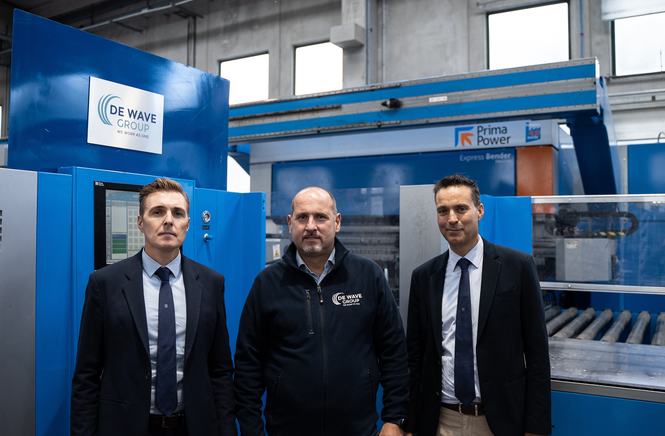
De Wave: Tehokkuus ja tuottavuus edellä
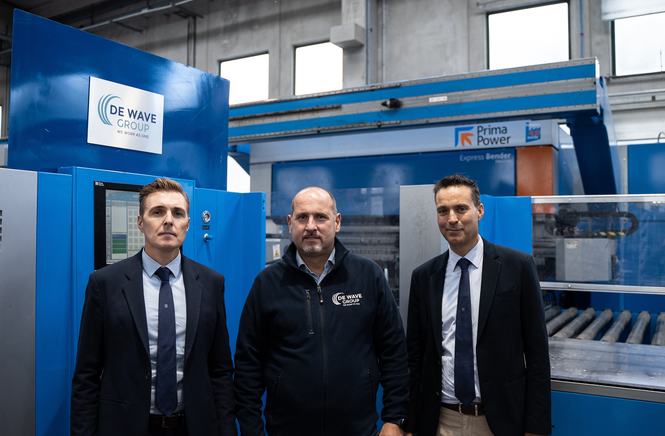
De Wave -konserni valmistaa Prima Powerin automaattisella valmistuslinjalla erilaisia kalusteita ja varusteita risteilyaluksiin, suuriin huviveneisiin ja jokiveneisiin, jotka kuljettavat ja majoittavat muutamasta kymmenestä muutamaan tuhanteen ihmistä.
Jos ”kaikki mitä tarvitset” elääksesi risteilyaluksella ikuisesti, on odottaa pari vuotta ja hankkia ylimääräinen miljoonaa dollaria (eräs risteily-yritys julkisti äskettäin ensimmäisenä maailmassa kaupan yksityiskäyttöön tarkoitetusta asuinaluksesta, jossa on yli 500 huoneistoa), niin onneksi tarvitset paljon vähemmän viettääksesi vain muutaman päivän rentoutuen risteilyaluksella ja vieraillessasi kaikilla mantereilla, tunnetuissa ja vähemmän tunnetuissa paikoissa. Itse asiassa on olemassa laaja valikoima aluksia, joihin mahtuu muutamasta kymmenestä muutamaan tuhanteen ihmistä (matkustajat ja miehistö), mukaan lukien suuret risteilyalukset, suuret jahdit sekä, ei yhtä hyvin varustetut, jokiveneet. Aivan kuten ne, joille De Wave valmistaa kalusteita ja varusteita, ja tekee yrityksestä referenssiurakoitsijan, jolla on laaja toimisto- ja tuotantolaitosverkosto, joka tukee purjehdus- ja huviveneilyteollisuutta maailmanlaajuisesti.
Viiden yrityksen fuusiosta syntyneenä, De Wave on tänä päivänä amerikkalaisen Platinum Equity -sijoitusrahaston kokonaan omistama tytäryhtiö. Sen pääkonttori sijaitsee Genovassa, Italiassa, mutta se on myös osa kansainvälistä konsernia, jolla on useita sivuliikkeitä Puolassa, Ranskassa, Saksassa, Suomessa, Singaporessa ja Miamissa Yhdysvalloissa. Italiassa se toimii myös Monfalconessa, jonka tehdas keskittyy pääasiassa hyttien paneelien ja kattojen valmistukseen.
”Erityyppisten paneelien ja verhoilujen päällystyselementtien on täytettävä äärimmäiset tarkkuus- ja laatustandardit. Näiden taustalla ovat esteettisiä ja turvallisuusvaatimuksia sisältävät korkeat teollisuusstandardit sekä tiukat toimitusajat”, sanoo De Wave -tehtaan päällikkö, Alberto Malatesta.
Nämä erityisominaisuudet saavutetaan nykyään Prima Powerin vuonna 2021 toimittaman ja asentaman vankan ja luotettavan teknologian ansiosta. Puhumme tietenkin PSBB-tuotantolinjan uudesta suorasta versiosta, joka voi käsitellä ohutlevyä varastosta, automatisoida materiaali- ja tiedonhallinnan ja yhdistää yksittäiset tuotantoprosessit täydelliseksi joustavaksi ja täysin integroiduksi prosessiksi.
