
JST Power Equipment, die richtige Ausrüstung zu haben, um jedes Mal „Ja“ zu Kunden zu sagen, ist unbezahlbar

Als traditioneller Hersteller von Transformatoren, hat JST Power equipment kürzlich einen neuen Produktionsstandort in Lake Mary, Florida, in Betrieb genommen, um eine neue Produktlinie zu produzieren: luftisolierte Schaltanlagen. Eine Herausforderung, die dank einer automatisierten Stanz-scherenkombinationsmaschine erfolgreich bewältigt wurde.
JST Power Equipment, ursprünglich in New Jersey ansässig und mit Betriebsstätten in Mexiko und China, wollte das Werk in Florida so vertikal wie möglich integrieren. Dieses Projekt landete direkt in den Händen von Mark Smith, Vice President of Operations.
„Ein Teil meines Aufgabenbereichs im Jahr 2020 bestand darin, zu entscheiden, wie groß die Erweiterung sein musste“, erinnert sich Smith. „Heute ist unser Werk in Florida vollständig vertikal integriert, wodurch die Produktqualität gewährleistet und gleichzeitig die Vorlaufzeiten verkürzt werden. Unsere Blechbearbeitungskapazitäten umfassen Stanzen, Scheren, Formen, Biegen und Pulverbeschichten.“
„Unsere neue Ausrüstung für die Blechbearbeitung ermöglicht es uns, unseren Sub‑Lieferanten die Kleinserien- und Rapid-Prototyping-Arbeit abzunehmen, damit wir ihren Betrieb nicht stören.“
AUF DEM BODEN: CNC STANZ-SCHNEID-KOMBINATION UND ELEKTRISCHE ABKANTPRESSE
Smith begann mit wochenlangen Recherchen und veranstaltete mehrere Termine mit Ausrüstungsherstellern für die Blechfertigungshalle des Werks - ein neuer 550 m² großer Anbau an die bestehenden, im Jahr 2019 erworbenen, 5.300 m². Kurz darauf leitete er die Arbeiten des JST-Managementteams, um den Kauf einer Shear Genius von Prima Power, die mit einem Prima Power Combo Tower für die Lagerung von Blechen ausgestattet war. Ebenfalls auf der Liste: eine servoelektrische Abkantpresse vom Typ Prima Power eP.
„Vor dem Aufbau unserer Fertigungsabteilung, haben wir die Blechbearbeitung ins Ausland verlagert“, sagt Smith. „Damals dauerte der Entwicklungszyklus bis zur Markteinführung eines neuen Produkts - so bedeutend wie unser neues Schaltanlagenprojekt - 5 bis 8 Jahre.“
„In diesem Fall konnten wir durch die Nutzung der neuen Fertigungsabteilung“, so Smith weiter, „die neue Produktlinie in nur 14 Monaten auf den Markt bringen. Bei Schaltanlagen handelt es sich um kundenspezifissche Produkte, die von Auftrag zu Auftrag stark variieren, und diese Variationen betreffen in der Regel nur eine Handvoll stahlgefertigter Komponenten, was für viele Auftragsfertiger nicht von Interesse ist. Das Gleiche gilt für Rapid-Prototyping- Arbeiten. Unsere neue Ausrüstung für die Blechbearbeitung ermöglicht es uns, unseren Sub‑Lieferanten die Kleinserien- und Rapid-Prototyping-Arbeit abzunehmen, damit wir ihren Betrieb nicht stören.“
Das Shear-Genius-Konzept zielt darauf ab, eine Anlage bereitzustellen, die in der Lage ist, ein vollflächiges Blech in Fertigteile umzuwandeln. Diese Teile können in die letzten Produktionsstufen gebracht und direkt in die Endmontage der Schaltanlage integriert werden. Das Herzstück der Shear Genius SGe ist eine aktualisierte servoelektrische 30-Tonnen-Stanzmaschine mit 1000 Hüben/min, einer Drehzahl von 250 U/min und einer Blechpositioniergeschwindigkeit von 150 m/min. Die rechtwinklige Schere verfügt über ein servoelektrisches Antriebssystem, das eine schnelle, vollständig CNC-gesteuerte Scherenbewegung ermöglicht. Die Maschine kann Weichstahlbleche bis zu einer Stärke von 4 mm, Aluminium bis zu 5 mm und Edelstahl bis zu 3 mm zuschneiden. Eine automatische Beladung wurde ebenso integriert wie eine programmierbare und automatische Teileentnahme und-sortierung.
