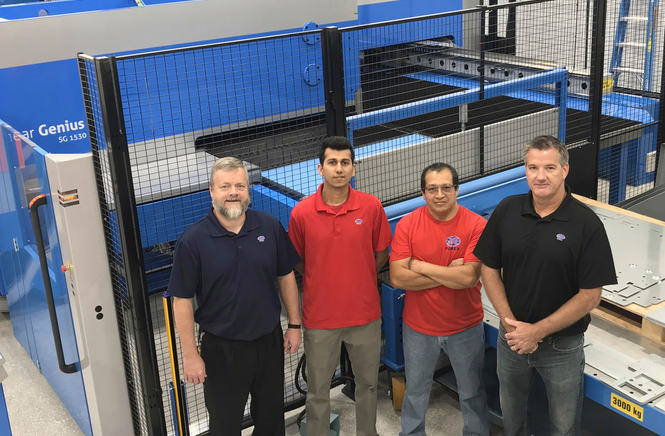
Pour JST Power Equipment, avoir les bonnes installations pour dire "oui" aux clients n'a pas de prix.
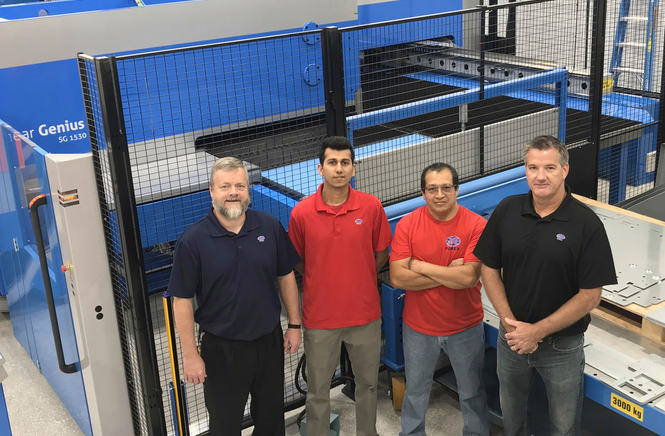
Les gammes d'appareillages électriques sont des produits conçus sur commande, avec beaucoup de variations entre les tâches, y compris les pièces en tôle fabriquées. Une machine automatisée combinée poinçonnage-cisaillage permet à la nouvelle usine de fabrication d'appareillages électriques de JST Power Equipment d'exceller dans la production de faibles volumes.
Traditionnellement fabricant de transformateurs, JST Power Equipment a passé les derniers mois à aménager un nouveau site de production à Lake Mary, en Floride, pour produire une nouvelle gamme de produits : les appareillages de commutation isolés à l'air. L'entreprise, initialement située dans le New Jersey et exploitant également des installations de production de transformateurs et d'appareillages de commutation au Mexique et en Chine, a cherché à rendre l'usine de Floride aussi verticalement intégrée que possible. Ce projet a été confié à Mark Smith, vice-président des opérations.
M. Smith a rejoint JST en juillet 2020 avec pour mission de concevoir un plan pour le démarrage initial de l'usine de Lake Mary. Il s'agissait notamment d'acheter des équipements de production de pointe.
"En 2020, je devais notamment décider de l'ampleur de l'expansion", se souvient M. Smith. "Dans le cadre de mes fonctions précédentes au sein d'autres entreprises, j'ai eu l'occasion de travailler avec des fabricants entièrement intégrés et avec une entreprise n'ayant absolument aucune intégration verticale.
"Aujourd'hui, notre usine de Floride est complètement intégrée verticalement, ce qui garantit la qualité des produits tout en réduisant les délais d'exécution", explique M. Smith. "Nos capacités en matière de tôlerie comprennent le poinçonnage, le cisaillage, le formage, le pliage et la peinture en poudre.
AU SOL : COMBINÉ POINÇONNEUSE-CISAILLE CNC ET PRESSE PLIEUSE ÉLECTRIQUE
M. Smith a commencé par effectuer des semaines de recherche et organiser plusieurs réunions avec des fabricants afin d'évaluer les capacités de l'équipement de production pour l'atelier d'usinage des tôles de l'usine - un nouvel ajout de 557 m2 au bâtiment existant de 5295 m2 que l'entreprise a acquis en 2019. Peu après, il a dirigé les efforts de l'équipe de direction de JST pour acheter une machine combinée poinçonneuse-cisaille servo-électrique (une Shear Genius de Prima Power) équipée d'une Combo Tower Prima Power pour le stockage des tôles. L'achat d'une presse plieuse servo-électrique modèle eP de Prima Power est également au programme.
