
Clivet, la technologie servo-électrique au service de la croissance

Comptant parmi les plus grands fabricants de pompes à chaleur et de refroidisseurs, Clivet a choisi la technologie servo-électrique de Prima Power pour moderniser son usine de traitement de tôle avec des solutions hautement automatisées et totalement intégrées à l'industrie 4.0. La ligne PSBB représente le cœur du département, gérant l'ensemble du processus de production avec des stations de poinçonnage, cisaillage, mise en tampon et pliage.
Fondée en 1989 par Bruno Bellò, Clivet est l'un des principaux acteurs du secteur de la climatisation. Entrer dans l'usine de Feltre, c'est non seulement découvrir les technologies qui ont fait de l'entreprise ce qu'elle est aujourd'hui, mais aussi expérimenter les valeurs d'innovation et de durabilité qui, depuis des années, définissent la mission de l'entreprise. Puisque nous sommes clairement formés par notre profession, notre histoire se concentre sur le département de transformation de la tôle. Cependant, les 50 000 m2 de l'usine Clivet témoignent de la conviction profonde de l'entreprise qu'un produit d'excellence offrant un confort et un bien-être durables à l'individu doit être créé dans un environnement durable, innovant et favorisant le bien-être. Avant de poursuivre notre article sur l'usine Clivet, il est important de souligner un autre élément qui ressort fortement lorsque l'on se promène dans cette usine : la croissance continue d'une marque qui, depuis plus de 30 ans, a réalisé un chiffre d'affaires de plus de 250 millions d'euros et a été reconnue comme un leader dans le secteur. Cela est également confirmé par son partenariat avec le groupe MIDEA et les plus de 90 pays qu'elle a conquis grâce à la qualité de ses produits et de ses stratégies.
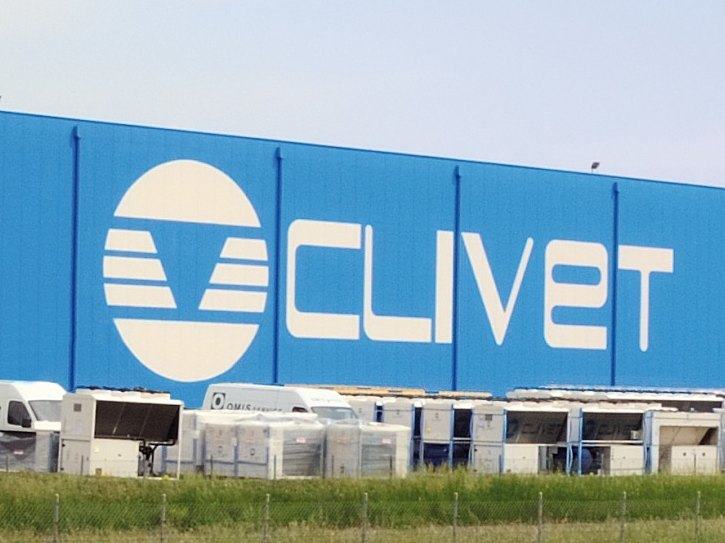
UN SAUT TECHNOLOGIQUE
Pour Clivet, cette croissance s'est également traduite par un élargissement progressif de sa gamme de produits, avec l'ajout de systèmes spécialisés basés sur des unités Roof-Top, des systèmes à eau circulaire et des systèmes conçus pour un usage résidentiel, en plus de ses refroidisseurs et pompes à chaleur.
"Au cours de ce processus de croissance, nous avons également réalisé que nos systèmes d'usinage des tôles n'étaient plus en mesure de répondre à nos besoins", explique Luca Martini, directeur industriel de Clivet, lors d'une visite de l'usine. "Les machines étaient en service depuis plus de 25 ans et étaient manifestement obsolètes. À ce stade, la décision était simple : nous devions soit externaliser l'usinage, soit investir dans de nouvelles machines plus performantes. Nous avons opté pour la seconde solution, notamment en raison des avantages liés au contrôle de la qualité des produits, au respect des délais et à la gestion des priorités qui découlent de la possibilité d'exécuter des processus aussi importants en interne. L'étape suivante consistait à déterminer quelle ligne composée d'une poinçonneuse et d'une panneauteuse était la mieux adaptée à nos besoins. Nous avons comparé différentes marques et technologies, et après une série d'essais, nous avons constaté que la solution Prima Power était capable de fabriquer 63% de nos produits sans déplacer la pièce sur d'autres machines. Nous avons donc choisi de commencer à travailler avec Prima Power, en installant dans un premier temps uniquement la machine combinée poinçonnage-cisaillage appelée Shear Genius de Prima Power".