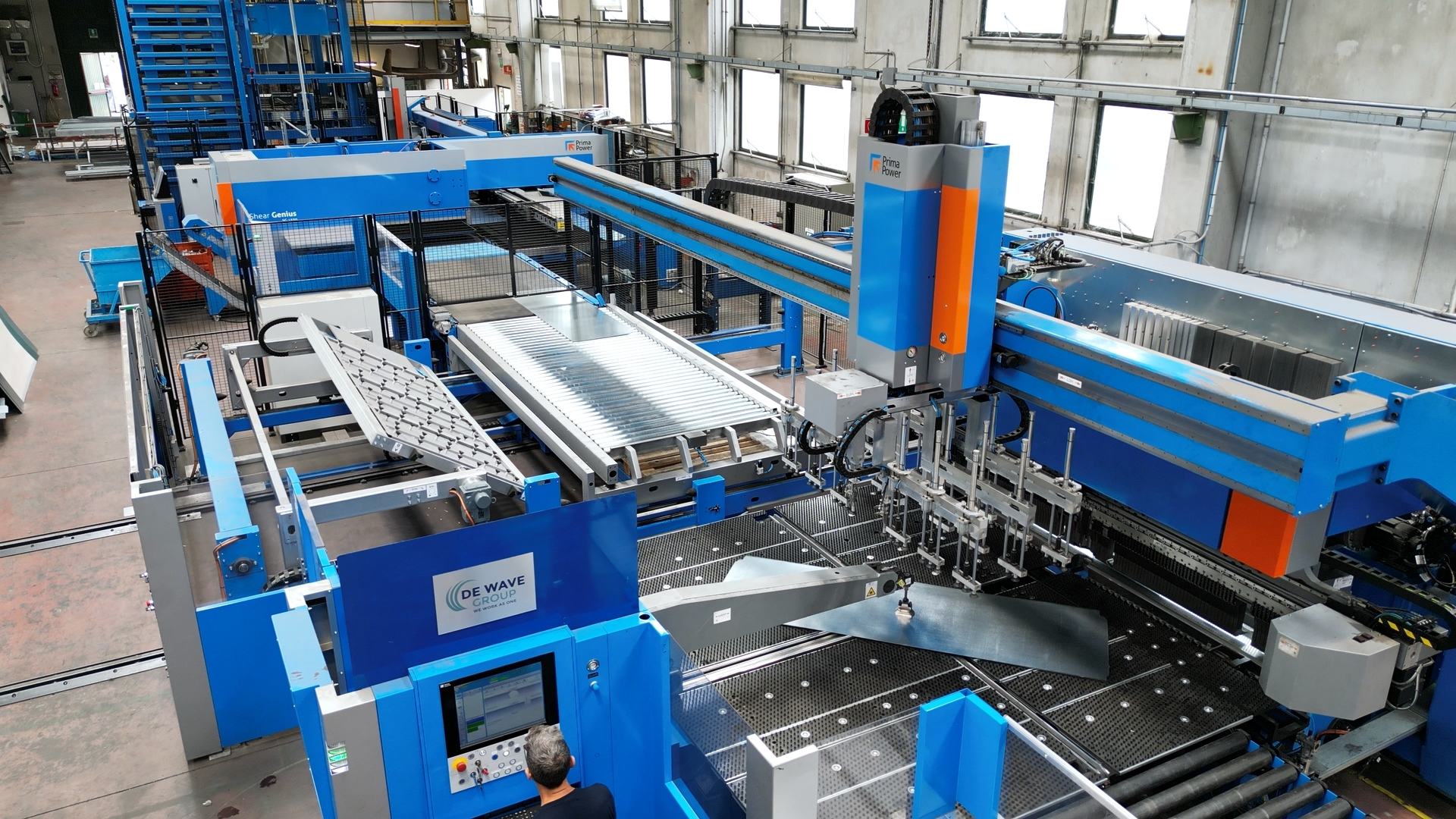
MANUAALISESTA LEIKKAUKSESTA TEHDASAUTOMAATIOON
Prima Powerin kompakti PSBB (lävistys, leikkaus, välivarastointi, taivutus) -tuotantojärjestelmä työstää aihiolevyt automaattisesti valmiiksi taivutetuiksi korkealaatuisiksi osiksi. Materiaalivirta voidaan järjestää joustavasti: kappaleet siirretään suoraan automaattiseen taivutukseen, taivutuksen ja lävistyksen/leikkauksen eri aikavaatimukset tasataan, materiaalia puretaan järjestelmästä ja uutta materiaalia lastataan järjestelmään. Joustavalla ja monipuolisella välivarastointitoiminnolla varmistetaan, että toiminta on mahdollisimman optimoitua valmistuskustannusten suhteen. Läpäisyaikaa puolestaan voi aina muuttaa kunkin valmistustehtävän vaatimusten mukaan. Joustava välivarastointi varmistaa integroitujen koneiden mahdollisimman optimaalisen toiminnan. Tämän konseptin tarjoama tuottavuus perustuukin monipuolisen sähköservokäyttöisen lävistysjärjestelmän ja integroitujen sähköservokäyttöisten leikkaus- ja taivutusjärjestelmien yhdistelmään. Kaikkea tätä koordinoi edistyksellinen ohjelmisto, joka varmistaa optimaalisen materiaalivirran ja prosessivaiheet.
“De Wave on päättänyt investoida Prima Powerin teknologioihin lisätäkseen teknologia- ja tuotantovirtaansa, ja parantaakseen tehokkuutta, mikä varmistaa suuremman tuottavuuden. Päätöksen taustalla oli myös erityinen halu tuoda omaan valmistukseen 100 % matkustamopaneelien ”kuorituotannosta”, joka tähän asti oli suurelta osin ulkoistettu,” toteaa Malatesta.