"Avant de créer notre département de fabrication, nous externalisions les travaux de tôlerie à l'étranger", explique M. Smith. "À l'époque, le cycle de développement d'un nouveau produit sur le marché - aussi important que notre nouveau projet d'appareillage de commutation - durait de 5 à 8 ans."
"Dans ce cas, en tirant parti du nouveau département de fabrication", poursuit M. Smith, "nous avons pu lancer la nouvelle ligne de produits en seulement 14 mois. Les appareillages de commutation sont des produits fabriqués sur commande ; il y a beaucoup de variations d'une commande à l'autre, et ces variations ne concernent normalement qu'une poignée de composants en acier, ce qui n'intéresse pas beaucoup de sous-traitants. Il en va de même pour les travaux de prototypage rapide. Notre nouvel équipement d'usinage des tôles nous permet d'exceller dans la prise en charge des travaux de prototypage rapide et de faible volume par nos sous-traitants, de manière à ne pas perturber leurs activités".
LE COMBINÉ POINÇONNEUSE-CISAILLE PERMET DE TRAVAILLER RAPIDEMENT SUR DES TÔLES ENTIÈRES
Avec le concept Shear Genius, l'objectif est de fournir un équipement capable de transformer une tôle pleine en pièces finies. Ces pièces peuvent être déplacées vers les étapes finales de la production pour être immédiatement intégrées à l'assemblage final de l'appareillage de commutation.
Au cœur de la Shear Genius SGe : une poinçonneuse servo-électrique mise à jour de 30 tonnes avec une vitesse de course de 1000 frappes/min, une vitesse d'indexation de 250 tours/min et une vitesse de positionnement de la tôle de 150 m/min. La cisaille à angle droit est équipée d'un système d'actionnement servo-électrique, qui permet un mouvement de cisaille rapide et entièrement contrôlé par la CNC. La machine peut cisailler des tôles en acier doux jusqu'à 4 mm d'épaisseur, en aluminium jusqu'à 5 mm et en acier inoxydable jusqu'à 3 mm. Le chargement automatique a été intégré, de même que le retrait et le tri automatiques et programmables des pièces.
"Nous apprécions également la possibilité de transférer les fichiers CAO SolidWorks directement à la machine", ajoute M. Smith, "et de ne pas avoir à programmer toujours hors ligne. Cela améliore considérablement notre flexibilité et nous permet de nous libérer des contraintes. Nous pouvons bien sûr programmer la machine hors ligne pour l'imbrication et l'optimisation de l'utilisation des tôles, mais nous n'y sommes pas obligés. Si nous avons besoin d'une pièce immédiatement, nous pouvons envoyer le dessin SolidWorks à la machine et fabriquer la pièce. Cela nous plaît beaucoup. La rapidité de mise sur le marché et la capacité à dire "oui" à nos clients n'ont pas de prix. C'est la raison pour laquelle nous avons investi dans la machine combinée plutôt que d'acheter des machines séparées. De nombreux fabricants disent "non" lorsque leur client a besoin de quelque chose de spécial. Nous voulons dire 'oui' à nos clients, quels que soient leurs besoins.
Le SGe élimine les squelettes inutiles et les opérations secondaires coûteuses telles que l'ébavurage. Les bords grignotés sur l'extérieur des pièces sont éliminés grâce à l'utilisation de la cisaille à angle droit intégrée. Les tôles entières - 4 x 8 ou 5 x 10 pieds - sont extraites automatiquement de la tour de stockage, chargées et équerrées dans la machine, sans intervention humaine, ce qui garantit la précision. De plus, les pinces qui maintiennent la tôle pour le poinçonnage la maintiennent également pour le cisaillement.
L'automatisation du chargement, du poinçonnage, du formage et de la mise en forme sur la combinaison poinçonnage-cisaille, ainsi que du déchargement, du tri et de l'empilage, permet d'obtenir des pièces finies avec peu ou pas de chutes, un minimum de travail manuel et une productivité optimale.
