
De Wave, Effizienz und Produktivität setzen sich durch

Sie fahren über die Weltmeere und beherbergen zwischen wenigen dutzend und einigen tausend Personen. Die Rede ist von Kreuzfahrtschiffen, grossen Yachten und Binnenschiffe, für welche die De Wave-Group, verschiedene Arten von Möblierung und Beschläge herstellt, alle mit den integrierten Technologien einer automatischen Hochleistungslinie von Prima Power.
Um für immer auf einem Kreuzfahrtschiff leben zu können, muss man nur ein paar Jahre warten und eine Million Dollar aufbringen (so die jüngste Ankündigung eines Kreuzfahrtunternehmens, das als erstes weltweit ein privates Wohnschiff mit mehr als 500 Appartements entwickelte): Glücklicherweise ist eine kürzere Reise mit einem Kreuzfahrtschiff sehr viel preiswerte, um mit diesem bekannte und weniger bekannte Orte auf allen Kontinenten zu besuchen. Tatsächlich gibt es eine große Auswahl an Schiffen, die zwischen wenigen Dutzend und einigen Tausend Personen (Passagiere und Besatzung) Platz bieten, darunter große Kreuzfahrtschiffe, Yachten und nicht weniger gut ausgestattete Binnenschiffe. So wie die, für die De Wave Möbel und Beschläge herstellt. Diese machen das Unternehmen mit seinem ausgedehnten Netz von Niederlassungen und Produktionsstätten, das die Yacht- und Freizeitschifffahrtsindustrie auf der ganzen Welt unterstützt, zu einem bevorzugten Partner.
De Wave ist aus einer Fusion von fünf Unternehmen hervor gegangen und ist heute eine hundertprozentige Tochtergesellschaft des amerikanischen Investmentfonds Platinum Equity. Das Unternehmen hat seinen Sitz in Genua, Italien, ist aber Teil einer internationalen Gruppe mit mehreren Niederlassungen in Polen, Frankreich, Deutschland, Finnland, Singapur und Miami, USA. In Italien verfügt das Unternehmen auch in Monfalcone (GO) ein Werk, das sich hauptsächlich auf die Herstellung von Paneelen und Decken für die Ausstattung von Kabinen konzentriert.
„Die verschiedenen Arten von Paneelen und Verkleidungselemente“, so Alberto Malatesta, Werksleiter bei De Wave, „müssen extreme Präzisions- und Qualitätsstandards erfüllen, um die hohen Anforderungen der Branche an Ästhetik und Sicherheit zu gewährleisten und es müssen strenge Lieferfristen eingehalten werden.“
Diese besonderen Merkmale werden heute mit der soliden und zuverlässigen Technologie von Prima Power sichergestellt, welche im Jahr 2021 geliefert und installiert wurde. Die Rede ist natürlich von der neuen Direct Version der PSBB-Produktionslinie, die Bleche aus einem Lager verarbeiten, das Material- und Informationsmanagement automatisieren und die einzelnen Produktionsprozesse zu einem flexiblen und voll integrierten Gesamtprozess zusammenführen kann.

VOM MANUELLEN ZUSCHNITT ZUR AUTOMATISCHEN FABRIK
Das kompakte Produktionssystem Prima Power PSBB (Punching, Shearing, Buffering, Bending - Stanzen, Scheren, Puffern, Biegen) formt Blechzuschnitte automatisch in hochwertige, fertig gebogene Bauteile um. Der Materialfluss kann mit maximaler Flexibilität organisiert werden: zur direkten Übergabe von Werkstücken an den Biegeautomaten, zum Ausgleich unterschiedlicher Biege- und Stanz-/Schneidezeitanforderungen, zum Ausschleusen aus dem System und zum Einschleusen von neuem Material in das System. Die flexible und vielseitige Pufferfunktion garantiert, unabhängig von der jeweiligen Aufgabe, jederzeit einen kosten- und zeitoptimierten Betrieb. Die Produktivität dieses Konzepts wird von der Integration eines vielseitigen servoelektrischen Stanzsystems mit integrierten servoelektrischen Scher- und Biegesystemen ermöglicht, die von einer ausgeklügelten Software gesteuert werden und einen optimalen Materialfluss und optimale Prozessablauf gewährleisten.
„De Wave“, bemerkt Malatesta, „hat sich für die Investition in die Technologien von Prima Power entschieden, um den technologischen und produktiven Ablauf zu verbessern, mehr Effizienz zu erreichen und damit eine höhere Produktivität zu gewährleisten. Die Entscheidung wurde weiterhin vom konkreten Wunsch geleitet, schrittweise 100 % der Produktion der Kabinenpaneele selbst zu übernehmen, denn sie wurden bisher weitgehend ausgelagert“.
