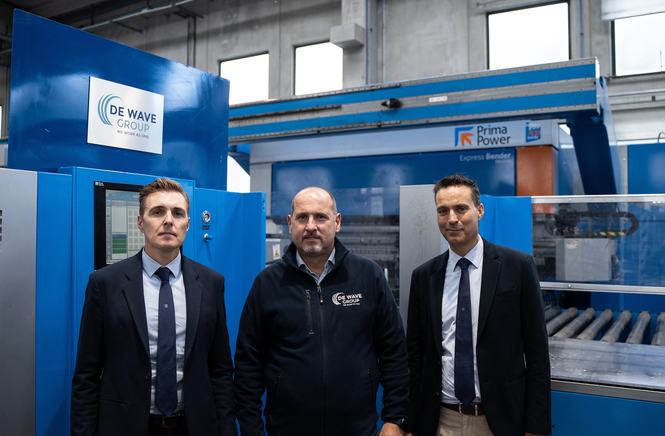
De Wave, La eficiencia y la productividad se afianzan
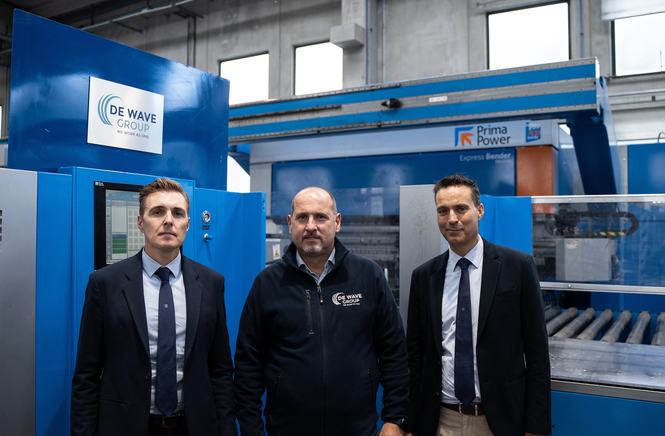
Surcan los mares de todo el mundo, acogiendo desde docenas hasta miles de personas. hablamos de cruceros, grandes yates y barcos fluviales para los que el grupo de wave produce diversos tipos de mobiliario y accesorios de a bordo, todos ellos creados utilizando tecnologías integradas de una línea automática de alto rendimiento de Prima Power.
Aunque para vivir eternamente en un crucero «solo hace falta» esperar un par de años y disponer de un millón de dólares de sobra (según el reciente anuncio de una compañía de cruceros que ha sido la primera del mundo en presentar un barco residencial privado con más de 500 apartamentos), afortunadamente se necesita mucho menos para pasar unos días de relax en un crucero, visitando lugares de todos los continentes, conocidos y menos conocidos. De hecho, existe una amplia oferta de embarcaciones con capacidad para entre unas decenas y unos miles de personas (pasajeros y tripulación), que incluye grandes cruceros, grandes yates, así como, aunque no menos equipados, barcos fluviales. Al igual que aquellos para los que De Wave produce mobiliario y accesorios, lo que le convierte en un contratista de referencia con una amplia red de oficinas e instalaciones de producción que apoya a la industria de los yates y las embarcaciones de recreo en todo el mundo.
Creada a partir de la fusión de cinco empresas, De Wave es hoy una filial propiedad al cien por cien del fondo de inversión estadounidense Platinum Equity. Tiene su sede en Génova (Italia), pero también forma parte de un grupo internacional con varias sucursales en Polonia, Francia, Alemania, Finlandia, Singapur y Miami (EE. UU.). En Italia, también opera en Monfalcone (GO), con una planta centrada principalmente en la producción de paneles y techos para el equipamiento de cabinas.
«Los distintos tipos de paneles y elementos de revestimiento», afirma Alberto Malatesta, director de planta de De Wave, «deben cumplir unas normas de precisión y calidad extremas para garantizar los elevados estándares industriales que se esperan de los requisitos estéticos y de seguridad, así como el cumplimiento de los estrictos plazos de entrega».
Estas particularidades se consiguen hoy gracias a la sólida y fiable tecnología suministrada e instalada en 2021 por Prima Power. Por supuesto, estamos hablando de la nueva versión Direct de la línea de producción PSBB, que puede procesar chapa metálica desde un sistema de almacenamiento, automatizar la gestión del material y de la información, y combinar los diferentes procesos de producción en un único proceso completo flexible y totalmente integrado.
