
Clivet, Wachstum durch servoelektrische Technologie

Clivet ist einer der führenden Hersteller von Wärmepumpen und Kühlaggregate. Für die Erneuerung seines Maschinenparks der Blechbearbeitung, entschied sich das Unternehmen für die servoelektrische Technologie von Prima Power und entsprechend hochautomatisierte und vollintegrierte Lösungen unter 4.0-Aspekten. Das Kernstück der Abteilung ist die PSBB-Linie. Sie steuert die gesamte Werkstückbearbeitung, die mithilfe von Stanz-, Scher-, Puffer- und Biegestationen erfolgt.
Beim Betreten des in Feltre ansässigen Werks von Clivet offenbaren sich nicht nur jene Technologien, durch die das 1989 von Bruno Bellò gegründete Unternehmen heute zur Spitzengruppe im Sektor Klimatechnik gehört, vielmehr enthüllt ein solcher Besuch, wie sehr Innovationen und Nachhaltigkeit das Unternehmen seit Jahren prägen. Obwohl unser Bericht aufgrund unserer Unternehmensausrichtung nur die Blechbearbeitungsabteilung umfasst, zeugt jeder der gut 50 000 m2 des Werks von Clivet von der tiefen und verwurzelten Überzeugung des Unternehmens, dass nachhaltige Spitzenprodukte zum Vorteil und Wohlbefinden aller Menschen in einer nachhaltigen, innovativen und gesunden Umgebung hergestellt werden müssen.
Vor der Fortsetzung unserer Reportage aus dem Werk von Clivet sei auf folgende wichtige Tatsachen hingewiesen, die sich dem Besucher im Laufe des Werkrundgangs erklären: Clivet verzeichnet ein kontinuierliches Wachstum seiner Marke, erzielte in dreißig Jahren über 250 Millionen Euro Umsatz und erreichte eine internationale Führungsposition. Von diesem Erfolg zeugen auch das Bündnis mit der industriellen Gruppe MIDEA und das über 90 Länder umfassende Absatzgebiet, das aufgrund der hervorragenden Produktqualität und der ausgezeichneten Produktionsstrategie gewonnen wurde.
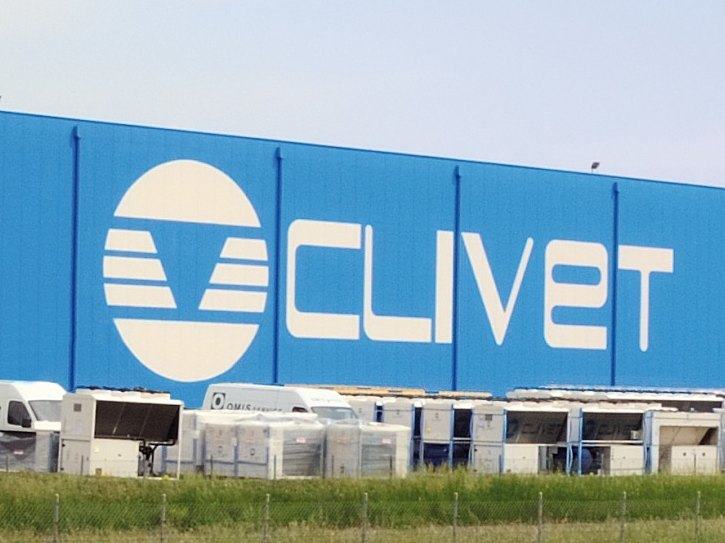
Technologischer Fortschritt
Im Zusammenspiel mit dem Wachstum erweiterte Clivet das Produktangebot kontinuierlich und ergänzte seine Produktion von Kühlaggregaten und Wärmepumpen um spezialisierte Systeme wie Rooftop-Einheiten und Wasserkreislaufsysteme sowie um spezielle Systeme für Wohnanlagen.