"Une autre caractéristique très intéressante est la capacité de formage vers le haut, pour réaliser des persiennes et d'autres éléments", ajoute l'opérateur de la machine, Milton Fuentes. "Nous disposons d'un outillage spécialisé pour ces opérations.
"Essentiellement, explique M. Smith, la Shear Genius permet au processus automatisé de commencer avec une tôle entière et de terminer avec une pièce finie après le chargement, le poinçonnage, le formage, le cisaillage et le déchargement automatisés, le tout en une seule opération".
"Nous n'avons pas besoin de bouger les pièces ou de nous occuper d'un squelette, ce qui est un énorme avantage pour moi", déclare Fuentes. "L'encombrement est également très réduit, ce qui était très important pour nous.
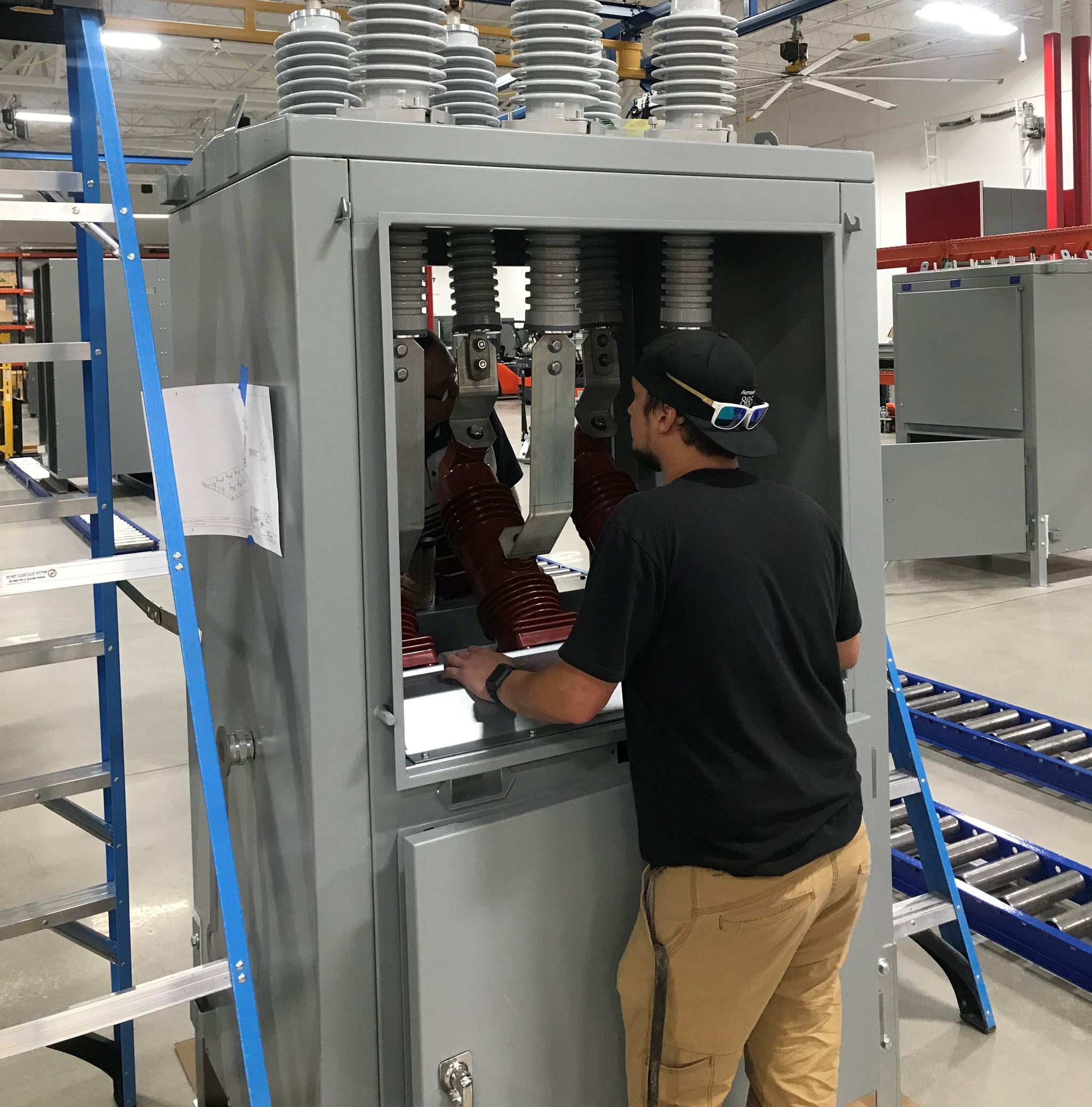
DES PARFAITS COMPLÉMENTS : COMBO TOWER, PRESSE-PLIEUSE SERVO-ÉLECTRIQUE
La Combo Tower à 10 niveaux permet à JST de stocker plusieurs épaisseurs d'acier galvanisé laminé à froid, d'acier inoxydable et d'aluminium.
