
De Wave, Efficiency and productivity take hold

They ply the seas across the world, hosting anywhere from a few dozen to a few thousand people. we’re talking about the cruise ships, large yachts and river boats for which the De Wave group produces various types of on-board furnishings and fittings, all created using integrated technologies of a high-performance automatic line by Prima Power
If ‘all you need’ to live on a cruise ship forever is to wait a couple of years and have a spare million dollars (according to a recent announcement by a cruise company that was the first in the world to unveil a private residential ship with more than 500 apartments), then luckily you need much less to spend just a few days relaxing on a cruise ship, visiting places on all the continents, well-known and lesser known. In fact, there is a wide choice of vessels that accommodate anywhere between a few dozen to a few thousand people (passengers and crew), including large cruise ships, large yachts, as well as, but no less well-equipped, river boats. Just like those for which De Wave produces furnishings and fittings, making it a reference contractor with a vast network of offices and production facilities that supports the yachting and pleasure boating industry globally.
Created from a merger of five companies, today De Wave is a wholly owned subsidiary of the American investment fund Platinum Equity. It is headquartered in Genoa, Italy, but is also part of an international group with several branches in Poland, France, Germany, Finland, Singapore and Miami, USA. In Italy, it also operates in Monfalcone (GO), with a plant that focuses mainly on the production of panels and ceilings for cabin fittings.
"The various types of panels and cladding covering elements," says Alberto Malatesta, Plant Manager at De Wave, "need to meet extreme precision and quality standards to guarantee the high industry standards expected of the aesthetic and safety requirements, as well as meeting strict delivery deadlines.”
These particular features are achieved today thanks to the solid and reliable technology supplied and installed in 2021 by Prima Power. Of course, we’re talking about the new Ddirect version of the PSBB production line, which can process sheet metal from a storage warehouse, automate material and information management, and combine the individual production processes into a complete flexible and fully integrated process.

FROM MANUAL CUTTING TO FACTORY AUTOMATION
The Prima Power PSBB (Punching, Shearing, Buffering, Bending) compact production system automatically transforms blank metal sheets into high-quality, preready-bent components. The material flow can be organised with maximum flexibility: to transfer workpieces directly to the automatic bending machine, to balance different bending and punching/shearing time requirements, to exit the system and to introduce new material into the system. The flexible and versatile buffering function ensures cost- and time-optimised operation at all times, irrespective of the task at hand. Indeed, the productivity offered by this concept derives from the intrinsic integration of a versatile servo-electric punching system with integrated servo-electric shearing and bending systems, all coordinated by sophisticated software that ensures optimal material flows and process steps.
"De Wave," remarks Malatesta, "has chosen to invest in Prima Power's technologies to increase its technological and production flow, and to achieve higher efficiency thus ensuring greater productivity. The decision was also driven by the specific desire to gradually bring in-house 100% of 'shell' production for cabin panels, which until now was largely outsourced."
Moreover, by incorporating additional automation and assembly technologies, the new Prima Power plant has also made it possible to switch from batch production to the much more streamlined and efficient 'one piece flow', thereby also increasing quality and competitiveness.
"The new line," adds Malatesta, "has provided process and product repeatability, an essential and decisive factor for our business, since the aesthetic aspect is heavily dependent on the join between one panel and the next, which mustn’t have any imperfections. Increased productivity has been achieved by removing the installation of a mechanically fixed jointing profile, thanks to the perfect bends obtained, which allow precise joints with very low tolerances."
The new system has therefore enabled De Wave to make a marked operational improvement, shifting from a purely manual cutting process to true factory automation.

FROM STORAGE TO PRESS-BENDING QUICKLY AND ACCURATELY
The equipment chosen for De Wave’s new PSBB system includes the FL sheet metal storage warehouse used in conjunction with the Shear Genius SG 1530 punch/shear combi and the EBe 2720 Express Bender panel bender.