Lisäksi lisäämällä automaatiota ja kokoonpanoteknologiaa uusi Prima Powerin koneista koostuva tehdas on mahdollistanut siirtymisen erätuotannosta paljon virtaviivaisempaan ja tehokkaampaan ”kappaletuotantoon”, mikä on myös parantanut laatua ja kilpailukykyä.
”Uusi linja on mahdollistanut prosessin ja tuotteen toistettavuuden, joka on liiketoimintamme kannalta olennainen ja ratkaiseva tekijä, koska esteettisyys riippuu suuresti paneelien välisestä liitoksesta, jossa ei saa olla virheitä. Lisääntynyt tuottavuus on saavutettu poistamalla mekaanisesti kiinnitetyn liitosprofiilin asennus, kiitos saavutettujen täydellisten taivutusten, jotka mahdollistavat tarkat liitokset erittäin pienillä toleransseilla”, lisää Malatesta.
Uusi järjestelmä on siksi mahdollistanut De Waven merkittävän operatiivisen parannuksen, kun se on voinut siirtyä puhtaasti manuaalisesta leikkausprosessista todelliseen tehdasautomaatioon.
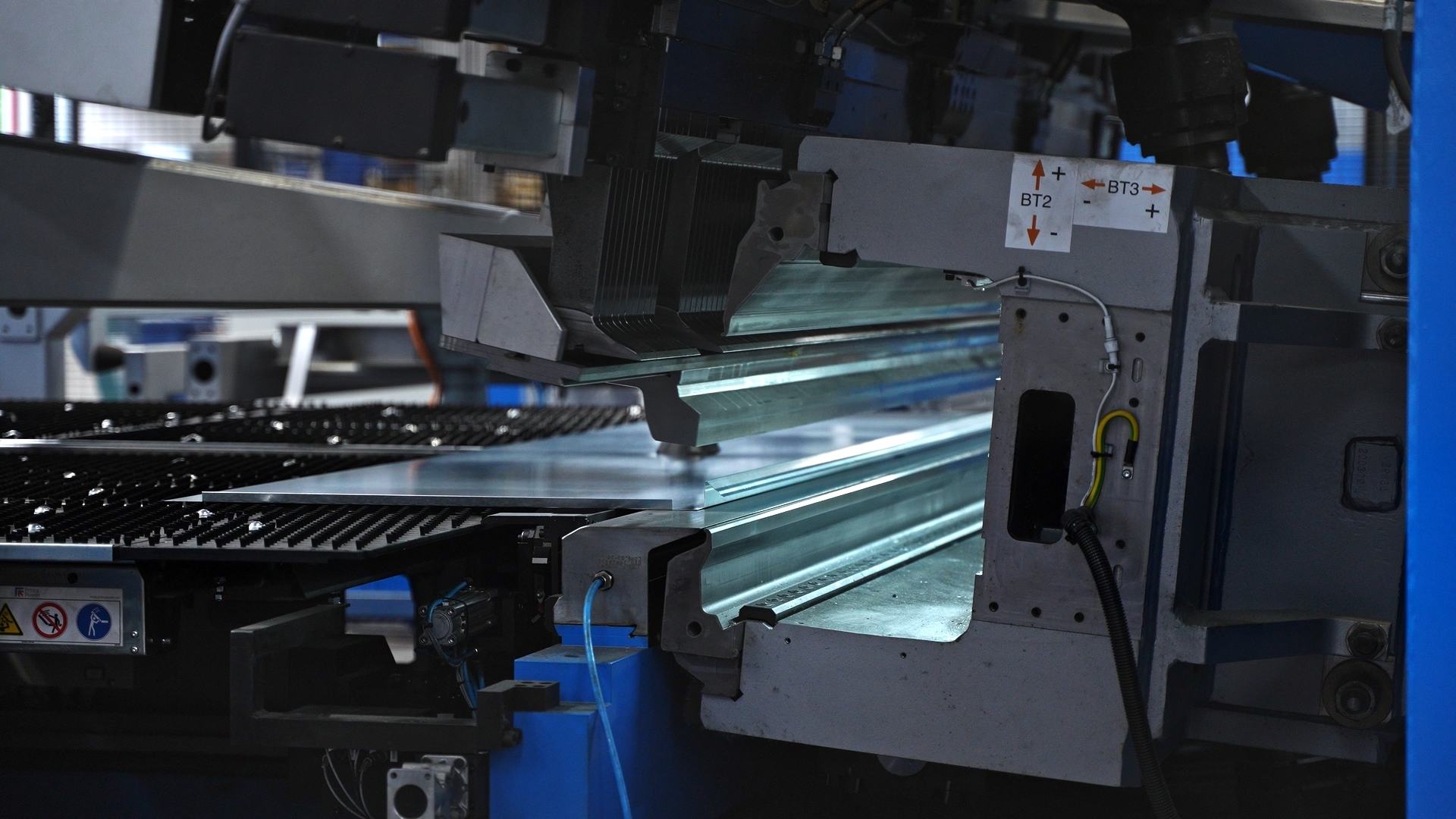
VARASTOSTA TAIVUTUKSEEN NOPEASTI JA TARKASTI
De Waven uuteen PSBB-järjestelmään valittu kokoonpano sisältää FL-ohutlevyvaraston, jota käytetään yhdessä Shear Genius SG 1530 -lävistys-leikkauskoneen ja EBe 2720 Express Bender -taivutusautomaatin kanssa.