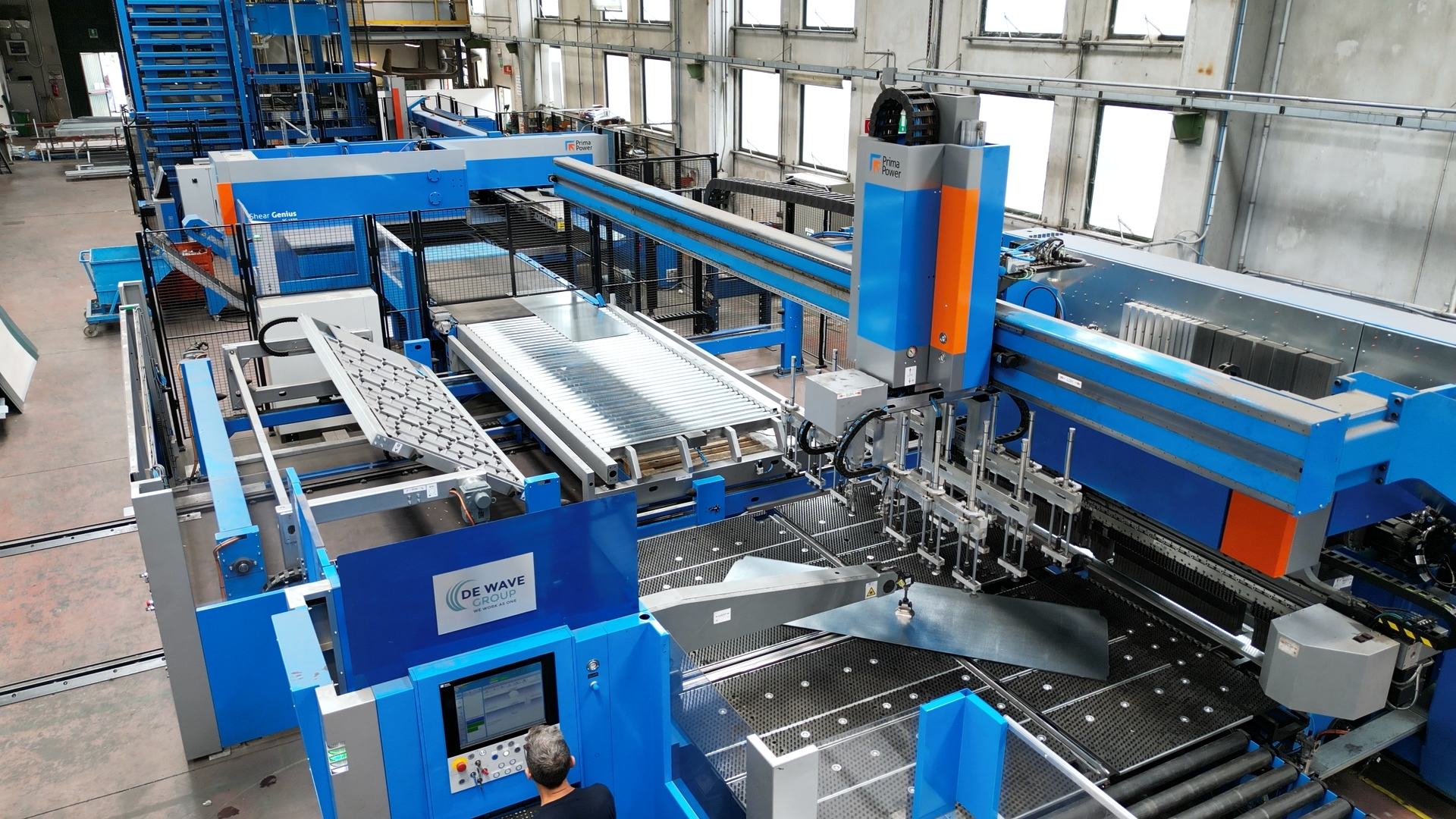
DEL CORTE MANUAL A LA AUTOMATIZACIÓN DE FÁBRICAS
El sistema de producción compacto Prima Power PSBB (punzonado, cizallado, conformado y plegado) transforma automáticamente las chapas metálicas en bruto en componentes de alta calidad listos para plegar. El flujo de material puede organizarse con la máxima flexibilidad: para transferir piezas directamente a la plegadora automática, para equilibrar los distintos requisitos de tiempo de plegado y punzonado/cizallado, para salir del sistema y para introducir nuevo material en el sistema. La función de almacenamiento intermedio, flexible y versátil, garantiza un funcionamiento optimizado en costes y tiempo en todo momento, independientemente de la tarea que se esté realizando. De hecho, la productividad que ofrece este concepto deriva de la integración intrínseca de un versátil sistema de punzonado servoeléctrico con sistemas integrados de cizallado y plegado servoeléctricos, todo ello coordinado por un sofisticado software que garantiza flujos de material y pasos del proceso óptimos.
«De Wave», señala Malatesta, «ha optado por invertir en las tecnologías de Prima Power para aumentar su flujo tecnológico y de producción, y lograr una mayor eficacia garantizando así una mayor productividad. La decisión también fue impulsada por el deseo específico de traer gradualmente a la empresa el 100% de la producción de ‘cáscaras’ para los paneles de cabina, que hasta ahora se externalizaba en gran medida».
Además, al incorporar tecnologías adicionales de automatización y ensamblaje, la nueva planta de Prima Power también ha permitido pasar de la producción por lotes al ‘flujo de una pieza’, mucho más racionalizado y eficaz, con lo que también han aumentado la calidad y la competitividad.«La nueva línea», añade Malatesta, «ha dotado de repetibilidad al proceso y al producto, un factor esencial y decisivo para nuestro negocio, ya que el aspecto estético depende en gran medida de la unión entre un panel y el siguiente, que no debe presentar imperfecciones. Se ha conseguido una mayor productividad al suprimir la instalación de un perfil de unión fijado mecánicamente, gracias a los pliegues obtenidos, que permiten uniones precisas con tolerancias muy bajas».
Así pues, el nuevo sistema ha permitido a De Wave realizar una notable mejora operativa, pasando de un proceso de corte puramente manual a una verdadera automatización de la fábrica.
