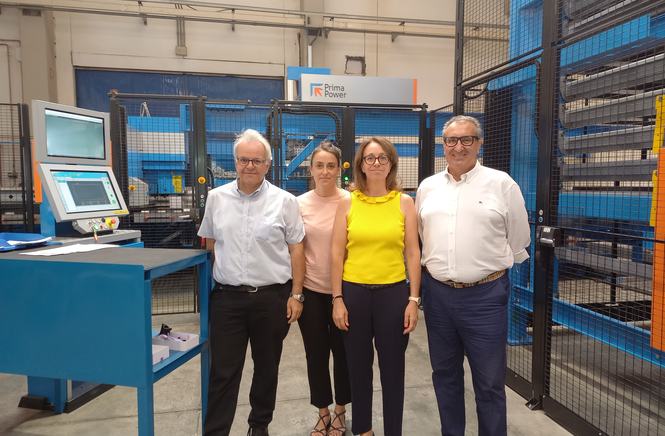
DAV, innovateurs par tradition
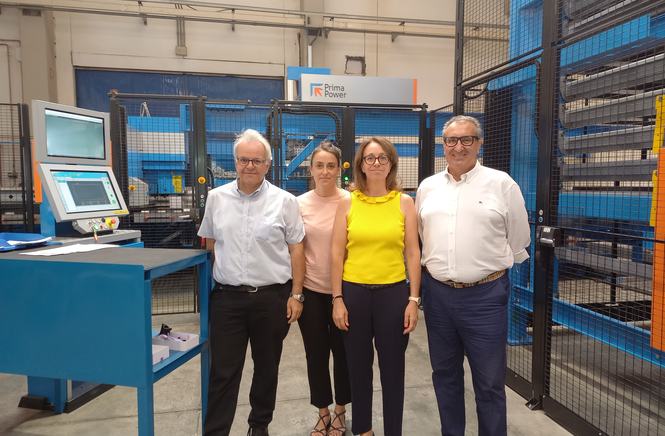
L’Industrie 4.0 avant même que la définition n'existe et toujours orientée vers l'investissement dans les nouvelles technologies, l’entreprise de métallurgie DAV de Rho a décidé de se concentrer sur une Combi Genius 1530 machine laser et poinçonnage hautement automatisée de Prima Power pour augmenter l'efficacité de la production et élargir la gamme d’opérations d’usinage qui peuvent être effectuées directement sur la machine.
S'adresser à de nombreux secteurs peut signifier se présenter comme un fournisseur générique, c'est-à-dire capable de fournir un service utile à de nombreuses entreprises différentes. Pour DAV, une menuiserie métallique fondée en 1969 à Rho (MI) par Angelo Vavassori et aujourd'hui dirigée par ses enfants Stefano, Barbara et Claudia, le défi permanent est de s'adresser à des interlocuteurs et des secteurs très différents en leur apportant l'expertise et les technologies qui leur permettront de fournir des services spécialisés à forte valeur ajoutée.
"DAV – expliquent Stefano et Barbara Vavassori, "est une entreprise multisectorielle car elle parvient à fournir un service complet et spécialisé à des entreprises très différentes (de l'automobile au secteur pharmaceutique, en passant par le pétrole et le gaz, l'intralogistique et le ferroviaire). En tant que menuisier métallurgiste, nous avons développé de nombreuses compétences ; le savoir-faire de notre personnel et les technologies de pointe nous permettent de fabriquer différents produits par découpe laser, poinçonnage, pliage, soudage, peinture et assemblage – tout en optimisant les délais et les coûts pour une plus grande satisfaction du client. Nous sommes un véritable partenaire unique dans les travaux de menuiserie".
" DAV ne se limite pas à la transformation de la tôle, mais propose également des services spécifiques très appréciés par les clients. « Nous offrons un support complet au client - continue Stefano Vavassori - nous contribuons au développement de solutions constructives pour perfectionner les produits du client, nous proposons des améliorations à la production, nous préparons la documentation technique (rapports dimensionnels, carnets de soudage, documentation PPAP, analyse FMEA et certifications) mettant à disposition 15 000 m2 d'espace de production pour fabriquer et stocker des produits selon les besoins du client". Il est important de souligner comment DAV a acquis au fil du temps une connaissance complète des types de produits de ses clients et des problèmes de fabrication qui y sont liés, ce qui permet à l'entreprise d'apporter un support précieux dans tous les secteurs.
" Il n'est pas facile de maintenir cette horizontalité - explique Barbara Vavassori – en effet, cela demande un engagement à toujours rester à la pointe de la technologie pour comprendre les spécificités des différents produits et obtenir des qualifications spécifiques du secteur. C'est précisément pour cette raison que DAV investit massivement, tant dans l'innovation technologique que pour maintenir un niveau de compétence élevé, en facilitant le transfert de connaissances des opérateurs expérimentés vers les nouveaux, avec des cours ciblés et des formations sur le terrain".
En plus de se proposer comme un véritable partenaire aux côtés du client, ces compétences déclenchent un cercle vertueux dans lequel DAV et ses clients s‘échangent mutuellement des compétences et des expériences utiles à la croissance et à l'innovation.