”Nämä korkean profiilin teknologiat”, jatkaa Malatesta, ”ovat tarkoittaneet työntekijöidemme kouluttamista tehtaan perustamis- ja käynnistysvaiheessa. He huomasivat siirtyvänsä perinteisestä prosessin käsittelystä, 2000-luvun alkupuolelta peräisin olevilla leikkaus-, lävistys- ja taivutuskoneilla, täysin automatisoituun linjaan. Tämä kasvupolku on kuitenkin johtanut työntekijöidemme osaamisen jatkuvaan kehittymiseen ja tähän mennessä on saavutettu erittäin tyydyttäviä tuloksia.”
Automatisoitu tuotantolinja koostuu kolmesta päätoiminta-alueesta. Ensimmäisenä on 10-paikkainen FL-varasto, josta valmis ohutlevy lastataan käsittelyä varten. Toisena on ensimmäinen käyttöasema, Shear Genius SG 1530 –yhdistelmäkone, ja jossa tapahtuu nestauksen optimointi. Kolmantena on Express Bender EBe 2720, jonne leikatut ja lävistetyt kappaleet syötetään lopullisen ”kuoren” luomiseksi. Linjan lopussa on kaksi erilaista materiaalipistettä: yksi valmiille ”kuorille”, jotka sitten asetetaan erityisiin telineisiin; ja toinen, johon syötetään paneloidut ”kuoret”, jotka vaativat lisätaivutuksen. Tämä tehdään Prima Powerin särmäyspuristimella linjan etupäässä, ennen kuin kuoret asetetaan takaisin muille telineille tuotantovirran jatkamiseksi.