"These high-profile technologies," continues Malatesta, "have meant training our employees in the set-up and start-up phase of the plant, as they found themselves switching from handling a traditional process carried out with a shear, punching machine and press-bender dating back to the early 2000s, to a fully automated line. This growth path, however, has led to a constant and continuous improvement in the skills of our employees, achieving very satisfactory results to date."
In particular, the automated production line consists of three main operating areas. The first is where the 10-position FL tower storage warehouse is located, where sheet metal ready to be processed is loaded. The second area is the first operating station where the Shear Genius SG 1530 combi is located and where nesting optimisation takes place. The third area is the Express Bender EBe 2720 and this is where sheared and punched parts are fed into to create the final 'shell'. There are two different material outlets at the end of the line: one for finished "shells", which are then placed on special racks; and another into which panelled "shells" that require an additional bend are fed. This is done by a another Prima Power bending machinepress brake at the front of the line, before being placed back on other racks to continue the production flow.
"Implementation of this new line," Malatesta reiterates, "has allowed us to insource a significant portion of our 'shell' production, allowing us to achieve increasingly strict delivery times, a reduction in non-conformities and an even better qualitybetter-quality product. We are now able to produce sheet metal shells in about 40 to 80 seconds in continuous flow, depending on their complexity and panel bends. We're