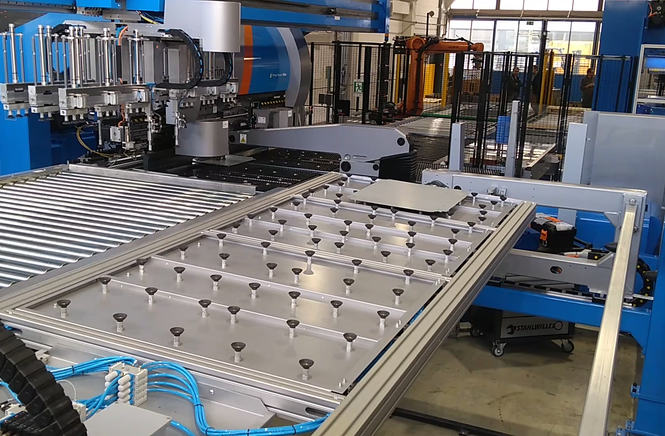
Schulthess Maschinen - The power of three
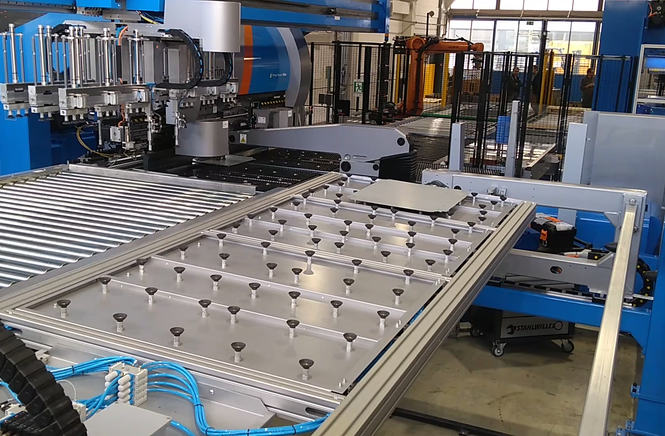
The eco-efficient cell with panel bender, press brake and industrial robot.
Most organizations today claim sustainability is one of their core values, yet it is not so common to find companies that are able to set better standards for environmental protection with their products. Schulthess Maschinen AG is one of these few game changers, thanks to its exceptionally energy-efficient washing machines and dryers.
The company, located in Wolfhausen, Switzerland, manufactures its sustainable products using an innovative bending solution by Prima Power, which combines a high level of automation with high efficiency – thus allowing end customers to reduce emissions even before the purchase, during the manufacturing process. Michael Winkler, Production Manager at Schulthess, tells us more about the successful cooperation between the two companies.
150+ YEARS OF EXPERIENCE
Schulthess has been Switzerland’s leading washing technology group since 1845 and produces high-quality machines, systems and system solutions for private, commercial and industrial clients. Offering outstanding, durable technology – such as lye tanks made of chrome steel – today this traditional company sets the benchmark in performance and functionality in over 25 countries, from Chile to China.
Schulthess is part of the NIBE Group, a global organization that develops and manufactures intelligent, eco-friendly, energy-efficient indoor comfort solutions for all types of properties. With approximately 20,400 employees around the world and over 30 billion Swedish kronor (2021 data) in generated sales, NIBE provides solutions that contribute to a lower carbon footprint and better utilization of energy.
“With our core competence in sheet metal production and assembly, we deliver 36,500 machines per year,” says Winkler. Going forward, he promises, “With our completely new, combined plant, we will ensure that there will be even more.”
In 2018, Prima Power delivered a robotic bending solution to the Schulthess factory in Wolfhausen. “Our clients are highly satisfied with our products, and this makes Schulthess confident to start producing even more machines thanks to the bending solution proposed by Prima Power,” Winkler adds. In fact, at Schulthess everybody believes in a fully automated future: the company realized that a complete bending solution was ideal to improve production, especially in the face of a shortage of skilled labor that seems to become only more severe and widespread with time.
