
Clivet, centrarse en lo servoeléctrico para crecer

Clivet, uno de los principales fabricantes de bombas de calor y enfriadoras, ha elegido la tecnología servoeléctrica Prima Power para renovar su parque de máquinas dedicado al trabajo de chapa con soluciones 4.0 altamente automatizadas y totalmente integradas. En el corazón del departamento se encuentra la línea PSBB, que gestiona todo el proceso de mecanizado de piezas con estaciones de punzonado, cizallado, almacenamiento intermedio y plegado.
Entrar en la fábrica de Clivet en Feltre significa, además de tener la oportunidad de descubrir las tecnologías que permiten a la empresa fundada en 1989 por Bruno Bellò ser uno de los protagonistas del sector de la climatización, también sumergirse en los valores de innovación y sostenibilidad que caracterizan desde hace años la misión de esta empresa. Debido a una evidente distorsión profesional, nuestra historia solo se detendrá en el departamento de chapistería, pero los 50 000 m² de la fábrica Clivet hablan de su arraigada convicción de que un producto de excelencia para el confort sostenible y el bienestar individual debe fabricarse en un entorno sostenible, innovador y saludable.
Antes de continuar con nuestro reportaje desde la fábrica de Clivet, es importante señalar otro elemento que emerge con fuerza al recorrer esta planta: el crecimiento continuo de una marca que, en treinta años, ha alcanzado una facturación de más de 250 millones de euros y un reconocido liderazgo internacional, confirmado asimismo por la alianza industrial con el grupo industrial MIDEA y los más de 90 países a los que ha llegado gracias a la calidad de sus productos y estrategias de producción.
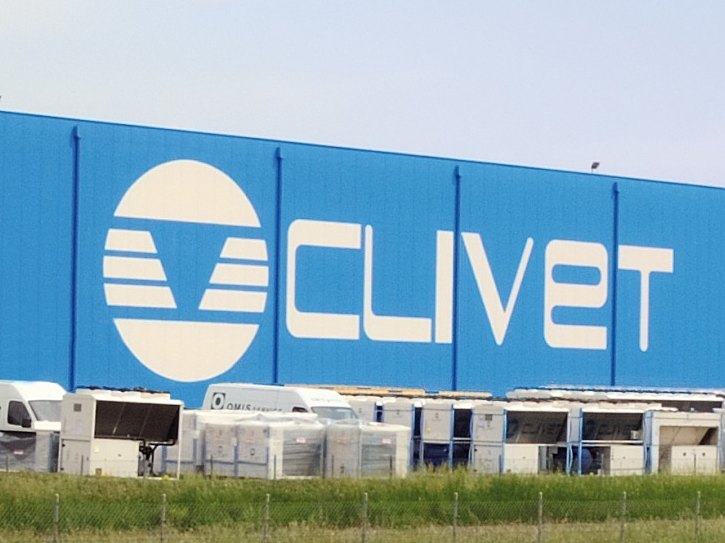
Un salto tecnológico
Para Clivet, este crecimiento también ha supuesto una ampliación progresiva de su gama de productos, flanqueando su producción de enfriadoras y bombas de calor con sistemas especializados basados en unidades Roof-Top, sistemas de bucle de agua y sistemas residenciales dedicados
«En este proceso de crecimiento también nos hemos dado cuenta de que las máquinas que teníamos para el procesado de chapa ya no podían satisfacer nuestras necesidades de producción», explica el ingeniero Luca Martini, director industrial de Clivet, mientras nos acompaña en nuestra visita a la fábrica. «Se trataba de máquinas con más de 25 años de servicio y, por tanto, muy anticuadas. En ese momento, la elección era sencilla: subcontratar todo el mecanizado o bien invertir y dotarse de máquinas nuevas de mayor rendimiento. Elegimos la segunda opción, entre otras cosas por las ventajas en términos de control de calidad de los productos, de plazos y gestión de prioridades que se derivan de mantener internamente procesos tan importantes para nuestros productos. El siguiente paso fue determinar qué línea compuesta por punzonadora y paneladora se adaptaba mejor a nuestras necesidades. Para ello, comparamos varias marcas y tecnologías y, tras una serie de pruebas, vimos que la solución de Prima Power era capaz de procesar el 63% de nuestros códigos sin necesidad de trasladar la pieza a otras máquinas. Por lo tanto, decidimos iniciar la cooperación con Prima Power instalando en una primera fase únicamente la combinación de cizalla punzonadora Shear Genius de Prima Power (en aquel momento con la marca Finn Power Ed, nota del redactor).»
