
De Wave, Efficienza e produttività prendono il largo

Solcano i mari di tutto il mondo, ospitando da qualche decina a qualche migliaio di persone. Stiamo parlando di navi da crociera, grandi yacht e imbarcazioni fluviali per le quali il gruppo de wave produce arredi e allestimenti di bordo di varia tipologia, realizzati sfruttando anche le tecnologie integrate di una performante linea automatica prima power.
Se per vivere per sempre su una nave da crociera “basterà” attendere un paio d’anni e avere un milione di dollari da spendere (stando a quanto recentemente diffuso da una compagnia di crociere che, per prima al mondo ha presentato una nave residenziale dotata di oltre 500 appartamenti), molto meno potrebbe invece servire per passare alcuni giorni di navigazione all’insegna del relax, visitando località dislocate in tutti i continenti, note e meno note. È infatti ampia la scelta di imbarcazioni in grado di ospitare da qualche decina a qualche migliaio di persone, tra passeggeri ed equipaggi, tra cui grandi navi da crociera, grandi yacht, oltre alle non meno attrezzate imbarcazioni fluviali. Come quelle per le quali De Wave produce arredi e allestimenti, posizionandosi come contractor di riferimento attraverso una vasta rete di uffici e impianti di produzione per supportare a livello globale la navigazione e la nautica da diporto.
Nata dalla fusione di cinque aziende, De Wave è oggi controllata interamente dal fondo d’investimento americano Platinum Equity, ha sede principale a Genova, ma è parte di un gruppo internazionale con diverse sedi anche in Polonia, Francia, Germania, Finlandia, Singapore e Miami, negli USA. In Italia è presente anche a Monfalcone (GO), con uno stabilimento la cui attività si focalizza principalmente sulla produzione di pannelli e soffitti a vista per l’allestimento delle cabine.
«Pannelli ed elementi di rivestimento di varia tipologia – precisa Alberto Malatesta, Plant Manager di De Wave – che devono soddisfare elevata precisione e qualità per garantire poi gli attesi requisiti estetici e di sicurezza, rispetto agli elevati standard di settore richiesti, nonché soddisfare i rigidi termini di consegna».
Peculiarità per il cui raggiungimento oggi l’azienda trova una valida e sicura alleata anche nella tecnologia fornita e installata nel 2021 da Prima Power. Stiamo parlando di una nuova linea di produzione PSBB in versione Direct, in grado di processare lamiere partendo da un magazzino di stoccaggio, automatizzando la gestione del materiale e delle informazioni, combinando i singoli processi produttivi in un completo processo flessibile e perfettamente integrato.

DAL TAGLIO MANUALE ALL’AUTOMAZIONE DI FABBRICA
Il sistema di produzione compatto Prima Power PSBB (acronimo di Punching, punzonatura – Shearing, cesoiatura – Buffering, immagazzinamento temporaneo – Bending, piegatura) trasforma automaticamente le lamiere grezze in componenti già piegati e di alta qualità. Il flusso del materiale può essere organizzato con la massima flessibilità: per il trasferimento dei pezzi direttamente alla piegatura automatica, per il bilanciamento delle diverse esigenze di tempo di piegatura e punzonatura/cesoiatura, per l’uscita dal sistema e per l’introduzione di nuovo materiale al suo interno. La funzione di buffering, flessibile e versatile, assicura di scegliere sempre un funzionamento ottimale in termini di costi e tempi di produzione, indipendentemente dall’attività in corso. La produttività offerta da questo concetto deriva infatti dalla intrinseca integrazione di un sistema di punzonatura servoelettrica versatile, dalla cesoiatura servoelettrica integrata, dalla piegatura anch’essa servoelettrica, coordinati da un sofisticato software che assicura gli ottimali flussi dei materiali e delle fasi di processo.
«De Wave – rileva Malatesta – ha scelto di investire nelle tecnologie di Prima Power per aumentare il proprio flusso tecnologico e produttivo, e ottenere un’efficienza più alta per garantire una maggiore produttività. La decisione è stata motivata anche dalla precisa volontà di portare progressivamente al proprio interno il 100% della produzione dei “gusci” delle pannellature delle cabine, fino ad ora data in gran parte in outsourcing».
Inoltre, grazie all’inserimento di altre tecnologie di automazione e di assemblaggio, il nuovo impianto Prima Power ha permesso anche di passare da una produzione per lotto alla ben più snella ed efficace a flusso continuo, ovvero “one piece flow”, incrementando anche qualità e competitività.