currently sitting at a total of about 15,000 panels/month, but with an ambitious forecast of more than 18,000 per month. These panels are also designed and machined to ensure fast and error-free assembly on site, normally in thicknesses between 0.5 and 0.8 mm."
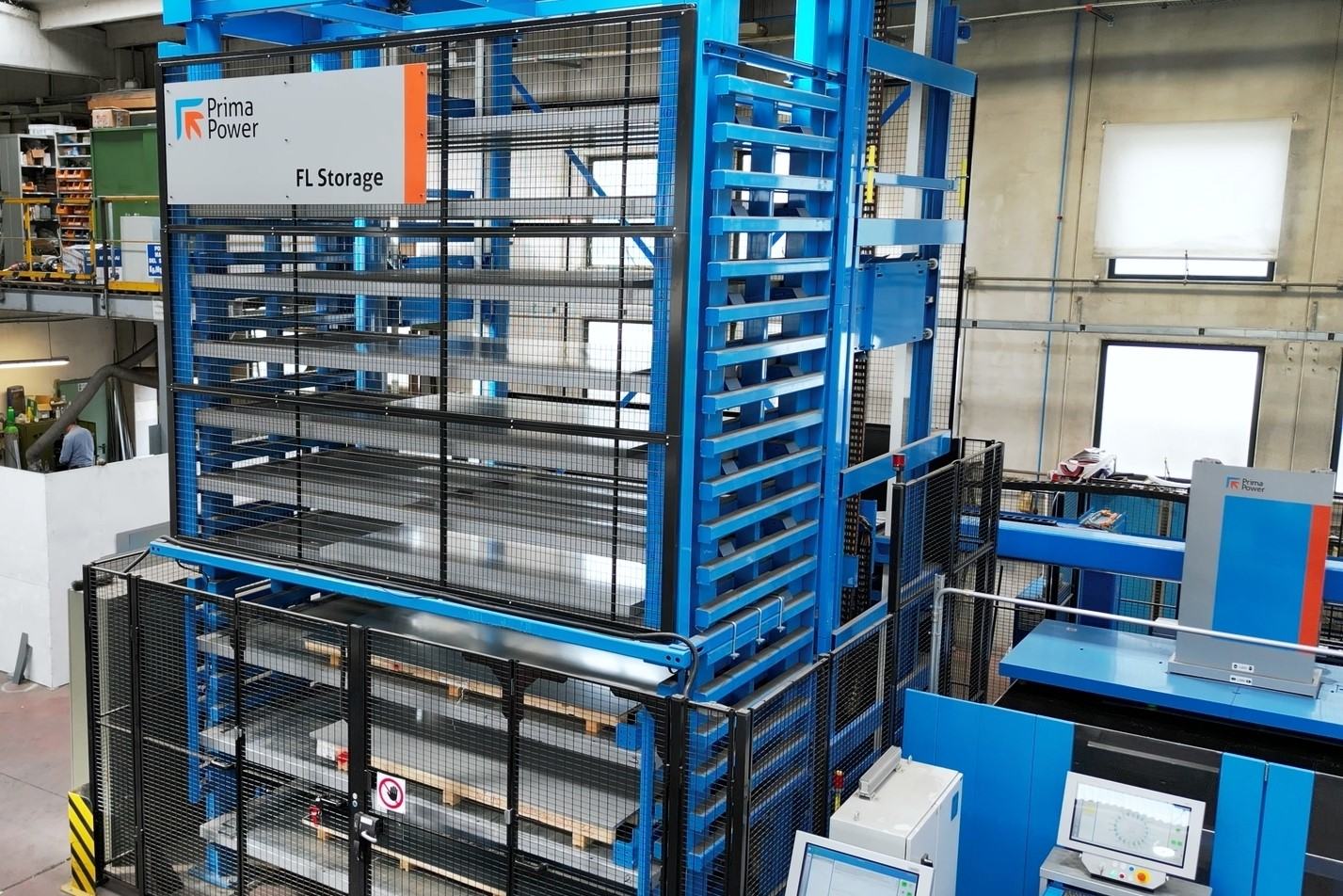
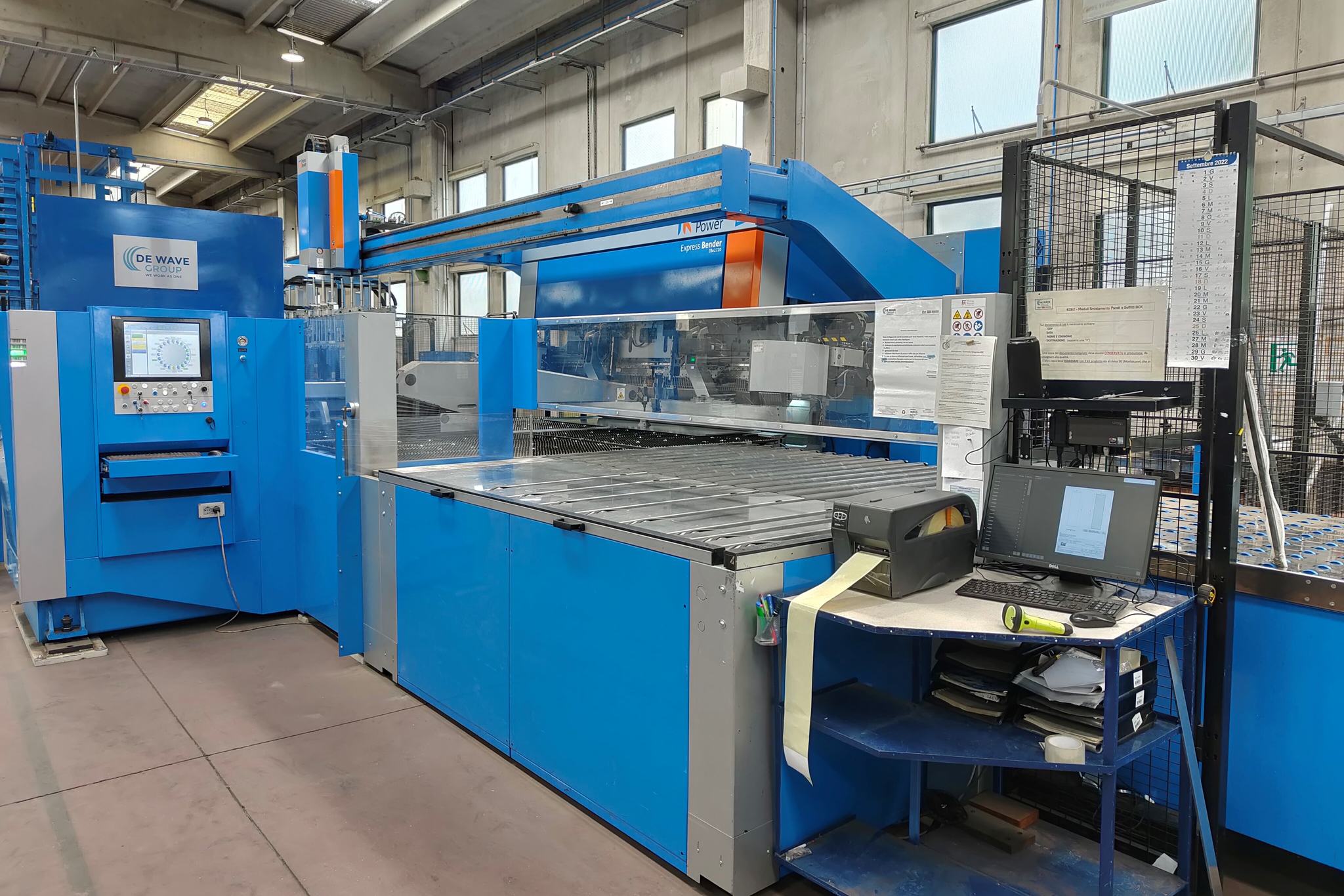
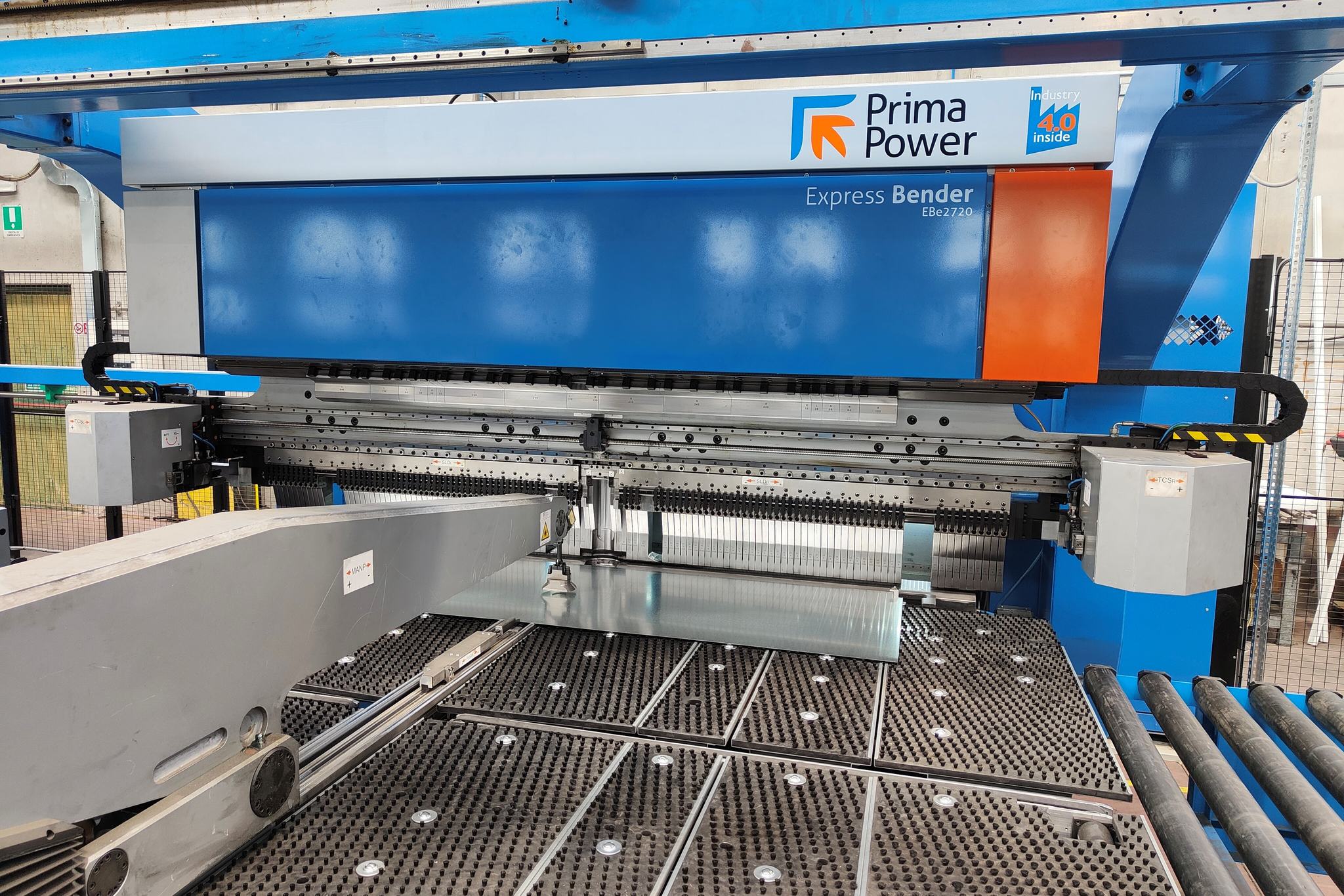
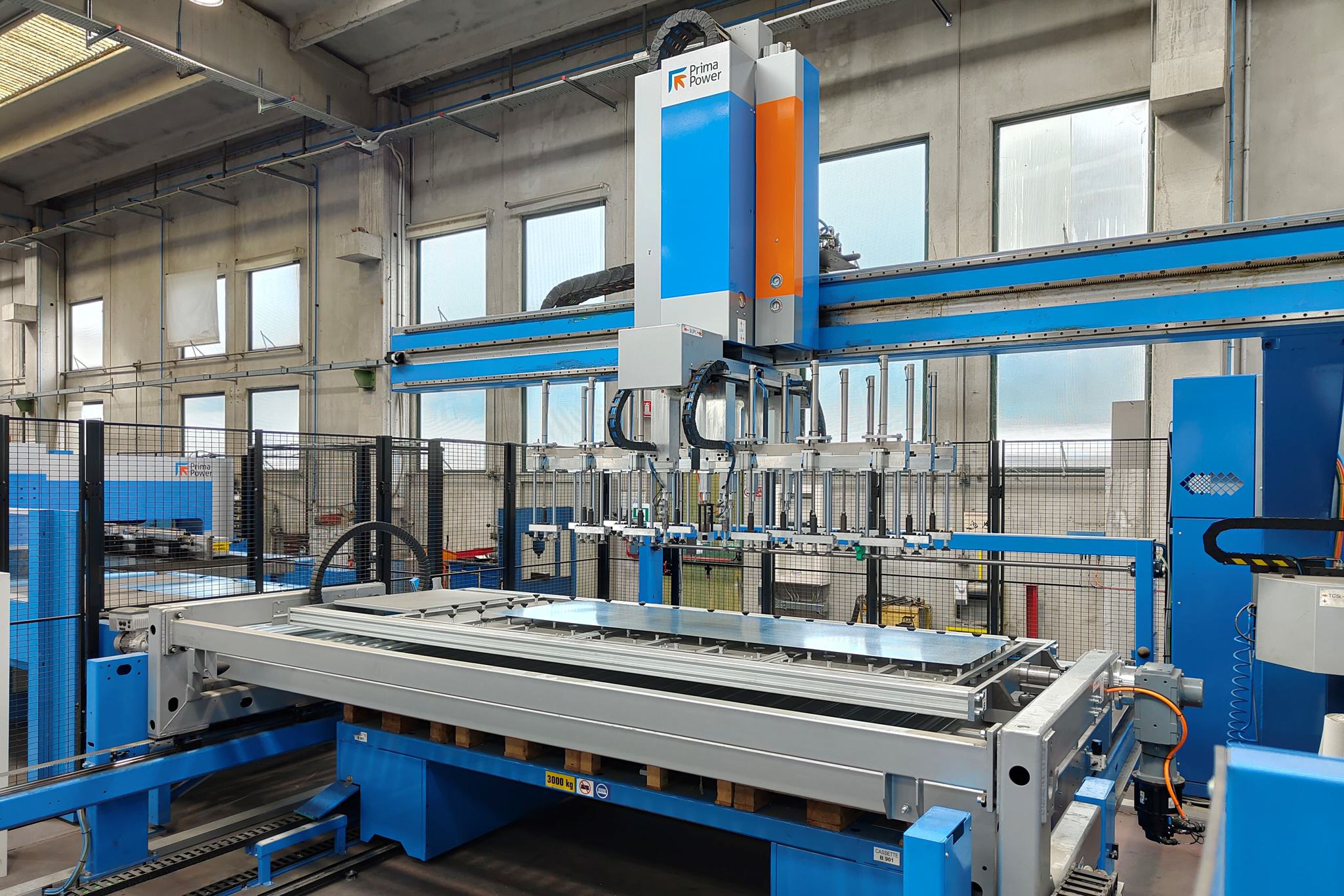
THE ADDED VALUE OF PARAMETRIC PROGRAMMING
The line configuration chosen by De Wave is perfectly calibrated to specific requirements. It is an excellent compromise that brings together flexibility, compactness and productivity, while the PCD system balances and equalises the time between the punching machine and panel bender.