La introducción de la cizalla Genius fue el primer paso de Clivet dentro del universo Prima Power, consciente de que un salto tecnológico tan importante requeriría también un periodo de adaptación para los operarios y técnicos. «Empezamos con la combinación», prosigue Martini, «porque una máquina como esta requería una mentalidad y un enfoque completamente nuevos para nosotros, por lo que necesitábamos algún tiempo para adaptarnos, cambiar de mentalidad y aprender a utilizar mejor una tecnología tan innovadora para nuestra realidad.En menos de un año, estábamos plenamente operativos e integramos la Shear Genius en nuestro flujo de trabajo.»
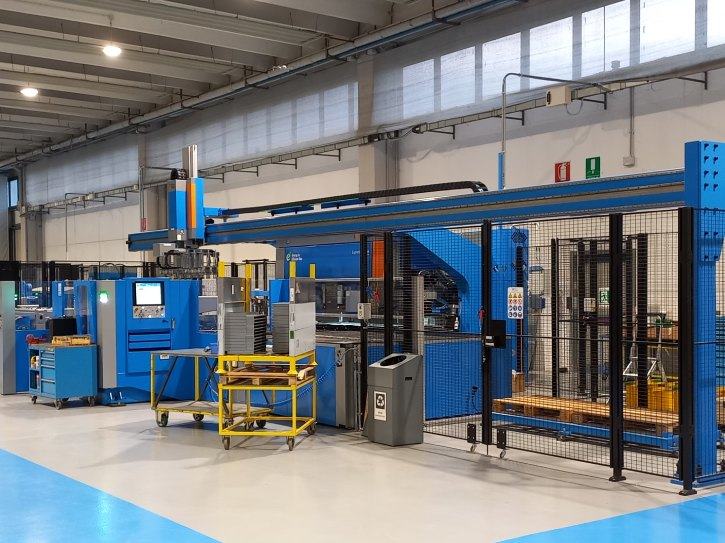
La integración en el flujo de producción es otro componente clave de la calidad y la eficiencia de Clivet, ya que la planta de Feltre es, a todos los efectos, Industria 4.0 en su máxima expresión.
«Para mí, integrarse en el flujo de producción significa partir de la orden de trabajo y llegar a la pieza acabada sin más intervención que la lectura óptica: aquí, cada pieza se etiqueta desde la chapa con programas e información para cada proceso posterior (corte, plegado, pintura, destino final en el proceso de producción) que siempre figuran en esta etiqueta para garantizar la trazabilidad, la automatización y la interconexión entre el sistema de gestión, las máquinas y las líneas de montaje.»
De este modo, Clivet ha conseguido garantizar la autonomía de producción de la máquina, permitiéndole trabajar en torno a tres turnos diarios.
«Hasta hace unos años, la mayor parte de nuestra producción era por encargo, las máquinas industriales muy personalizadas, y en pequeñas series, lo que llamamos comercial aplicada y ligera, es decir, máquinas con potencias grandes e intermedias. Ahora que estamos entrando con fuerza en el sector de las bombas de calor, también tenemos una producción de gran volumen: una ‘producción en masa’, teniendo en cuenta que, con la nueva fábrica, pretendemos llegar a las 100 000 bombas de calor producidas.» Estos nuevos requisitos de producción supusieron nuevas inversiones y la modernización de las tecnologías. «Con estos volúmenes, una paneladora era una opción muy atractiva, entre otras cosas porque nos permitiría depender menos de nuestros proveedores externos, al tiempo que disponíamos de un control total sobre la calidad del producto. Recurrimos a Prima Power para continuar este camino y la Shear Genius se transformó en una línea PSBB (del inglés Punching, Shearing, Buffering, Bending, punzonado, cizallado, almacenamiento intermedio, plegado), con la adición de una paneladora EBe 2720. La paneladora no solo funciona en línea, sino que también se puede cargar desde el exterior con un vagón adicional para las piezas que solo hay que plegar.»
La línea PSBB de Prima Power es, de hecho, una solución altamente flexible capaz de transformar automáticamente chapa en bruto en componentes plegados de alta calidad. PSBB es, como ya se ha mencionado, un acrónimo de Punching + Shearing + Buffering + Bending, es decir, punzonado, cizallado, almacenamiento intermedio y plegado con todos los procesos realizados mediante tecnología servoeléctrica.