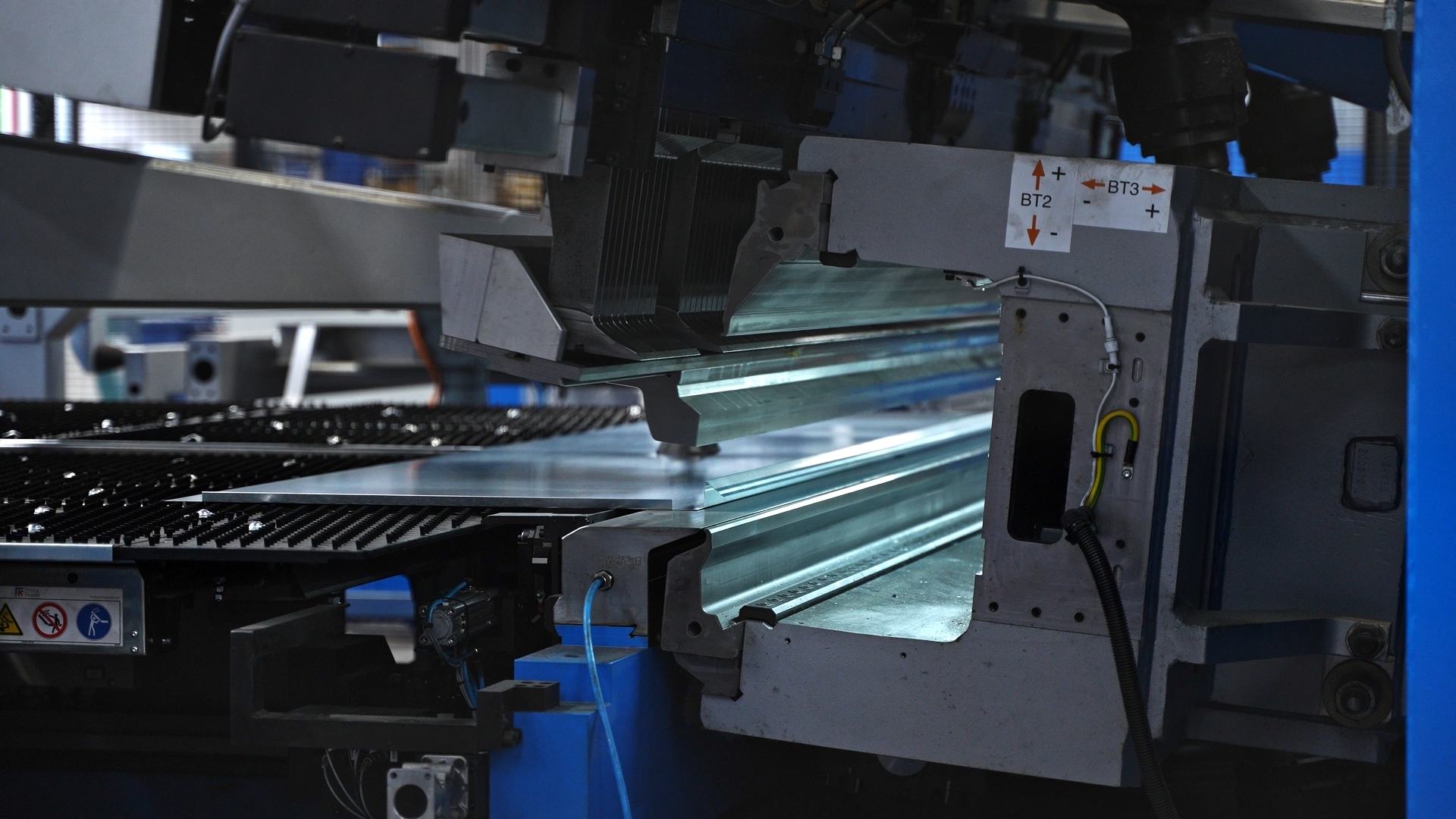
DEL SISTEMA DE ALMACENAMIENTO AL PLEGADO EN PRENSA DE FORMA RÁPIDA Y PRECISA
El equipo elegido para el nuevo sistema PSBB de De Wave incluye el sistema de almacenamiento de chapa FL utilizado junto con la punzonadora/cizalla combinada Shear Genius SG 1530 y la plegadora de paneles Express Bender EBe 2720.
«Estas tecnologías de alto nivel», prosigue Malatesta, «han implicado la formación de nuestros empleados en la fase de instalación y puesta en marcha de la planta, porque han pasado de manejar un proceso tradicional realizado con una cizalla, una punzonadora y una plegadora-prensa de principios de los años 2000, a una línea totalmente automatizada. Esta trayectoria de crecimiento, sin embargo, ha llevado a una mejora constante y continua de las competencias de nuestros empleados, alcanzando resultados muy satisfactorios hasta la fecha».
En concreto, la línea de producción automatizada consta de tres áreas operativas principales. La primera es donde se encuentra el almacén de 10 posiciones de la torre FL, donde se cargan las chapas listas para ser procesarlas. La segunda zona es la primera estación operativa donde se encuentra la Shear Genius SG 1530 combi y donde tiene lugar la optimización del nesting. La tercera zona es la Express Bender EBe 2720 y es donde se introducen las piezas cizalladas y punzonadas para crear la ‘cáscara’ final. Hay dos salidas de material diferentes al final de la línea: una para las ‘cáscaras’ acabadas, que se colocan en estanterías especiales; y otra en la que se introducen las ‘cáscaras’ paneladas que requieren un plegado adicional. De esto se encarga una plegadora Prima Power situada en la parte delantera de la línea, antes de volver a depositarse en otras estanterías para continuar el flujo de producción.
«La puesta en marcha de esta nueva línea», reitera Malatesta, «nos ha permitido subcontratar una parte importante de nuestra producción de 'cáscaras', lo que nos permite lograr plazos de entrega cada vez más estrictos, una reducción de las no conformidades y un producto de calidad aún mejor. Ahora, tenemos capacidad para producir cáscaras de chapa en unos 40 a 80 segundos en flujo continuo, dependiendo de su complejidad y de los pliegues de los paneles. Actualmente estamos en un total de unos 15 000 paneles/mes, pero con una ambiciosa previsión de más de 18 000 al mes. Estos paneles también están diseñados y mecanizados para garantizar un montaje rápido y sin errores en la obra, normalmente en espesores de entre 0,5 y 0,8 mm».
