
Robotic Bending Cells

ROBOTIC BENDING CELLS
Full performance optimization into your arms
Flexible standalone bending cells for diversified applications thanks to the integration in a panel bender or press brake.
High repeatability of the parts and fast return of the investment, thanks to the robot assisted bending process applied to the servo-electric technology.
Fully unmanned production combined with the widest range of modular machines that integrate cutting, stacking and laser.
Process-oriented approach simplifies and optimizes production flow through advanced robotics integration and modular automation.
Robotics integration is the key to unlocking greater efficiency, flexibility, and productivity in sheet metal manufacturing.
The great versatility of our Robotic Bending Cells allows them to find proper applications in any industrial segment and adapt to batches of any dimension. Our Robotic Bending Cells can be personalized according to customer needs. The several available sizes of the press brake or panel bender, the robot, the tools supplied are evaluated based on two scenarios: the autonomy desired by the customer (i.e., how much the operator needs to intervene to feed or unload the line) and the required automation level, such as the use of automatic systems for tool change.
The flexibility in personalization ensures that our robotic bending solutions achieve the best operating conditions in any application field.
Designed to meet the diverse needs of OEMs and job shops of any size, Prima Power's Robotic Bending Cells offer:
Fully automated operation ensuring high efficiency and productivity even for small production runs.
Extreme flexibility and versatility to handle a wide range of metal types and thicknesses, making our Robotic Bending Cells suitable for a variety of applications. Their modular design allows for