„Wir schätzen auch die Möglichkeit, SolidWorks CAD-Dateien direkt in die Maschine zu übernehmen“, fügt Smith hinzu, „und müssen nicht immer offline programmieren. Dies verbessert unsere Flexibilität erheblich und hilft uns, aus Engpässen herauszukommen. Wir können die Maschine natürlich auch offline programmieren - für Verschachtelungen und zur Optimierung der Blechausnutzung - aber wir müssen es nicht. Wenn wir ein Teil sofort benötigen, können wir die SolidWorks-Zeichnung mit zur Maschine nehmen und das Teil herstellen. Das gefällt uns sehr. Die schnelle Markteinführung und die Fähigkeit unseren Kunden auch dann „Ja“ zu sagen, wenn sie etwas Besonderes brauchen, sind unbezahlbar. Deshalb haben wir in die Kombinationsmaschine investiert, anstatt einzelne Maschinen zu kaufen.“
Da das Beladen, Stanzen, Formen und Umformen auf der Stanz-Schneid-Kombination automatisiert wird, ebenso wie das Entladen, Sortieren und Stapeln, entstehen fertige Teile mit wenig bis gar keinem Ausschuss, minimaler manueller Arbeit und optimaler Produktivität. „Ein wirklich schönes Merkmal ist die Möglichkeit des Umformens, um Lamellen und andere Merkmale zu formen“, fügt Maschinenbediener Milton Fuentes hinzu.
„Wir haben Spezialwerkzeuge für diese Arbeiten. Ein weiteres großes Pluspunkt für mich ist, dass wir die Teile nicht ausschütteln oder mit einem Gerüst auseinander setzen müssen.“
„Wir schätzen auch die Möglichkeit, SolidWorks CADDateien direkt in die Maschine zu übernehmen und müssen nicht immer offline programmieren.“