„Im Laufe dieses Wachstumsprozesses erkannten wir, dass unsere Blechbearbeitungsmaschinen die Produktionsanforderungen nicht mehr erfüllten“, erklärt Ing. Luca Martini, Industriemanager von Clivet, während er uns auf unserer Tour durch das Werk begleitet. „Es handelte sich um über 25 Betriebsjahre alte und entschieden überholte Maschinen. Wir mussten uns daher entscheiden, die komplette Bearbeitung entweder auszulagern oder in den Maschinenpark zu investieren und neue, leistungsfähigere Maschinen anzuschaffen. Wir entschieden uns für die Investition. Dadurch konnten wir eigenverantwortlich die Qualitätskontrolle sowie das Zeiten- und Prioritätenmanagement für unsere Produktion in die Praxis umsetzen. Im nächsten Schritt mussten wir entscheiden, welche der Linien, die Stanz- und Biegemaschinen umfassten, unseren Bedürfnissen am besten entsprach. Wir verglichen also einzelne Marken und Technologien und stellten nach einer Reihe von Prüfungen fest, dass die Lösung von Prima Power 63 % unserer Produkte bearbeiten konnte, ohne Werkstücke zu anderen Maschinen bringen zu müssen. Danach stand einer Zusammenarbeit mit Prima Power nichts mehr im Weg. In der Anfangsphase installierten wir nur die Kombination aus Stanz- und Schneidmaschine Shear Genius von Prima Power (Anm. d. Red.: sie führte damals noch den Markennamen Finn Power)“.
Durch die Installation von Shear Genius betrat Clivet das erste Mal das Prima Power-Universum. Natürlich war allen klar, dass sich Bediener als auch Techniker nach einem solch großen Technologiesprung zunächst eingewöhnen müssten. „Wir entschieden uns, mit dieser Maschinenkombination zu beginnen“, erklärt Martini, „da wir hierfür zunächst eine völlig neue Mentalität und Herangehensweise entwickeln mussten. Wir brauchten einige Zeit, um uns anzupassen, unsere Denkweise zu ändern und zu lernen, wie wir diese innovative Technologie am besten für unser Unternehmen nutzen können. Innerhalb eines Jahres hatten wir die optimale Produktionskapazität erreicht und die Shear Genius war vollständig in unseren Arbeitsablauf integriert.“
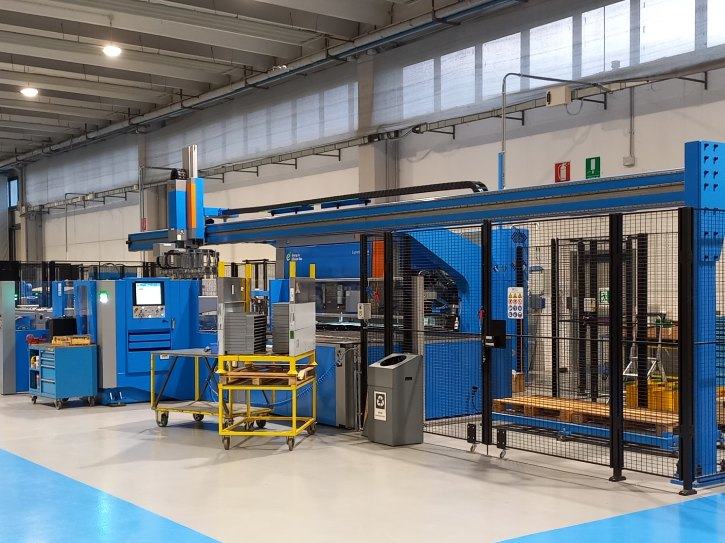