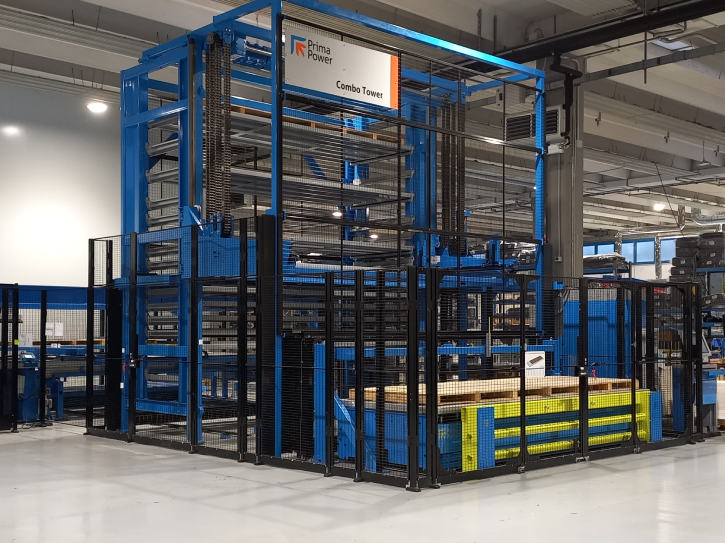
Cuando con una línea ya basta…
«La introducción de la línea PSBB de Prima Power respondió a nuestras necesidades y decidimos dar un paso más para cubrir una laguna que teníamos: me refiero al procesado de chapas de mayor espesor y, sobre todo, de chapas de 4 metros de longitud. Por tanto, optamos por equiparnos con una punzonadora láser combinada porque necesitábamos ser productivos y flexibles a la vez, gracias a que estas máquinas pueden realizar el mecanizado y el conformado por láser. Instalamos una combinación de punzón/láser Prima Power Combi Laser 1540 con un cargador automático Combo Tower para satisfacer estos requisitos.
Clivet utiliza mucha chapa metálica en sus productos, tanto para los componentes estructurales como para los considerados estéticos.
«Precisamente porque manejamos tantos códigos, la Combi es la máquina que mejor se adapta a nuestras necesidades», prosigue Martini, «por ejemplo, con el láser podemos producir cantos redondeados, tal y como solicitan nuestros clientes, mientras que el conformado nos permite ahorrar espesor sin dejar de garantizar ese refuerzo de la chapa que evita las molestas vibraciones.»
Con estas inversiones, Clivet aspira a ser completamente independiente en materia de transformación de chapas metálicas.
«Crecemos más de un 30% cada año y, por tanto, seguimos necesitando proveedores externos para satisfacer nuestras necesidades. Al mismo tiempo, estamos completando la transición de los antiguos códigos a los nuevos programas que se aplicarán en la nueva línea; estamos hablando de entre 20 000 y 30 000 códigos y, en consecuencia, es un trabajo que lleva tiempo completar. Sin embargo, nuestro objetivo no es dejar de tener proveedores externos, sino poder complementar nuestra capacidad de producción con apoyo externo para hacer frente a picos de trabajo o emergencias.»

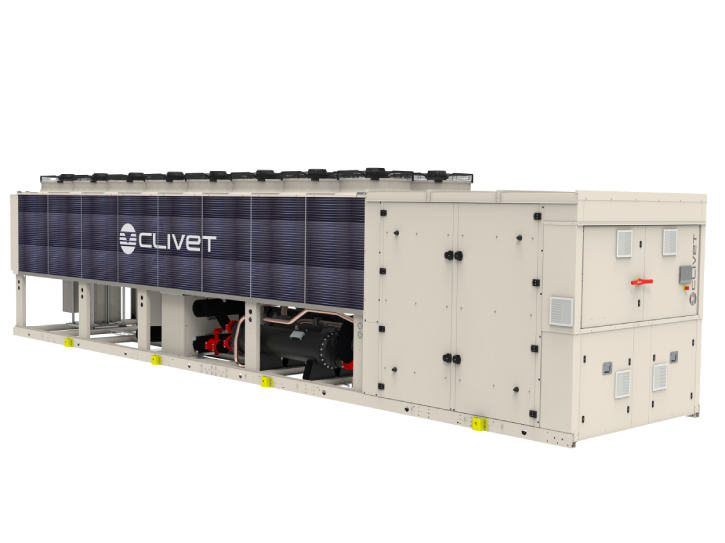
Un futuro cada vez más automatizado
La inversión en la línea PSBB y la Combi Laser también ilustra la importancia de la automatización para Clivet, que gestionará estos volúmenes de producción crecientes con soluciones altamente automatizadas y robotizadas en su nuevo centro de producción de 30 000 m². En la Combi Genius, por ejemplo, el LSR (acrónimo de «Robot de carga y apilado») se utiliza para cargar y descargar las piezas con el fin de evitar la intervención manual y aumentar la fiabilidad del proceso de recogida de piezas cortadas por láser. El robot de carga, descarga y apilado LSR es un robot de manipulación de materiales y piezas para punzonadoras láser combinadas. LSR carga las planchas en la máquina y apila las piezas acabadas en los palés de apilado, garantizando un proceso de manipulación de materiales preciso y eficaz. Cabe señalar que la pinza robótica dispone de varias zonas de succión, cada una de las cuales puede controlarse por separado. El sistema de movimiento de apilado servoaccionado garantiza la máxima precisión. Para aumentar la fiabilidad del proceso de recogida de piezas cortadas por láser, Prima Power también ha desarrollado la tecnología RALC (Robot Assisted Last Cut).