La Shear Genius a été le premier pas de Clivet dans le monde de Prima Power, sachant qu'un saut technologique d'une telle ampleur nécessiterait une période d'adaptation à la fois pour les opérateurs et les techniciens. "Nous avons commencé par la solution combinée" poursuit Martini, "parce qu'une machine comme celle-là exige une approche et une mentalité complètement nouvelles ; nous avons eu besoin d'un certain temps pour nous adapter, changer notre mentalité et apprendre comment utiliser au mieux une technologie aussi innovante pour notre entreprise. En l'espace d'un an, nous avons atteint notre capacité de production optimale et la Shear Genius a été entièrement intégrée à notre flux de travail.
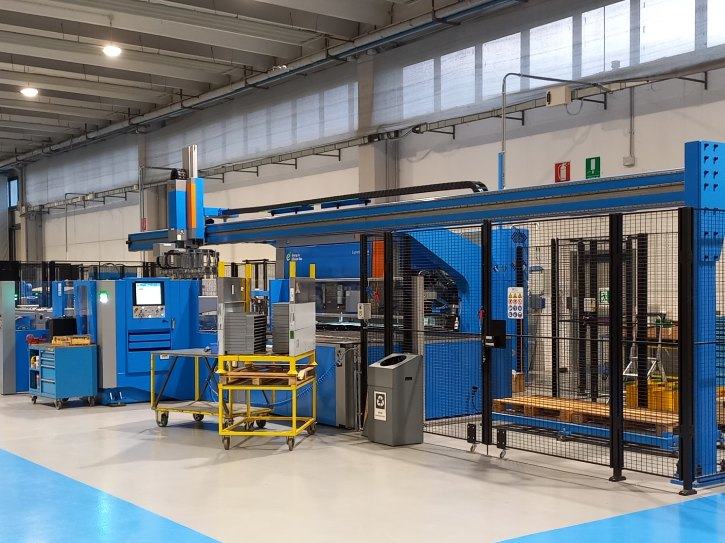
"Jusqu'à il y a quelques années, la plupart de nos produits étaient fabriqués sur commande. Nous fabriquions de petites quantités de machines industrielles hautement personnalisées, ce que nous appelons des machines commerciales appliquées et légères, c'est-à-dire des machines de grande et moyenne puissance. Aujourd'hui, après avoir fait une percée significative sur le marché des pompes à chaleur, nous envisageons également la production de masse, sachant qu'avec notre nouvelle usine, nous avons un objectif de production de 100 000 pompes à chaleur. Ces nouvelles exigences de production ont nécessité de nouveaux investissements et la modernisation de nos technologies. Une panneauteuse était une option très intéressante pour de tels volumes, également parce qu'elle nous aurait permis d'être moins dépendants de nos fournisseurs externes et d'avoir un contrôle total sur la qualité des produits. Nous nous sommes donc tournés vers Prima Power, et la Shear Genius a été transformée en ligne PSBB (Punching, Shearing, Buffering, Bending), avec l'ajout d'une panneauteuse EBe 2720. La panneauteuse ne travaille pas seulement en ligne, mais peut également être chargée à l'extérieur grâce à un wagon supplémentaire pour les pièces qui doivent seulement être pliées".
La ligne PSBB de Prima Power est en fait une solution très flexible capable de transformer automatiquement des tôles brutes en composants de haute qualité déjà pliés. Comme indiqué, PSBB est l'acronyme de Punching + Shearing + Buffering + Bending, tous les processus étant réalisés à l'aide d'une technologie servo-électrique.