Durch die Integration zusätzlicher Automatisierungs- und Montagetechnologien ermöglicht das neue Werk, geliefert von Prima Power, außerdem die Umstellung von der Serienfertigung auf die wesentlich rationellere und effizientere „Losgröße Eins“, wodurch auch die Qualität und die Wettbewerbsfähigkeit gesteigert werden.
„Die neue Linie“, fügt Malatesta hinzu, „hat die Wiederholbarkeit des Prozesses und des Produkts ermöglicht, was ein wesentlicher und entscheidender Faktor für unser Geschäft ist, weil der ästhetische Aspekt stark von der Verbindung zwischen einer Paneele und der nächsten abhängt, denn sie darf keine Unvollkommenheiten aufweisen. Durch den Verzicht auf die Installation eines mechanisch befestigten Verbindungsprofils konnte die Produktivität durch die perfekten Biegungen, die präzise Verbindungen mit sehr geringen Toleranzen ermöglichen, gesteigert werden.“
Das neue System hat es De Wave ermöglicht, die Betriebsabläufe deutlich zu verbessern und von einem rein manuellen Zuschnitt zu einer automatischen Fabrik überzugehen.

SCHNELL UND PRÄZISE VON DER LAGERUNG ZUM PRESSBIEGEN
Zu den Anlagen, die für das neue PSBB-System von De Wave ausgewählt wurden, gehört das FL-Blechlager, das in Verbindung mit der Stanz-Schneide-Kombination Shear Genius SG 1530 und der Blechbiegemaschine EBe 2720 Express Bender eingesetzt wird.
„Diese Spitzentechnologien“, fährt Malatesta fort, „bedeuteten, dass unsere Mitarbeiter in der Einrichtungs- und Inbetriebnahmephase der Anlage geschult werden mussten, denn sie mussten von einem traditionellen Prozess mit einer Schere, einer Stanzmaschine und einer Abkantpresse aus den frühen 2000er Jahren zu einer vollautomatischen Linie wechseln. Dieser Wachstumspfad hat jedoch zu einer ständigen und kontinuierlichen Verbesserung der Fähigkeiten unserer Mitarbeiter geführt, die bis heute sehr zufriedenstellende Ergebnisse erzielt haben.“
Die automatische Produktionslinie besteht aus drei Hauptbereichen. Im ersten Bereich befindet sich das FL-Turmlager mit 10 Plätzen, in dem die zu bearbeitenden Bleche gelagert werden. Der zweite Bereich ist die erste Arbeitsstation, in der sich die Shear Genius SG 1530 Combi befindet und in der die Optimierung der Verschachtelung durchgeführt wird. Der dritte Bereich ist der Express Bender EBe 2720. Hier werden die gescherten und gestanzten Teile zur Herstellung der endgültigen „Hülle“ zugeführt. Am Ende der Linie gibt es zwei verschiedene Materialausgänge: einen für fertige „Hüllen“ und getäfelte „Hüllen“. Erstere werden auf spezielle Gestelle gelegt und zweitere, die eine zusätzliche Biegung benötigen. Dies geschieht mit einer Prima Power Abkantpresse am Anfang der Linie, bevor sie wieder auf andere Gestelle gelegt werden, um den Produktionsfluss fortzusetzen.