”Tämän uuden linjan käyttöönotto”, Malatesta toistaa, ”on antanut meille mahdollisuuden tehdä merkittävä osa ”kuorituotannosta” talon sisällä, mikä antaa meille mahdollisuuden saavuttaa yhä tiukemmat toimitusajat, vähentää poikkeamia ja saada aikaan entistä parempi laatu ja laadukkaampi tuote. Pystymme nyt valmistamaan ohutlevykuoria noin 40-80 sekunnissa jatkuvassa virtauksessa, niiden monimutkaisuudesta ja paneelintaivutuksista riippuen. Valmistamme tällä hetkellä yhteensä noin 15 000 paneelia/kk, mutta kunnianhimoinen tavoitteemme on yli 18 000 kuukaudessa. Nämä paneelit on myös suunniteltu ja työstetty varmistamaan nopea ja virheetön kokoonpano paikan päällä, yleensä 0,5—0,8 mm:n paksuuksilla.”
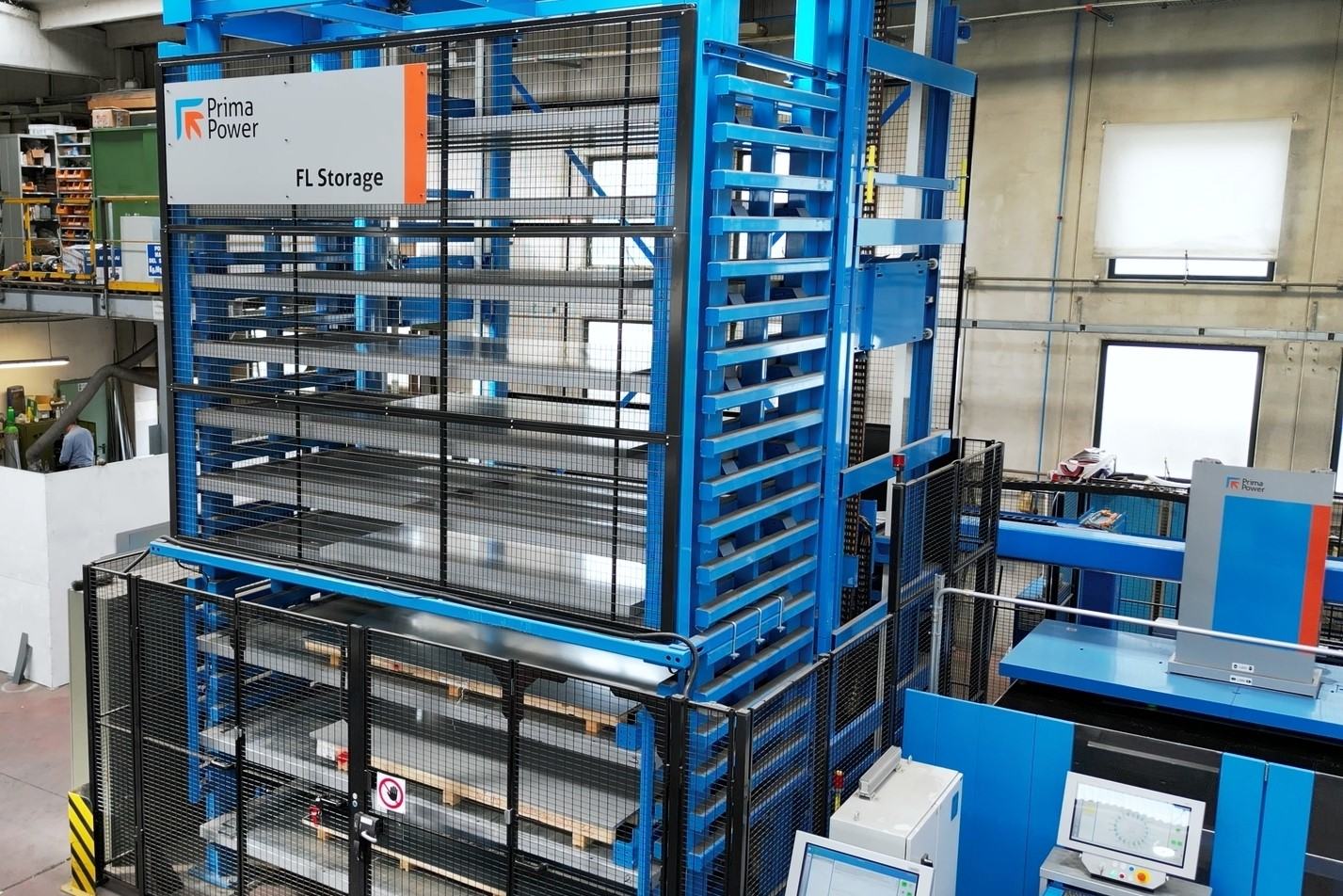

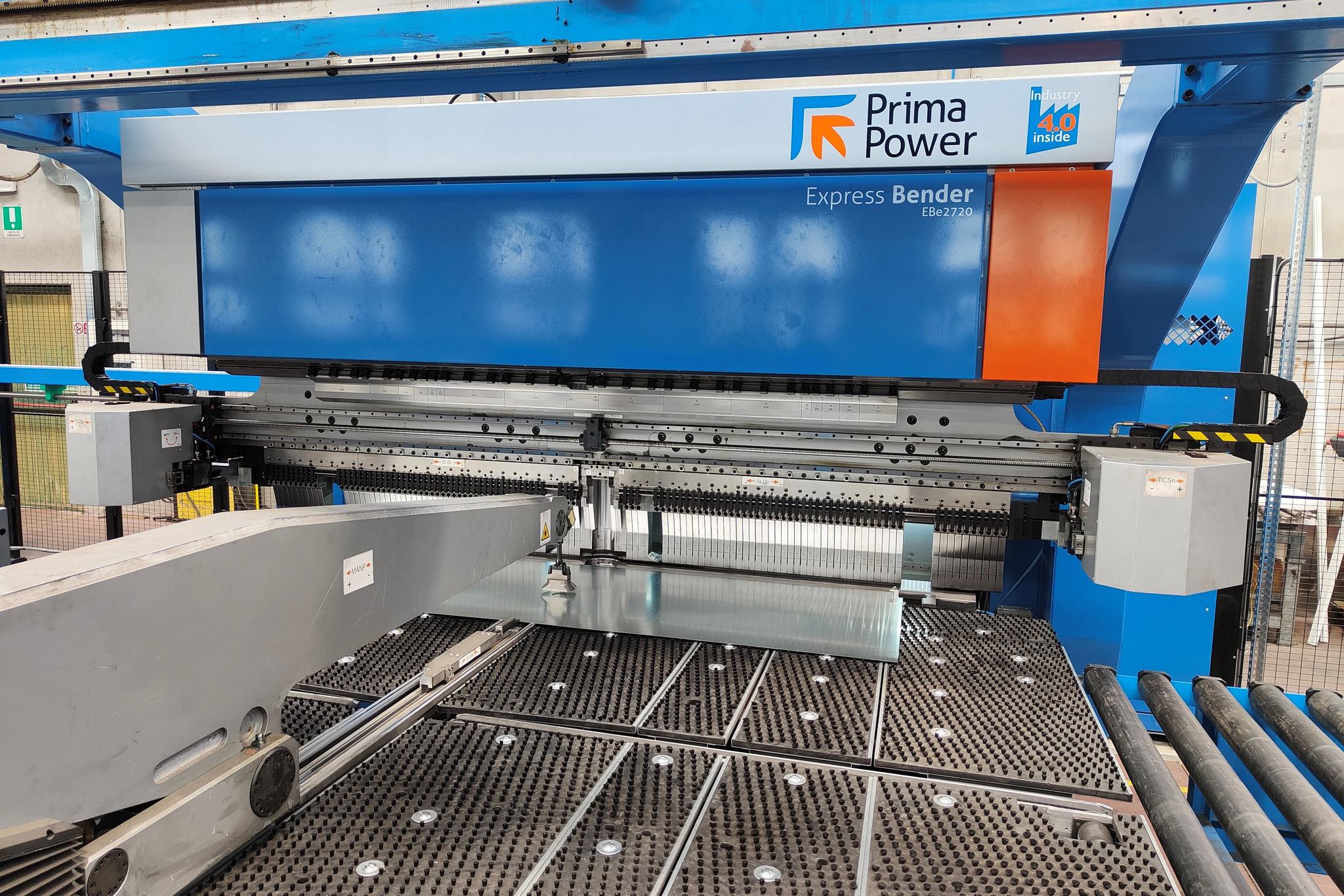
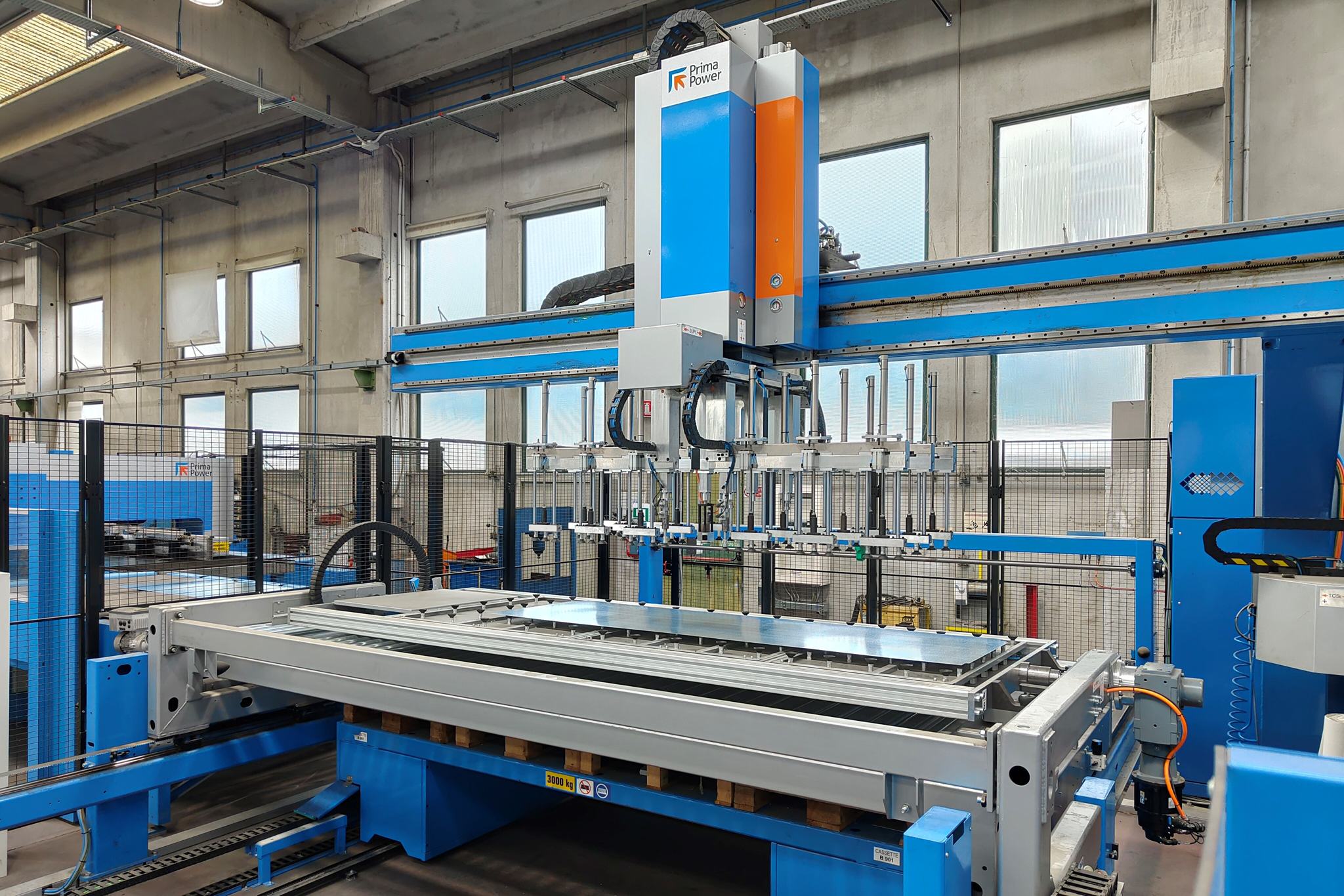
PARAMETRISEN OHJELMOINNIN LISÄARVO
De Waven valitsema linjakokoonpano on täydellisesti kalibroitu erityisvaatimuksiin. Se on erinomainen kompromissi, jossa yhdistyvät joustavuus, kompakti koko ja tuottavuus, samalla kun PCD-järjestelmä tasapainottaa ja tasoittaa lävistyskoneen ja taivutusautomaatin välistä aikaa.