«La nuova linea – aggiunge Malatesta– ha permesso di garantire la ripetibilità di processo e di prodotto, fattore essenziale e determinante per la nostra attività, in quanto la parte estetica è proprio relativa alla giunzione, ovvero al giunto tra un pannello e l’altro, che non deve presentare alcuna imperfezione. Rispetto all’aumentata produttività, la stessa è stata resa possibile in seguito all’eliminazione dell’installazione di un profilo di giunzione fissato meccanicamente, grazie alle perfette pieghe ottenibili che permettono incastri precisi, con tolleranze molto ridotte».
Il nuovo impianto ha dunque permesso a De Wave di compiere un importante miglioramento operativo, passando da un processo di taglio prettamente manuale a una vera e propria automazione di fabbrica.

DALLO STOCCAGGIO ALLA PRESSOPIEGATURA IN MODO RAPIDO E PRECISO
La dotazione scelta per il nuovo sistema PSBB da De Wave include il magazzino di stoccaggio lamiere FL, in asservimento alla Combinata punzonatura/cesoia Shear Genius SG 1530 e alla pannellatrice Express Bender EBe 2720.
«Tecnologie di alto profilo – continua Malatesta – che nella fase di allestimento e avvio dell’impianto hanno reso necessaria la formazione dei nostri addetti, in quanto si sono trovati a passare dal gestire un processo tradizionale, eseguito con cesoia, punzonatrice e pressopiegatrice, ormai risalenti ai primi anni Duemila, a una linea completamente automatizzata. Un percorso di crescita che ha però portato un costante e continuo miglioramento delle capacità degli stessi addetti, ottenendo dei risultati ad oggi molto soddisfacenti».
Più nel dettaglio la linea automatica di produzione si compone di tre zone operative principali. Una prima dove è situato il magazzino di stoccaggio a torre FL a 10 posizioni nel quale viene caricata la lamiera pronta per essere processata. La seconda zona è di competenza della prima stazione operativa dove è posta la macchina combinata cesoiatrice-punzonatrice Shear Genius SG 1530 e dove viene effettuata l’ottimizzazione del nesting. Alla terza zona, ovvero alla pannellatrice Express Bender EBe 2720, confluiscono le parti cesoiate e punzonate per la realizzazione del “guscio” finale. A fondo linea sono previste due differenti uscite materiale: una dedicata ai “gusci” finiti, che vengono quindi sistemati su apposite rastrelliere; un’altra alla quale confluiscono invece quei “gusci” pannellati che necessitano di una piega aggiuntiva, effettuata da un’ulteriore pressopiegatrice, sempre Prima Power, frontalmente posizionata alla linea, per poi finire a loro volta su altre rastrelliere e continuare il flusso produttivo.
«L’implementazione della nuova linea – ribadisce Malatesta – ha permesso di internalizzare una parte importante di produzione dei “gusci”, con conseguente rispetto dei sempre più rigidi tempi di consegna, un abbattimento delle non conformità e un prodotto qualitativamente ancora più valido. Oggi siamo in grado di realizzare gusci in lamiera in circa 40 – 80 secondi a flusso continuo, a seconda della loro complessità e delle pieghe del pannello. Per un totale di circa 15.000 pannelli/mese ma con un’ambiziosa proiezione a regime di superare le 18.000 unità al mese. Pannelli pensati e lavorati anche per garantire un montaggio veloce e privo di errori in cantiere, normalmente in spessori compresi tra 0,5 e 0,8 mm».
