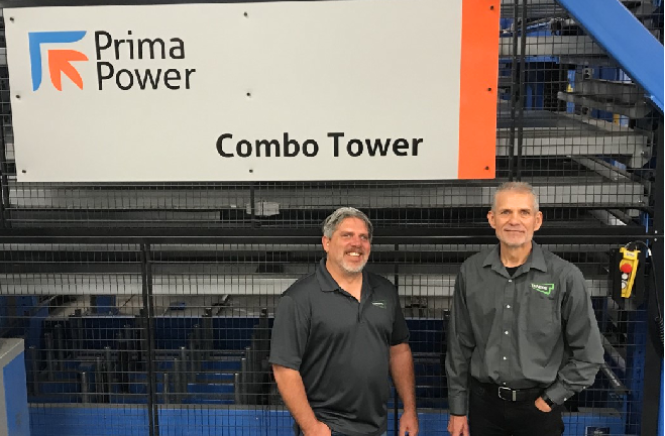
Cadrex - Combining technologies to evolve capabilities
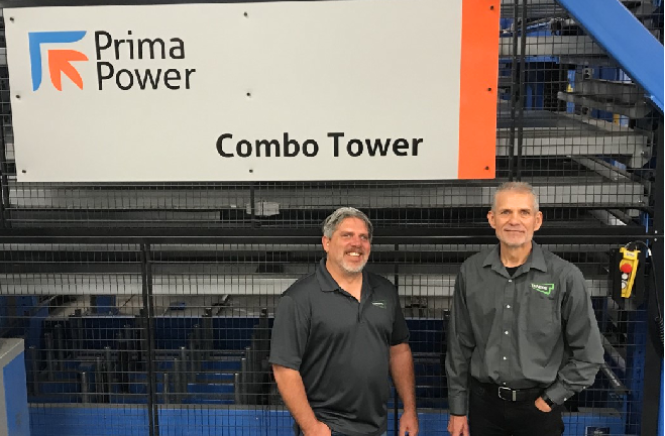
American company leverages Prima Power for streamlined process integration.
CADREX, A LEADING US-BASED MANUFACTURING SOLUTIONS PROVIDER, UPGRADED ITS CAPABILITIES BY ADOPTING PRIMA POWER’S LPBB INTEGRATED AND FLEXIBLE SYSTEM
In 2022, Chicago-based CGI Manufacturing Holdings rebranded itself as Cadrex Manufacturing Solutions. The company has transformed itself into a unified platform that leverages Industry 4.0 technology to drive medium- to high-volume manufacturing solutions. It has combined company acquisitions, technology investments, and a team of skilled craftspeople to serve a diverse range of industries. With 1.5 million sq. ft. of manufacturing space in 20 locations across the U.S. and Mexico, Cadrex has become one of the largest mechanical providers in North America.
The Cadrex facility in Dresser, Wisconsin, manufactures and assembles custom sheet metal and injection molded products that range from cloud and edge infrastructure, network, compute and storage, fiber optics and 5G, and renewable energy. To keep pace with its sales growth, the company began looking for a laser cutting and bending flexible manufacturing system in 2019.
This search led to Prima Power’s showroom in Arlington Heights, Illinois. “We decided on Prima Power’s LPBB integrated system, which includes the laser/punch Combi Genius, a loading and stacking robot, the Combo Tower and the EBe automated bender,” says Ed Moryn, automation manager for Cadrex. “We reviewed the different capabilities of the system, and what would fit into our building. We also discussed where Prima Power was with Industry 4.0 and we concluded they would be a good partner to move forward with.”