„Die Einführung dieser neuen Linie“, so Malatesta, „hat es uns ermöglicht, einen bedeutenden Teil unserer „Hüllen“-Produktion zurückzuholen, so dass wir immer kürzere Lieferzeiten, eine Verringerung der Nichtkonformitäten und eine noch bessere Produktqualität erreichen konnten. Wir sind jetzt in der Lage, abhängig von der Komplexität und Biegung der Bleche, Blechhüllen in etwa 40 bis 80 Sekunden im Durchlaufverfahren herzustellen. Zurzeit verarbeiten wir etwa 15.000 Bleche pro Monat, aber wir haben das ehrgeizige Ziel mehr als 18.000 pro Monat zu erreichen. Diese Paneelen werden auch so konstruiert und bearbeitet, dass eine schnelle und fehlerfreie Montage vor Ort gewährleistet ist, normalerweise in Stärken zwischen 0,5 und 0,8 mm.“
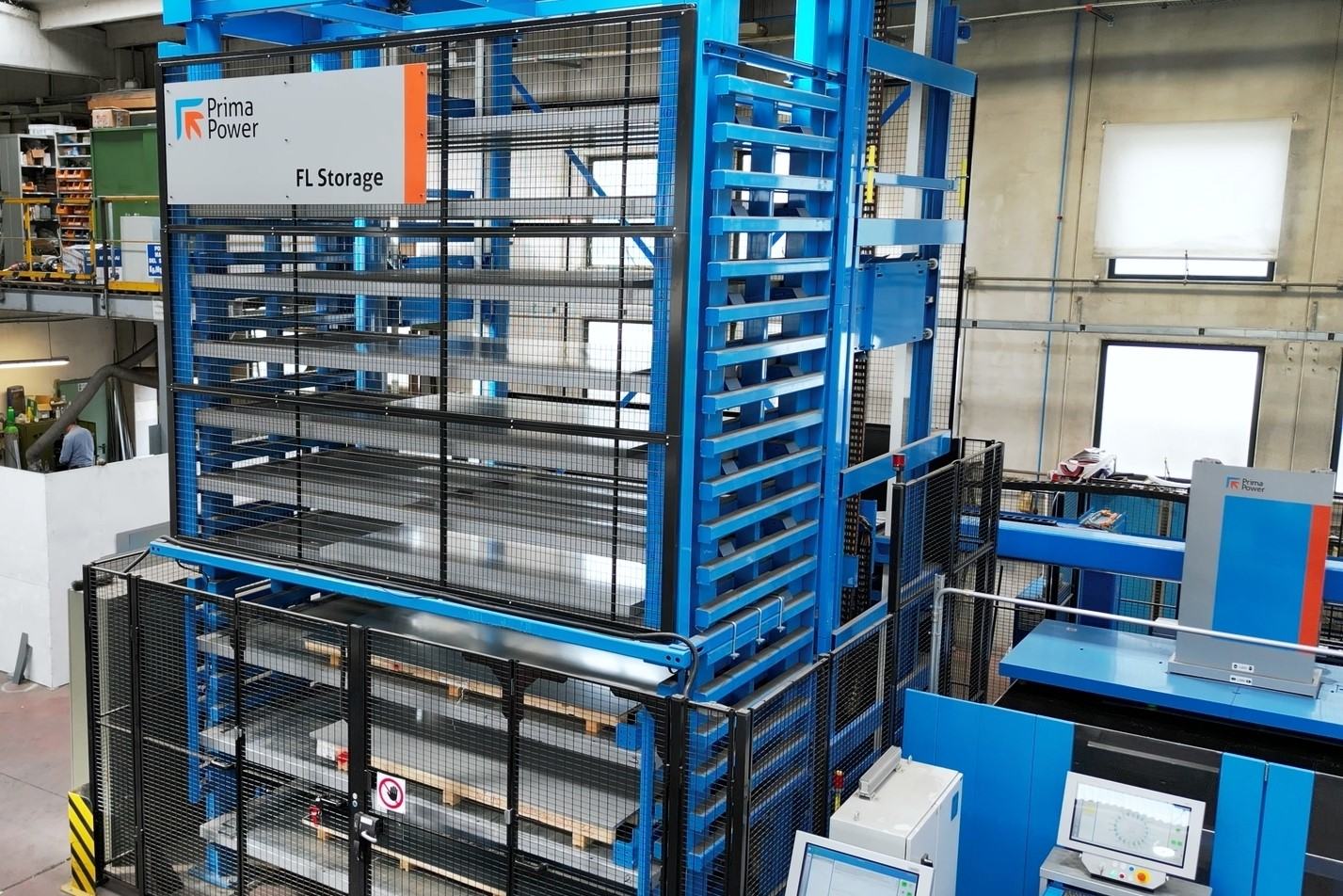
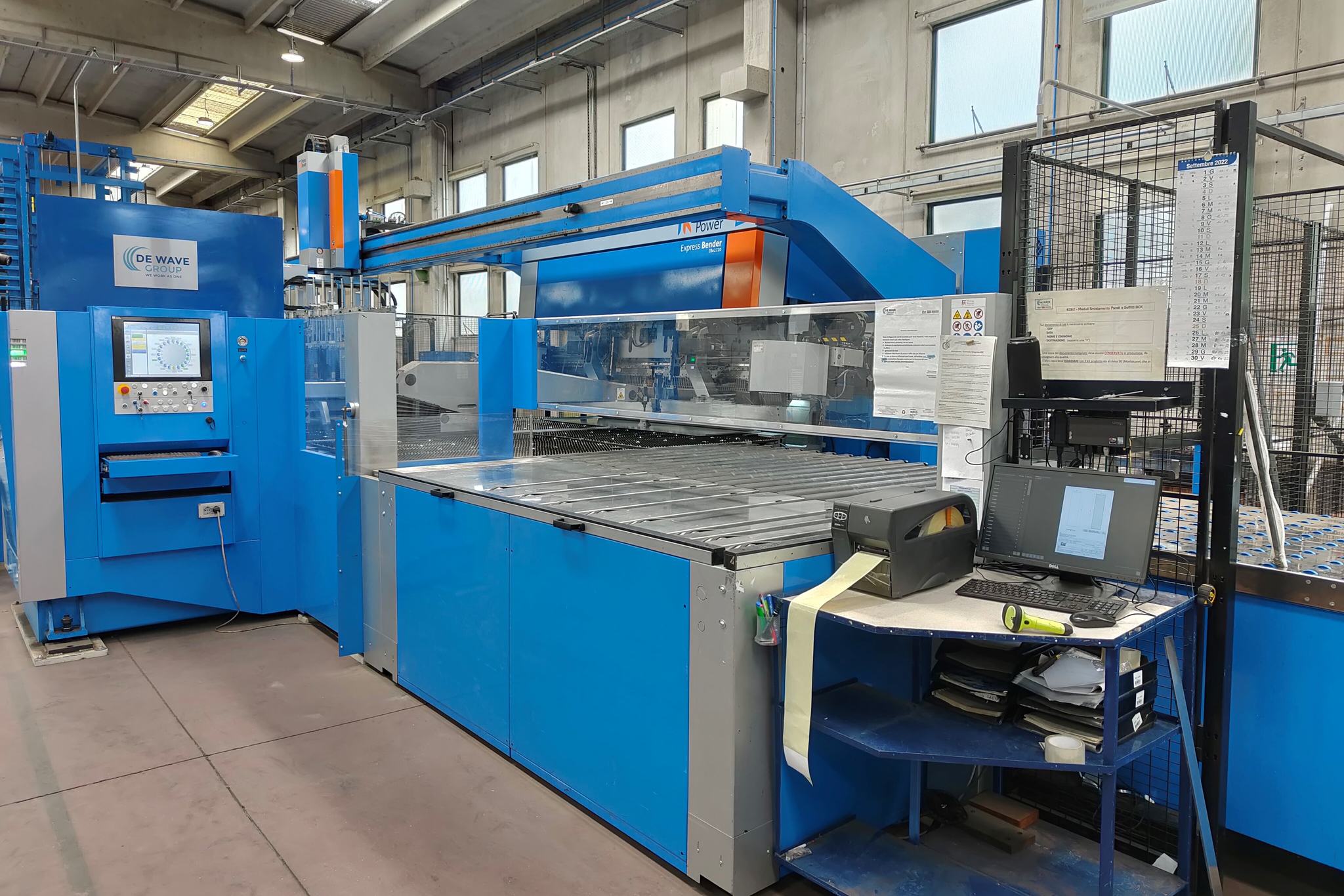
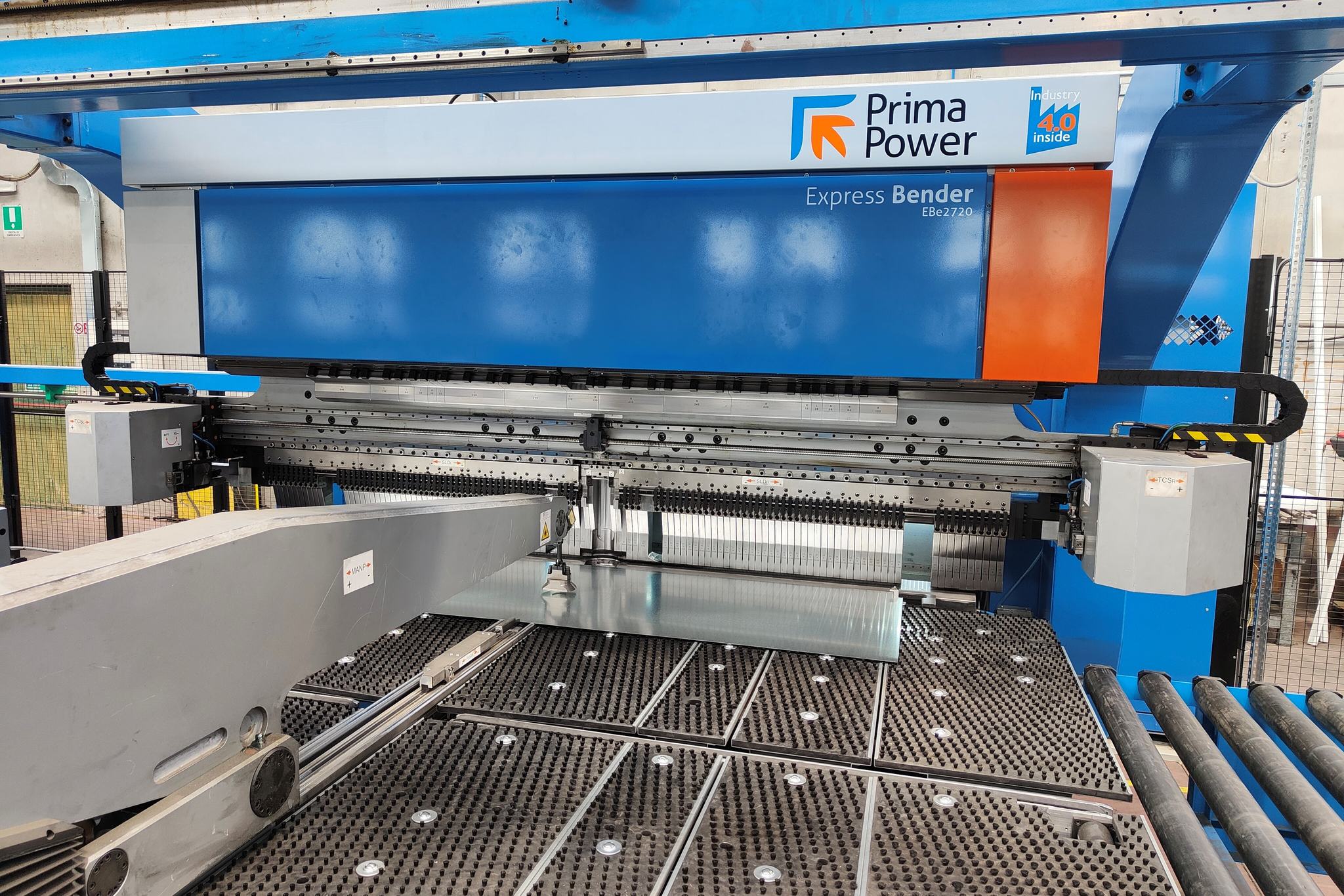