"The software side of things," Malatesta emphasises, "has also proved to be key in internal operational growth. From this point of view, parametric programming was one of the requirements discussed and requested when evaluating choice of plant, since our panels essentially differ in size, starting from a basic geometry. Once the reference panel section is defined, the system quickly switches the kits into production using one of the already saved variables, adjusting just a few cutting and bending parameters, with the advantage of being able to maximise production speed and then leave the line ready for assembly, electrification, packaging and shipment to the site.
Shipment to site is treated with equal care and consideration in order to maintain all requirements, including those already mentioned related to aesthetics and safety.
"These safety requirements," adds Malatesta, "correspond to compliance with fire resistance and a specific structural load once the panel is finished. From this perspective, we must remember not only the continuous stresses the parts are subjected to, given that they are mounted on boats, but also the fact that they’re in contact with a marine environment, which could lead to corrosion phenomena and interfere with their durability."
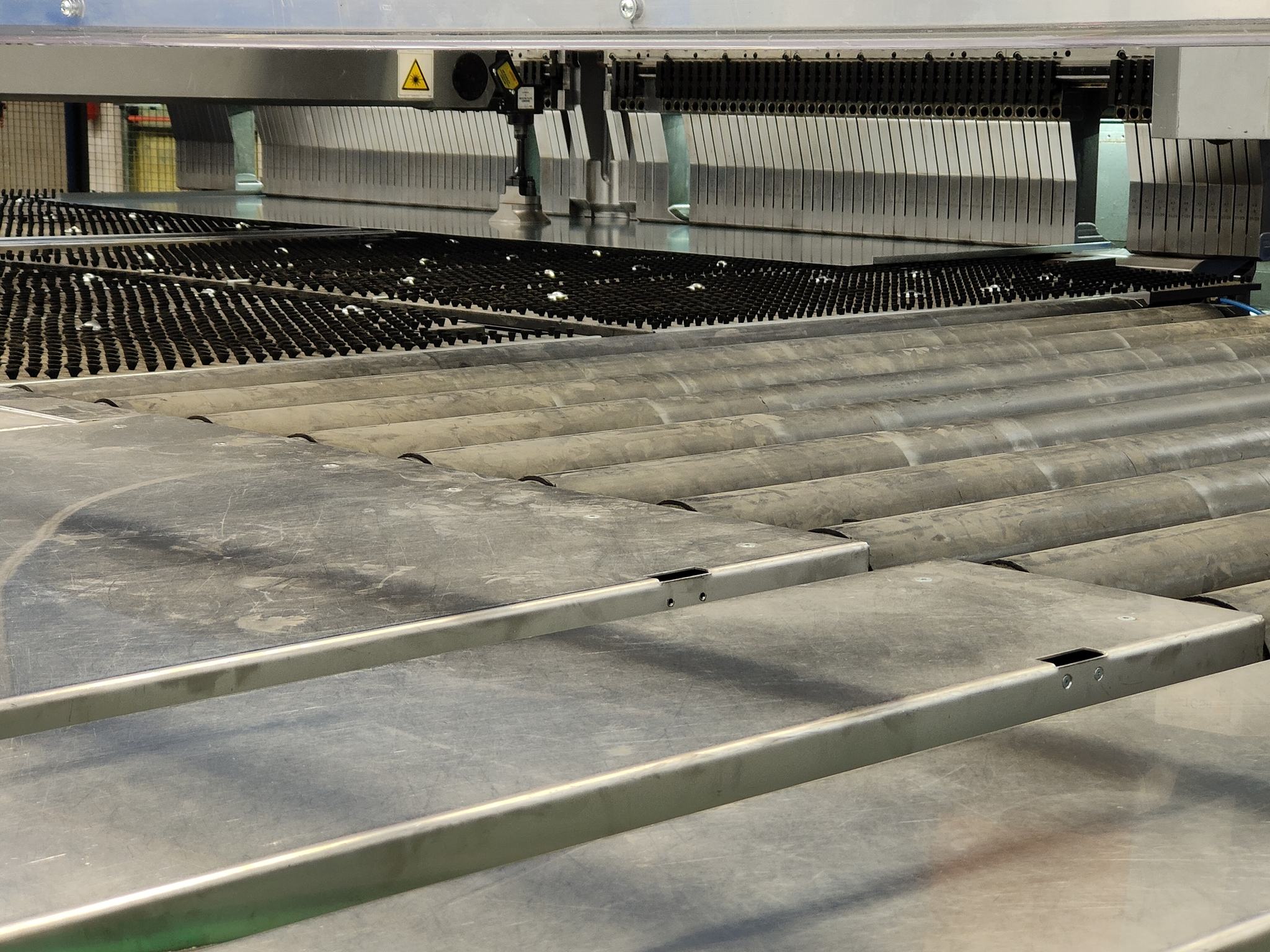
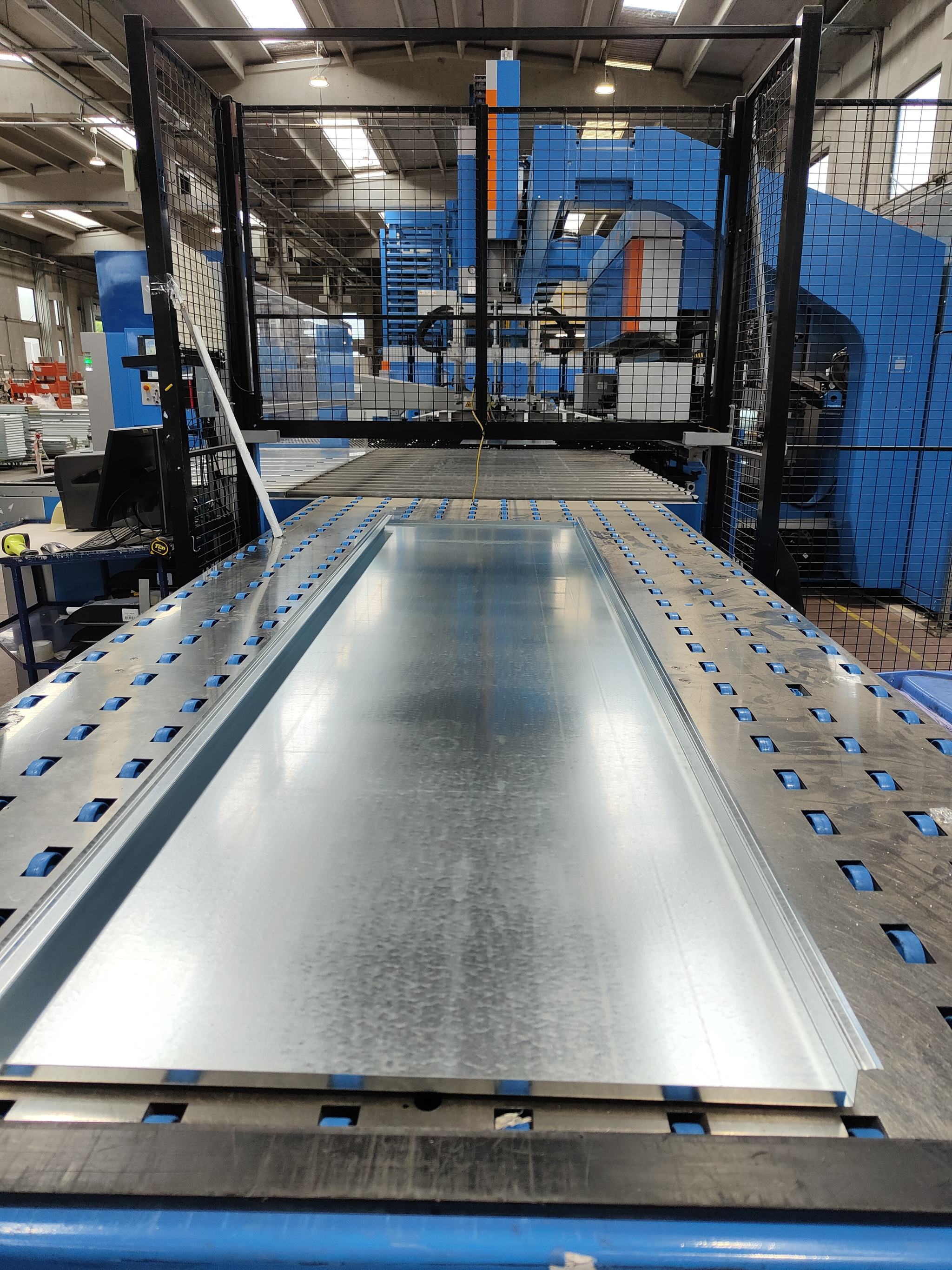
FROM PANEL TO TURNKEY
Integration of the new Prima Power line has allowed De Wave to redesign its operating assets, as already mentioned, by bringing a greater percentage of the production of panelled 'shells' in-house, but also by bringing back others which were also previously outsourced, such as the production of wet units carried out in the company's Polish factories.
"The Monfalcone plant," Malatesta continues, "where we currently process about 200,000 square metres of finished panels per year, has an average of about 80 employees spread across the various departments and working on several process lines."
