
Gi.Metal, listo para un lote de productividad

Si la cocina italiana es una de las más famosas y renombradas del mundo, es sin duda gracias a los chefs que han exportado las recetas, pero quienes fabrican los utensilios de cocina también desempeñan un papel muy importante. Ese es el caso de Gi.Metal, especializada en la fabricación de equipamiento para pizzerías, que utiliza láseres de prima power en el proceso de corte.
La pizza se come ahora en todo el mundo. Donde hay una pizzería, hay un horno y donde hay un horno, hay (muy probablemente) una pala fabricada por Gi.Metal. Hoy en día, la empresa Montale de la provincia de Pistoia es un auténtico coloso en la producción de accesorios para la hostelería. Sin embargo, si repasamos su historia, no siempre fue así.
«La empresa fue fundada en 1986 por mi padre», afirma el actual director general, Marco D'Annibale. «Era una herrería que quería hacer algo completamente diferente. Por aquel entonces estaba terminando mis estudios, pero en cuanto terminé, en 1988, me incorporé a la empresa y empecé a trabajar en producción. En aquella época ya hacíamos unas cuantas palas para pizza, y cada fase se hacía manualmente: cortar, amolar y montar exactamente igual que se hacía hace 100 años. Con el tiempo, nos dimos cuenta de que estos productos se estaban convirtiendo poco a poco en nuestro negocio principal, así que decidimos especializarnos y esta ha sido la clave de nuestro éxito.»
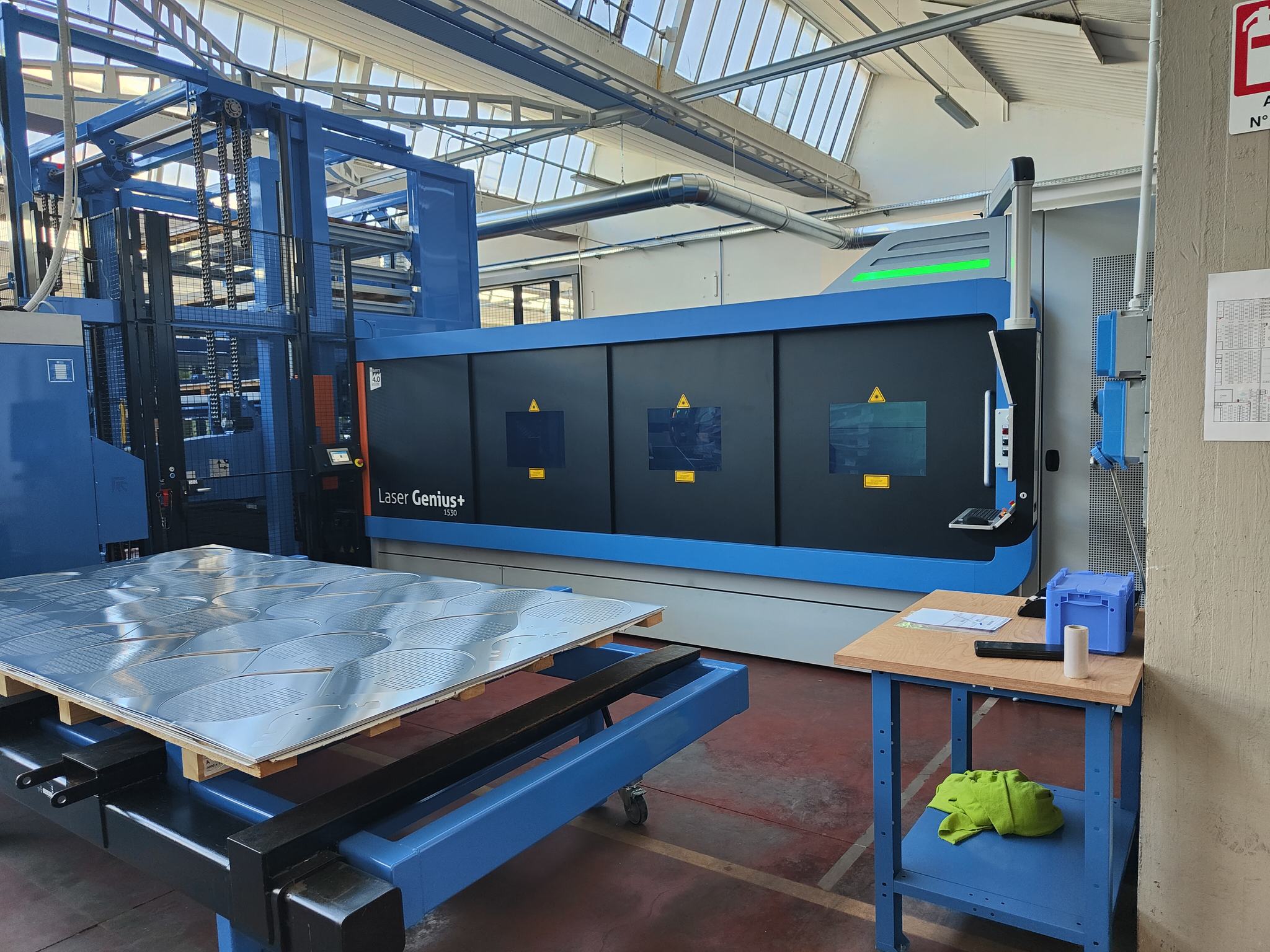
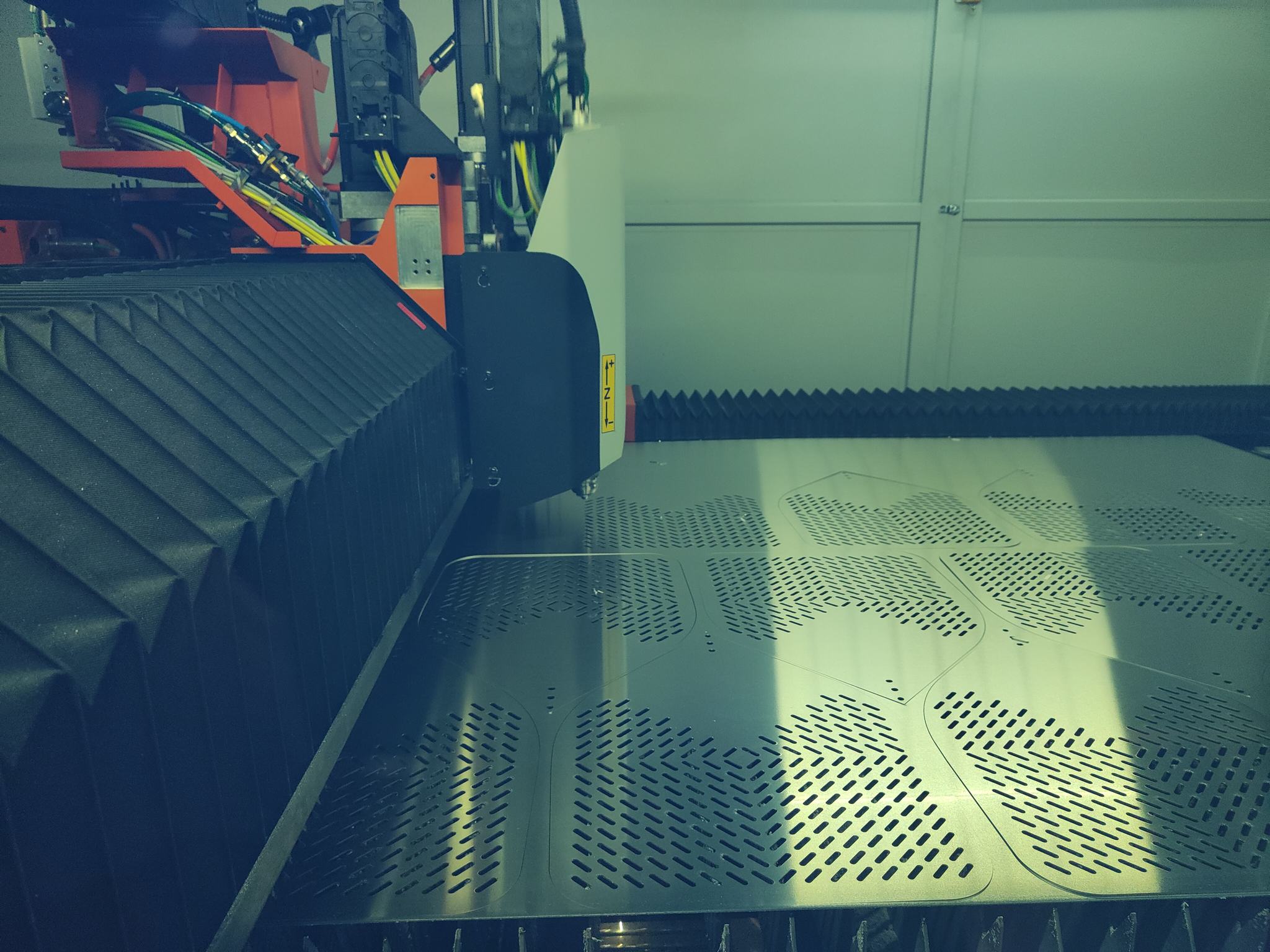
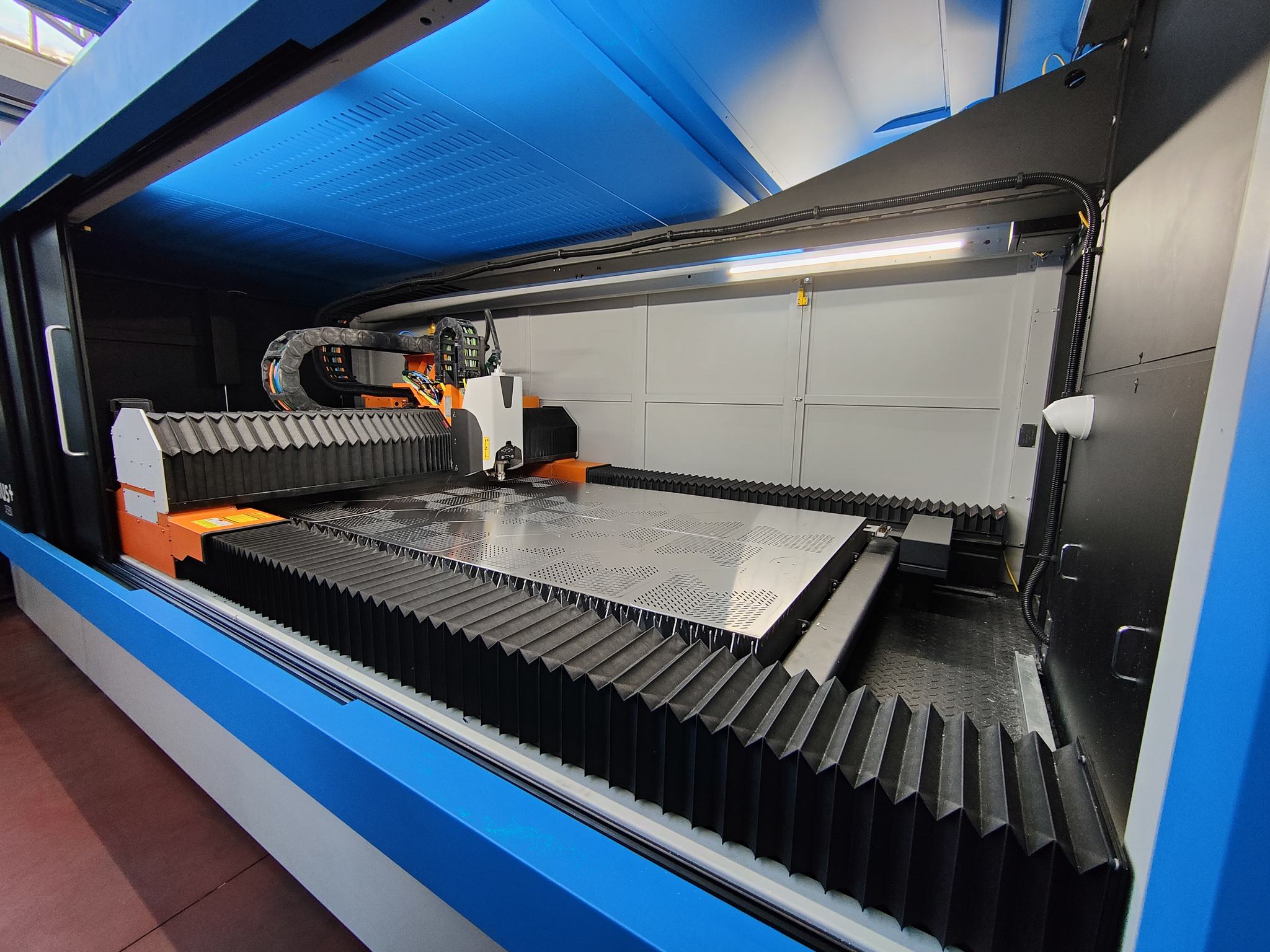
Se trata de una vocación artesanal y, aunque se ha adaptado y renovado para adecuarse a los tiempos modernos, no se ha visto comprometida a lo largo de los años; de hecho, a pesar de su importante estructura, la empresa siempre está atenta a las necesidades de sus clientes y no duda en fabricar ediciones limitadas o productos personalizados según los requisitos de los clientes.
«Las palas y el equipo para hacer pizzas exigen conocer al cliente y su cocina», dice D'Annibale. «En realidad, no existe una única forma de cocinar la pizza en todo el mundo y cada cliente tiene sus propios gustos y exigencias. Así, a medida que entramos en contacto con nuevas empresas, intentamos comprender sus preferencias y necesidades, lo que a menudo nos lleva al desarrollo de nuevos productos. La dificultad para nosotros ha sido combinar nuestra vocación artesanal con el espíritu industrial y, en este reto, la tecnología es de suma importancia, ya que debe permitir la productividad sin sacrificar la flexibilidad.»