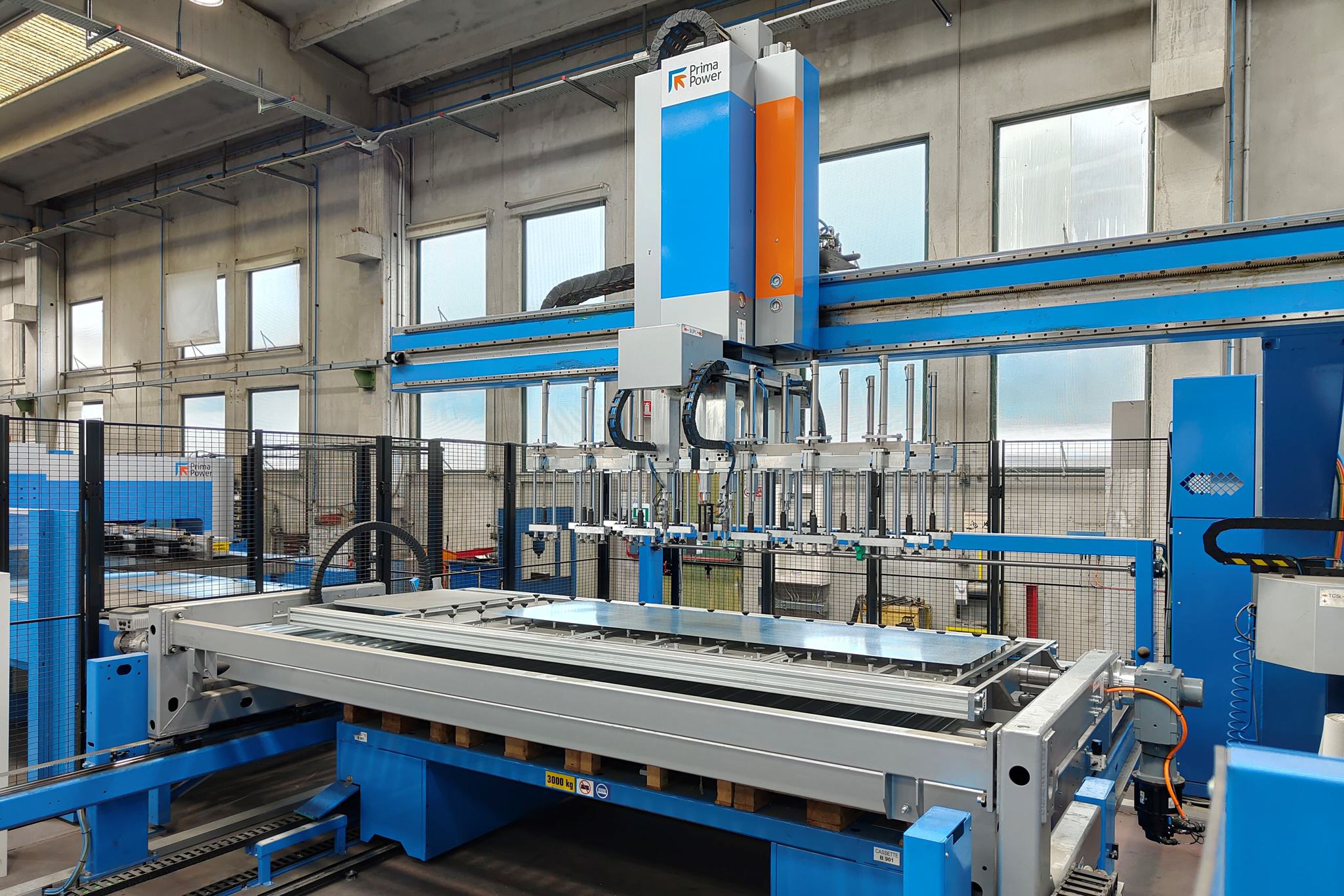
DER MEHRWERT DER PARAMETRISCHEN PROGRAMMIERUNG
Die von De Wave gewählte Linienkonfiguration ist perfekt auf die spezifischen Anforderungen abgestimmt. Sie ist ein hervorragender Kompromiss, der Flexibilität, Kompaktheit und Produktivität vereint, während das PCD-System die Zeit zwischen der Bearbeitung auf der Stanz- und Blechbiegemaschine ausgleicht und anpasst.