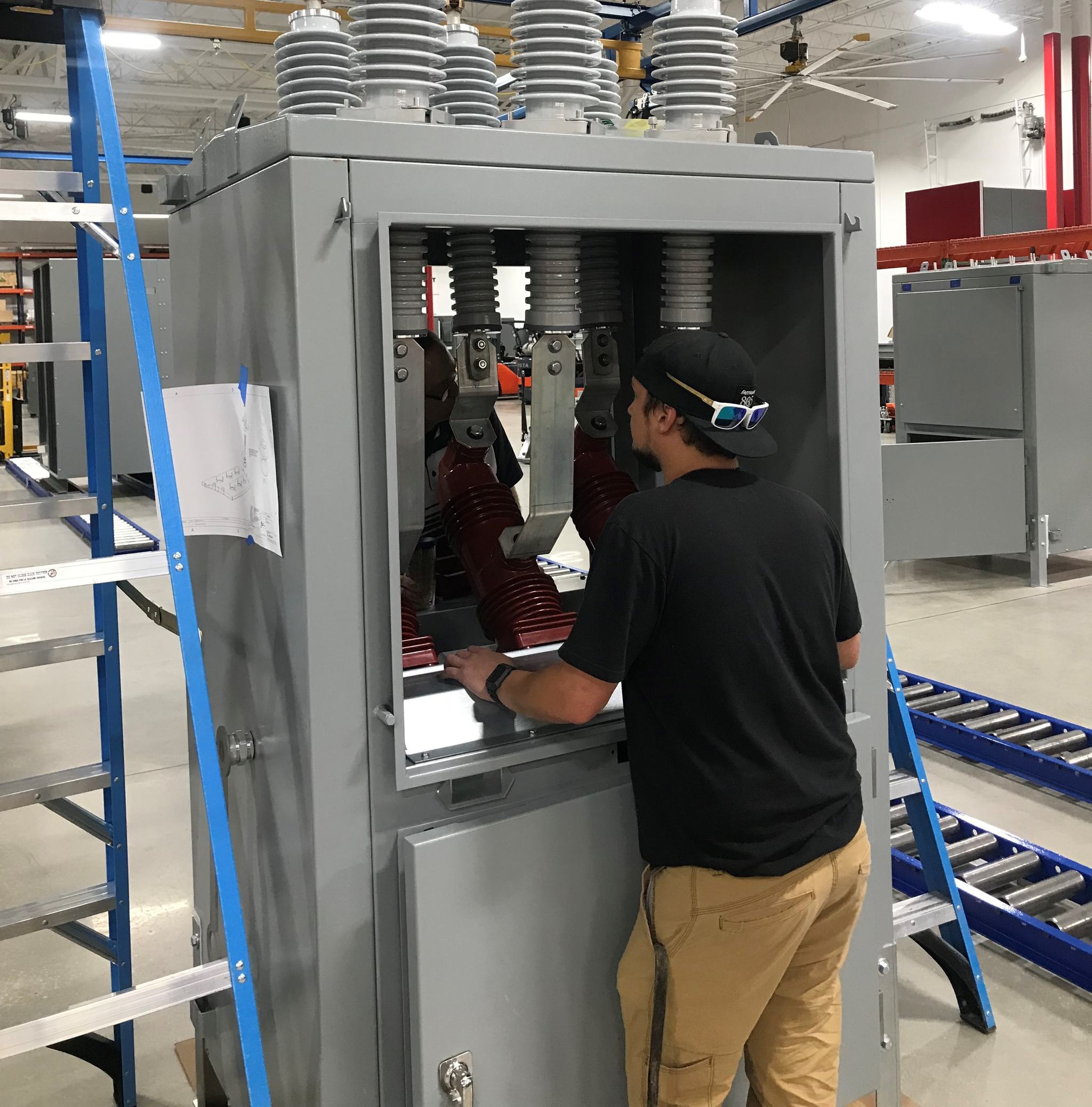
PERFEKTE ERGÄNZUNGEN: COMBO TOWER, SERVO-ELEKTRISCHE ABKANTPRESSE
Der Combo Tower mit 10 Stationen ermöglicht es JST, verschiedene Stärken aus verzinktem, kaltgewalztem Stahl, Edelstahl und Aluminium zu lagern.
„Es ist eine große Platzersparnis und ideal für die Materialverfolgung. Er hat sich sehr schnell bezahlt gemacht“, sagt Smith. Insgesamt haben das SGe und der Combo Tower „unsere Vorlaufzeit bis zur Markteinführung drastisch verkürzt“, so Smith weiter. „Aufgrund dieser internen Kapazität konnten wir eine Reihe von Terminen einhalten.“
Im Anschluss an die automatisierte Stanz-Scher-Maschine wird praktisch jedes Teil, das die hochproduktive Zelle herstellt, an die Abkantpresse eP 1336 der Prima Power eP-Serie weitergeleitet. Smith schreibt der Abkantpresse zu, dass sie - dank der hohen Beschleunigung, Verzögerung und schnellen Reaktionszeiten ihres servoelektrischen Antriebssystems - mit dem konstanten Teilefluss Schritt halten kann.
„Im Vergleich zu den konventionellen hydraulischen Abkantpressen, an die ich gewöhnt bin“, sagt Smith, „führen die schnelle Einrichtung, die Betriebsgeschwindigkeit und die Qualität der elektrischen Abkantpresse zu einer erheblich höheren Produktivität bei kürzeren Zykluszeiten.“
Die Abkantpresse, ein eP 1336-Modell, verfügt über Hinteranschlag-Aufrüstungen zur Optimierung der Systemsteifigkeit, einschließlich eines Stahlrahmens (anstelle von Aluminium), einer doppelt gehärteten Linearführung für die Z-Achse und einer Doppelführung an der X-Achse.