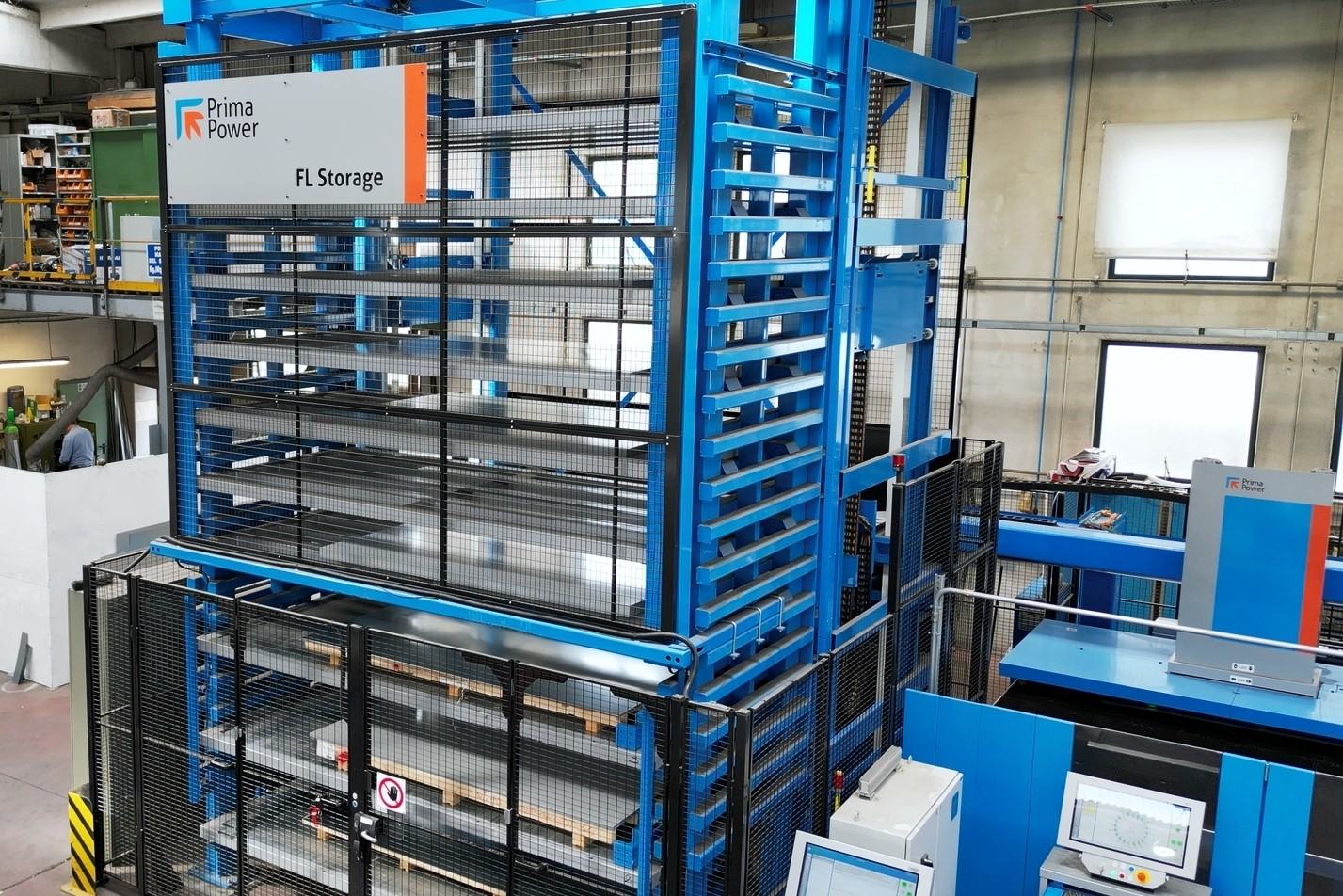
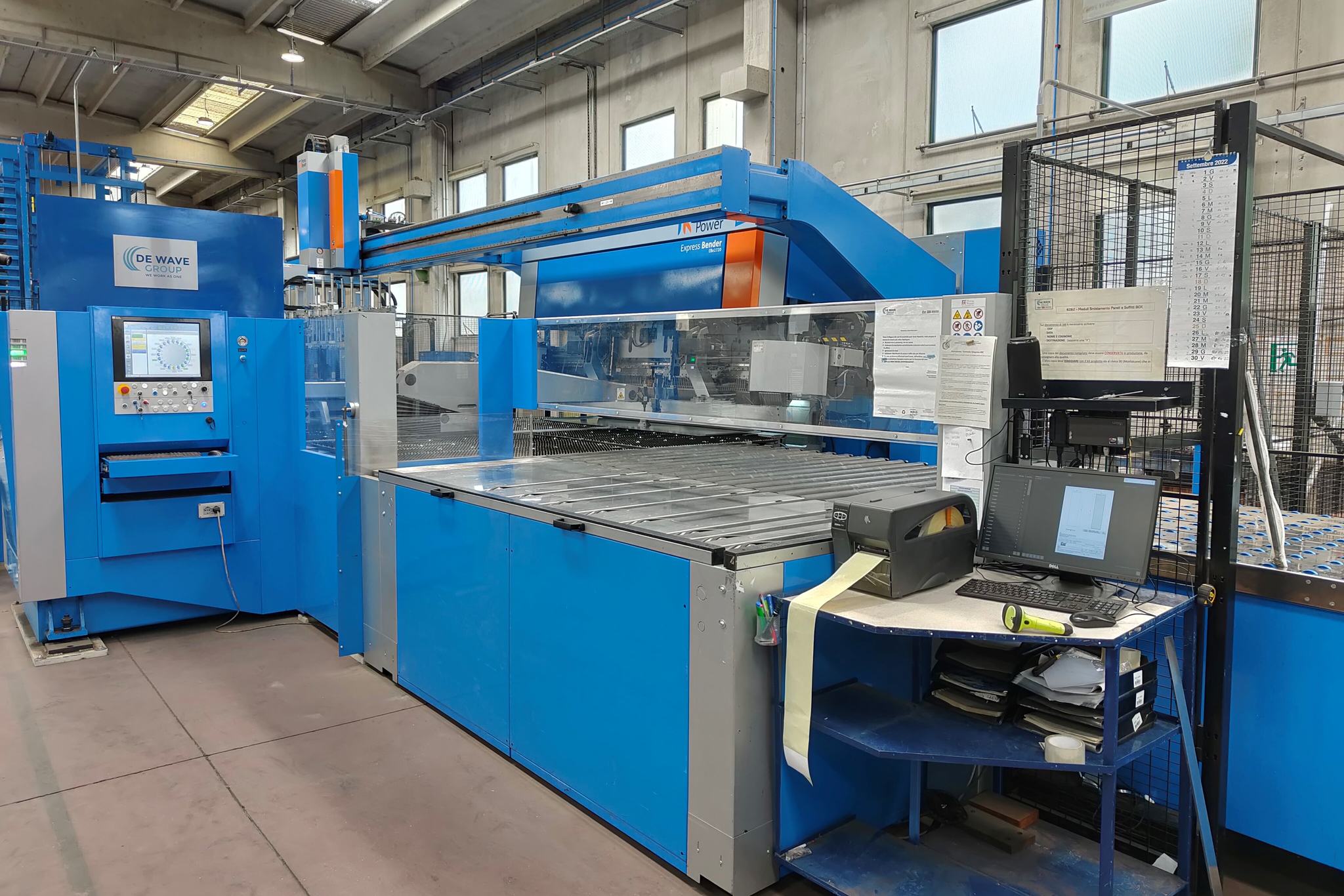
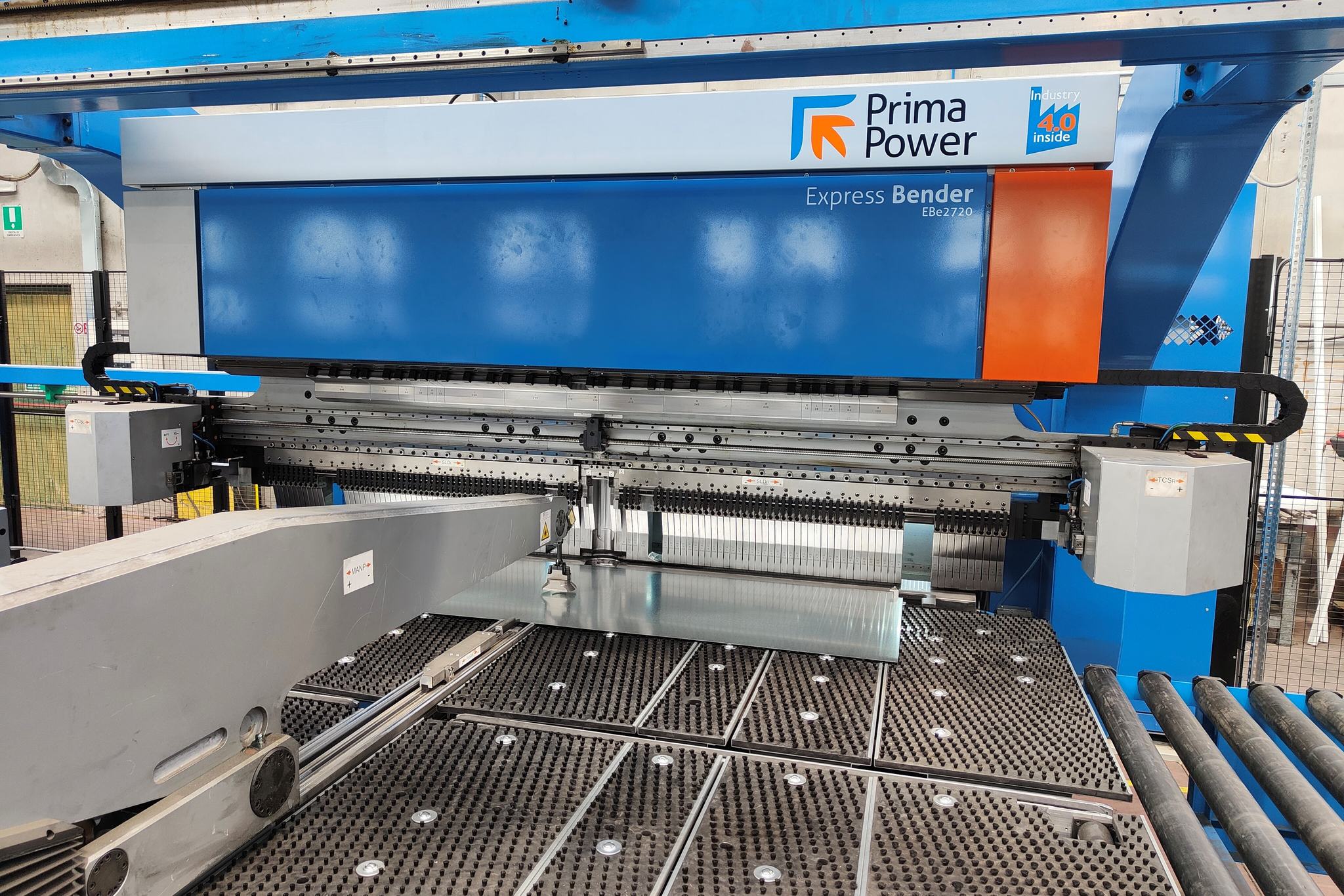
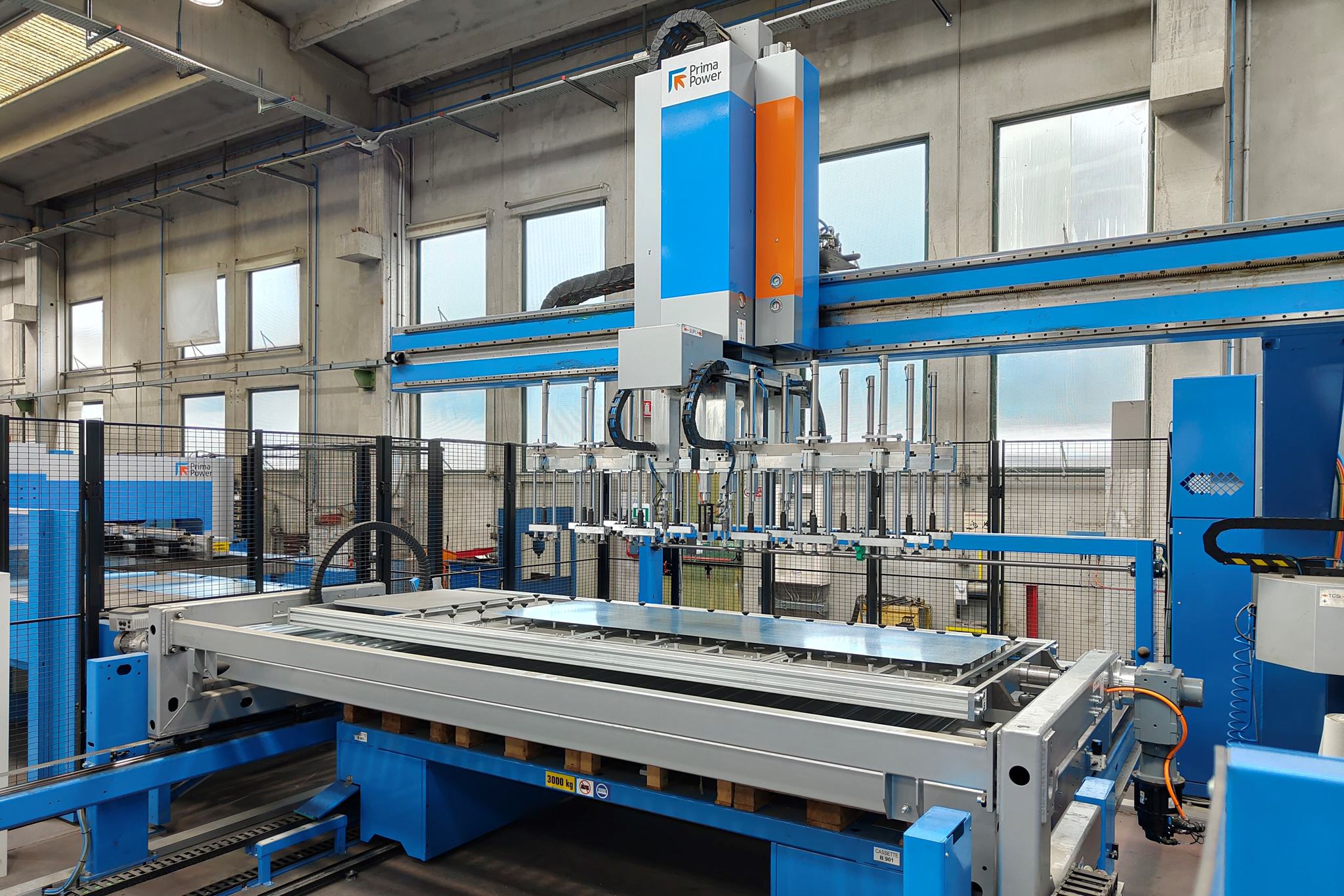
EL VALOR AÑADIDO DE LA PROGRAMACIÓN PARAMÉTRICA
La configuración de la línea elegida por De Wave está perfectamente calibrada en función de los requisitos específicos. Se trata de un excelente compromiso que aúna flexibilidad, compacidad y productividad, mientras que el sistema PCD equilibra e iguala el tiempo entre la punzonadora y la paneladora.
«El aspecto del software», subraya Malatesta, «también ha demostrado ser clave en el crecimiento operativo interno. Desde este punto de vista, la programación paramétrica fue uno de los requisitos discutidos y solicitados a la hora de evaluar la elección de la planta, ya que nuestros paneles difieren esencialmente en tamaño, partiendo de una geometría básica. Una vez definida la sección del panel de referencia, el sistema pasa rápidamente los kits a producción utilizando una de las variables ya guardadas, ajustando solo unos pocos parámetros de corte y plegado, con la ventaja de poder maximizar la velocidad de producción y dejar la línea lista para el montaje, la electrificación, el embalaje y el envío a la obra.