„Die Softwareseite“, betont Malatesta, „hat sich ebenfalls als Schlüssel für das interne betriebliche Wachstum erwiesen. Unter diesem Gesichtspunkt war die parametrische Programmierung eine der Anforderungen, die bei der Auswahl der Anlage diskutiert und gefordert wurde, da sich unsere Paneele ausgehend von einer Grundgeometrie im Wesentlichen in ihrer Größe unterscheiden. Sobald der Querschnitt der Referenzpaneele definiert ist, schaltet das System die Sets schnell auf die Produktion um, indem es eine der bereits gespeicherten Variablen verwendet und nur einige wenige Schneide- und Biegeparameter anpasst. Dies hat den Vorteil, dass die Produktionsgeschwindigkeit maximiert werden kann und die Linie dann bereit für die Montage, Verkabelung, Verpackung und den Versand an die Baustelle ist.
Der Versand zur Baustelle erfolgt mit der gleichen Sorgfalt und Vorsicht, um allen Anforderungen, einschließlich der bereits erwähnten in Bezug auf Ästhetik und Sicherheit, gerecht zu werden.„Diese Sicherheitsanforderungen“, fügt Malatesta hinzu, „entsprechen der Einhaltung der Feuerbeständigkeit und einer bestimmten strukturellen Belastung nach Fertigstellung der Paneele. In dieser Hinsicht müssen wir nicht nur an die ständigen Belastungen denken, denen die Teile ausgesetzt sind, weil sie auf Schiffen montiert werden, sondern auch an die Tatsache, dass sie mit der Meeresumwelt in Berührung kommen, was zu Korrosionserscheinungen führen und die Haltbarkeit beeinträchtigen könnte.“