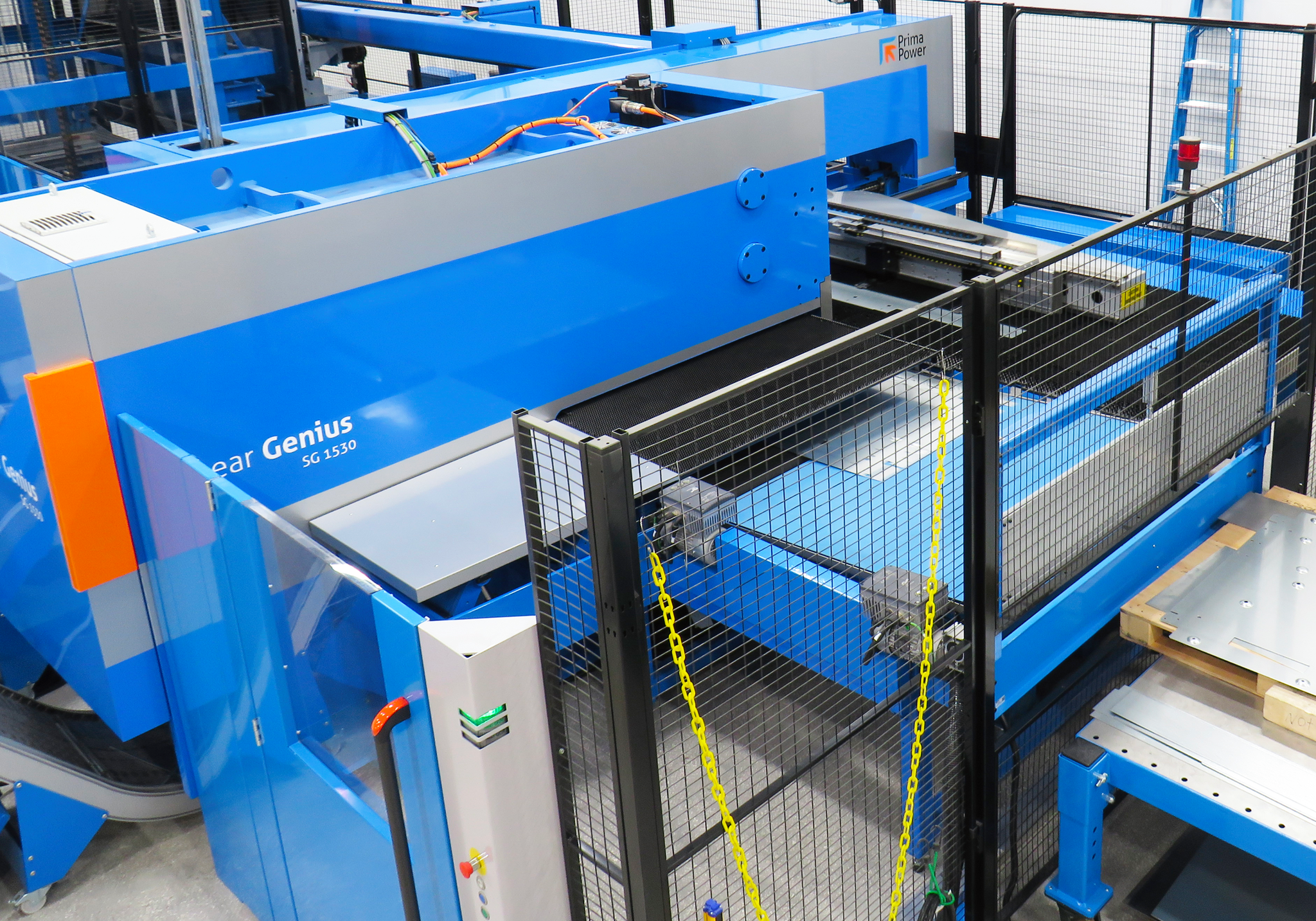
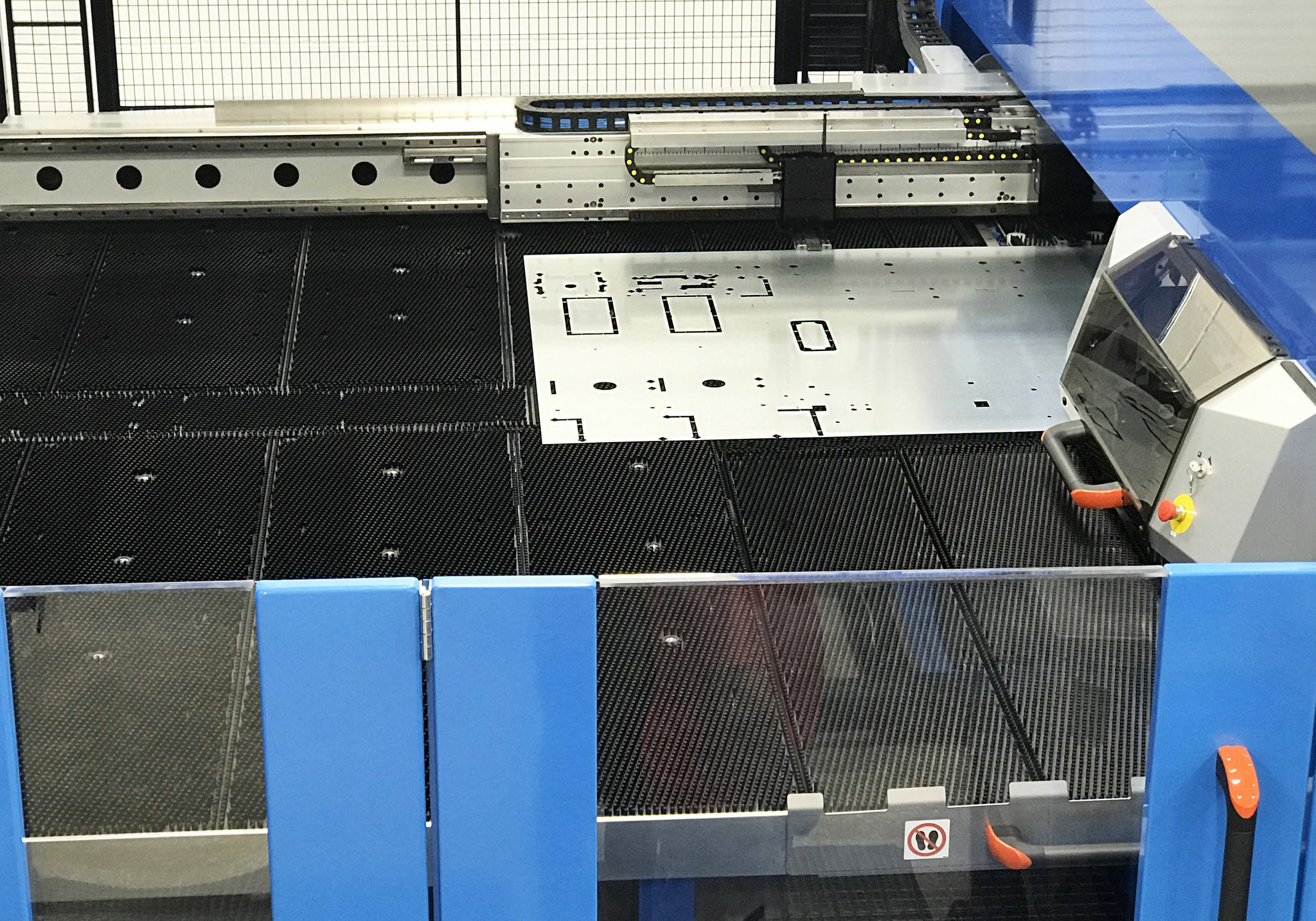
„Unsere neuen Blechbearbeitungsanlagen ermöglichen uns die Kleinserienproduktion, die einteiligen Teile und alle späten technischen Änderungen zu bewältigen, die in der Schaltanlagenbranche üblich sind“, so Smith abschließend.
Insgesamt haben das SGe und der Combo Tower unsere Vorlaufzeit bis zur Markteinführung drastisch verkürzt. Dank dieser internen Kapazitäten konnten wir eine Reihe von Terminen einhalten.