These process lines include the new PSBB, as well as a semi-automatic, continuous-flow assembly line serviced by two robots (one for cutting the insulation and the other spraying the glue), flanked by two press brakes and a punching machine. There is also a profiling machine for making staves, and a shear.
"We have kept some manual panel assembly stations as a backup," continues Malatesta, "to cover for plant downtime, maintenance work or extreme work peaks."
In this regard, new investments in technology (also at the Monfalcone site) have already been planned with a view to continuous improvement and growth, thus further enhancing and optimising production flow, both with additions and replacements of machines that have now become obsolete.
"The company's vision," Malatesta concludes, "is to integrate the entire plant engineering side of shipbuilding with the visible production, specifically panels, ceilings and wet units. That’s why we’re moving into the market not only with investments in technology, but also with company acquisitions so that we can provide an ever more complete turnkey service."
In short, to present itself as an increasingly global manufacturer and contractor able to cover the entire range of interior fittings for cruise ships, large yachts and riverboats, both new and refitted.
Implementation of this new line has allowed us to insource a significant portion of our 'shell' production, allowing us to achieve increasingly strict delivery times, a reduction in non-conformities and an even better-quality product.
Are you looking for a similar solution for your company? Find it here
Shear Genius
PUNCHING AND SHEARING COMBINED MACHINES