"At Schulthess everybody believes in a fully automated future: the company realized that a complete bending solution was ideal to improve production."
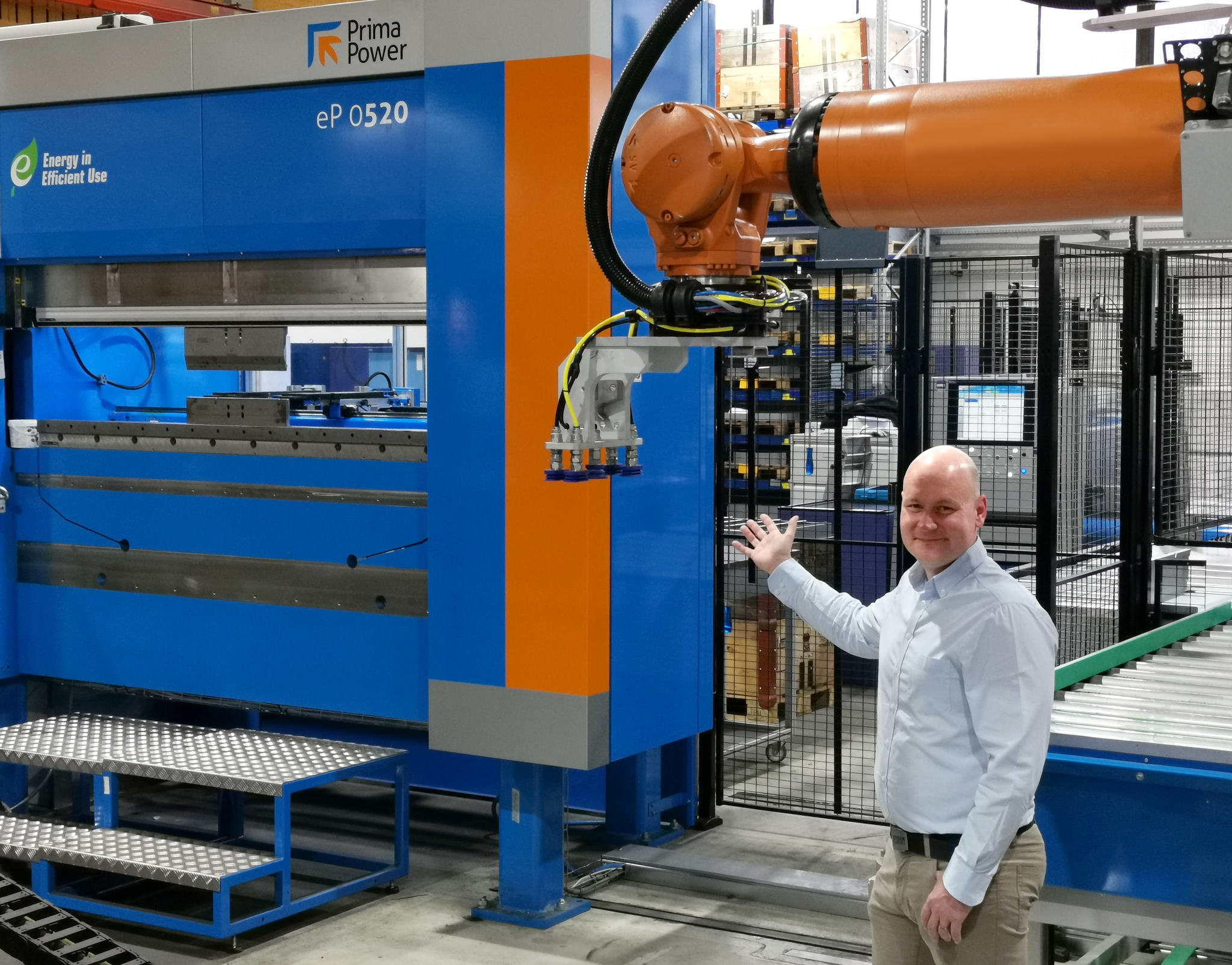
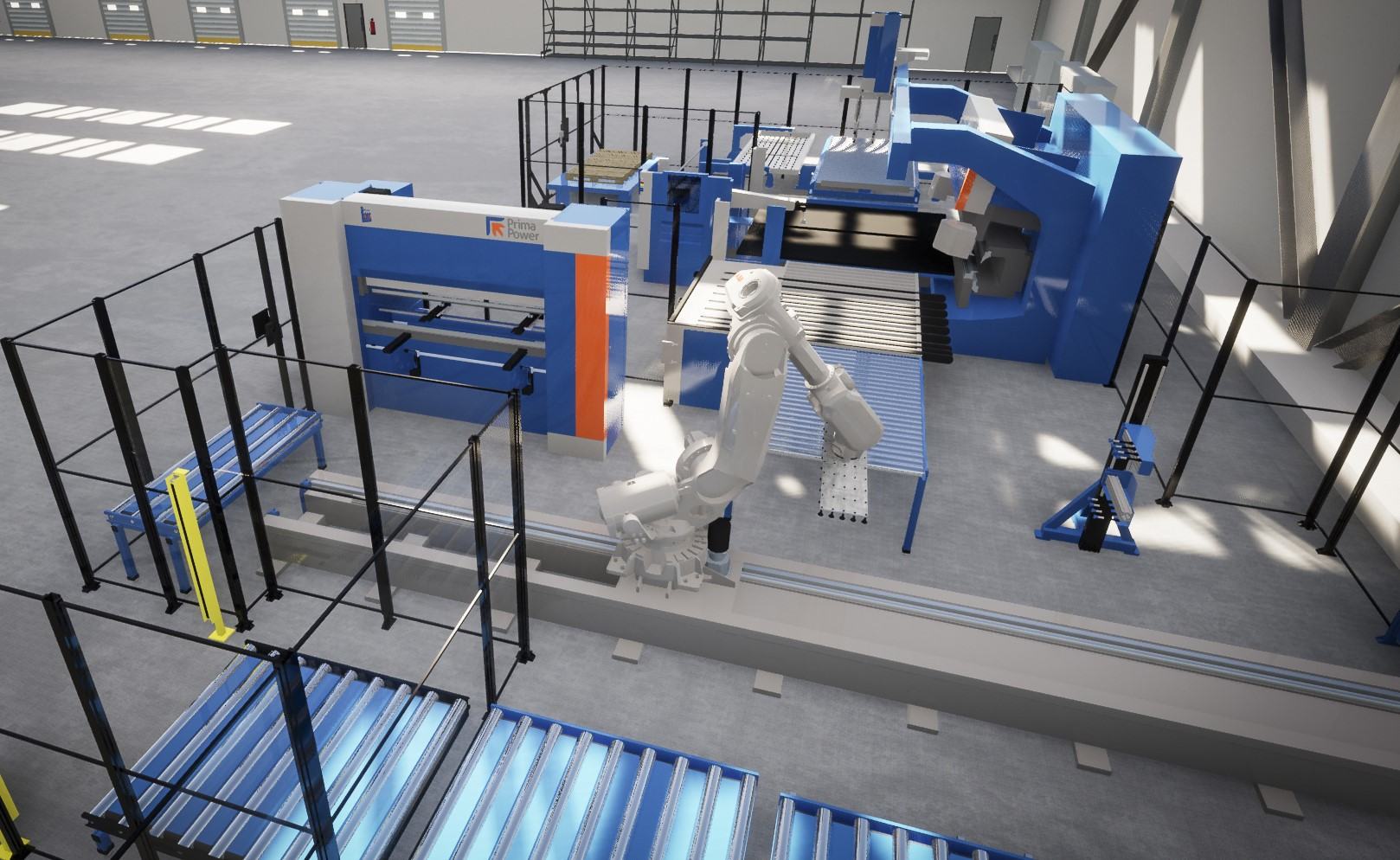
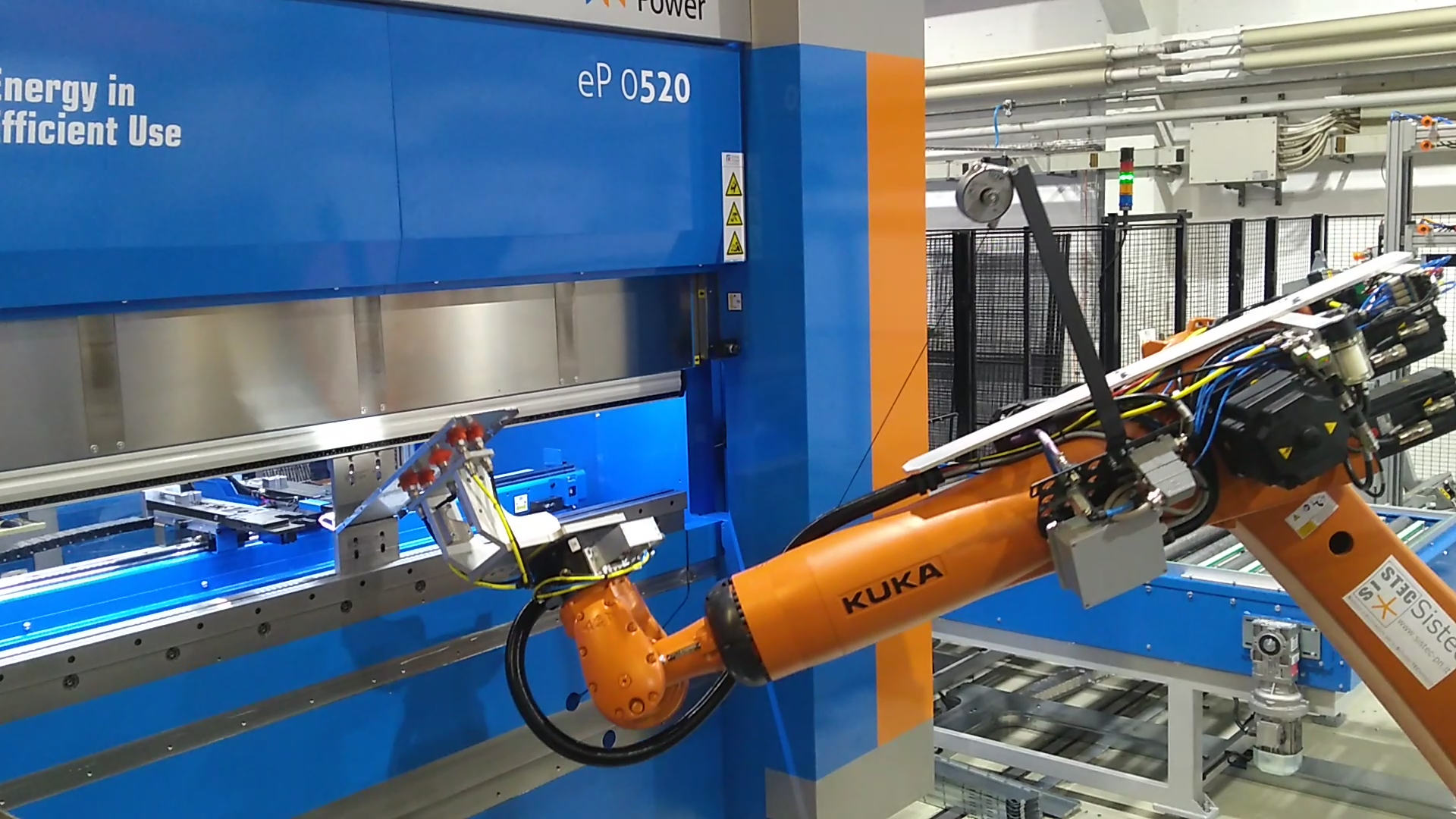
A SHARED AND COMMON PROJECT
One of the reasons why Schulthess got in touch with Prima Power was to find connected solutions to facilitate unmanned operations. As an innovator in the washing machine industry, Schulthess was also forward-thinking in looking for a future-oriented system that could be used longer over time and cover the entire production flow. After several visits and factory tours, everybody came to the same conclusion: the decision to develop something new with the help of Prima Power, the only company that could intelligently combine three different machines into one bending system with the highest automation level.
