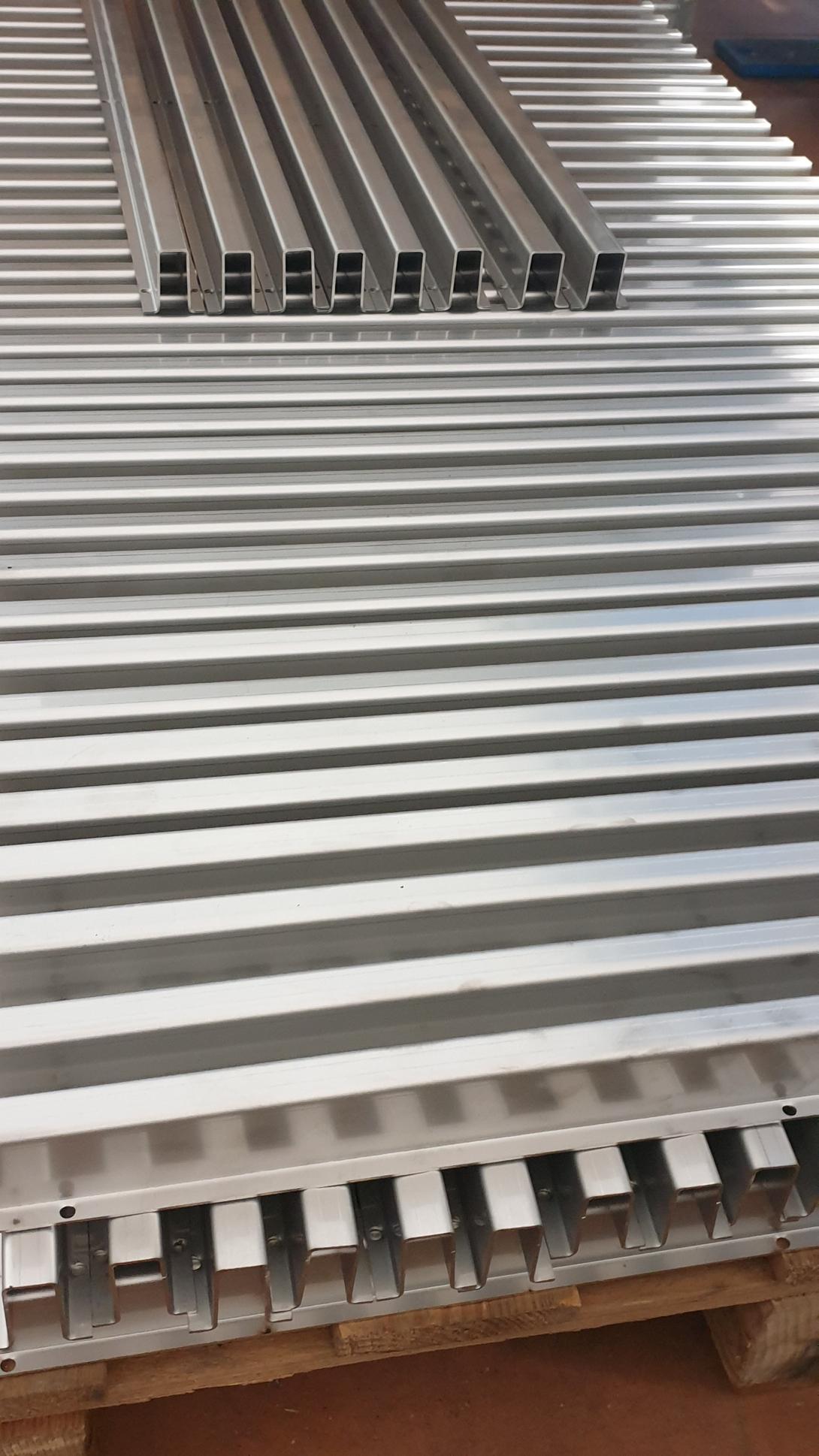
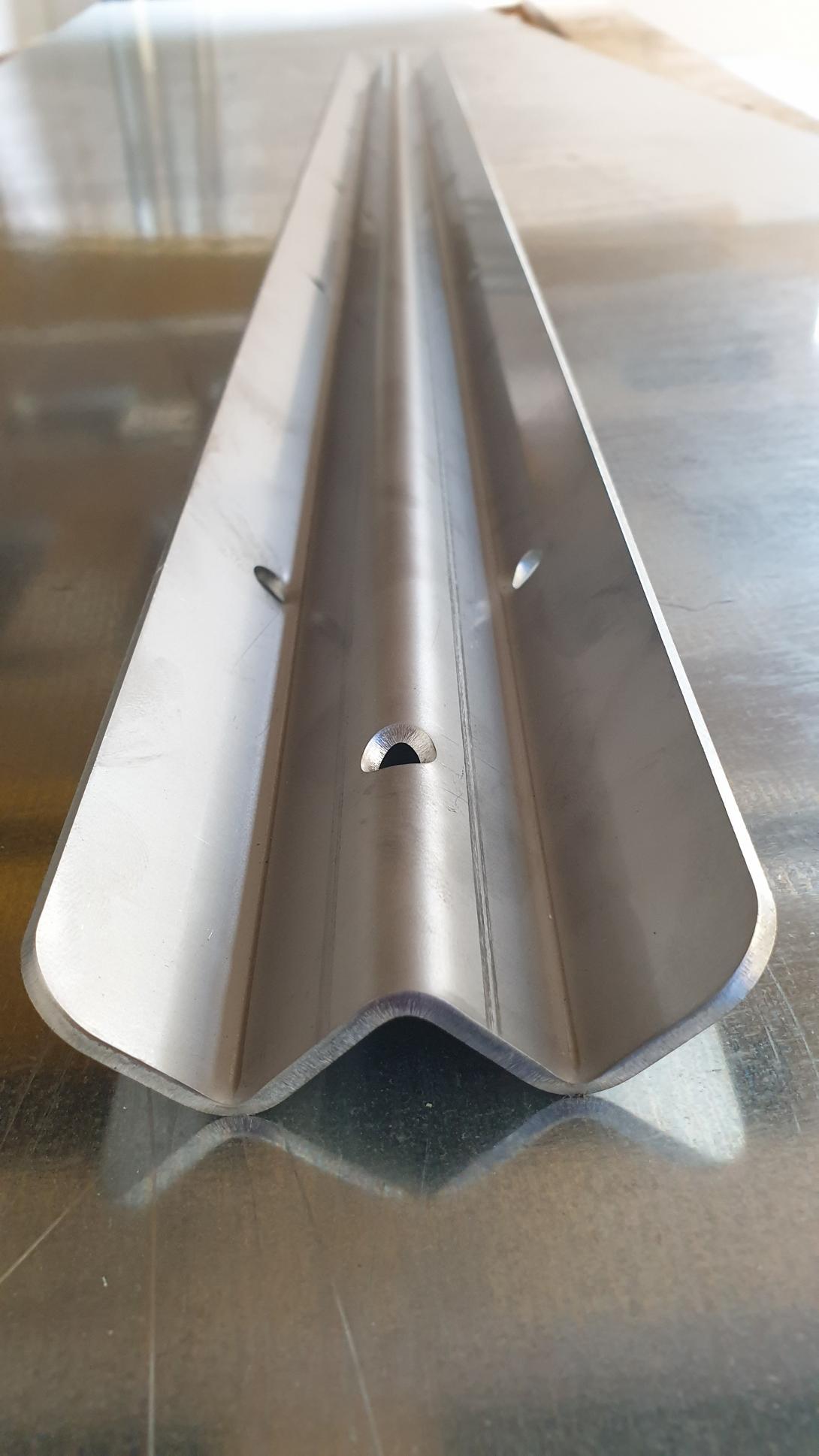
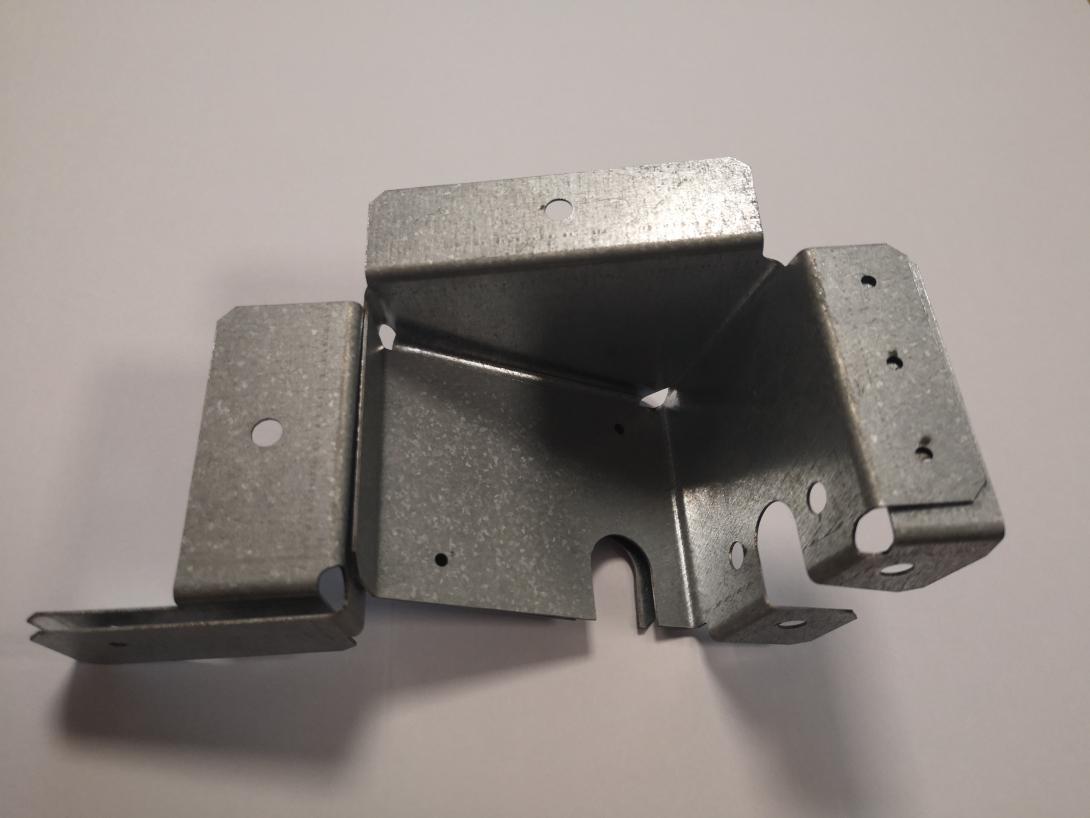