”Ohjelmistopuoli”, Malatesta painottaa, ”on myös osoittautunut avaintekijäksi sisäisen operatiivisen kasvun kannalta. Tästä näkökulmasta parametrinen ohjelmointi oli yksi niistä vaatimuksista, joista keskusteltiin ja pyydettiin tehdasvalintaa arvioitaessa, koska paneelimme eroavat olennaisesti kooltaan perusgeometriasta alkaen. Kun vertailupaneelin osio on määritelty, järjestelmä kytkee sarjat nopeasti tuotantoon käyttämällä yhtä jo tallennetuista muuttujista, säätämällä vain muutamia leikkaus- ja taivutusparametreja. Etuna on, että se pystyy maksimoimaan tuotantonopeuden ja jättämään sitten linjan valmiiksi kokoonpanoa, sähköistämistä, pakkaamista ja lähettämistä varten.
Lähetys asiakkaalle käsitellään yhtä huolellisesti ja harkiten kaikkia vaatimuksia noudattaen, mukaan lukien jo mainitut estetiikkaan ja turvallisuuteen liittyvät vaatimukset.
”Nämä turvallisuusvaatimukset”, lisää Malatesta, ”vastaavat palonkestävyyden ja tietyn rakenteellisen kuormituksen noudattamista, kun paneeli on valmis. Tästä näkökulmasta meidän on muistettava paitsi jatkuvat rasitukset, jotka kohdistuvat kappaleisiin, koska ne on asennettu veneisiin, myös se, että ne ovat kosketuksissa meriympäristöön, mikä voi johtaa korroosioilmiöihin ja vaikuttaa niiden kestävyyteen.”