En la actualidad, Gi.Metal ocupa 8 000 metros cuadrados de planta. Cuenta con un departamento de producción, un área de montaje y un centro logístico que gestiona la entrega de productos en todo el mundo, porque el 70 % de la producción se destina al extranjero, principalmente a Europa y América (donde Gi.Metal está presente tanto con una oficina en Chicago, la cuna estadounidense de la pizza americana, como en Brasil, en Curitiba). Todas las fases de trabajo de chapa se realizan internamente, empezando por el corte de la forma, para lo que la empresa utiliza la tecnología láser Prima Power 2D.
TECNOLOGÍAS MADE IN ITALY PARA EL ESTÁNDAR DE LA COCINA ITALIANA EN TODO EL MUNDO
Entrando en más detalles sobre el equipo para pizzas, D'Annibale explica:
«Nuestro cliente necesita principalmente tres artículos. En primer lugar, la pala de pizza, que debe tener al menos la superficie necesaria para colocar encima la masa laminada; suele ser de aluminio para garantizar su ligereza. A continuación, se necesita una pala más pequeña para girar la pizza en el horno. Este utensilio suele ser más pequeño, ya que se prefiere la agilidad y la manejabilidad: ya no son necesarias unas dimensiones más grandes, puesto que la pizza gana estructura a medida que se cocina y no se necesita un utensilio que sujete toda la pizza. Debe ser de acero para protegerlo de la mayor exposición al calor. El tercer utensilio es el cepillo para limpiar el horno.»
Gi.Metal ha internalizado por completo la parte de trabajo de chapa de estos productos. Una vez identificado el material, que es principalmente acero inoxidable 441 o acero preendurecido o incluso aluminio serie 6000 en espesores que van de 0,8 mm a 2,5 mm, se pasa a la fase de corte. Para ello, la empresa cuenta con una sólida colaboración con Prima Power, que comenzó hace más de 15 años con la adquisición de un láser de CO2, seguido de un modelo de fibra y se ha renovado recientemente con un flamante Laser Genius+ con automatización de carga/descarga y almacenamiento Combo Tower Laser.