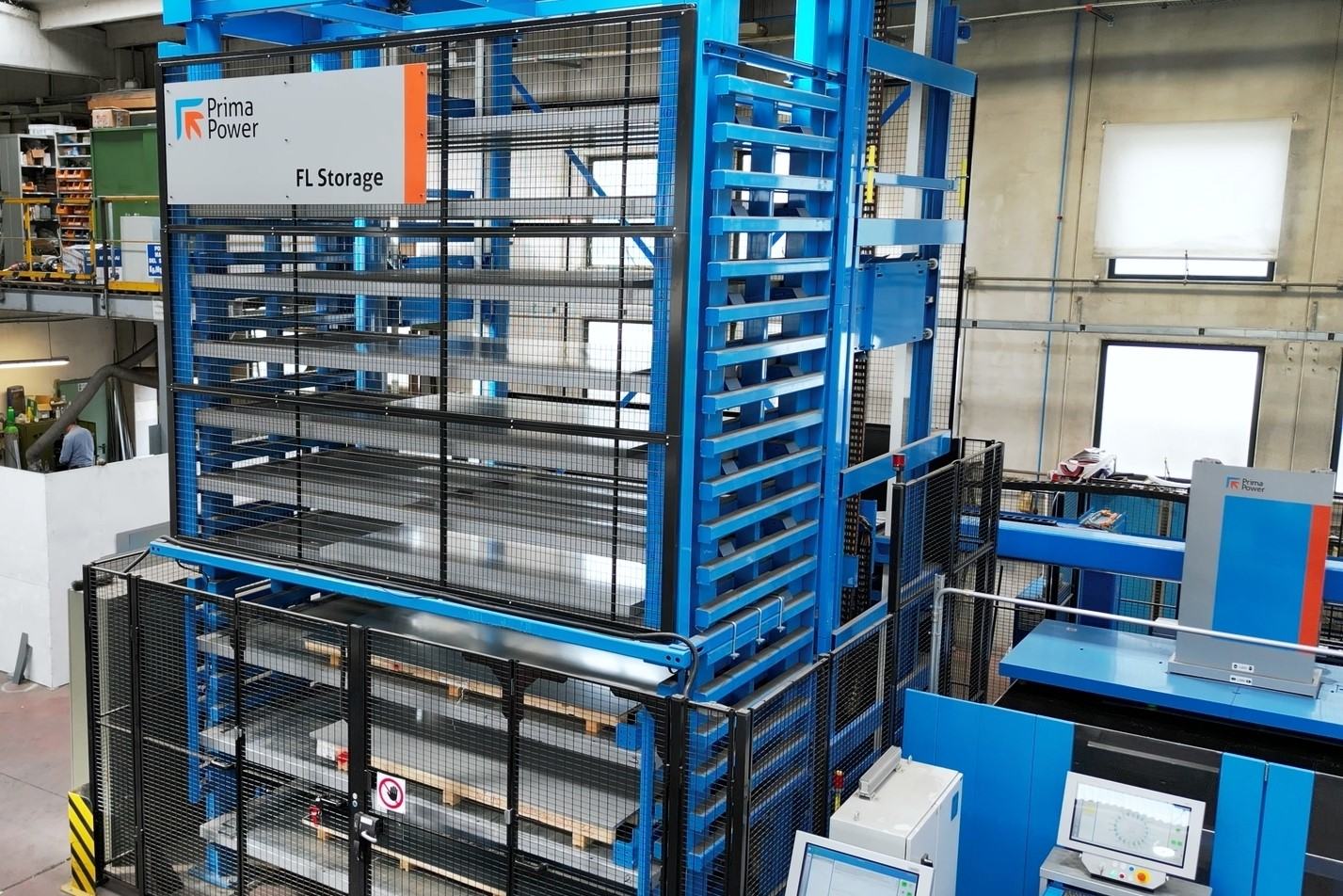
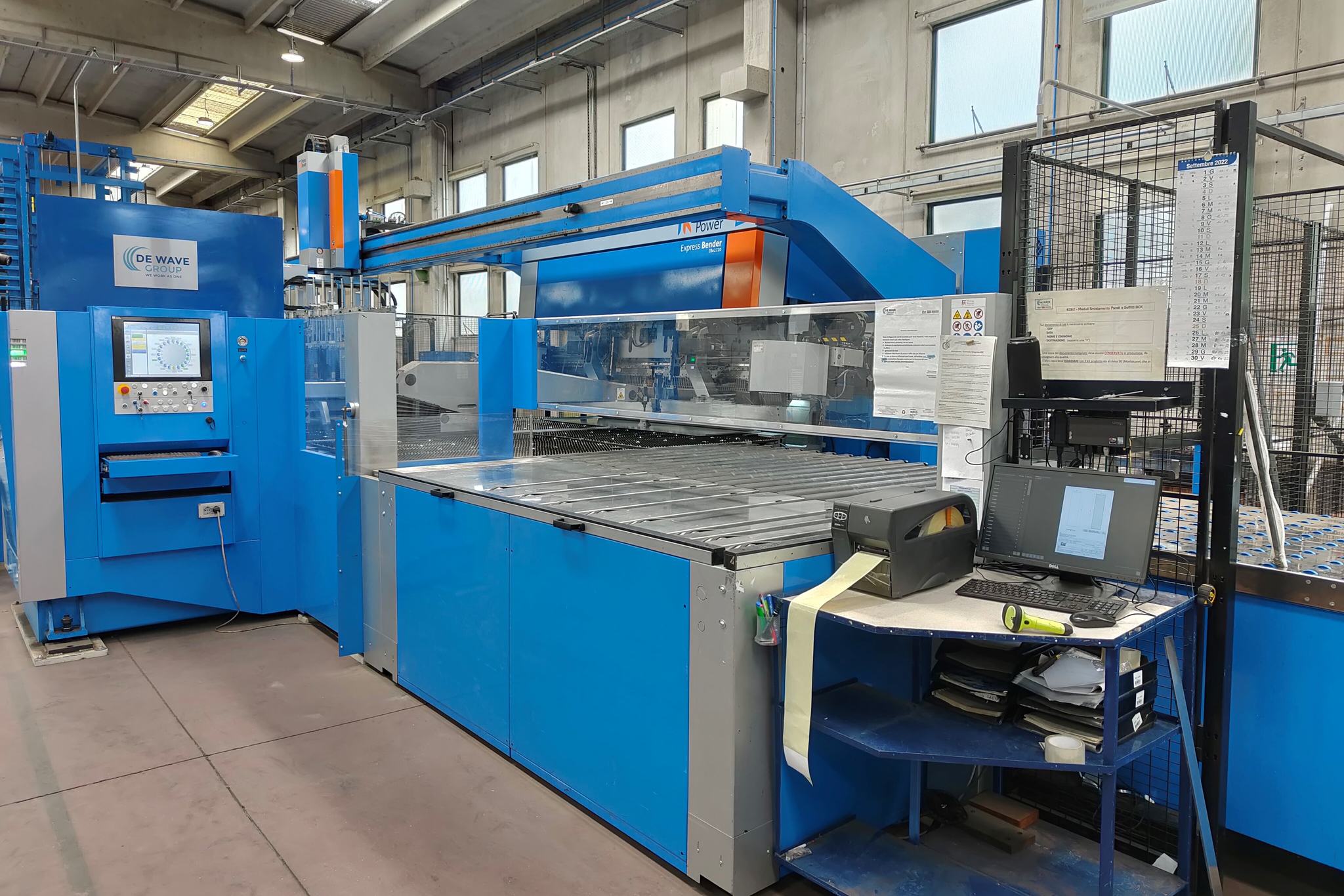
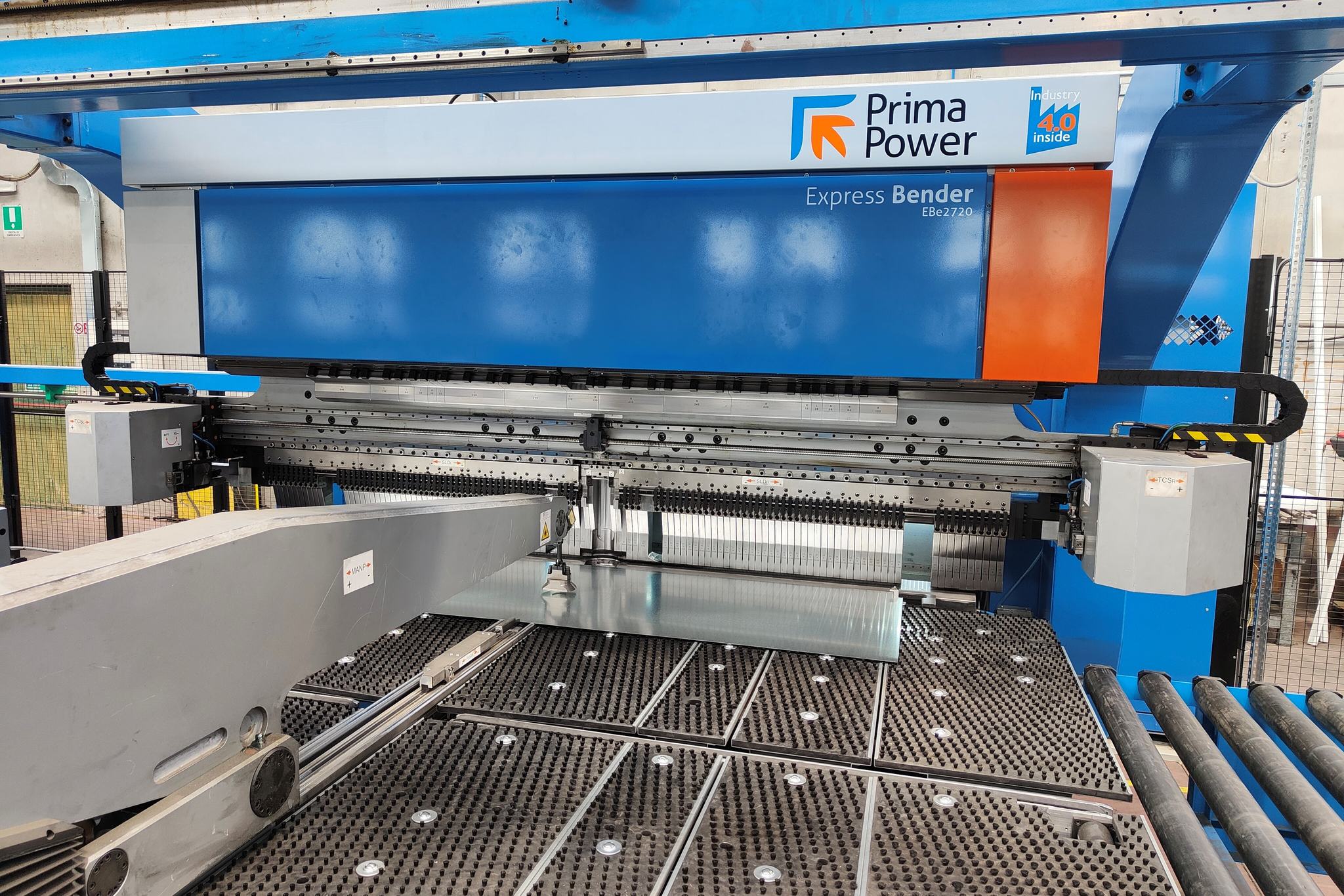
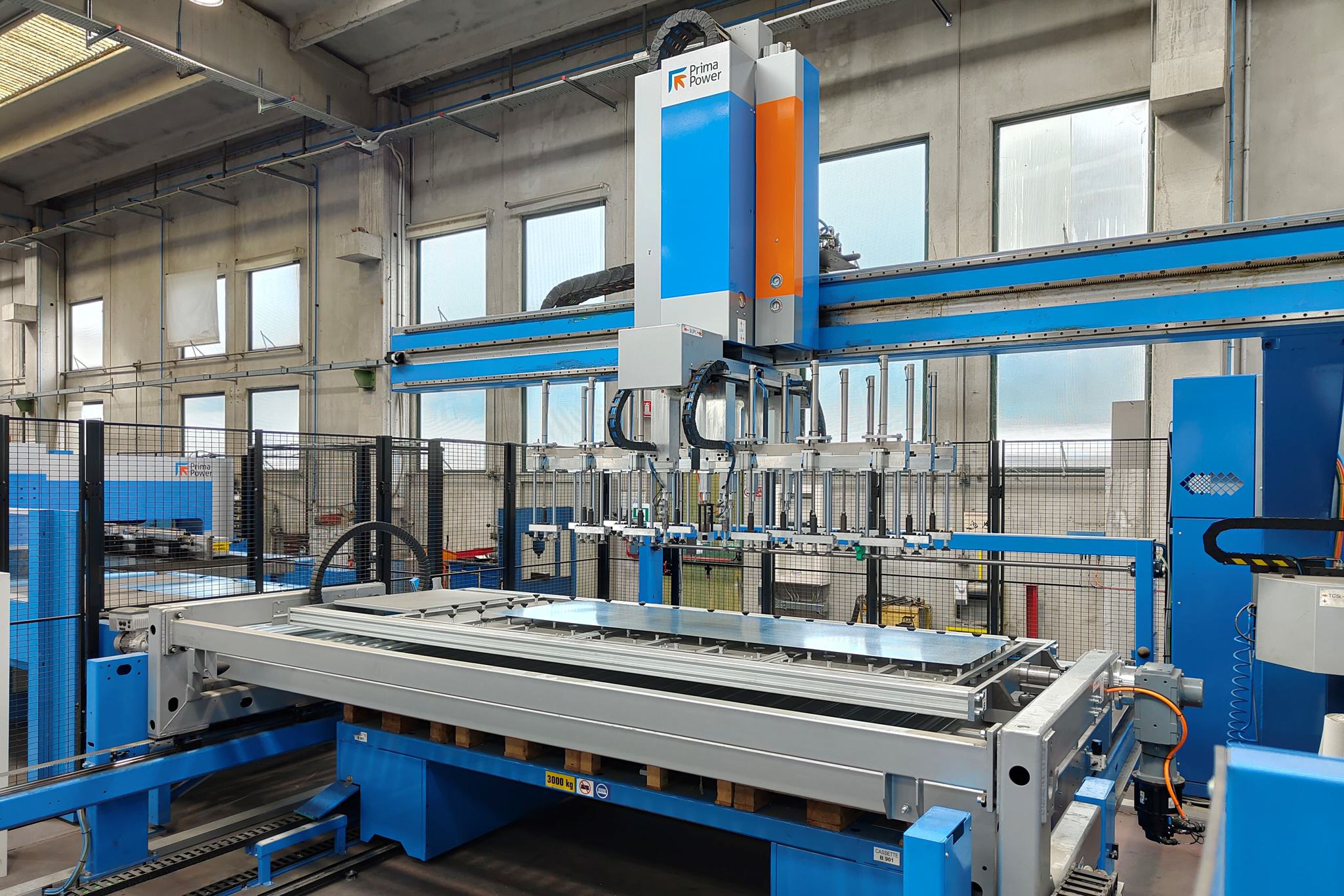
IL VALORE AGGIUNTO DELLA PROGRAMMAZIONE PARAMETRICA
La configurazione di linea scelta da De Wave risulta perfettamente calibrata sulle specifiche esigenze, rappresentando un ottimo compromesso che unisce flessibilità, compattezza e produttività, con il sistema PCD chiamato a bilanciare ed equilibrare i tempi tra punzonatrice e pannellatrice.
«Anche la parte software – sottolinea lo stesso Malatesta – si è rivelata chiave nella crescita operativa interna. Da questo punto di vista la programmazione parametrica è stata per esempio uno dei requisiti dibattuti e richiesti in fase di valutazione della scelta