„Bis vor einigen Jahren produzierten wir fast nur auf Bestellung, entweder äußerst kundenspezifische Industriemaschinen oder Kleinserien, also meistens Maschinen mit großer oder mittlerer Leistungsfähigkeit. Im Augenblick dringen wir verstärkt in den Bereich für Wärmepumpen vor und stellen auch Massenproduktionen her; im neuen Werk wollen wir beispielsweise 100 000 Wärmepumpen herstellen“. Diese neuen Anforderungen an die Produktion erforderten abermalige Investitionen und technologische Modernisierung. „In Anbetracht dieser Mengen wurde die Anschaffung einer Biegemaschine interessant. Diese würde uns mehr Autonomie gegenüber externen Lieferanten garantieren und uns gleichzeitig volle Kontrolle über die Produktqualität verschaffen. „Mit diesem Gedankengang wandten wir uns erneut an Prima Power. Daraufhin wurde unsere Shear Genius auf eine PSBB-Linie (Punching, Shearing, Buffering, Bending [Stanzen, Scheren, Puffern, Biegen]) aufgerüstet, diese um eine Biegemaschine vom Typ EBe 2720 ergänzt. Die Biegemaschine kann nicht nur im Linienbetrieb arbeiten, sondern lässt sich mithilfe eines zusätzlichen Wagens auch manuell mit nur zu biegenden Werkstücken beladen. Die sehr flexible PSBB-Linie von Prima Power formt Rohbleche auf automatische Weise in hochqualitative, bereits gebogene Komponenten um.
Wie bereits erwähnt steht PSBB für Punching, Shearing, Buffering und Bending bzw. übersetzt für Stanzen, Scheren, Puffern und Biegen. Die Ausführung all dieser Prozesse erfolgt mit servoelektrischer Technologie.
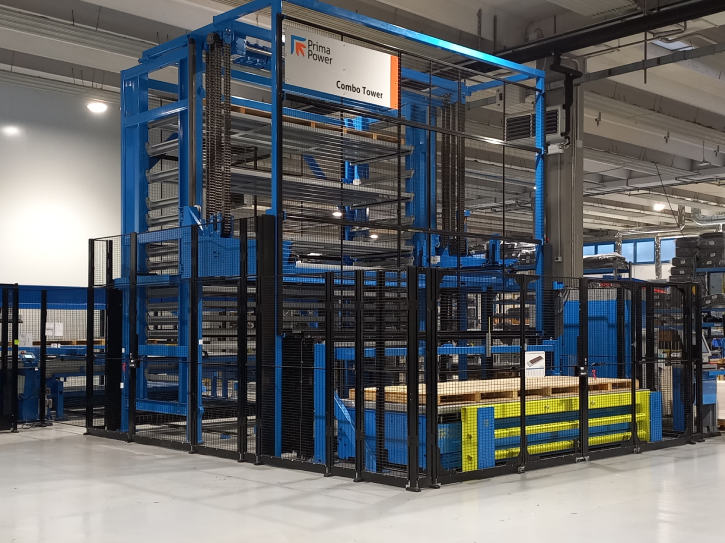
Wenn eine einzige Linie nicht ausreicht ...
„Nach der Produktionsinbetriebnahme der PSBB-Linie von Prima Power erkannten wir, dass die Leistungen der Linie unsere Erwartungen voll erfüllte. Da wir bei der Bearbeitung von stärkeren Blechen – insbesondere von 4 m langen Blechen – Nachholbedarf hatten, entschlossen wir uns, eine weitere Investition zu tätigen. Wir entschieden uns für eine kombinierte Laserstanzmaschine, weil wir dank dieser Maschinen, die sowohl Laserbearbeitung als auch Umformung ermöglichen, gleichzeitig produktiv und flexibel sein wollten. Anschließend erfolgte die Installation der kombinierten Laserstanzmaschine Combi Laser 1540 von Prima Power, die das automatische Magazin Combo Tower besitzt und damit unseren Bedürfnissen entsprach.
Für die Produkte von Clivet werden viele Blechtafeln verarbeitet, die sowohl strukturelle als auch ästhetische Aufgaben erfüllen.