Otros pasos de la producción implican el uso de tubos láser para mecanizar las asas, prensas plegadoras, fresadoras y prensas de moldeo para dar forma y producir las nervaduras de la pala y, por último, máquinas de satinado para el tratamiento de la superficie. Los únicos trabajos subcontratados a una red de empresas de confianza son la pintura y el anodizado, así como la producción de unos pocos componentes de plástico.
Además de las palas, el producto estrella de Gi.Metal, la empresa de Pistoia también fabrica accesorios para la preparación, el corte, el servicio y el transporte de la masa, así como una línea de carros para el sector de la restauración. En todos estos productos la chapa metálica desempeña un papel protagonista.
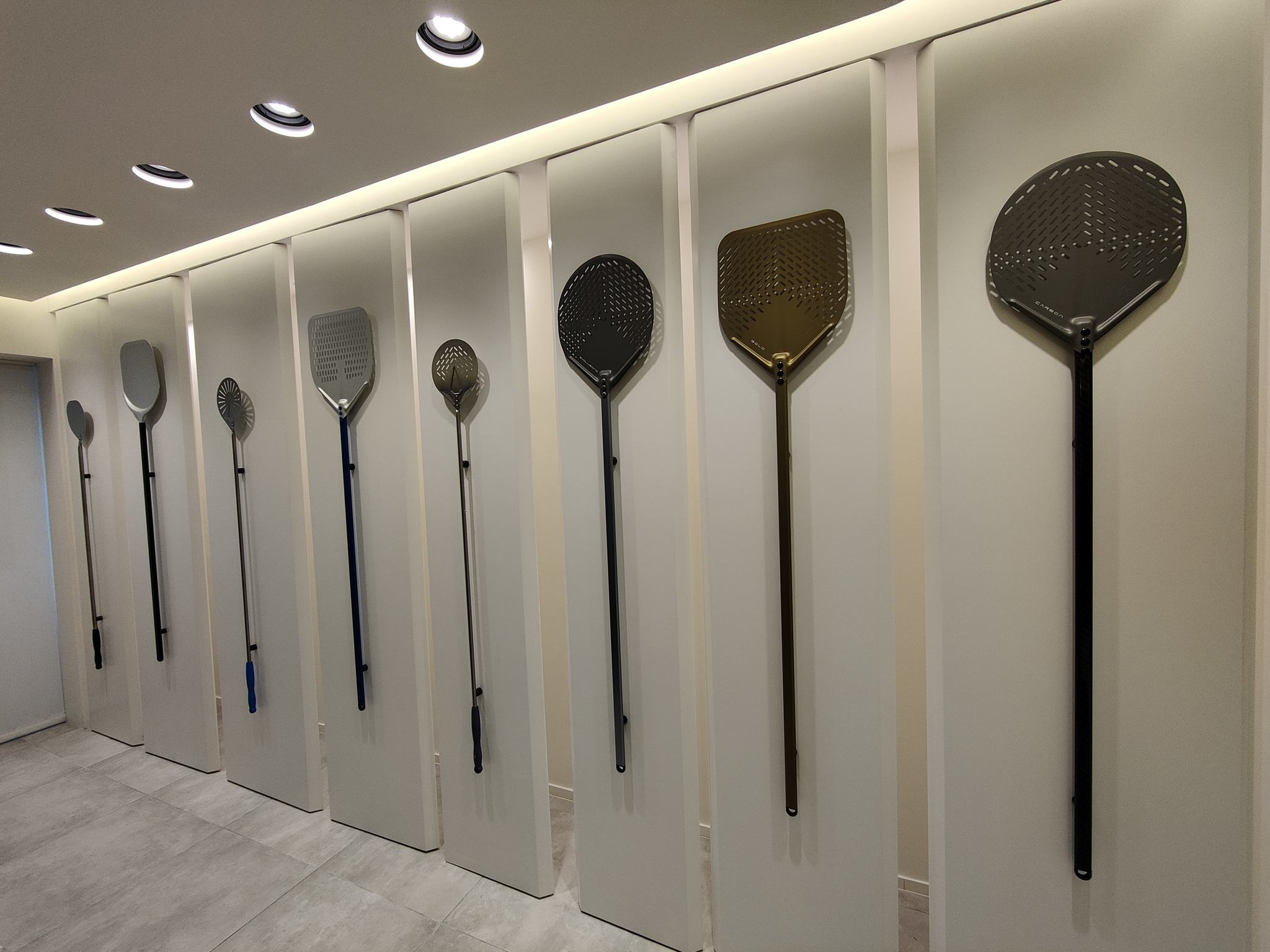
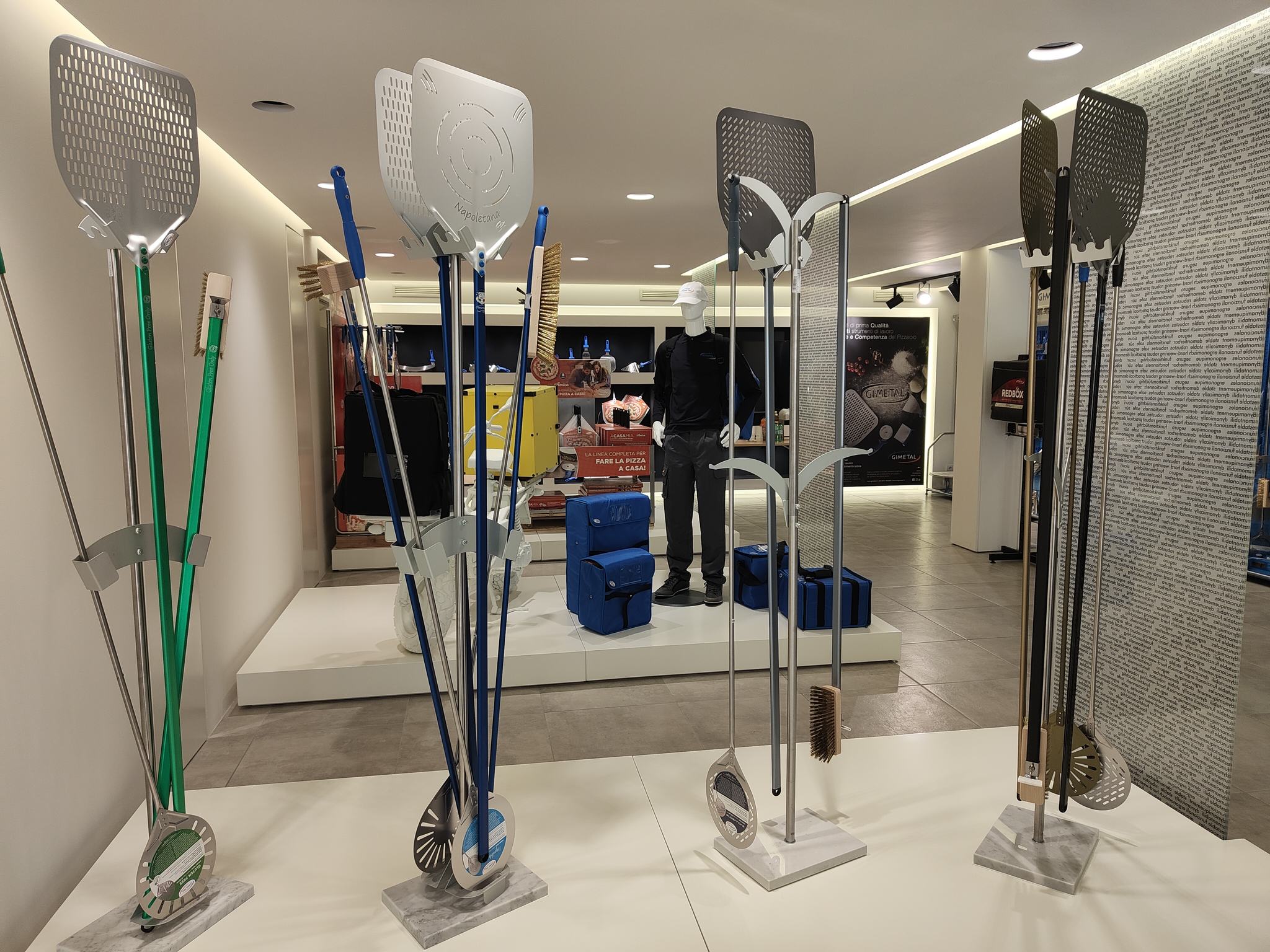
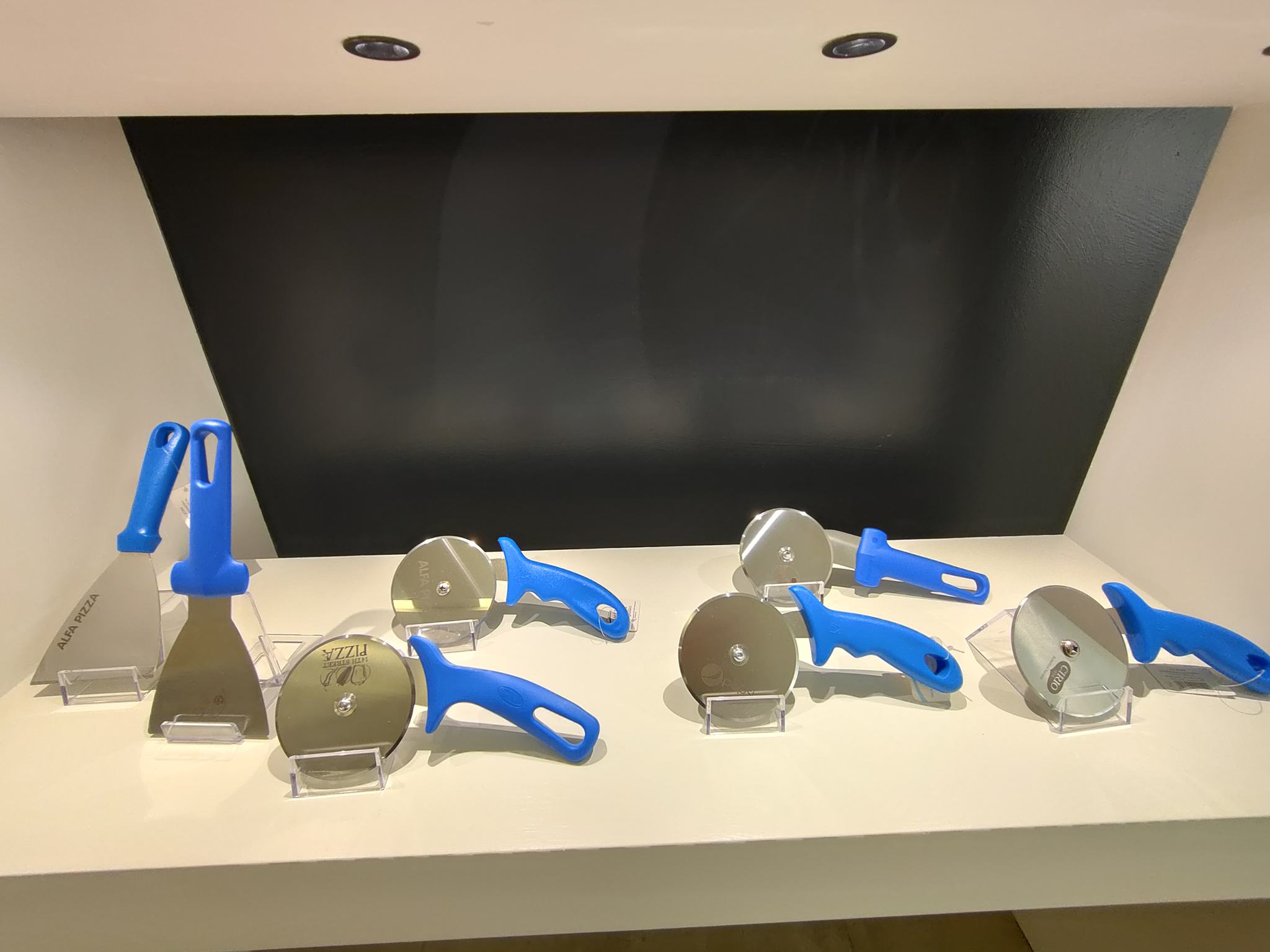
LA TECNOLOGÍA DETRÁS DE LA SENCILLEZ
A primera vista, no resulta evidente que, incluso detrás de artículos tan sencillos como las palas de pizza, hay importantes factores de diseño y fabricación que a menudo marcan la diferencia, y que requieren una planificación precisa y tecnología punta.