"C'est un gain de place considérable et un outil idéal pour le suivi des matériaux. Il a été amorti très rapidement", précise M. Smith. Dans l'ensemble, le SGe et la Combo Tower "ont considérablement réduit notre délai de mise sur le marché", poursuit M. Smith. "Nous pouvons désormais passer du concept au prototype en quelques heures, alors que les délais de livraison de nos fournisseurs pendant Covid étaient de 6 à 8 semaines. Le fait de disposer de cette capacité interne nous a permis de respecter un certain nombre de délais.
Parallèlement, en aval de la combinée poinçonneuse-cisaille automatisée, pratiquement toutes les pièces fabriquées par la cellule hautement productive sont acheminées vers la presse plieuse Prima Power eP-series. Smith attribue à la presse plieuse la capacité de suivre le flux constant de pièces, grâce aux temps d'accélération et de décélération élevés et aux temps de réponse rapides de son système d'entraînement servo-électrique.
"Par rapport aux presses plieuses hydrauliques conventionnelles auxquelles je suis habitué", explique M. Smith, "la rapidité d'installation, la vitesse de fonctionnement et la qualité de la presse plieuse électrique se traduisent par une productivité considérablement accrue et des temps de cycle réduits".
La presse plieuse, un modèle eP 1336, comporte des évolutions de la jauge arrière de Prima Power qui, selon la société, optimisent la rigidité du système, notamment un cadre en acier (plutôt qu'en aluminium), un guide linéaire à double trempe pour l'axe Z et un double guide sur l'axe X. Smith a choisi d'inclure le suiveur de pliage en option avec la presse pour éviter d'avoir à recourir à un opérateur supplémentaire lors du pliage de pièces plus grandes et pour garantir la précision de l'angle de pliage. Smith a choisi d'inclure le suiveur de pliage optionnel avec le frein pour éviter d'avoir recours à un opérateur supplémentaire lors du pliage de pièces plus grandes et pour garantir la précision de l'angle de pliage.
Caractéristiques techniques : 130 tonnes de force de pliage, longueur du plateau de 144 pouces avec 155 pouces entre les châssis latéraux. La précision et la régularité de l'angle de pliage sont optimisées grâce au système poulie-courroie qui entraîne la presse plieuse, actionné par des servomoteurs et répartissant la force de pliage sur toute la longueur de pliage. Le système se compose de rouleaux fixes et mobiles répartis sur la longueur totale de la poutre supérieure. Les servomoteurs offrent un contrôle et une précision supérieurs des mouvements. De plus, Smith a choisi d'ajouter l'option de CNC crowning pour compenser la déflexion du châssis inférieur pendant le pliage.