Im Zusammenhang mit der Blechbearbeitung ist es das Ziel von Clivet, dank dieser Investitionen völlig autonom agieren zu können. „Unser jährliches Wachstum beträgt mehr als 30 Prozent. Zur Deckung unseres Bedarfs sind wir also nach wie vor auf externe Lieferanten angewiesen. Eine weitere Aufgabe für uns ist die Umwandlung alter Codes in neue Programme, um diese auf der neuen Linie ausführen zu können. Dabei gehen wir von 20 000 bis 30 000 Codes aus, was einen gewissen Zeitbedarf erfordert. Wir wollen jedoch unsere externen Zulieferer nicht abschaffen, sondern vielmehr eine externe Unterstützungsplattform ins Leben rufen, die uns dabei hilft, unsere eigenen Produktionskapazitäten zu ergänzen und Auftragsspitzen oder Extremsituationen zu meistern.“

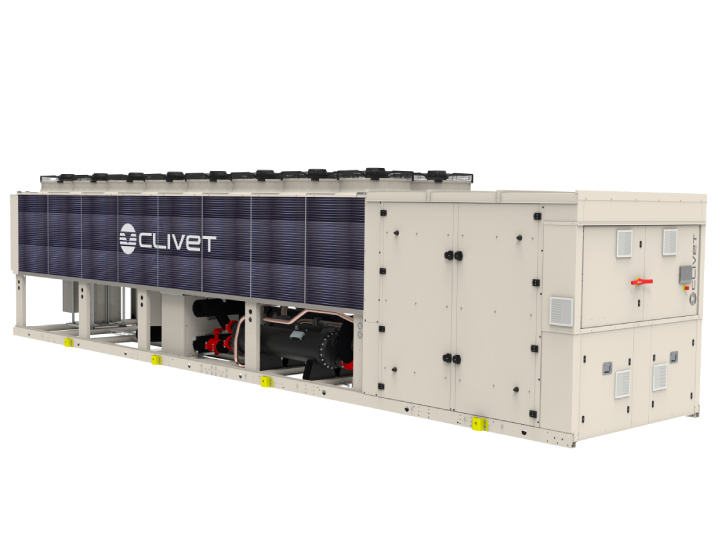
Stark automatisierte Zukunft
Die Investitionen in die PSBB-Linie und die Laserstanzmaschine Combi Laser bestätigen den Stellenwert, den die Automatisierung für Clivet hat. Auch in der neuen, 30 000 m2 großen Produktionsstätte wird das Unternehmen die steigenden Produktionsmengen hochautomatisiert und roboterisiert bewältigen. Die Combi Genius sieht beispielsweise das Vorhandensein eines Roboters vom Typ LSR vor (ein Akronym für „Loading and Stacking Robot [Belade- und Stapelroboter]“). Er be- und entlädt Werkstücke und vermeidet dadurch händische Tätigkeiten. Gleichzeitig erhöht sich auf diese Weise die Zuverlässigkeit beim Entladen der lasergeschnittenen Werkstücke. Der Be-, Entlade- und Stapelroboter LSR unterstützt kombinierte Laserstanzmaschinen, indem er Materialien und Werkstücke versetzt. Der LSR belädt die Maschine mit den Blechtafeln und stapelt die fertigen Werkstücke auf Stapelpaletten; er garantiert im Laufe des Prozesses für eine akkurate und effiziente Ausführung der Materiaversetzung. Hervorzuheben ist, dass der Robotergreifer über voneinander unabhängige Ansaugbereiche verfügt, die sich einzeln kontrollieren lassen. Das von einem Servosystem angetriebene Versetzungs- und Stapelsystem weist maximale Ausführungsgenauigkeit auf. Zur Steigerung der Zuverlässigkeit der Entnahme der vom Laser geschnittenen Werkstücke hat Prima Power die Technologie RALC entwickelt (Robot Assisted Last Cut [Robotergestützter Abschlussschnitt]). Hierbei führen die Maschine und der Roboter beim abschließenden Schnitt simultane, synchronisierte Achsenbewegungen aus; dies garantiert eine sichere und zuverlässige Werkstückentnahme.