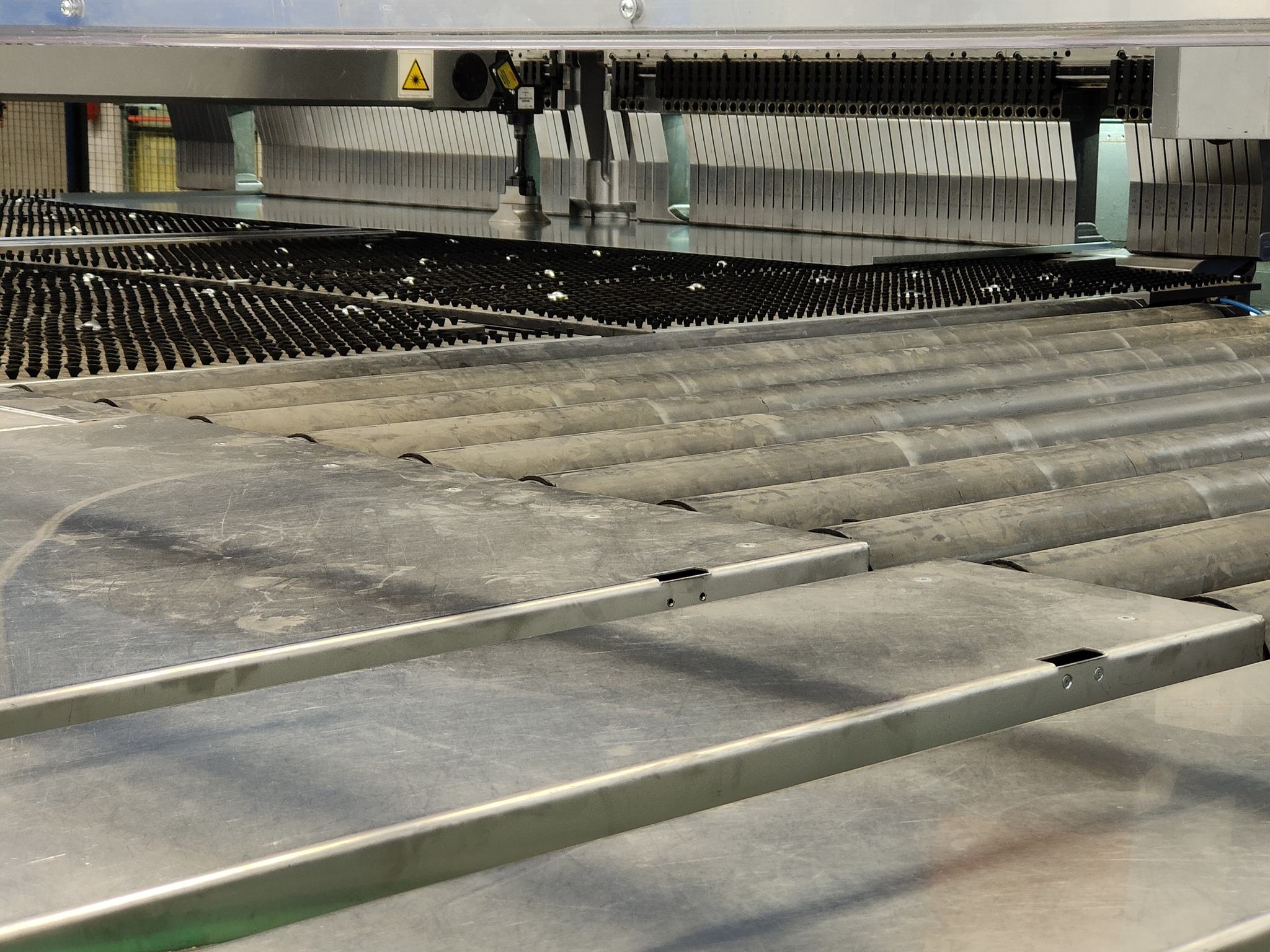
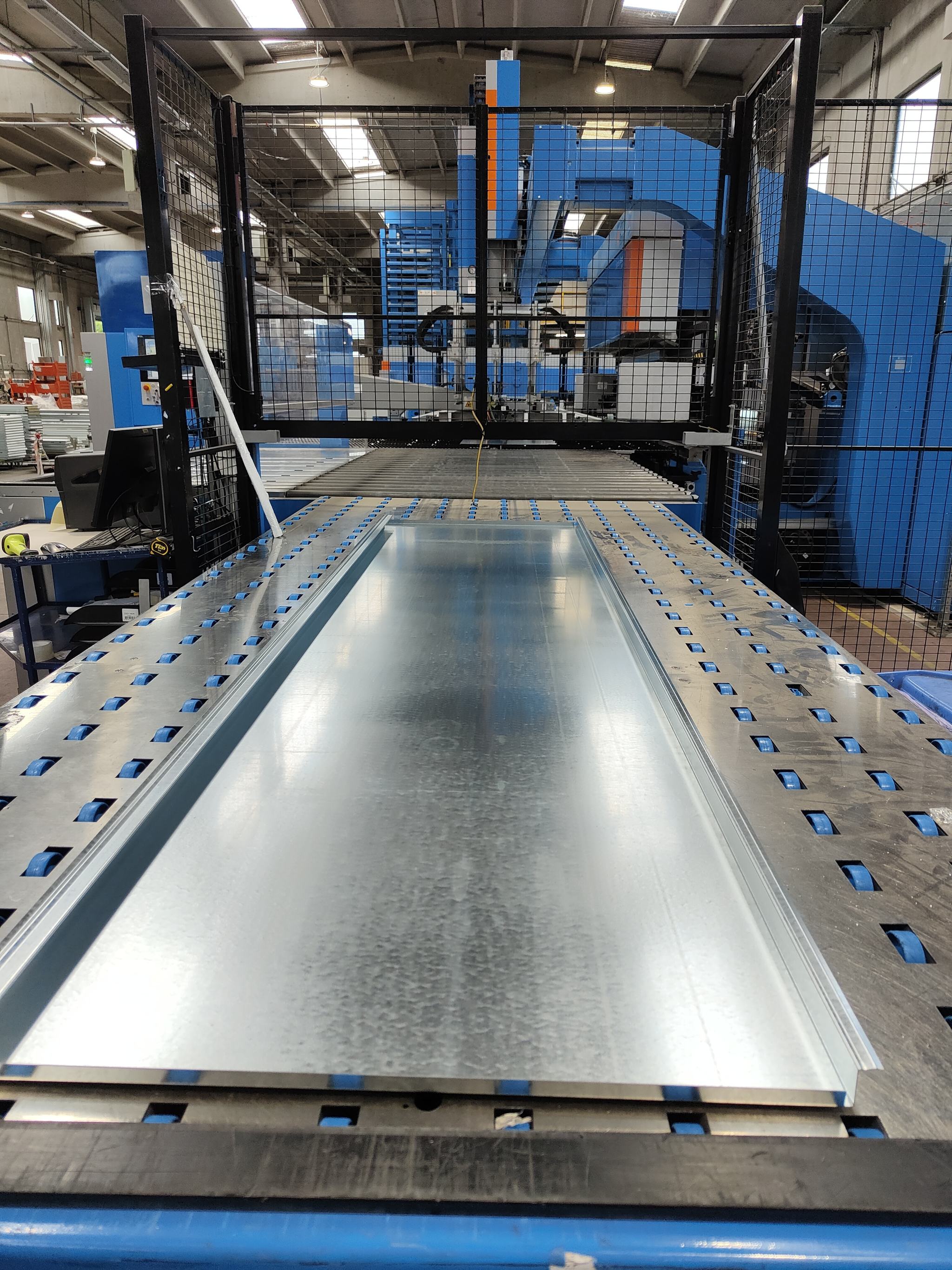
PANEELISTA AVAIMET KÄTEEN -PALVELUUN
Uuden Prima Power -linjan integrointi on antanut De Wavelle mahdollisuuden suunnitella tuotantokapasiteettinsa uudelleen, kuten jo mainittiin, tuomalla suuremman prosenttiosuuden paneloitujen ”kuorien” tuotannosta talon sisälle, mutta myös tuomalla takaisin muita, aiemmin ulkoistettuja toimintoja, kuten yrityksen Puolan tehtailla toteutetun märkäyksiköiden tuotannon.
”Monfalconen tehtaalla, jossa käsittelemme tällä hetkellä noin 200 000 neliömetriä valmiita paneeleja vuodessa”, Malatesta jatkaa, ”on keskimäärin noin 80 työntekijää eri osastoilla ja he ovat töissä useilla prosessilinjoilla.”
Nämä prosessilinjat sisältävät uuden PSBB:n sekä puoliautomaattisen, jatkuvavirtaisen kokoonpanolinjan, jota hoitaa kaksi robottia (toinen eristeen leikkaamista ja toinen liiman ruiskuttamista), ja jota reunustavat kaksi särmäyspuristinta ja lävistyskone. Mukana on myös profilointikone tappien tekemiseen sekä leikkuri.
”Olemme säilyttäneet joitakin manuaalisia paneelikokoonpanoasemia varmuuden vuoksi”, jatkaa Malatesta, ”kattamaan tehtaan seisokit, huoltotyöt tai äärimmäiset työhuiput.”