dell’impianto, in quanto i nostri pannelli si differenziano essenzialmente nelle dimensioni, partendo da una geometria base. Una volta definita la sezione del pannello di riferimento, il sistema permette rapidamente di passare in produzione i kit in una delle variabili già memorizzate, agendo su pochi parametri di taglio e piega, col vantaggio di poter massimizzare la velocità di produzione per poi uscire dalla linea pronti per l’assemblaggio, l’elettrificazione, l’imballaggio e la spedizione in cantiere».
Spedizione in cantiere trattata con altrettanta cura e attenzione per il mantenimento di tutti i requisiti, incluso quelli già menzionati relativi all’estetica e alla sicurezza.
«Requisiti di sicurezza – aggiunge Malatesta – che a pannello finito corrispondono per esempio al soddisfacimento di resistenza al fuoco e a un determinato carico strutturale. Ricordiamo da questo punto di vista non solo le sollecitazioni continue cui sono sottoposti i manufatti, dato che si tratta di elementi montati su imbarcazioni, ma anche il fatto che gli stessi siano a contatto con un ambiente marino che potrebbe portare a fenomeni di corrosione interferendo sulla loro durabilità».
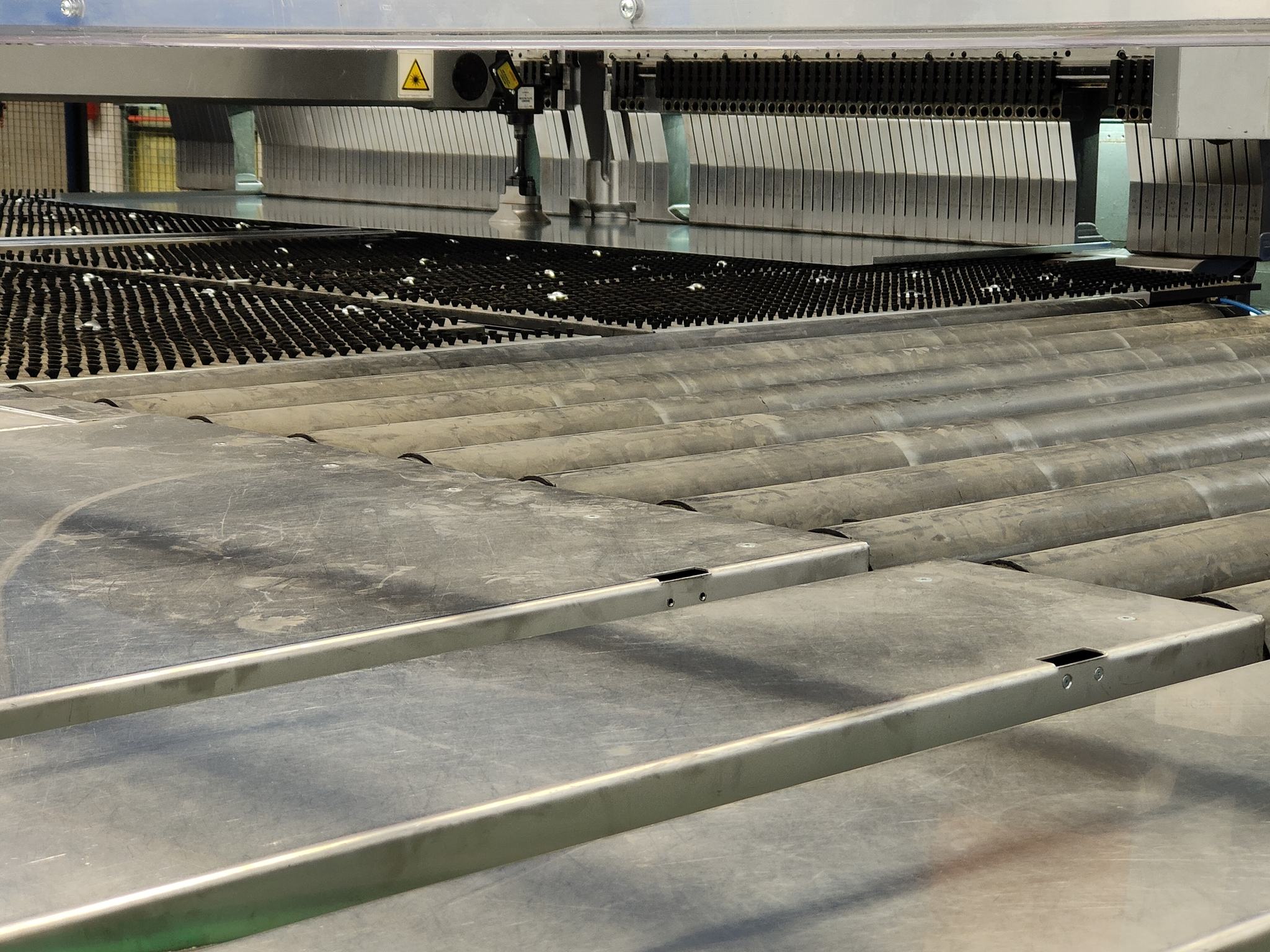
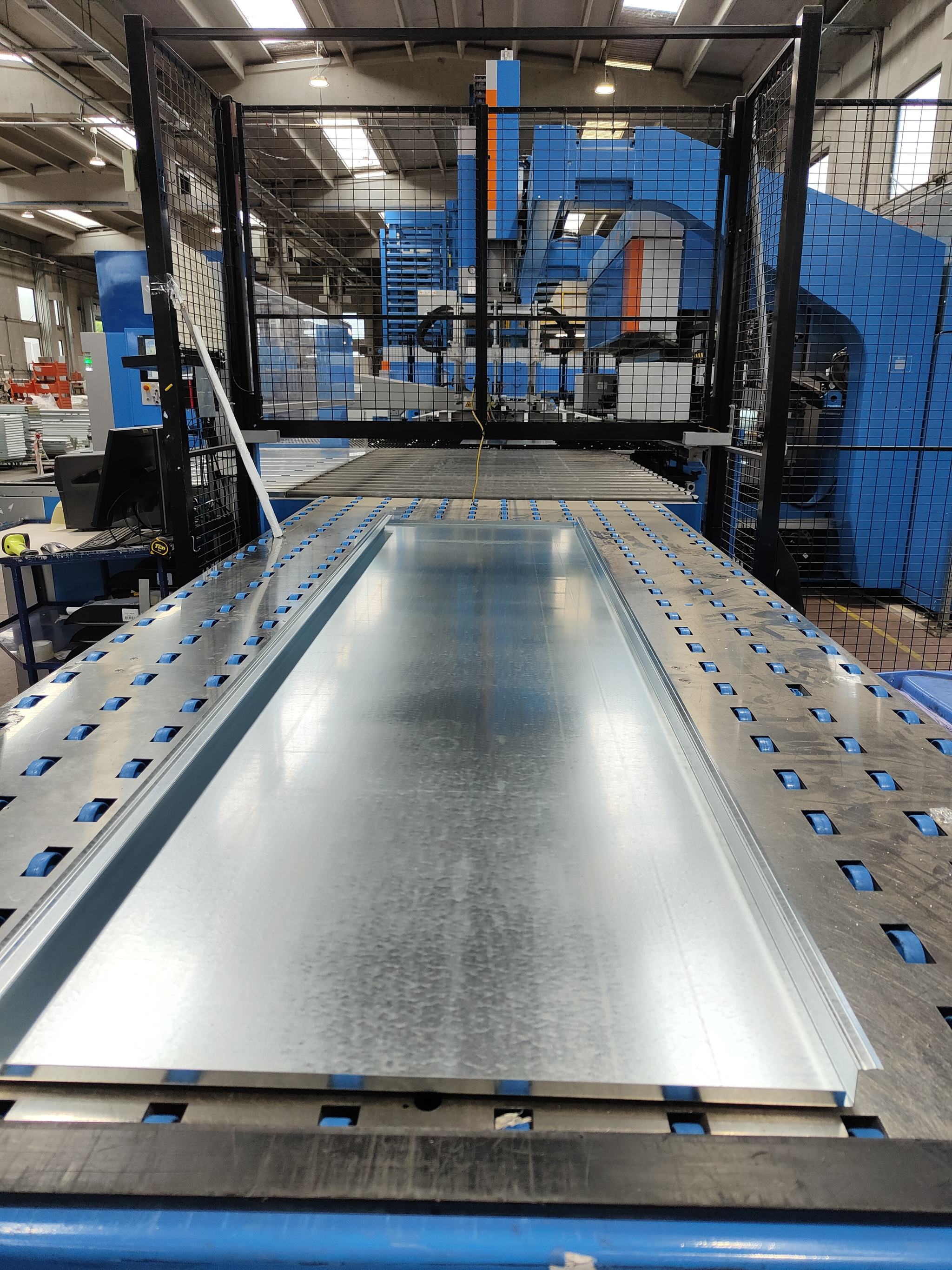
DAL PANNELLO AL PRODOTTO FINITO “CHIAVI IN MANO”
L’integrazione della nuova linea Prima Power ha permesso a De Wave di ridisegnare il proprio asset operativo, come già sottolineato, riportando al proprio interno una maggiore percentuale di produzione dei “gusci” pannellati, ed anche attivandone