Ein spezielles automatisches Lager war für Clivet fast schon obligatorisch. Seit einigen Jahren arbeitet das Unternehmen daran, seine Systeme dank einer automatischen Lagerung, die eine konstante Versorgung über 24 Stunden gewährleistet, autonom zu gestalten. Combo Tower erfüllt die Anforderungen an eine flexible Lagerhalterung mit automatisiertem Materialfluss, da der Tower bei Bedarf unterschiedliche Materialien automatisch und unmittelbar bereitstellt und dadurch ein Puffer- bzw. Zwischenlager für fertige Komponenten darstellt.
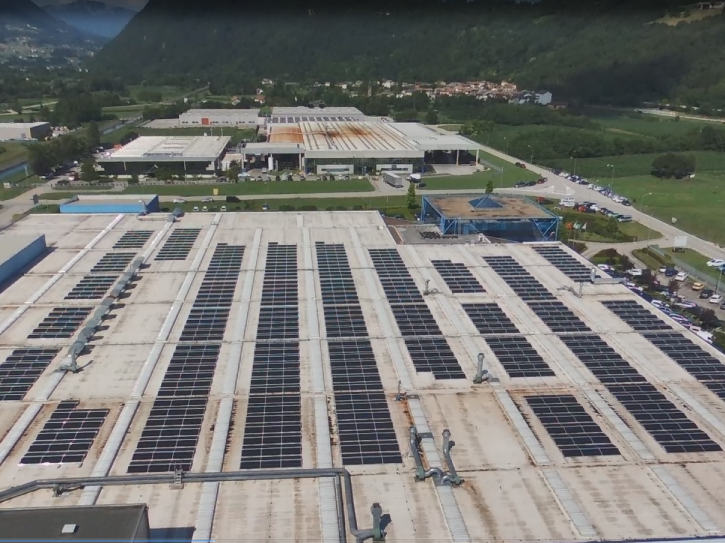
Nachhaltigkeit durch servoelektrische Technologie
Clivet entschloss sich zum Einsatz von servoelektrischer Technologie, und diese ist ein Wesensmerkmal der Maschinen von Prima Power – tatsächlich verkörpert sie in Bezug auf die Nachhaltigkeit einen integralen Bestandteil der Produktionsstrategie.
„Servoelektrische Maschinen eignen sich ideal für unser Verständnis von Produktionsvorgängen, denn sie nutzen Strom und Energie ausschließlich bei Bedarf und nur in den notwendigen Mengen – sie arbeiten also verschwendungsfrei. Wir sind zuversichtlich, dass mit dieser Maschine am meisten Energie eingespart wird, und das ist uns sehr wichtig. Tatsächlich will Clivet den Umweltschutz unterstützen und innerhalb der nächsten drei bis vier Jahre klimaneutral werden. Zum Erreichen dieses Ziels und Bewältigen der entsprechenden Aufgaben ist die Technologie von Prima Power ein wichtiger Helfer. “
Clivet hat aus diesem Grund seinen Maschinenpark um drei servoelektrische Biegepressen von Prima Power erweitert: zwei eP 1030 mit 3 m und eine eP 2040 mit 4 m. Dabei ist zu bedenken, dass bereits das gesamte Werk in Feltre diesbezüglich umfangreich renoviert wurde; beispielsweise wurden LED-Beleuchtungen und Klimasysteme mit Wärmepumpen installiert sowie eine Photovoltaikanlage aufgestellt, deren augenblickliche Leistung von 1,2 MW bis März 2023 verdoppelt wird.
Clivet has set itself a green goal: to achieve carbon neutrality in the next three to four years and Prima Power technology is a fundamental ally in overcoming this challenge.