Durante la última sección de corte, la máquina y el robot realizarán movimientos simultáneos y sincronizados de los ejes, lo que garantiza una extracción segura y fiable de las piezas. La puesta a disposición de un almacén automatizado específico también era casi obligatoria para Clivet, que desde hace algunos años aspira a que sus plantas sean autónomas gracias a almacenes automatizados que garanticen un suministro constante las 24 horas del día. De hecho, Combo Tower es una solución de almacenamiento flexible diseñada para automatizar el flujo de materiales, ya que permite disponer de los distintos materiales en cuanto se necesitan de forma automática y sin demora, actuando como almacén intermedio o pulmón para los componentes acabados.
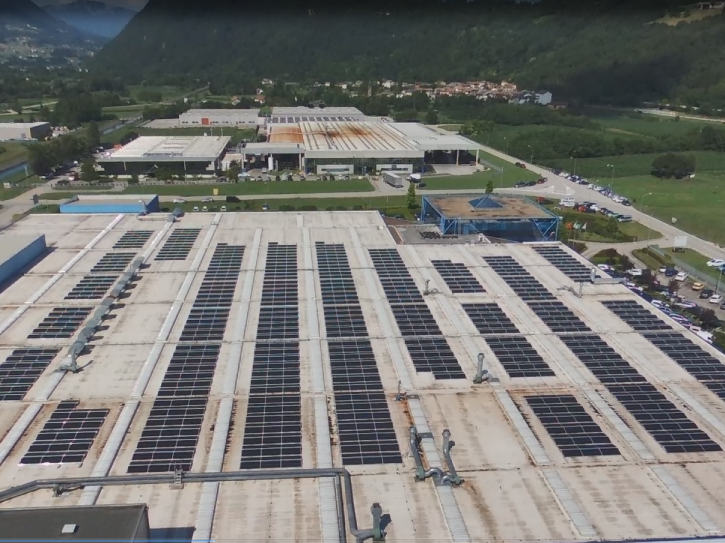
Elija sostenibilidad, elija servoeléctrico
Clivet ha optado por centrarse en la tecnología servoeléctrica que caracteriza a las máquinas Prima Power como parte integrante de su estrategia de producción bajo el lema de la sostenibilidad medioambiental.
«Las máquinas servoeléctricas son perfectas para nuestra visión de la producción porque consumen potencia y energía solo cuando es necesario y solo en la cantidad necesaria, sin derroches. Por eso estamos convencidos de que es la máquina que más energía ahorra y eso es muy importante para nosotros. Clivet se ha fijado un objetivo ecológico: alcanzar la neutralidad de carbono en los próximos tres o cuatro años, y la tecnología Prima Power es un aliado clave para superar este reto.
Precisamente por este motivo, Clivet ha completado su parque de máquinas con tres plegadoras servoeléctricas Prima Power: dos eP 1030 de 3 m y una eP 2040 de 4 m. Cabe destacar que toda la planta de Feltre ya se ha renovado profundamente en este sentido con la instalación de luces LED, sistemas de aire acondicionado con bombas de calor y un sistema fotovoltaico que ahora vale 1,2 MW, pero que se duplicará en marzo de 2023.
Clivet has set itself a green goal: to achieve carbon neutrality in the next three to four years and Prima Power technology is a fundamental ally in overcoming this challenge.