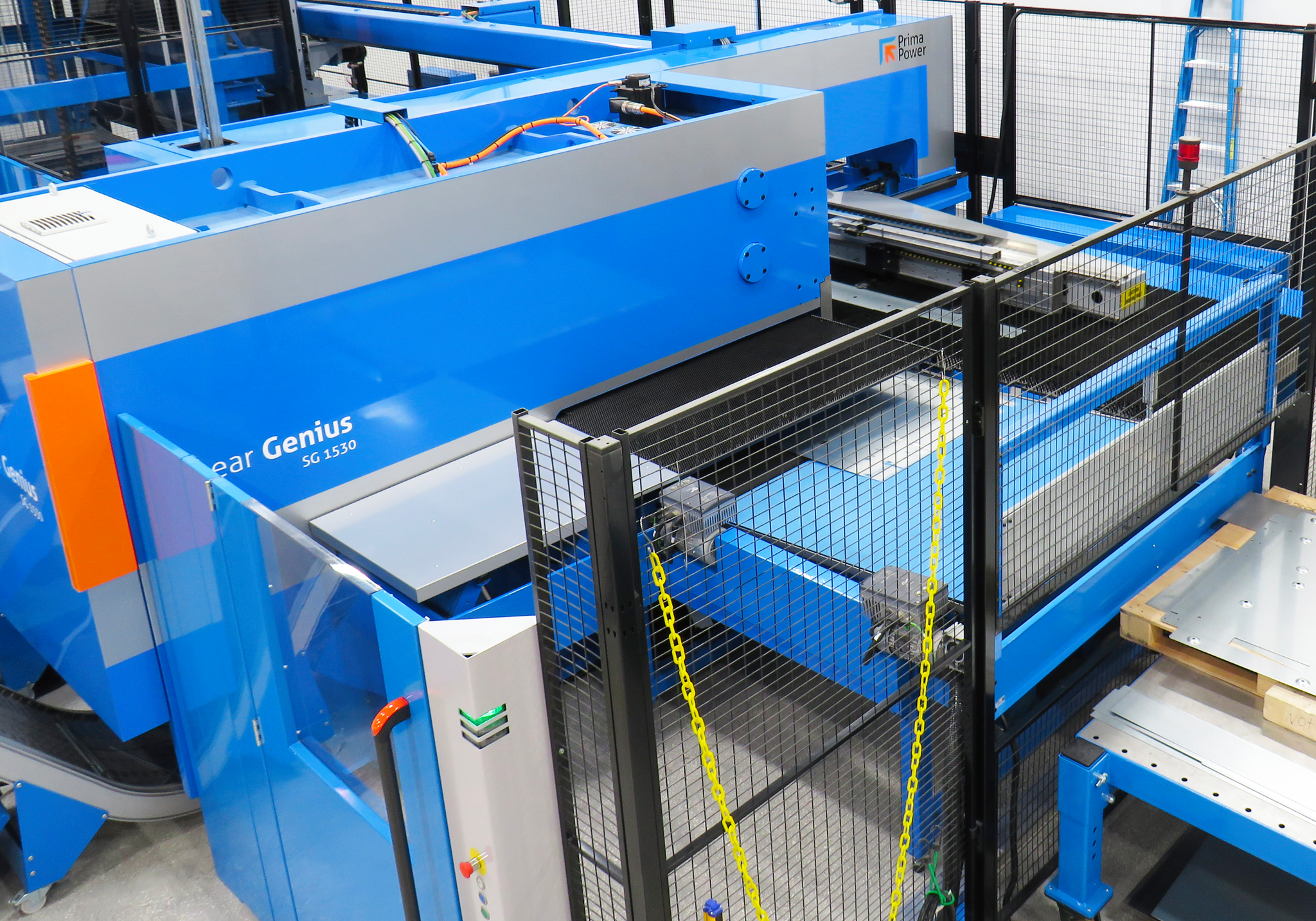
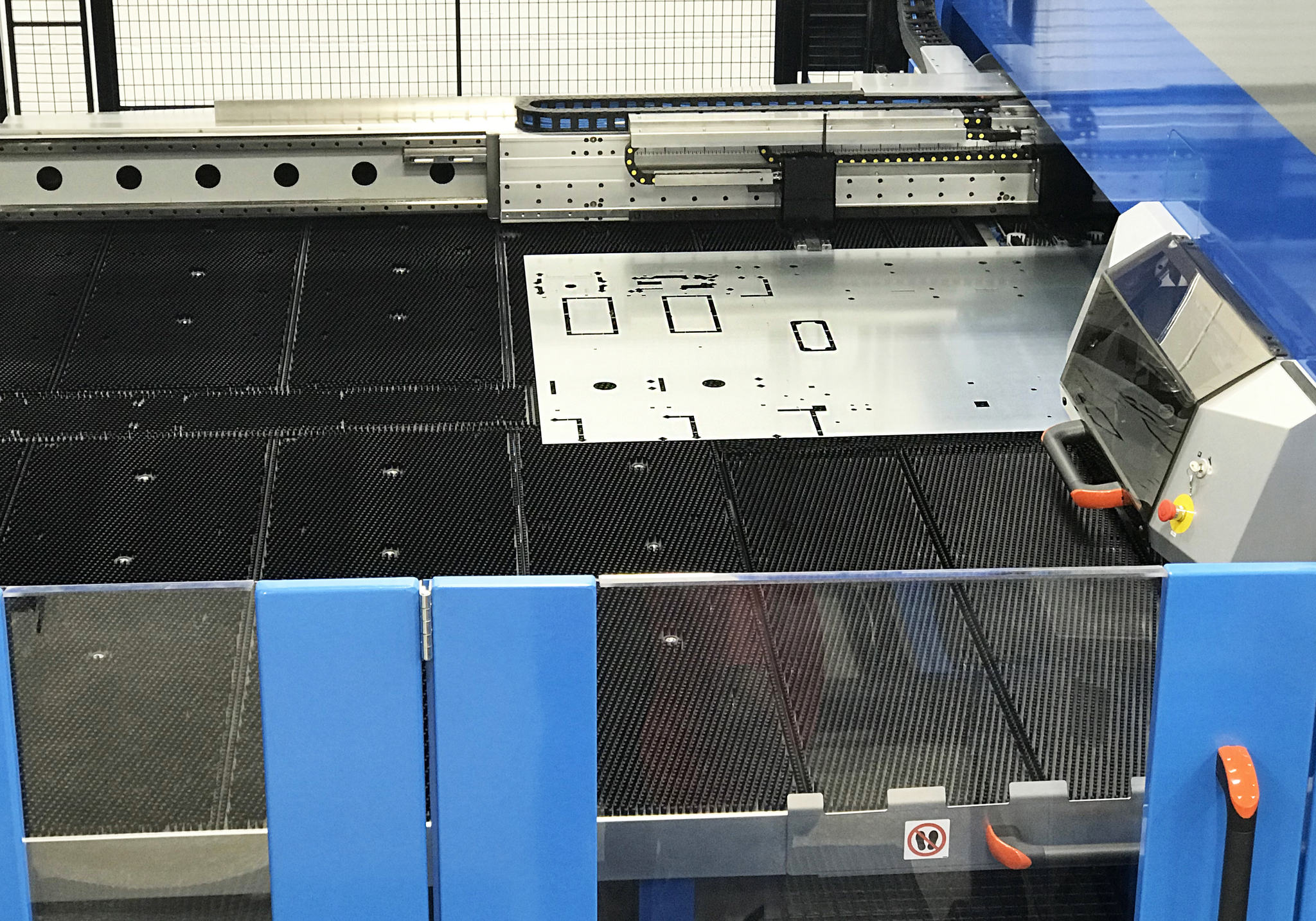
Les presses plieuses Prima Power de la série eP sont également dotées d'un cadre en O rigide qui garantit l'alignement de l'outil, même en cas de déformation, car il n'y a pas de déplacement horizontal. La position de la poutre supérieure, par rapport à la poutre inférieure, est mesurée par deux encodeurs linéaires Y1 et Y2 fixés indépendamment du bâti de la machine, et qui sont référencés par rapport au banc. Cette conception, selon Prima Power, isole la précision du positionnement du vérin de toute déflexion des châssis latéraux sous charge et maintient un positionnement précis même pendant les opérations de pliage décentré. Répétabilité du vérin : ±0,005 mm.
"Nous sommes en mesure de combiner de petites matrices segmentées de 100 ou 200 mm pour obtenir des longueurs personnalisées, plutôt que de manipuler des matrices plus grandes", explique M. Smith, "ce qui réduit considérablement le temps d'installation par rapport à la nécessité de retirer complètement une grande section de matrice et de la remplacer par une autre matrice pour s'adapter à une nouvelle configuration. De plus, nous obtenons une qualité de première pièce, aucune pièce mise au rebut à chaque réglage. J'ai l'habitude de jeter la première pièce à chaque réglage".
"Notre nouvel équipement d'usinage de tôles nous permet de gérer les faibles volumes de production, les pièces uniques et toutes les modifications techniques tardives propres à l'industrie des appareillages de commutation", conclut M. Smith. "Nous avons conçu notre atelier de fabrication pour gérer la partie de notre activité relative au prototypage sur mesure et à la demande rapide. Chaque pièce que nous fabriquons est personnalisée. Nous savions dès le départ que nous ne recherchions pas un taux d'utilisation élevé ni un retour sur investissement rapide. Nous voulions des performances."
Dans l'ensemble, le SGe et la Combo Tower ont considérablement réduit notre délai de mise sur le marché. Le fait de disposer de cette capacité interne nous a permis de respecter un certain nombre de délais.