easy customization and scalability, ensuring that they can be adapted to each customer's specific requirements.
High precision and repeatability to ensure consistent quality and reduce the risk of errors.
Optimized layouts that reduce footprint and simplify integration into the factory while enhancing efficiency.

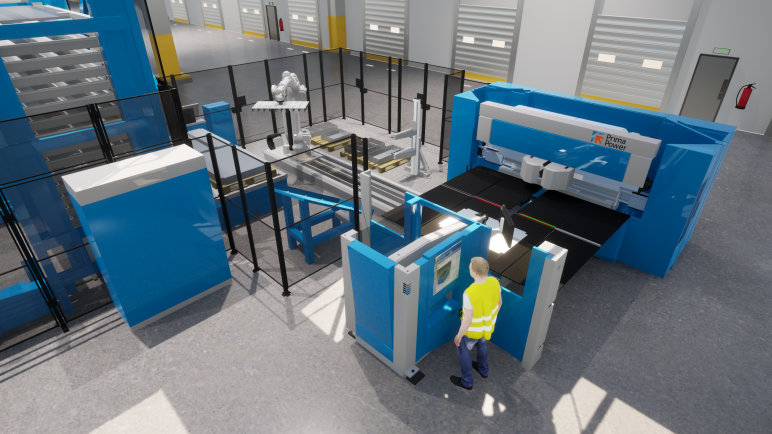
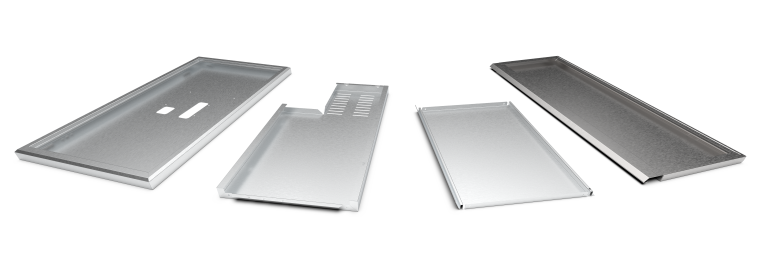
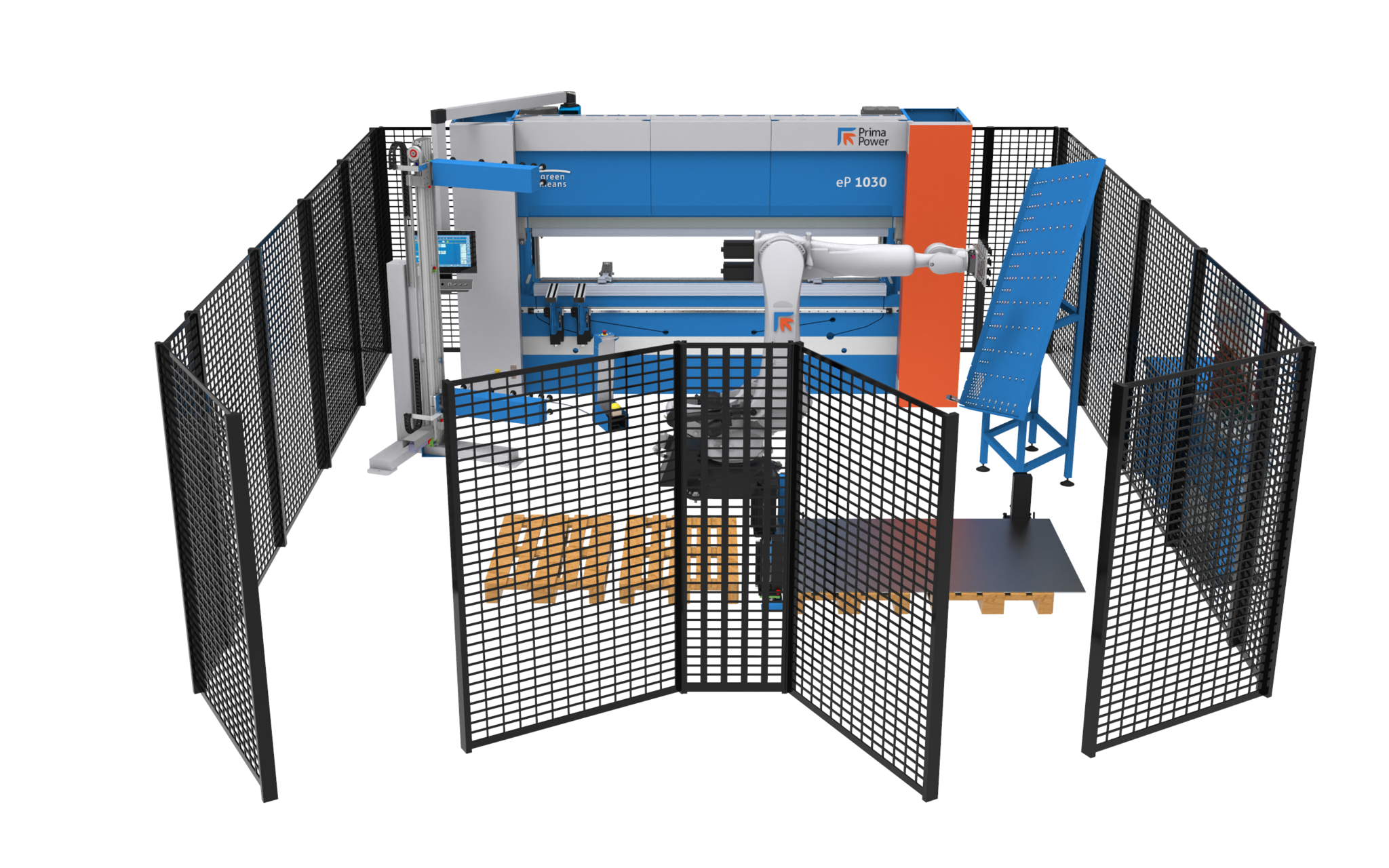
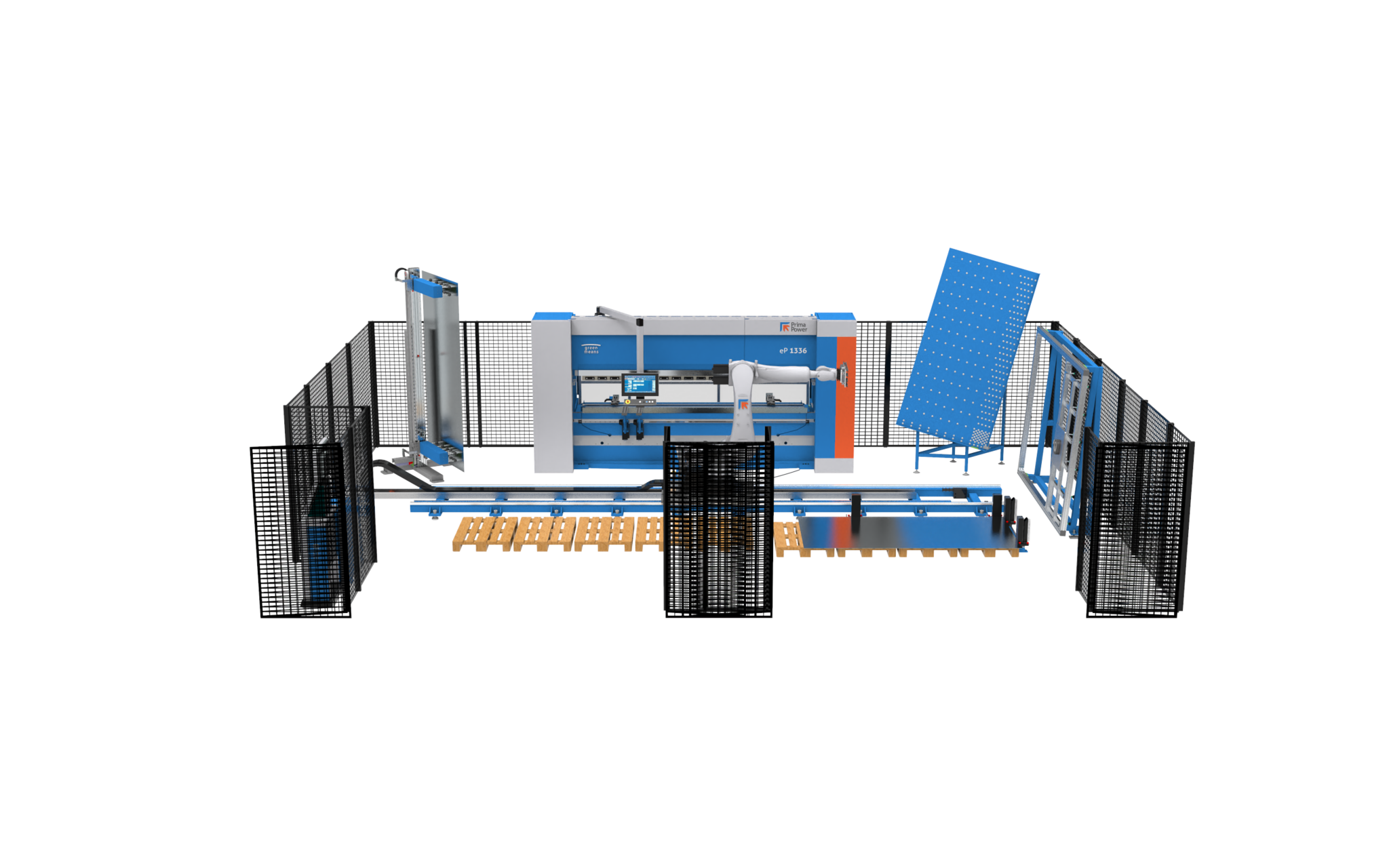