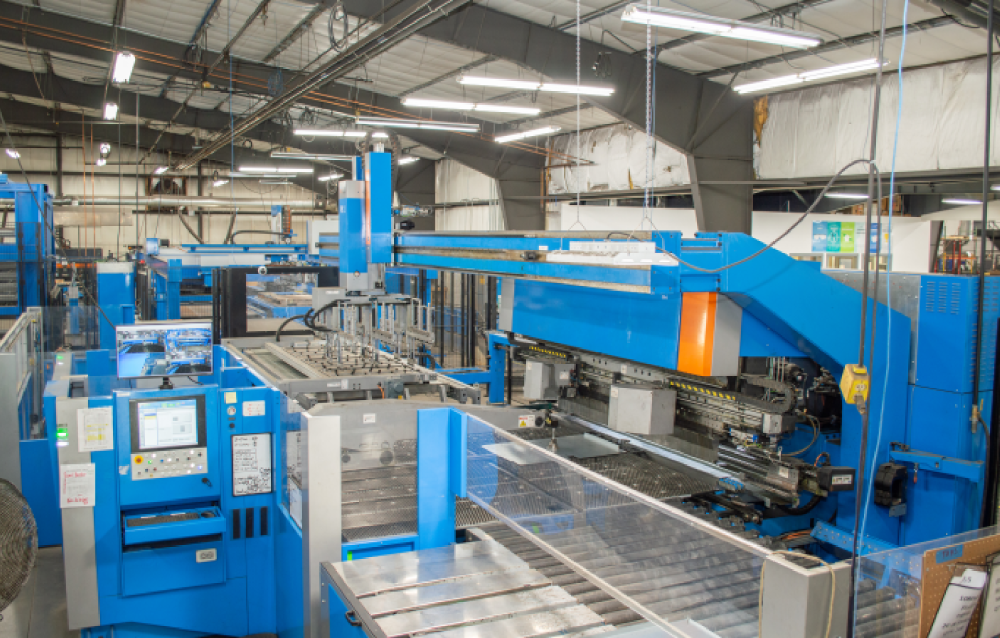
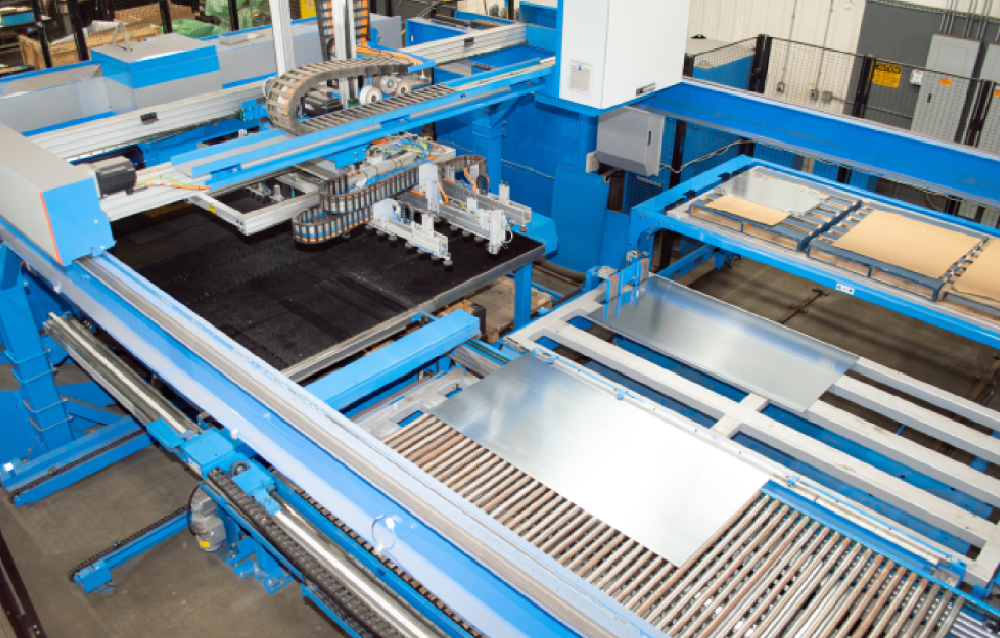
ENHANCING PRODUCTIVITY BY INTEGRATING MULTIPLE PROCESSES
While Cadrex purchased the LPBB system in 2019, the onset of COVID delayed delivery. The Express Bender was installed in 2019, followed by the Combi Genius and the manufacturing cell’s other components in 2020.