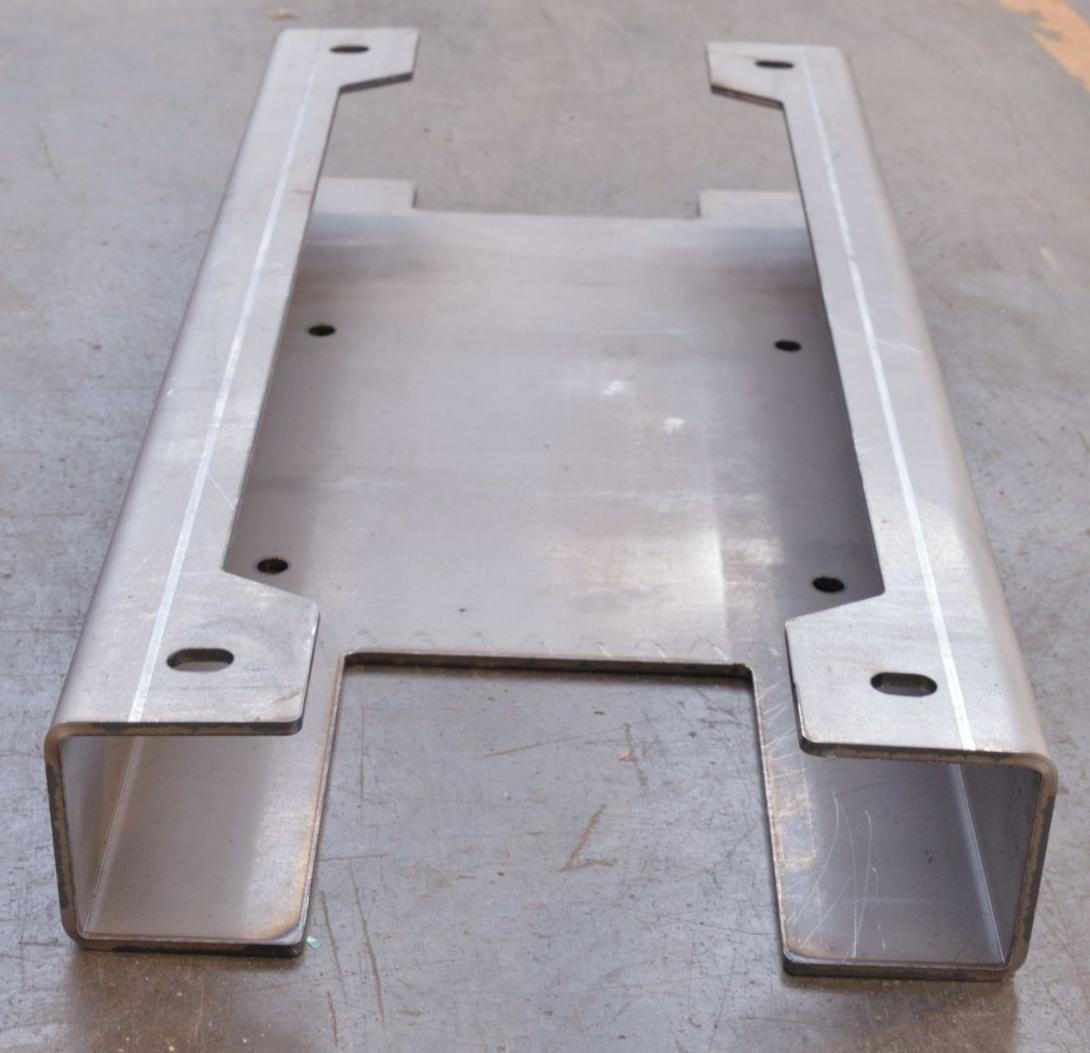
Robotic Bending Cells
Choose the perfect Robotic Bending Cell automation for you
Thinking about Robotic Bending Cells two words come to mind: configurability and modularity.