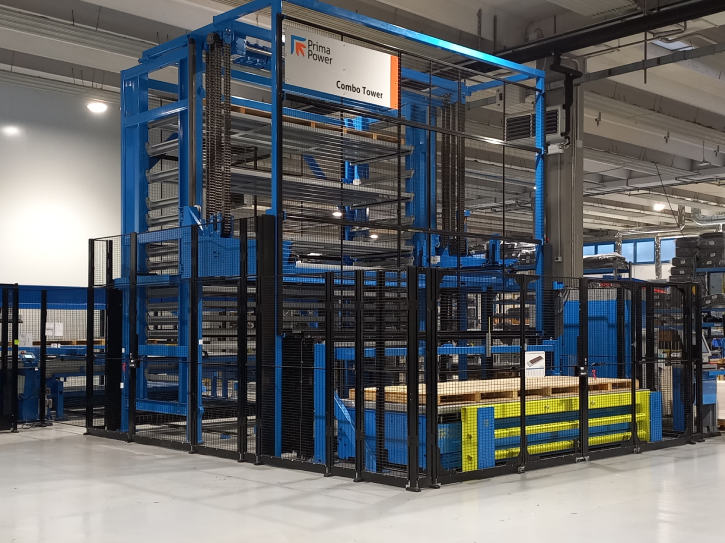
QUAND UNE SEULE LIGNE NE SUFFIT PAS
"L'introduction de la ligne PSBB de Prima Power répondait à nos besoins, nous avons donc décidé d'aller plus loin pour combler une carence : l'usinage de tôles plus épaisses et, surtout, de tôles de 4 mètres de long. Nous avons choisi un combiné poinçonnage-laser car nous avions besoin d'être à la fois productifs et flexibles, grâce à ces machines qui nous permettent de faire de l'usinage laser et du formage. Nous avons installé le combiné poinçonneuse-laser Prima Power Combi Laser 1540, avec le magasin automatique Combo Tower qui nous permet de répondre à ces besoins".
Clivet utilise beaucoup de tôle dans ses produits, tant pour les composants structurels que pour les composants dits esthétiques.
"En raison du grand nombre de pièces que nous gérons, la machine combinée est la plus adaptée à nos besoins", poursuit M. Martini. "Par exemple, avec le laser, nous pouvons créer des bords arrondis selon les demandes de nos clients, tandis que la déformation nous permet de gagner en épaisseur tout en garantissant une certaine résistance de la tôle, ce qui évite les vibrations gênantes".
Grâce à ces investissements, Clivet vise à devenir complètement indépendant en matière de traitement de la tôle. "Nous connaissons une croissance de plus de 30 % par an et, à ce titre, nous continuons à avoir besoin de l'aide de fournisseurs externes pour répondre à nos besoins. Dans le même temps, nous achevons le transfert de nos anciens codes d'articles vers de nouveaux programmes qui seront créés sur la nouvelle ligne - il s'agit de 20 000 à 30 000 codes d'articles et cela prendra donc un certain temps. Notre objectif n'est pas de cesser de faire appel à des fournisseurs externes, mais d'être en mesure de combiner notre capacité de production avec un soutien externe pour gérer les pics de travail ou les situations d'urgence.

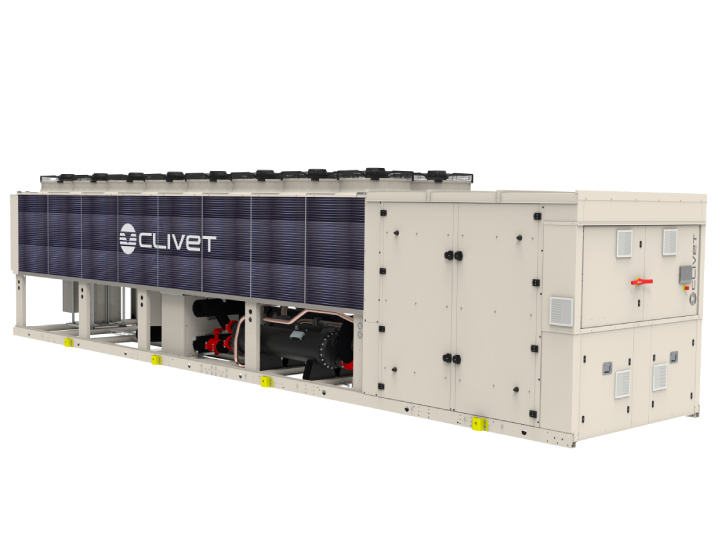
UN AVENIR TOUJOURS PLUS AUTOMATISÉ
L'investissement dans la ligne PSBB et dans le Combi Laser démontre également l'importance de l'automatisation pour Clivet qui, dans sa nouvelle usine de 30 000 m2, gérera des volumes accrus avec des solutions hautement automatisées et robotisées. Le Combi Genius, par exemple, a été conçu pour inclure un LSR (acronyme de "Loading and Stacking Robot") pour le chargement et le déchargement des pièces afin d'éviter les interventions manuelles et d'augmenter la fiabilité du processus de prélèvement des pièces découpées au laser. Le robot de chargement, de déchargement et d'empilage LSR est un robot de manutention des matériaux et des pièces pour les machines combinées poinçonnage-laser. Le LSR charge les tôles sur la machine et empile les pièces finies sur les palettes d'empilage, garantissant ainsi un fonctionnement précis et efficace du processus de manutention. Il convient de souligner que la pince robotisée dispose de différentes zones d'aspiration, chacune pouvant être contrôlée séparément. Grâce au système de mouvement d'empilage servocommandé, elle garantit une précision maximale. Pour augmenter la fiabilité du prélèvement des pièces découpées au laser, Prima Power a également développé la technologie RALC (Robot Assisted Last Cut). Pendant la dernière partie de la découpe, la machine et le robot effectuent des mouvements simultanés et synchronisés des axes, ce qui garantit un prélèvement sûr et fiable des pièces.