El envío a la obra se trata con el mismo cuidado y consideración para mantener todos los requisitos, incluidos los ya mencionados relacionados con la estética y la seguridad.«Estos requisitos de seguridad», añade Malatesta, «corresponden al cumplimiento de la resistencia a incendios y a una carga estructural específica una vez terminado el panel. Desde esta perspectiva, debemos recordar no sólo las continuas tensiones a las que están sometidas las piezas, dado que se montan en los barcos, sino también el hecho de que están en contacto con un entorno marino, lo que podría provocar fenómenos de corrosión e interferir en su durabilidad».
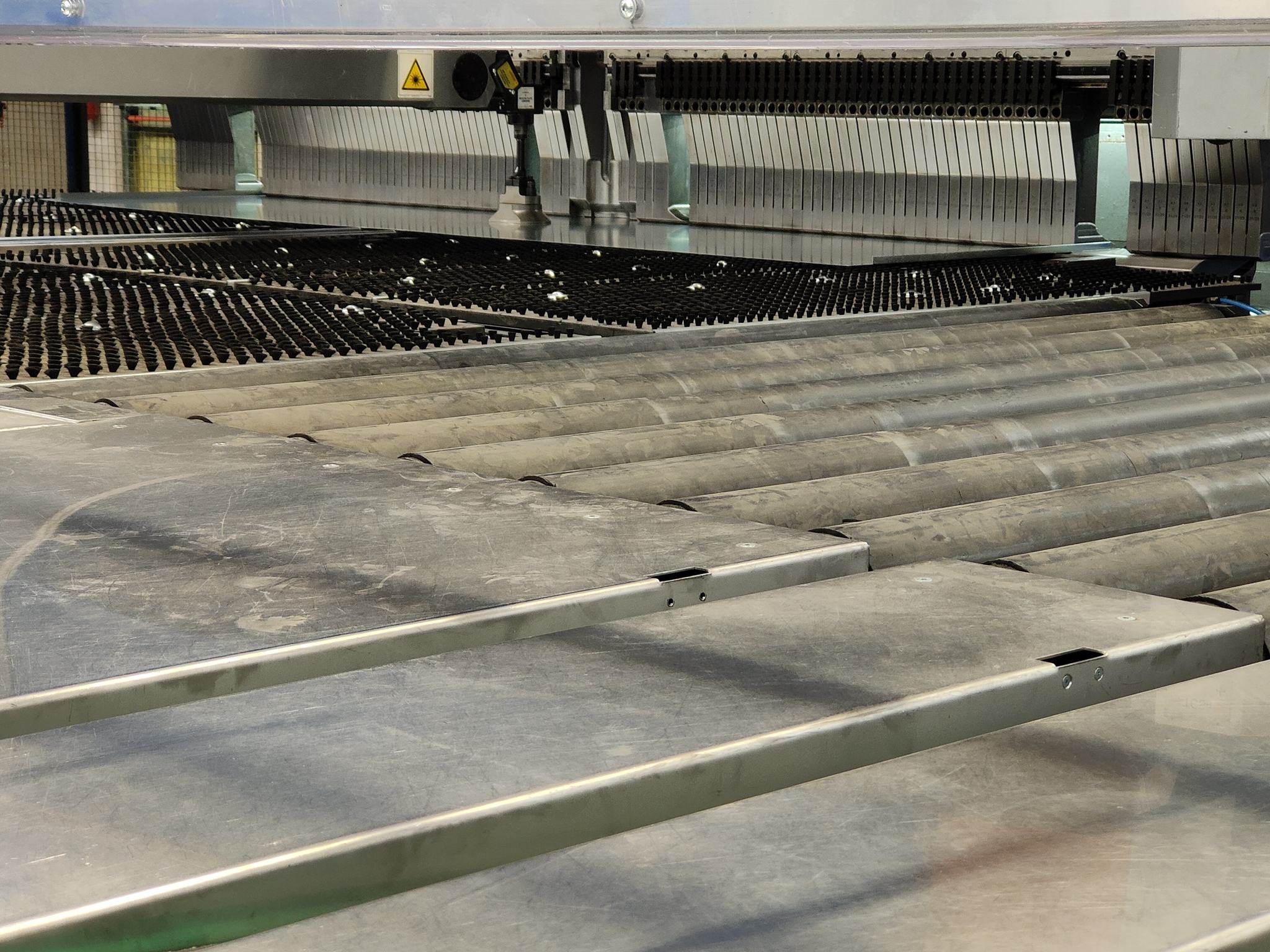
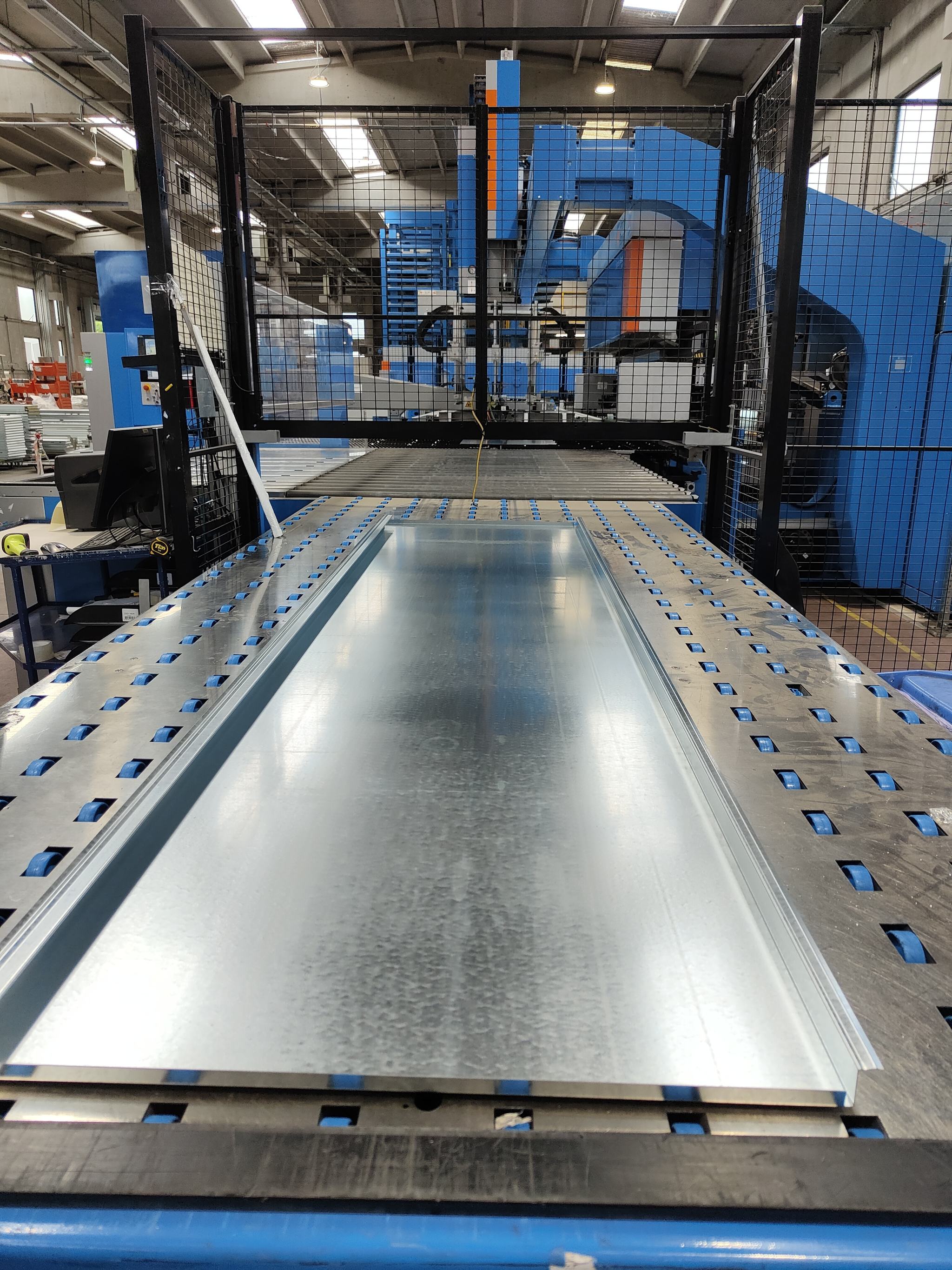
DE PANELES A LLAVE EN MANO
La integración de la nueva línea Prima Power ha permitido a De Wave rediseñar sus activos operativos, como ya se ha mencionado, incorporando internamente un mayor porcentaje de la producción de ‘cáscaras’ paneladas, pero también trayendo de vuelta otras que antes también se externalizaban, como la producción de unidades húmedas realizada en las fábricas polacas de la empresa.
«La planta de Monfalcone», prosigue Malatesta, «donde actualmente procesamos unos 200 000 metros cuadrados de paneles acabados al año, cuenta con una media de unos 80 empleados repartidos entre los distintos departamentos y trabajando en varias líneas de proceso».
Estas líneas de proceso incluyen la nueva PSBB, así como una línea de montaje semiautomática de flujo continuo atendida por dos robots (uno para cortar el aislamiento y otro para rociar el pegamento), flanqueada por dos prensas plegadoras y una punzonadora. También hay una perfiladora para fabricar duelas y una cizalla.