The compact LPBB sheet metal manufacturing system processes blank sheets into ready-bent, high-quality components automatically. The system integrates punching, laser cutting, bending and intelligent part handling. The automatic Express Bender employs Prima Power’s servo-electric technology for faster production and reduced energy consumption and maintenance costs. The Combi Genius represents a significant change to the sheet metal fabrication process by combining different technologies, such as servo-electric and fiber laser, to process components in just one setup. Faster and more accurate, the system eliminates the need for multiple setups and the resulting longer production times.
“The efficiency and productivity of the EBe panel bender has been phenomenal,” says Steve Riemenschneider, director of engineering soft tool for Cadrex. “We have infrastructure parts that have hems, up and down bends, and some bends that are large, measuring up to 2 ft. by 8 ft. The panel bender replaces three press brakes and six people”, he says.
“With the current marketplace, adding six additional press brake operators would have been a real challenge. The EBe picks the sheet off the Combi Genius, bends it and then stacks it for assembly. Our throughput is much better. The automated EBe has eliminated much of the human error that occurred when bending was done with manual press brakes.”
Riemenschneider says the Combi Genius allows the company to use its standard turret tooling that we have in its stand-alone turret punch presses. “It produces 300 parts per hour and runs lights out. Between the Combo Tower and the loading and stacking robot that was added to the Combi Genius, we have seen 300 percent productivity gains in comparison to our standard methods. The bender is closer to productivity gains of 500 to 600 percent.”