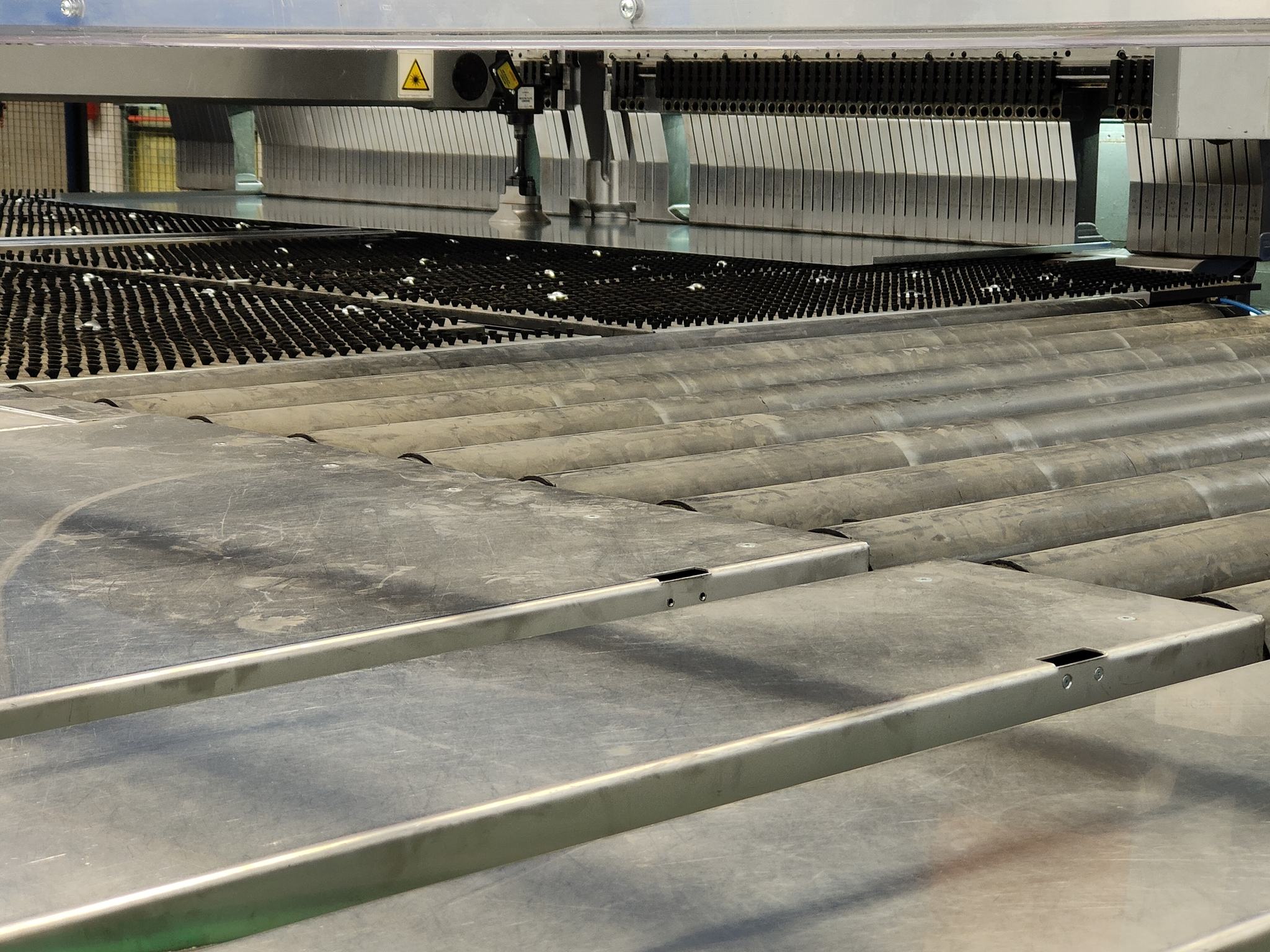
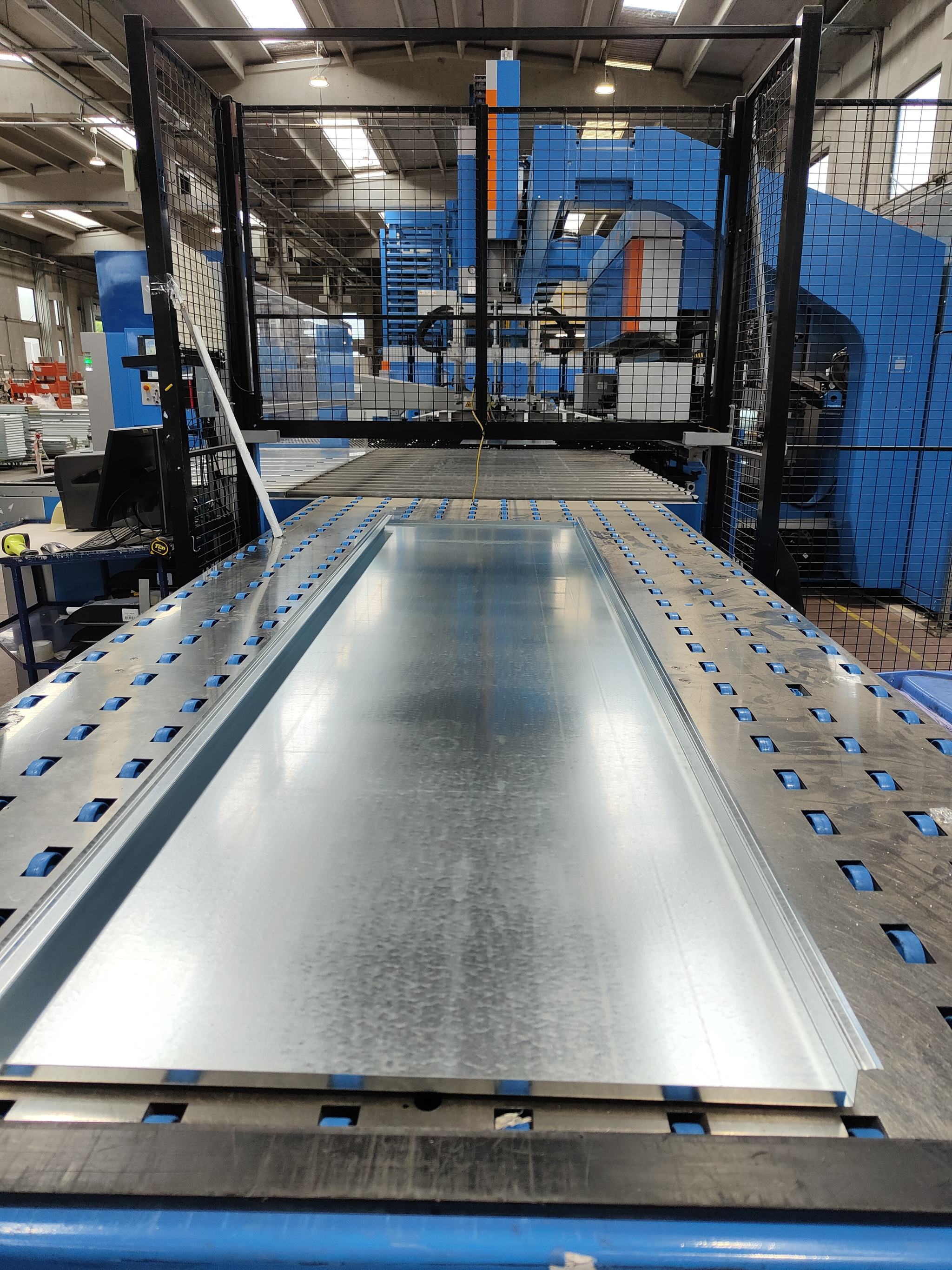
VOM PANEEL ZUR SCHLÜSSELFERTIGEN EINHEIT
Durch die Integration der neuen Produktlinie von Prima Power konnte De Wave, wie bereits erwähnt, seine Betriebsmittel umgestalten, indem der Prozentsatz der Produktion von Paneelen im eigenen Haus erhöht und andere Bereiche, welche zuvor ausgelagert waren, wie die Produktion von Nasseinheiten in die polnischen Fabriken des Unternehmens, zurückgeführt wurden.
„Das Werk in Monfalcone“, so Malatesta weiter, „in dem wir derzeit etwa 200.000 Quadratmeter fertige Blech pro Jahr verarbeiten, beschäftigt im Durchschnitt etwa 80 Mitarbeiter, die sich auf die verschiedenen Abteilungen aufgliedern und an mehreren Prozesslinien arbeiten.“
Zu diesen Prozesslinien gehören die neue PSBB sowie eine halbautomatische, kontinuierliche Montagelinie, die von zwei Robotern bedient wird (einer für den Zuschnitt der Isolierung und der andere für das Aufsprühen des Klebers), flankiert von zwei Abkantpressen und einer Stanzmaschine. Weiterhin stehen eine Profiliermaschine für die Herstellung von Stäben und eine Schere zur Verfügung.
„Wir haben einige manuelle Blechmontagestationen als Reserve behalten“, fährt Malatesta fort, „um Anlagenstillstände, Wartungsarbeiten oder extreme Arbeitsspitzen abdecken zu können.“