«Hemos mantenido algunas estaciones manuales de montaje de paneles como reserva», prosigue Malatesta, «para cubrir las paradas de la planta, los trabajos de mantenimiento o los picos de trabajo extremos».
En este sentido, ya hay planeadas nuevas inversiones en tecnología (también en la planta de Monfalcone) con vistas a una mejora y un crecimiento continuos, mejorando y optimizando aún más el flujo de producción, tanto con ampliaciones como con sustituciones de máquinas que ya han quedado obsoletas.
«La visión de la empresa», concluye Malatesta, «es integrar toda la parte de ingeniería de planta de la construcción naval con la producción visible, concretamente paneles, techos y unidades húmedas. Por eso, nos estamos introduciendo en el mercado no solo con inversiones en tecnología, sino también con adquisiciones de empresas para poder ofrecer un servicio llave en mano cada vez más completo».
En resumen, presentarnos como un fabricante y contratista cada vez más global, capaz de cubrir toda la gama de equipamiento interior de cruceros, grandes yates y barcos fluviales, tanto nuevos como reacondicionados.
La puesta en marcha de esta nueva línea nos ha permitido subcontratar una parte importante de nuestra producción de 'cáscaras', lo que nos permite lograr plazos de entrega cada vez más estrictos, una reducción de las no conformidades y un producto de calidad aún mejor.
Busca una solución similar para su empresa? Encuéntralo aquí
PSBB
SISTEMAS DE MANUFACTURA FLEXIBLE
Un sistema de manufactura flexible
Shear Genius EVO
MÁQUINAS COMBINADAS DE PUNZONADO Y CIZALLADO