altre, anch’esse fatte precedentemente in outsourcing, come per esempio la realizzazione dei box igiene eseguite negli stabilimenti polacchi dell’azienda.
«Nel plant di Monfalcone – afferma sempre Malatesta – dove lavoriamo oggi circa 200mila mq di pannelli finiti all’anno, ci avvaliamo mediamente di un’ottantina di addetti distribuiti nei vari reparti e impegnati sulle varie linee di processo».
Linee di processo che, oltre alla nuova PSBB, includono anche una linea di assemblaggio semiautomatica, a flusso continuo, asservita da due robot (uno che realizza il taglio dell’isolante e l’altro lo spruzzo della colla), affiancate da due pressopiegatrici e da una punzonatrice, oltre a una profila per la realizzazione delle doghe e a una cesoia.
«Abbiamo mantenuto come backup – prosegue Malatesta – alcune postazioni di assemblaggio manuale dei pannelli, per supplire in caso di fermi impianto, di interventi di manutenzione o di picchi di lavoro estremi».
A questo proposito, in ottica di miglioramento e di crescita continua, sono stati comunque già pianificati nuovi investimenti in tecnologie, sempre presso la sede friulana, per potenziare e ottimizzare ulteriormente il flusso produttivo, sia con integrazioni, sia con sostituzioni di macchine divenute ormai obsolete.
«La vision dell’azienda – conclude Malatesta – è quella di integrare nel navale alla parte di produzione a vista, ovvero pannelli, soffitti e box igiene, anche tutta la parte impiantistica. Motivo per cui si sta muovendo sul mercato non solo con investimenti in tecnologia, ma anche con acquisizioni societarie per riuscire a fornire un allestimento sempre più completo, “chiavi in mano”».
In sintesi, proporsi come produttore e contractor sempre più globale in grado di servire l’intera gamma di allestimenti interni per navi da crociera, grandi yacht e imbarcazioni fluviali, nuove ma anche con attività di refitting.
Implementation of this new line has allowed us to insource a significant portion of our 'shell' production, allowing us to achieve increasingly strict delivery times, a reduction in non-conformities and an even better-quality product.
Stai cercando una soluzione simile per la tua azienda? Ecco qui
PSBB
SISTEMI DI PRODUZIONE FLESSIBILI
Un sistema di produzione flessibile
Shear Genius
MACCHINE COMBINATE PER PUNZONATURA E CESOIATURA