El CEO lo explica: «Las palas son principalmente redondas o rectangulares, estas últimas son más fáciles de usar, pero dependen mucho de los gustos del pizzero. La principal característica de nuestros productos es que algunos de ellos tienen agujeros para ayudar a eliminar el exceso de harina de la pala antes de colocar la pizza sobre ella. Si hay demasiada harina, el sabor de la pizza no será el mismo y habrá que limpiar el horno más a menudo. No todo el mundo es capaz de producir estos agujeros. El sistema Laser Genius+ ha sido de vital importancia para nosotros, ya que garantiza altos volúmenes de producción gracias a su dinámica, al tiempo que permite la creación de orificios limpios con bordes bien definidos, lo que evita la acumulación de harina."
Una de las ventajas de Laser Genius+ es su rendimiento en la realización de agujeros: durante las pruebas realizadas en el Tech Center de Collegno, se hicieron 11 agujeros en menos de 5 segundos.
Otro aspecto clave para permitir los altos volúmenes de producción requeridos es la automatización de la Laser Genius+. Gracias a la Combo Tower Laser, la máquina puede trabajar fácilmente sin personal, y los técnicos de Prima Power han efectuado una serie de adaptaciones y mejoras para mantener la calidad y el acabado estético de los productos semiacabados.
«Mecanizamos chapas extremadamente finas», afirma Riccardo Barneschi, director de planta de Gi.Metal, «y si una chapa se raya durante la manipulación, el anodizado no se adhiere eficazmente a la pala, por lo que la calidad se resiente. Esta era inicialmente una de nuestras preocupaciones a la hora de adoptar una solución con carga y descarga automatizadas, pero Prima Power pudo resolver la situación proponiendo cintas que permiten que la pieza se deslice gradualmente hacia el muelle de descarga sin fricción real, y también insertando una lámina entre los dos productos semiacabados si tienen partes afiladas.
Algo no menos importante y también relacionado con el sistema de automatización que completa la planta es la gestión de los residuos: la gestión de los residuos por parte del sistema Prima Power es automática y permite a Gi.Metal un ahorro cuantificado de 3-4 horas de trabajo a la semana al tiempo que permite la separación de los materiales en varios contenedores.»
«Estamos muy satisfechos de haber reconfirmado nuestra elección de Prima Power», afirma Barneschi. «Con el Laser Genius+ podemos cortar en 40 minutos lo que un láser de CO2 corta en dos horas y lo que un láser de fibra de la generación anterior tardaba en procesar algo más de una hora.»
Esta elección coherente no solo viene determinada por el rendimiento tecnológico, sino también por la flexibilidad y el enfoque de resolución de problemas característicos de la empresa turinesa, que han sido muy apreciados en Gi.Metal.
El director de la planta lo explica: «Aunque contamos con la tecnología Prima Power desde hace más de 15 años, también consultamos a otros fabricantes antes de adquirir nuestro último láser. La disponibilidad de los técnicos de Prima Power, que analizaron nuestro anidado y nuestros productos y nos ayudaron a optimizar nuestros programas de corte, por ejemplo, reduciendo los movimientos del cabezal al taladrar, resultó fundamental para aumentar la productividad y es uno de los factores que nos permitieron volver a confirmar nuestra confianza en el fabricante turinés. Una vez instalada la máquina, también pudimos apreciar la configuración plug&play de la Laser Genius+, que permitió realizar la instalación en un tiempo récord.»