The automatic bending system consists of a servo-electric EBe4FM panel bender with a PCD (Picking & Centering Device) complete with double and scissor wagons and a BTD (Bending Turning Device), an eP0520 press brake with 5-axis back gauges, a 7-axis industrial robot sliding on rails to automate the process between EBe4 and eP0520 and one palletized conveyor area with automatic pallet feed and press brake ATC automatic tools change set-up.
“What we like the most is the fact that the whole system is extremely flexible!”
“The three elements – panel bender, press brake and robot – integrate perfectly in one cell,” explains Winkler, who is proud to add: “This is a truly unique bending solution with a panel bender, a robot and an integrated press brake. But what we like the most is the fact that the whole system is extremely flexible! Schulthess’s decision on this project was to make complex processes – such as sheet metal manufacturing and assembly – much simpler, thanks to intelligent automation derived from precise bending and advanced automation technology.”
OUTSTANDING EFFICIENCY WITH SERVO-ELECTRIC TECHNOLOGY
Another decisive aspect for Schulthess, which is deeply oriented towards respect for the environment and any consequent sustainability issues, was the highly efficient servo-electric technology in use in all Prima Power bending machines (panel benders and press brakes).
“Go Clean Go Green is more than just a motto for us. We live and breathe it.”
Winkler indeed recalls, “At Schulthess, CEO Thomas Marder and CFO Martin Keller – who are also both owners of the company – give particular importance to the sustainability philosophy: Go Clean Go Green is more than just a motto for us. We live and breathe it. The fact that the machines are non-hydraulic solutions is attractive in terms of lifecycle costs because they do not generate heat processes and do not require hydraulic oil, with consequent contamination of the produced parts and disposal costs; they also use less energy and require considerably less maintenance, and furthermore they ensure an accurate bending