Prima Power can offer different solutions integrating its Panel Benders and Press Brakes with an anthropomorphic robot that is equipped with further devices in order to handle the material or to support the bending.
The robotics solution offered by Prima Power allows a high level of integration and automation for programming (offline CAM), connection to ERP production management and planning, and feedback and reporting in line with Industry 4.0 requirements.
Product families
Choose the perfect Bending machine for you
BCe Smart+
PANEL BENDER
New semi-automatic panel bender to level up your flexibility and productivity with the right balance
BCe Bending Centre
PANEL BENDERS
Flexibility at your service semi automatic panel bender combining flexibility and productivity
eP Genius
PRESS BRAKES
Efficient servo-electric bending solution with a fast and automatic tools change storage
FBe Fast Bend
PANEL BENDERS
The answer to multiple applications. Semi-automatic bending solution for simple, flexible and accessible production
STORIES OF EVOLUTION
Find out how Prima Power Bending technology took part in a company’s success
Dunbarton, meeting objectives
Fabricator achieves higher productivity and accuracy with servo-electric technology.
JST Power Equipment, having the right facilities to say ‘yes’ to clients is priceless.
Switchgear lineups are engineered-to-order products with a lot of variation among jobs, including fabricated sheet metal parts. Enabling the new JST Power Equipment switchgear-manufacturing plant to excel at taking on low-volume production: an automated punch-shear combination machine.
Why a metal fabricator jumped into panel bending
FlexMet continues to change its manufacturing focus, now with a new bending tool. A new product focus and a desire to automate bending are just two of the reasons that FlexMet, Franklin, Tenn., operates a panel bending machine instead of relying on more press brakes for its bending needs.
Schulthess Maschinen - The power of three
The eco-efficient cell with panel bender, press brake and industrial robot.
Most organizations today claim sustainability is one of their core values, yet it is not so common to find companies that are able to set better standards for environmental protection with their products. Schulthess Maschinen AG is one of these few game changers, thanks to its exceptionally energy-efficient washing machines and dryers.
A look at the technology behind turnkey organic poultry plants
SKA srl manufactures poultry systems for organic free-range farming with high levels of product customisation by taking advantage of innovative Prima Power technology.
Order and efficiency drive productivity, from first cut to finished product
Astra was founded just short of thirty years ago as the result of an innovative instinct which proved successful in just a few years: that stainless steel would become the technological material of the future.
Deluxe sheet metal processing
The construction phase of the new Biohort manufacturing site in Herzogsdorf (Upper Austria) lasted just over a year. With cutting-edge industry standards and optimised process cycles, the specialist for storage space solutions created new resources for further growth with new Plant 2, an addition to its Neufelden headquarters.
Prima Power EBe Express Bender Increases Productivity & Quality at Georgia Job Shop
When Randy Williams opened his job shop, he was already a seasoned fabricator. “I grew up with metal fabrication,” explains Williams. “My dad was an aerospace engineer who built trampolines part-time when I was 10 years old, and I helped build parts in the basement. His business evolved into making ferris wheels and other portable amusement rides, but eventually the liability insurance became too challenging for the small company.”
Silicon Valley Job Shop Achieves Success with Prima Power Machines
Since A & J Precision Sheetmetal Inc., San Jose, CA, first opened its doors in 1995, the company has earned a stellar reputation as a leading job shop producing high-quality precision parts in the demanding Silicon Valley.
Flexibility and precision in the manufacture of custom rack cabinets
After having chosen Prima Power as the supplier of the company's very first laser cutting machine, ATP decided to continue focusing on the quality and technology of the Italian manufacturer by also investing in a servo-electric bending machine
Facing Adversity and Winning with Prima Power Equipment
How many job shops could lose a customer that accounted for 98% of their business and recover in just a few years? Elm Machining was faced with that scenario several years ago.
Snow- and ice-free roads even faster now
After about thirty years, Giletta, a company that is part of the Bucher Municipal group, a landmark in the production and sale of snow removal machines and equipment, decided to bring the steelwork department back in-house by installing a new fiber laser cutting system and a servo-electric press brake both by Prima Power.
Riding the Night Train to Higher Productivity
The Minerva Group in Bologna, Italy is a company that truly embodies skills, technology, and entrepreneurial spirit.