TECNOLOGÍA 4.0 Y UN ENFOQUE EN EL PERSONAL DE LA "VIEJA ESCUELA"
Una producción tan eficiente, imbuida de una filosofía lean, no puede lograrse sin un mapeo y una gestión completos de los datos del proceso que cumplan plenamente los dictados de la Industria 4.0. Todas las máquinas de la empresa, empezando por los láseres Prima Power, están conectadas dentro del ecosistema empresarial para suministrar a los responsables la información oportuna y facilitarles tomar las mejores decisiones posibles. En el proceso no solo intervienen máquinas de última generación, con los láseres Prima Power a la cabeza, sino que también se han readaptado tecnologías más antiguas para permitir un mapeado completo de la zona de producción. A continuación, estos flujos de información se integran con las fases posteriores y anteriores, como la facturación, las compras y el almacenamiento, para proporcionar un cuadro de mando de gestión empresarial en tiempo real que puede utilizarse en cualquier lugar del mundo.
Con un enfoque tan moderno de la gestión de la maquinaria, Gi.Metal entiende claramente que el operario que está detrás de la máquina es igual de importante para la producción, como mejor resume el lema de la empresa «Hecho con pasión».
«En mi opinión, centrarse en las personas es clave», afirma D'Annibale, «porque no son máquinas, sino entidades mucho más complejas, cada una con sus propias fragilidades, ambiciones y esperanzas, por lo que la empatía es esencial. Si se tiene esto en cuenta, se puede crear un entorno favorable en la empresa donde los empleados se sientan protegidos; con esto me refiero no solo a proporcionarles una recompensa económica justa, sino también un buen bienestar en la empresa, recompensas y una formación que refleje sus ambiciones.»
SIEMPRE LISTOS PARA NUEVOS RETOS
Los planes de Gi.Metal para el futuro incluyen ir más allá del mundo pospandémico. La dirección viajaba por todo el mundo asistiendo a ferias y exposiciones junto con otras empresas del sector con el fin de llevar la idea de la cocina italiana al extranjero; esta costumbre ha tenido que pasar a un segundo plano en los últimos dos años, pero ello no ha frenado el volumen de negocio, que no ha dejado de aumentar.
«Asistíamos a más de 50 ferias comerciales antes de la pandemia», comenta D'Annibale, «y era una excelente oportunidad para conocer nuevas empresas de las que sacábamos importantes ideas para plasmarlas en nuevos productos. Ha sido duro para mí en los últimos años no poder subirme a tantos aviones como solía, pero espero que las cosas se reanuden bajo esta nueva normalidad y que siga descubriendo que siempre es posible crear algo nuevo, incluso en un mundo donde la gente piensa que ya está todo inventado, continuando con el avance de Gi.Metal tal y como es ahora: una industria moderna, pero que hace hincapié en la artesanía, a la vez que promueve la etiqueta Made in Italy en todo el mundo. La contribución de un socio como Prima Power, que también promueve la marca Made in Italy, será cada vez más fundamental en este sentido.»
PRECISIÓN Y PRODUCTIVIDAD MADE IN COLLEGNO
Velocidad, precisión y eficacia son las principales características de la Laser Genius+, la última incorporación a la gama de máquinas de Prima Power dedicadas al corte por láser en 2D. Se trata de una máquina láser de fibra extremadamente productiva y flexible que puede adaptarse a cualquier disposición del cliente sin comprometer la configuración. La Genius+ láser cuenta con una arquitectura de pórtico que garantiza altos niveles de estabilidad térmica, amortiguación de vibraciones y una gran dinámica, gracias también a unos motores y una transmisión compactos con mayor potencia por superficie ocupada y máxima eficiencia energética.
Laser Genius+ es una máquina plug&play diseñada para facilitar la instalación, permitiendo un funcionamiento inmediato y reduciendo el retorno de la inversión. El generador láser, los enfriadores, los motores y la óptica están integrados en la cabina y garantizan una instalación fácil y rápida: solo se tarda dos días desde la entrega hasta la producción en cualquier planta.
Para satisfacer las necesidades de producción de la más amplia gama de clientes, Laser Genius+ está disponible en tres tamaños: 1530 (con carreras de eje de 3 150 × 1 600 mm y una carga máxima mecanizable de 1 150 kg), 2040 (con carreras de eje de 4 320 × 2 200 mm y una carga máxima mecanizable de 2 100 kg) y 2060 (con carreras de eje de 6 320 × 2 200 mm y una carga máxima mecanizable de 3 050 kg). La velocidad de trayectoria máxima alcanzable en todas las versiones es de 180 m/min y pueden instalarse fuentes de fibra de 2 a 10 kW.
Para garantizar la máxima productividad, la Laser Genius+ puede suministrarse con todos los automatismos de la gama Prima Power: desde soluciones de carga y descarga hasta sistemas de clasificación y el sistema de producción flexible Night Train.
La disponibilidad de los técnicos de Prima Power, que analizaron nuestro nesting y nuestros productos y nos ayudaron a optimizar nuestros programas de corte, fue fundamental para aumentar la productividad y es uno de los factores que nos permitieron volver a confirmar nuestra confianza en el fabricante turinés.