process without unnecessary environmental impacts, at higher aesthetical quality. Prima Power has been a pioneer in this field for over 20 years: this makes the investment even more reliable and beneficial for our company.”
As with any challenge, the support of a like-minded partner can make it easier to identify the right solution, implement the necessary steps and finally come through successfully.
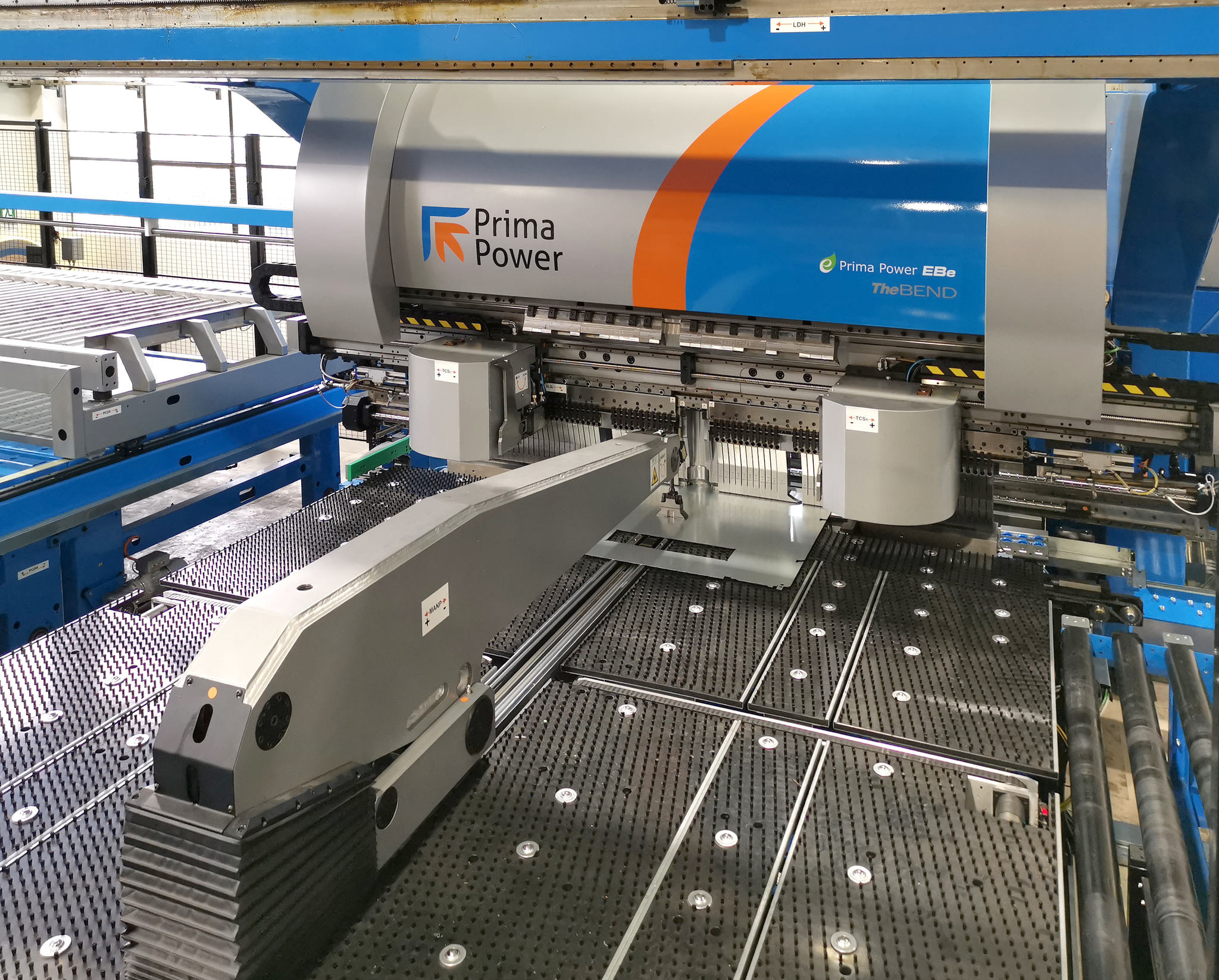
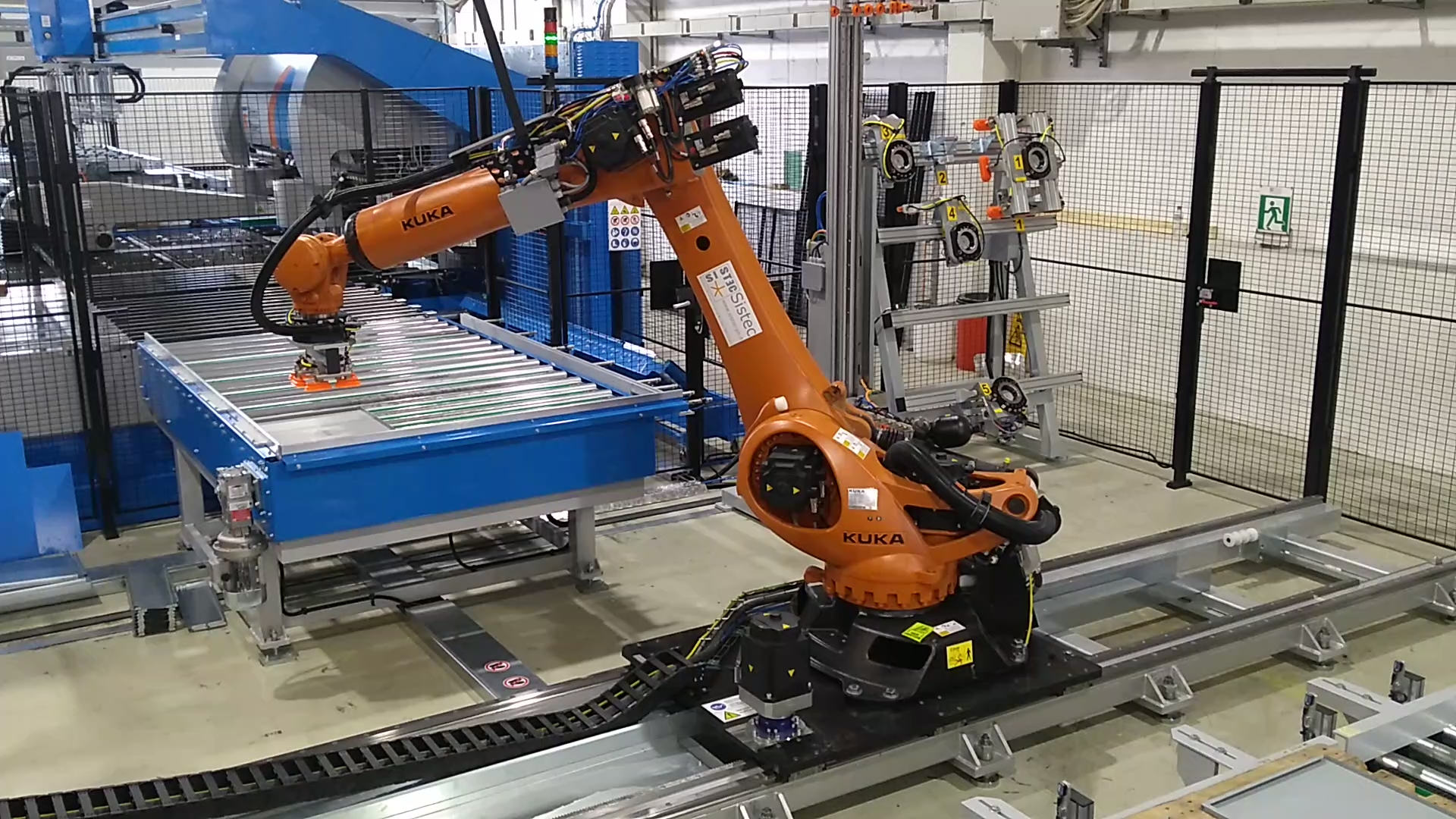
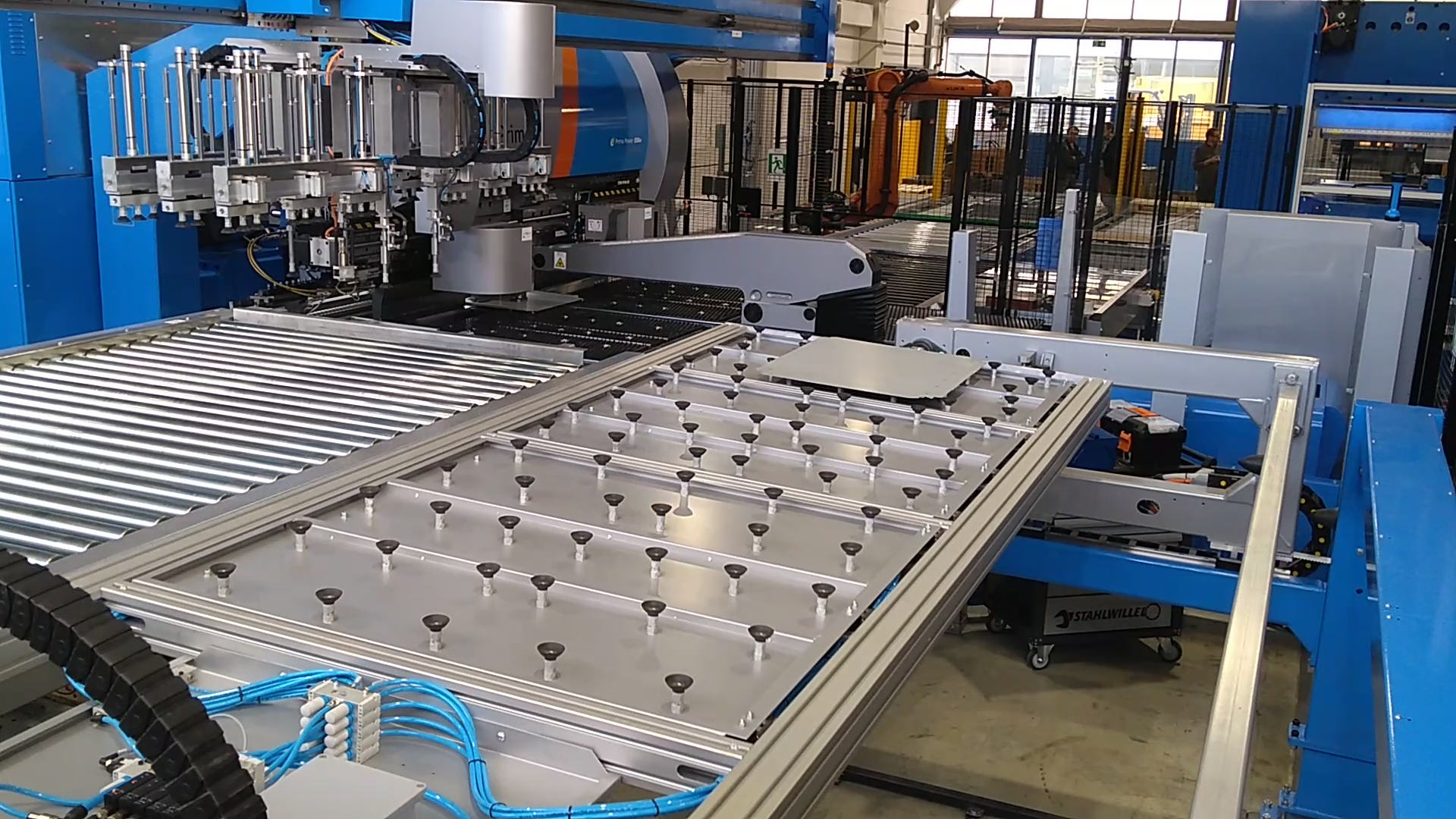
AROUND THE CLOCK
During daytime production at Schulthess, the profiles automatically bent by the EBe4 and completed with the eP0520 are randomly checked and then released for final assembly.
The robot is increasingly used during the night shift, even when no human resources are present at the plant and the system is monitored with cameras. The robot, the EBe4 and the eP0520 independently produce the large series that is put together the next day by the assembly department. If, during this so-called “ghost shift”, the system detects that a different gripper is needed for a certain work, the robot quickly and independently changes it, and continues to work autonomously.
“This plant is designed for eight to ten years of operations according to Industry 4.0 standards,” says Winkler. “That’s a lot of time at peak performance, and it is also a highly sustainable solution – which is crucial for us.”
Finally, the only question that remains is about the error rate. “That’s very easy to answer,” Winkler is pleased to say: “The error rate is zero!”
“What we appreciate most about Prima Power solution,” he concludes, “is the outstanding performance offered by an efficient and flexible bending solution and the fact that all special customer requests are easily accommodated.”
This is a truly unique bending solution with a panel bender, a robot and an integrated press brake. But what we like the most is the fact that the whole system is extremely flexible!
Are you looking for a similar solution for your company? Find it here
Robotic Bending Cells
ROBOTIC BENDING CELLS