Un entrepôt automatique dédié était presque obligatoire pour Clivet qui, depuis quelques années, s'efforce de rendre ses systèmes autonomes grâce à un stockage automatisé qui garantit un approvisionnement constant sur 24 heures. Combo Tower est en effet une solution de stockage flexible destinée à automatiser le flux des matériaux, puisqu'elle met automatiquement à disposition les différents matériaux dès qu'ils sont nécessaires, sans délai, en servant de tampon ou de stockage intermédiaire pour les composants finis.
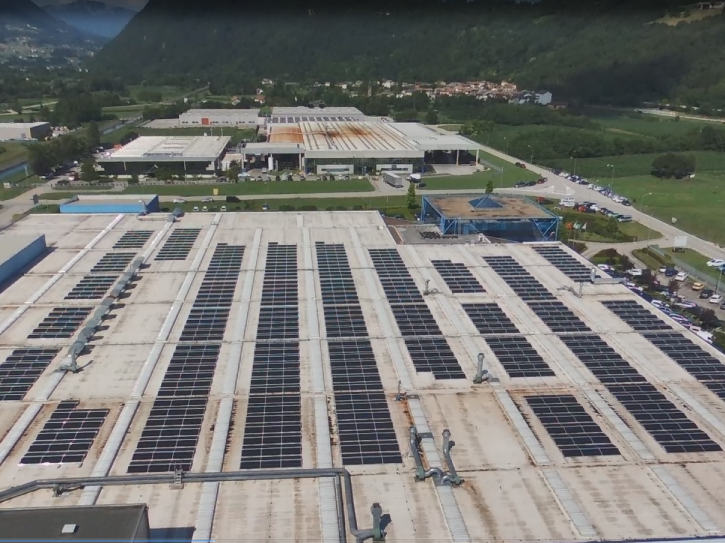
CHOISIR LA DURABILITÉ, CHOISIR LA TECHNOLOGIE SERVO-ÉLECTRIQUE
Pour soutenir la durabilité environnementale, Clivet a choisi de se concentrer sur la technologie servo-électrique qui est une caractéristique clé des machines Prima Power en tant que partie intégrante de sa stratégie de production.
"Les machines servo-électriques correspondent parfaitement à notre vision de la production, car elles ne consomment de la puissance et de l'énergie qu'en cas de besoin et uniquement dans les quantités requises, sans gaspillage. C'est pourquoi nous sommes convaincus que c'est la machine qui économisera le plus d'énergie, ce qui est très important pour nous. En fait, Clivet s'est fixé un objectif écologique : être neutre en carbone dans les trois ou quatre prochaines années et la technologie Prima Power est un allié fondamental pour atteindre cet objectif."
C'est pourquoi Clivet a complété son parc de machines avec trois presses plieuses servo-électriques Prima Power : deux eP 1030 de trois mètres et une eP 2040 de quatre mètres. Il est important de souligner que l'ensemble de l'usine de Feltre a déjà fait l'objet d'une rénovation durable importante, avec l'installation de lumières LED, de systèmes de climatisation utilisant des pompes à chaleur et d'un système photovoltaïque de 1,2 MW, dont la capacité sera bientôt doublée.
Clivet s'est fixé un objectif écologique : atteindre la neutralité carbone dans les trois ou quatre prochaines années et la technologie Prima Power est un allié fondamental pour relever ce défi.