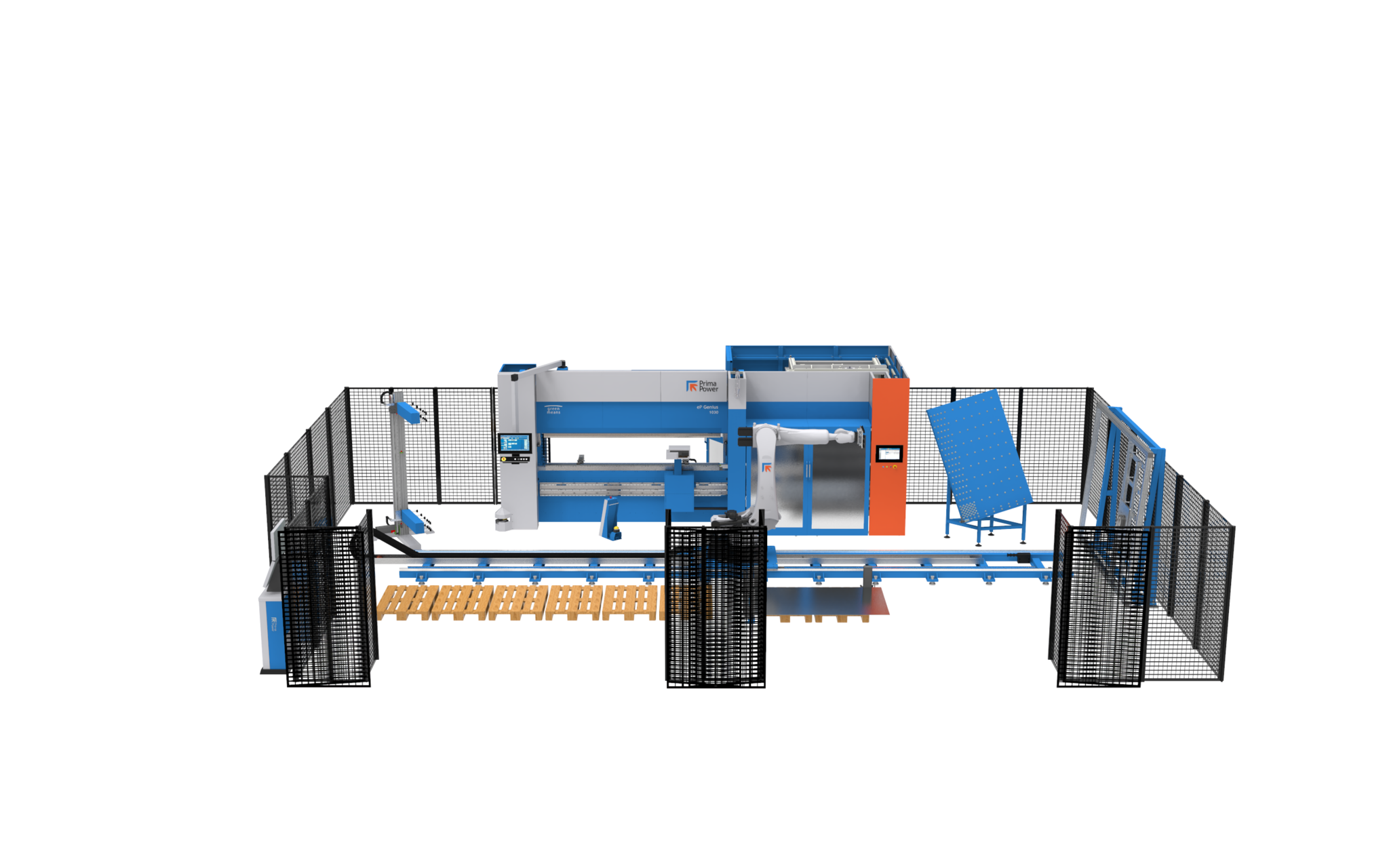
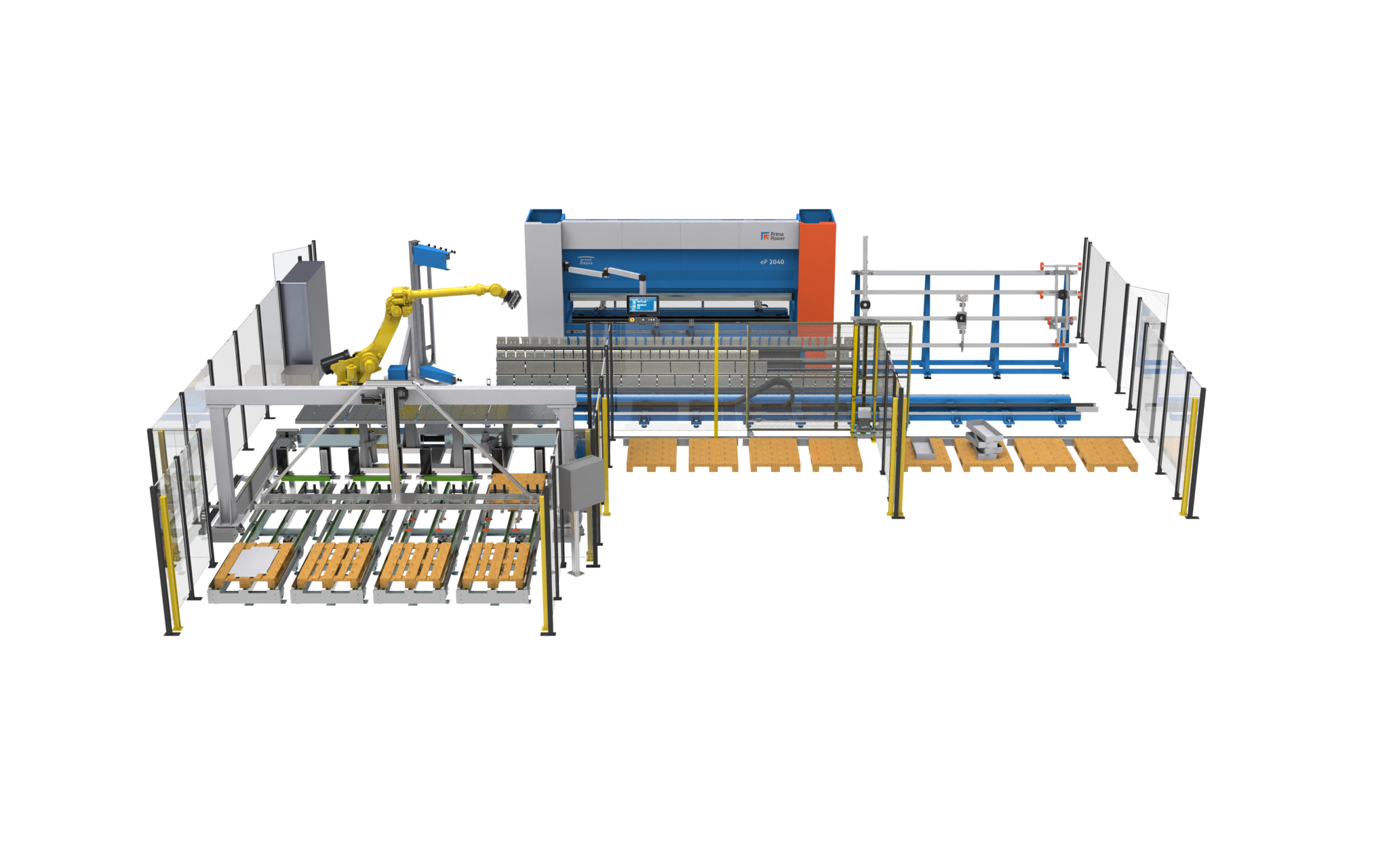
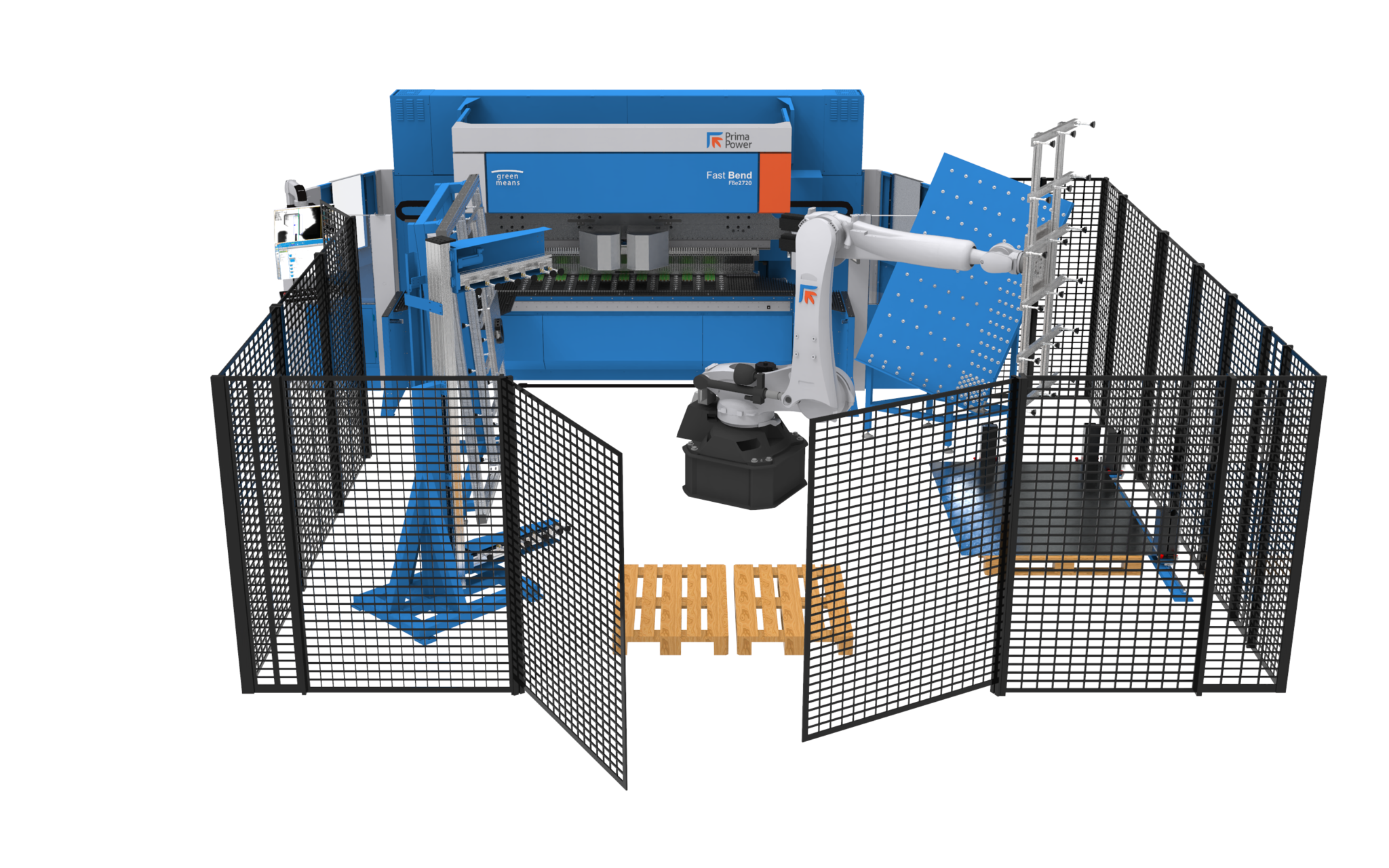
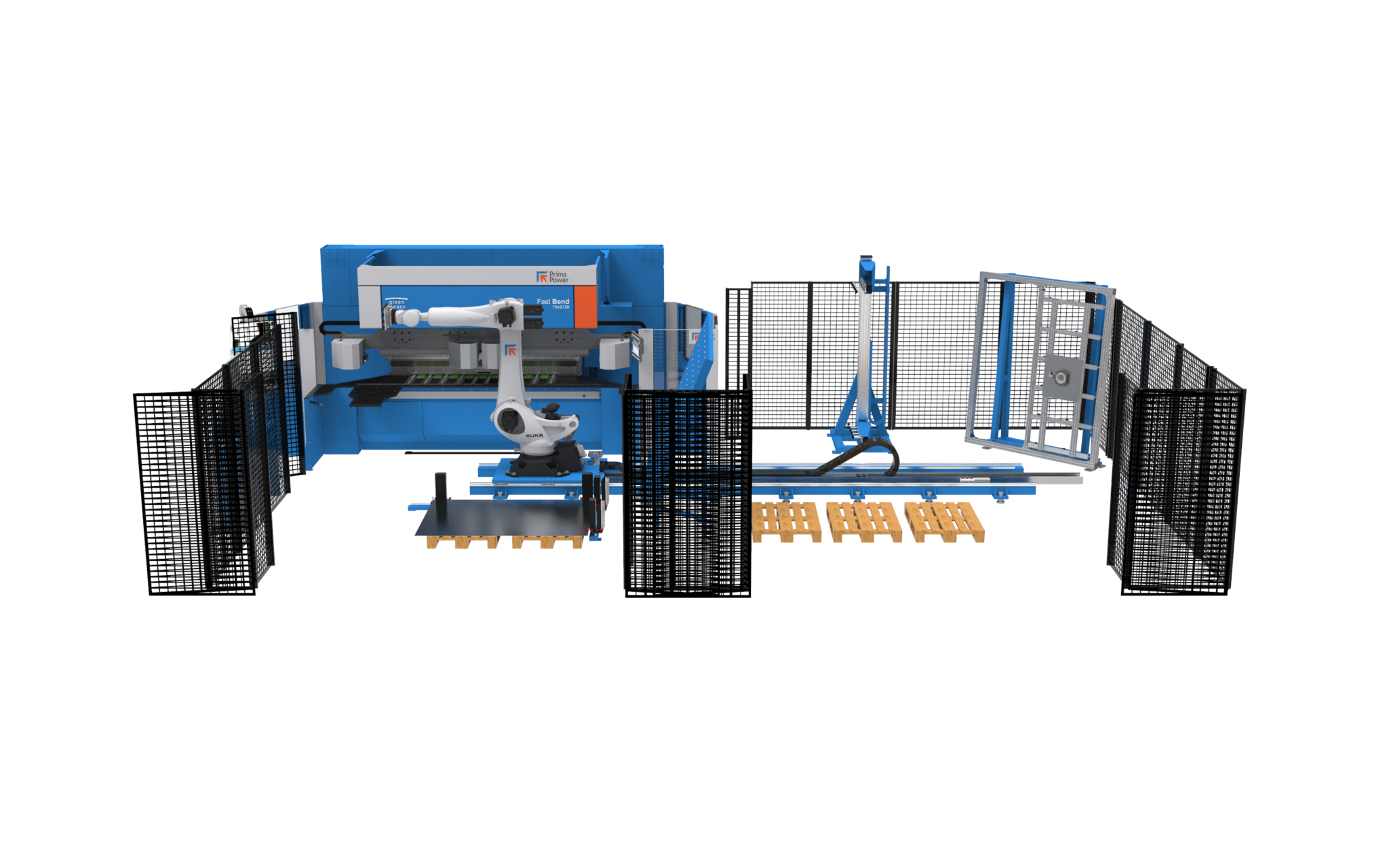
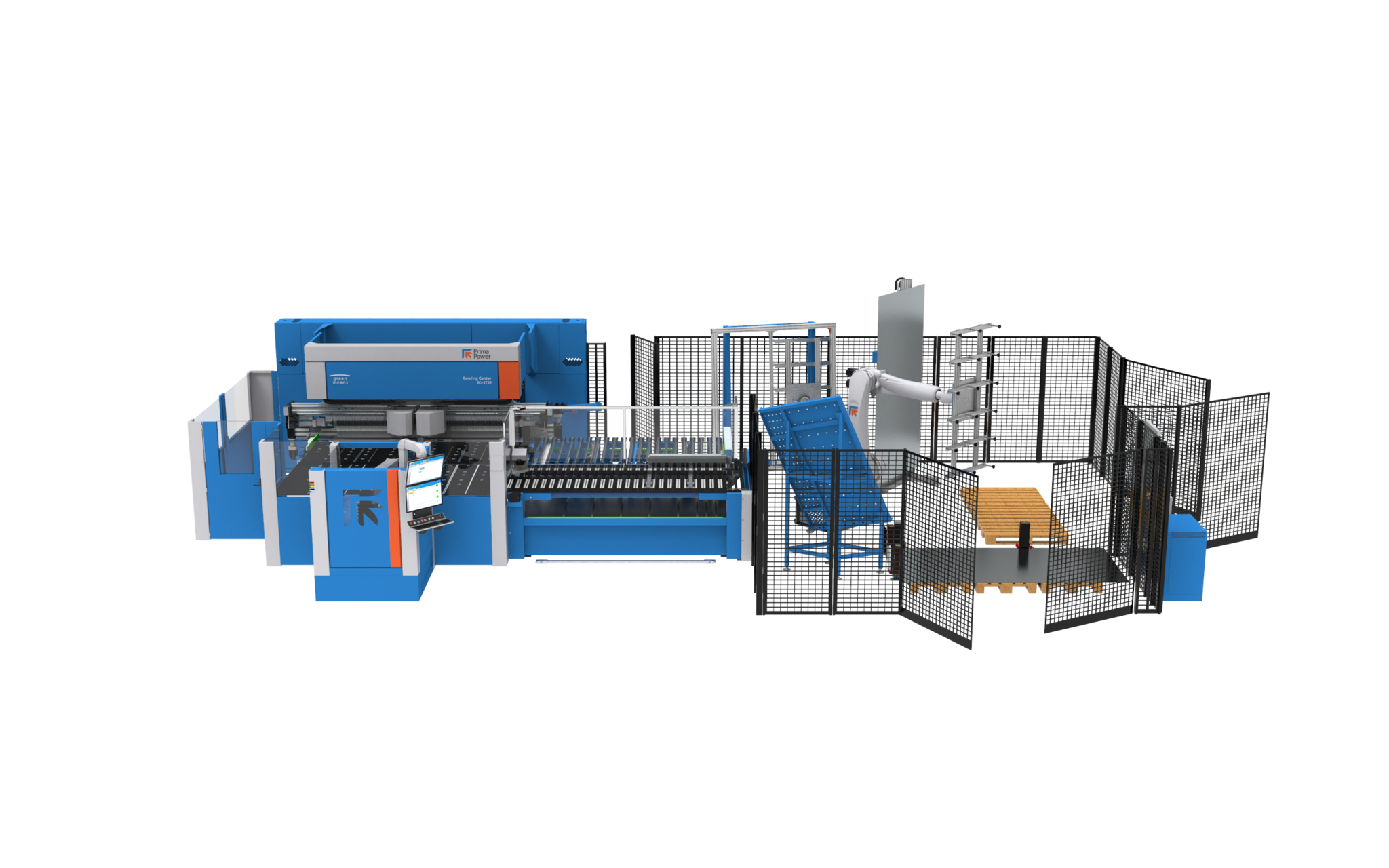
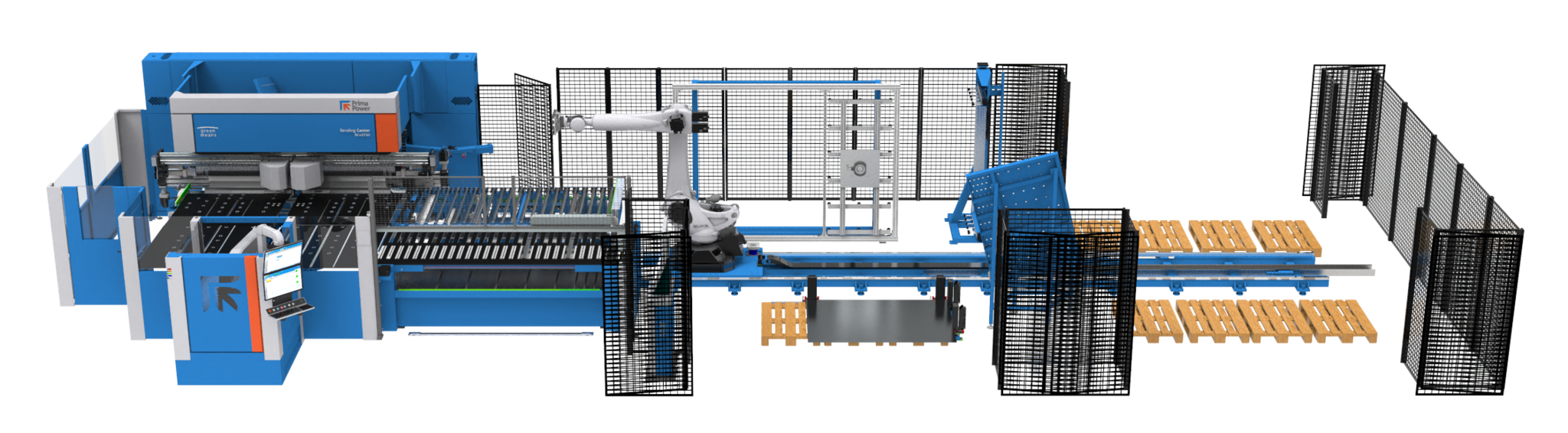
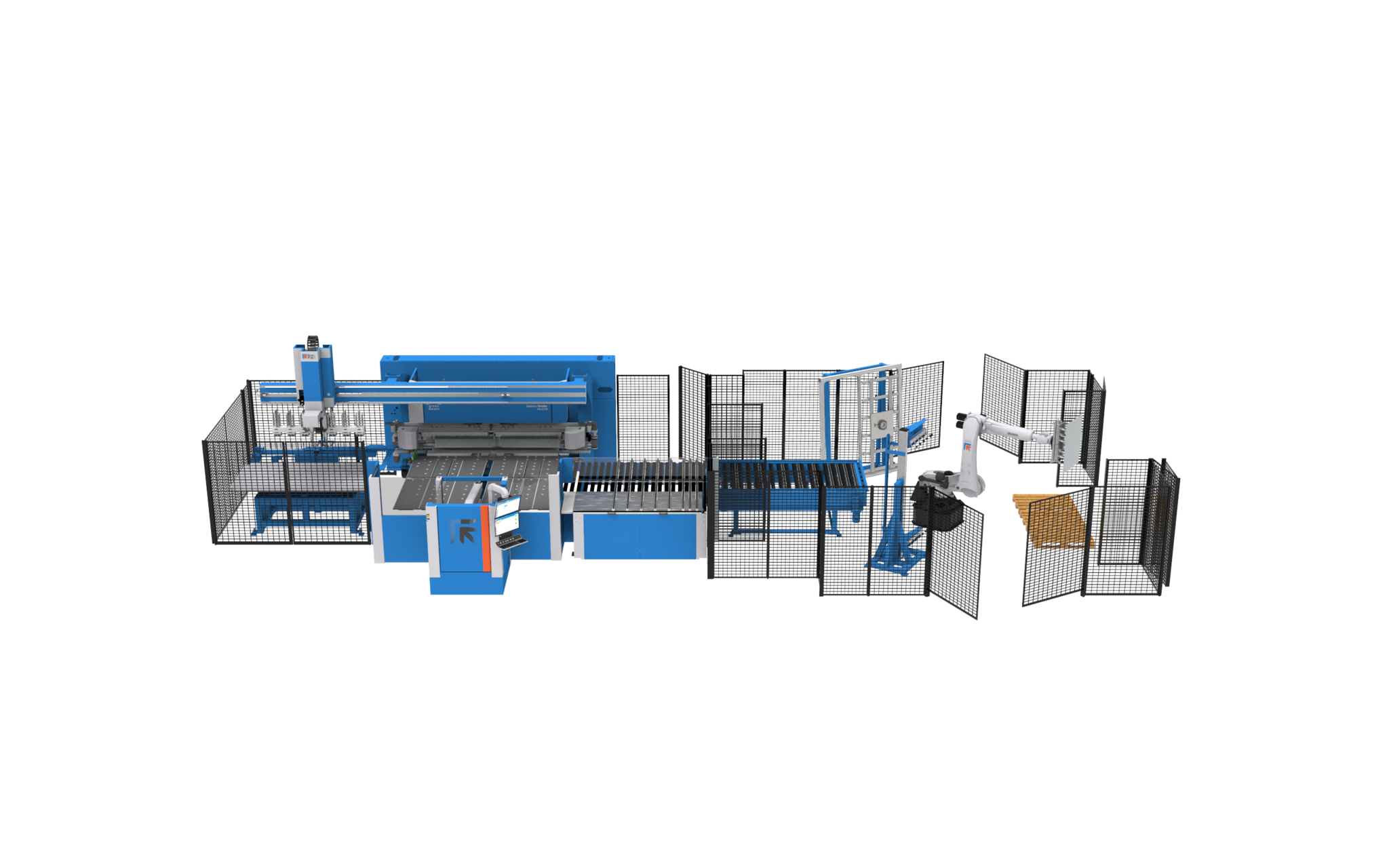
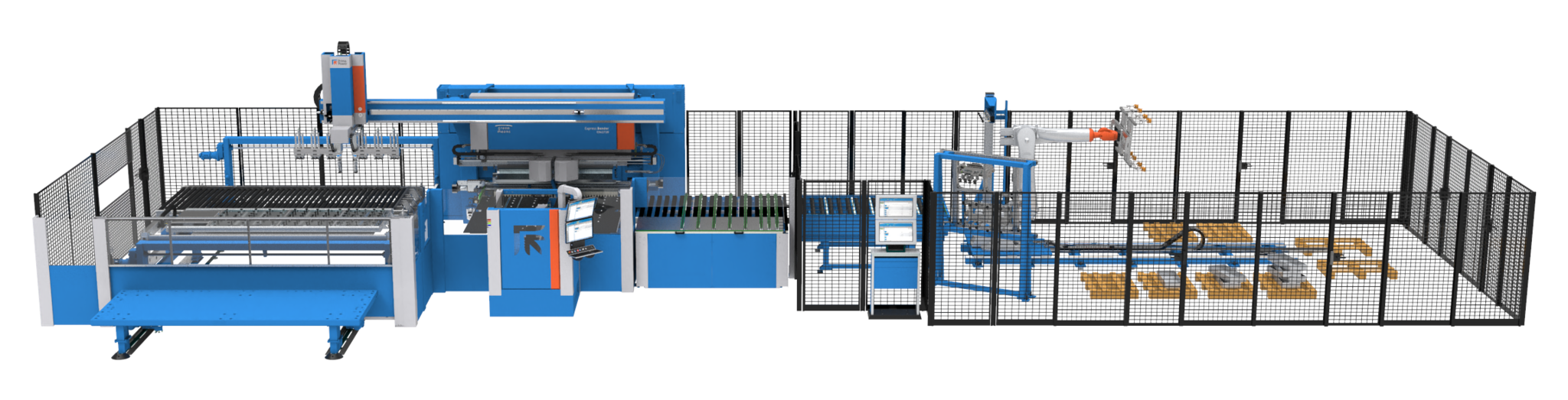
Optimize your Prima Power machine
Tul-Robot
H.M.I.
The operator interface that allows managing the system and the part programs during the production phase.
Related technologies
RELATED AUTOMATIONS
Robotics Integration Solutions
MATERIAL HANDLING SOLUTIONS
Free your potential with a complete all-in-one partner
Night Train FMS®
FLEXIBLE MANUFACTURING SYSTEMS
Leading technology storage solution in automated flexible manufacturing systems
FBe Fast Bend
PANEL BENDERS
The answer to multiple applications. Semi-automatic bending solution for simple, flexible and accessible production
BCe Bending Centre
PANEL BENDERS
Flexibility at your service semi automatic panel bender combining flexibility and productivity
SUCCESS STORIES
Find out how a Prima Power Robotic Bending System machine took part in a company's success
A look at the technology behind turnkey organic poultry plants
SKA srl manufactures poultry systems for organic free-range farming with high levels of product customisation by taking advantage of innovative Prima Power technology.