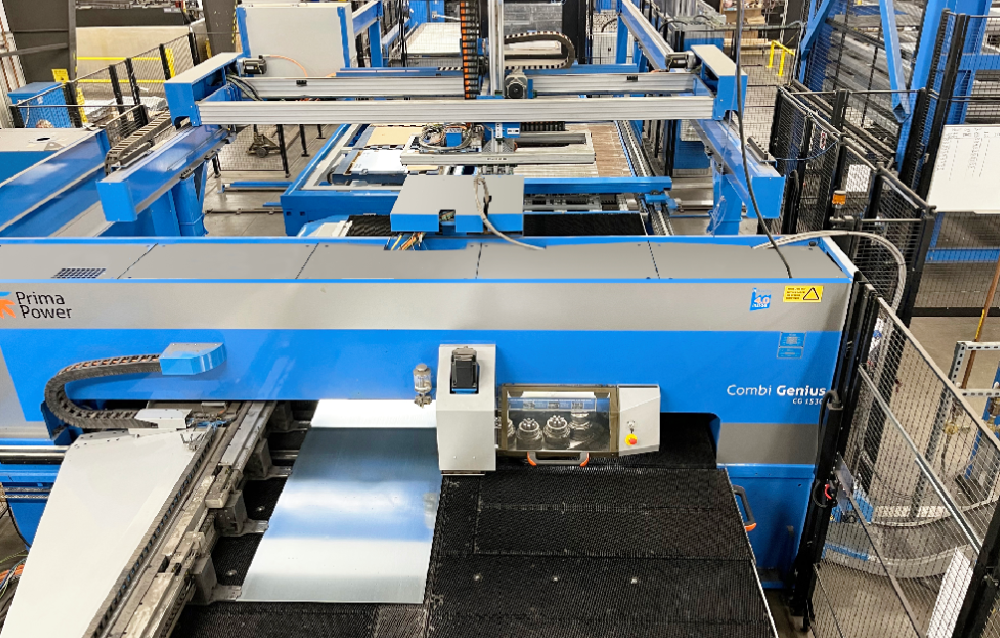
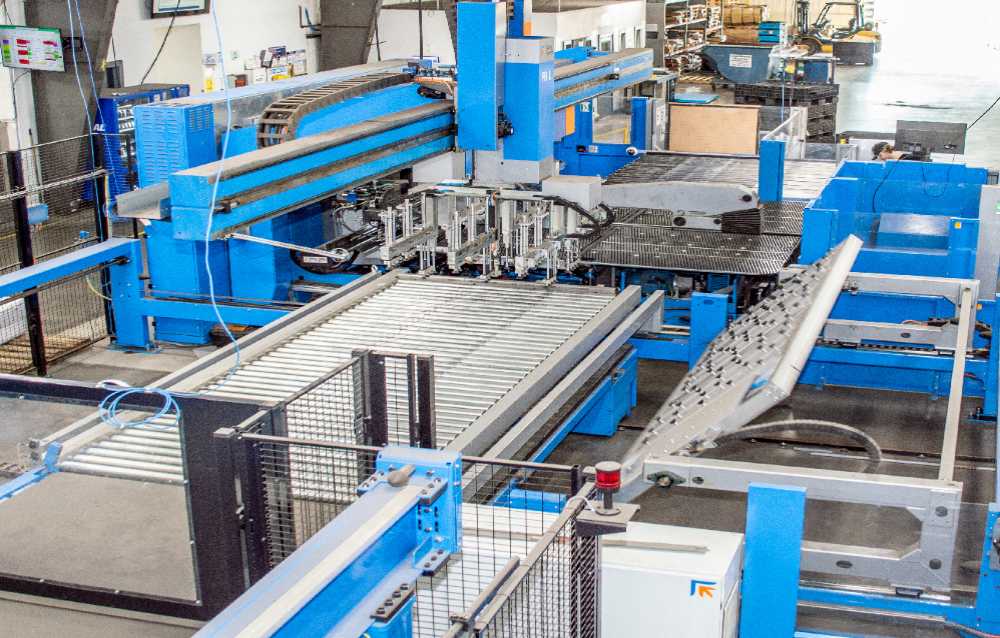
BOOSTING PROFITABILITY WITH PRIMA POWER’S LPBB AND COMBO TOWER
The low maintenance turret punch press uses numerically controlled, servo-electric axes for high-speed operations that are energy efficient. In addition to large tool capacity, the wide range of tools available supports easy, fast setups and changes. The Combi Genius combines punching with advanced fiber laser cutting to boost productivity, ensuring high speed and quality.
The Combo Tower supports the flexible manufacturing cell’s automated operation by serving as material and buffer storage for punched and laser-cut parts. Combo Tower storage can have one or two shelving units which can be adjusted to customer-specific needs.
“Profitability with the LPBB has been our number one benefit,” says Riemenschneider. “By adding one piece of equipment, we didn’t have to add another operator and we have five or six times the capacity compared to a standard press brake.”
With the LPBB, he says, “we can sell more parts and be on time. Our part rate on the press brake is 12 parts per hour. On the panel bender, we do 68 parts per hour.”
“The technology of the Prima Power package challenged us on how we will approach our fabrication solutions moving forward,” says Moryn. “Today, we’ve seen the remarkable progress we’ve made in upgrading our capabilities, and this will significantly enhance our thought process as we move forward to explore the possibilities of the next generation of equipment.”