Tältä osin on jo suunniteltu uusia teknologiainvestointeja (myös Monfalconen tehtaalle) jatkuvan kehittämisen ja kasvun varmistamiseksi, mikä tehostaa ja optimoi tuotantovirtaa entisestään sekä uusien koneiden lisäyksillä että vanhentuneiden koneiden vaihdoilla.
”Yrityksen visio”, Malatesta toteaa, ”on integroida koko laivanrakennuksen tehdassuunnitelupuoli näkyvään tuotantoon, erityisesti paneeleihin, kattoihin ja märkäyksiköihin. Siksi valtaamme markkina-alaa paitsi teknologiainvestoinneilla, myös yritysostoilla, jotta voimme tarjota yhä täydellisemmän avaimet käteen -palvelun.”
Lyhyesti sanottuna, haluamme olla yhä globaalimpi valmistaja ja alihankkija, joka pystyy kattamaan risteilyalusten, suurten huviveneiden ja jokiveneiden koko sisustusvarustelun, sekä uusina että kunnostettuina.
Tämän uuden linjan käyttöönotto on antanut meille mahdollisuuden tehdä merkittävä osa ”kuorituotannosta” talon sisällä, mikä antaa meille mahdollisuuden saavuttaa yhä tiukemmat toimitusajat, vähentää poikkeamia ja saada aikaan entistä parempi laatu ja laadukkaampi tuote.
Etsitkö vastaavaa ratkaisua yrityksellesi? Löydä se täältä
Shear Genius
LÄVISTYKSEN JA KULMALEIKKAUKSEN YHDISTÄVÄT KONEET