In diesem Zusammenhang sind bereits neue Investitionen in die Technologie (auch am Standort Monfalcone) im Hinblick auf eine kontinuierliche Verbesserung und ein Wachstum geplant, um so den Produktionsfluss, sowohl durch Ergänzungen als auch durch den Ersatz von veralteten Maschinen, weiter zu verbessern und zu optimieren.
„Die Vision unseres Unternehmens ist es“, so Malatesta abschließend, „den gesamten Anlagenbau des Schiffbaus mit der sichtbaren Produktion, insbesondere der Paneele, Decken und Nasseinheiten, zu integrieren. Deshalb investieren wir nicht nur in Technologie, sondern drängen auch mit Firmenübernahmen auf den Markt, um einen immer umfassenderen schlüsselfertigen Service anbieten zu können.“
Kurz gesagt, um sich als zunehmend globaler Hersteller und Auftragnehmer zu präsentieren, der in der Lage ist, die gesamte Palette der Innenausstattung von Kreuzfahrtschiffen, großen Yachten und Flussschiffen, sowohl neu als auch nachgerüstet, abzudecken.
Die Einführung dieser neuen Linie hat es uns ermöglicht, einen beträchtlichen Teil unserer Kabinenproduktion zurückzuholen, so dass wir immer kürzere Lieferzeiten, eine geringere Anzahl von Nichtkonformitäten und eine noch höhere Produktqualität erreichen können.
Sie suchen eine ähnliche Lösung für Ihr Unternehmen? Finden Sie es hier
Shear Genius
KOMBINIERTE MASCHINEN ZUM STANZEN UND SCHEREN