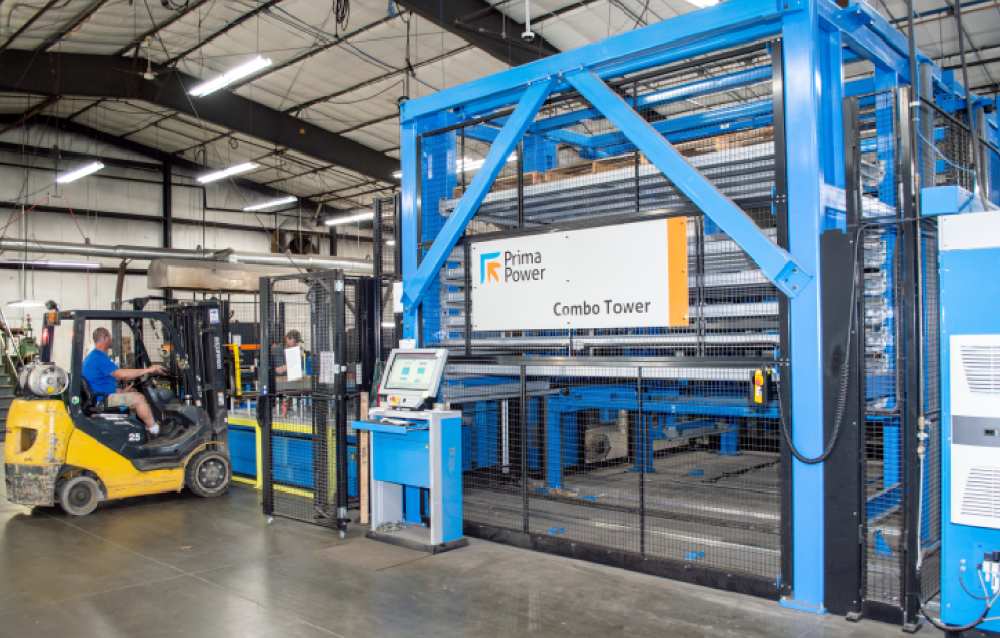
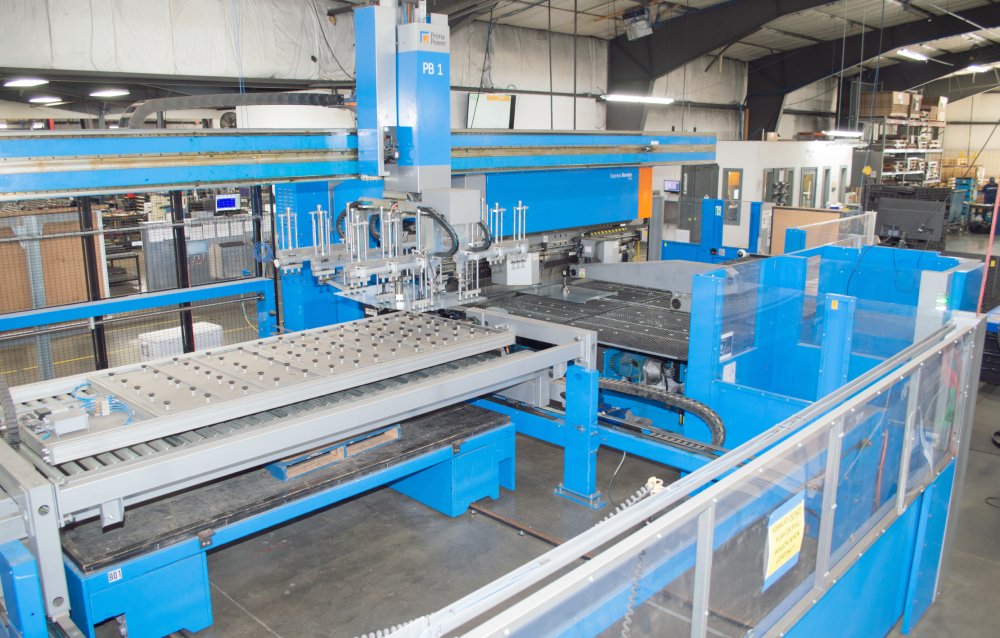
The automated EBe has eliminated much of the human error that occurred when bending was done with manual press brakes.
Are you looking for a similar solution for your company? Find it here
Комбинированный пробивной пресс с лазером Combi Genius
КОМБИНИРОВАННЫЕ ПРОБИВНЫЕ/ЛАЗЕРНЫЕ СТАНКИ
Штамповка + Лазерная Резка = Экономия производственных ресурсов
Линия LPBB
ГИБКИЕ ПРОИЗВОДСТВЕННЫЕ СИСТЕМЫ
Искусство интеграции
Панелегиб EBe
ПАНЕЛЕГИБЫ