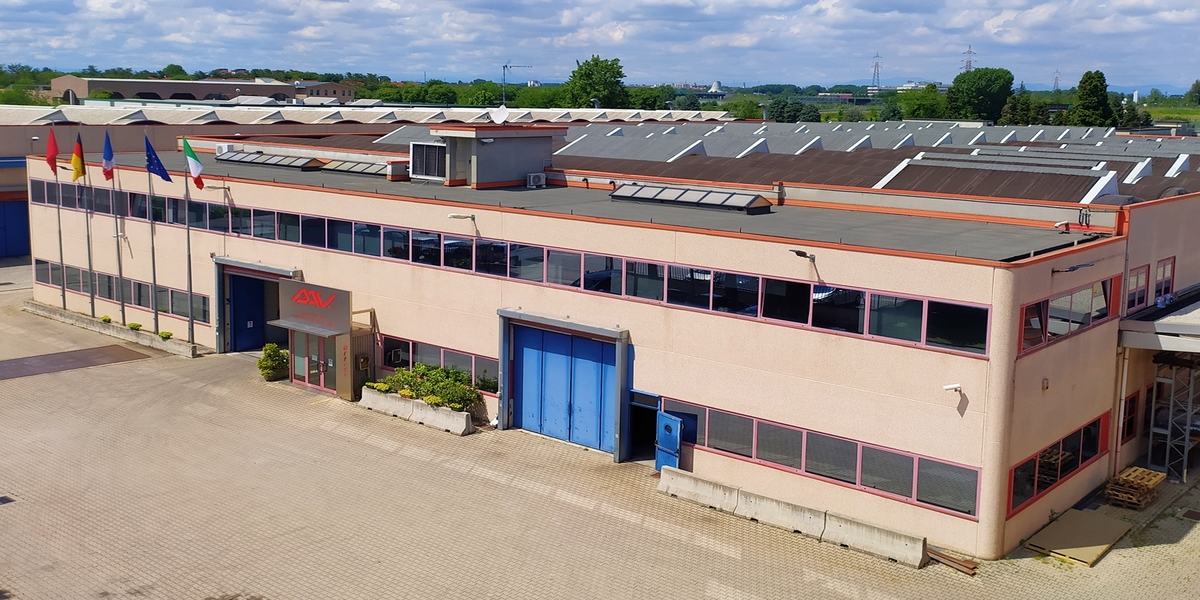
L'INNOVATION AU SERVICE DU CLIENT
Un trait distinctif de l'histoire entrepreneuriale de DAV est sa volonté de toujours investir dans des technologies innovantes, en identifiant à l'avance les solutions qui lui permettent de répondre aux besoins de ses clients.
"Notre père – se souvient Barbara Vavassori – a été parmi les premiers en Lombardie dans les années 90 à acheter une machine de découpe laser : l'innovation a toujours été pour nous un élément de différenciation, cela se reflète également dans le choix d'adapter le processus de production et le système de gestion de l’entreprise aux normes de qualité ISO 9001 dès 1999 ou d'investir dans un entrepôt automatisé pour la tôle quelques années plus tard". Nous parlons d'une entreprise qui a achevé l'intégration et l'interconnexion entre l'entrepôt, la production et la conception avant même l'émergence du concept d'Industrie 4.0.
" DAV a été pendant de nombreuses années l'Industrie 4.0 pour l'usinage de découpe laser – expliquent les propriétaires – en 2005, grâce au développement interne d'un logiciel dédié, les plans d'usinage étaient envoyés du service technique aux machines laser, puis à la fin du processus de production toutes les données de production étaient automatiquement inscrites dans le système de gestion, mettant à jour les temps de coupe, les quantités et les stocks de matières premières.
L'investissement récent dans un combiné poinçonnage - découpe laser Combi Genius 1530 de Prima Power avec une source laser fibre de 4 kW, une table de travail de 3 000 mm x 1 500 mm et une automatisation élevée s'inscrit précisément dans cette stratégie d'innovation continue.
" Nous pension déjà une telle machine depuis quelques années – explique Stefano Vavassori -, mais au cours des dernières années, la quantité de pièces nécessitant à la fois des opérations de découpe et de formage a considérablement augmenté. Il s'agissait d'effectuer d'abord les opérations de découpe sur une machine laser, puis de déplacer les pièces vers la poinçonneuse et de réaliser les autres opérations. Cela représentait une perte de temps considérable et, avec la hausse des prix des matières premières, nous risquions de ne plus être compétitifs sur le marché de ces produits". L’arrêt des activités imposé par le confinement a été l’occasion de répondre à ce besoin et de chercher une solution sur le marché.
Nous étions tous coincés à la maison, nous sommes donc allés sur le site web de Prima Power et avons demandé de nous contacter pour plus d'informations sur le Combi Genius qui, à ce moment-là, nous semblait être la machine idéale pour nos besoins de production".
C'est à ce moment-là, et avec beaucoup de facilité, qu’une relation d'échange et de connaissance mutuelle s'est instaurée entre les deux sociétés, ce qui nous a permis de nous concentrer davantage sur les besoins de DAV et les solutions Prima Power les plus adaptées.
" Avec Prima Power, nous avons non seulement visité des entreprises qui utilisaient déjà le Combi Genius, mais nous avons également effectué une série de tests dans leurs usines pour produire certains types de pièces. Le résultat a été surprenant : quand j'ai vu les vidéos et les rapports de production, nous avons compris que c'était exactement la bonne machine étant donné qu'elle permettait de réduire le temps de production de plus de 60%."
L'automatisation, à savoir un robot LSR de chargement, de déchargement et d'empilage et un système de stockage double Combo Tower, ont également joué un rôle crucial dans cet investissement. « Comme nous avions déjà un haut niveau d'intégration entre la production, l'entrepôt et le bureau technique – explique Barbara Vavassori – il était également assez simple d'interfacer notre système de gestion avec l’usine Prima Power, qui, comme nous le rappelons, est fournie prête pour le 4.0 et avec un logiciel dédié."
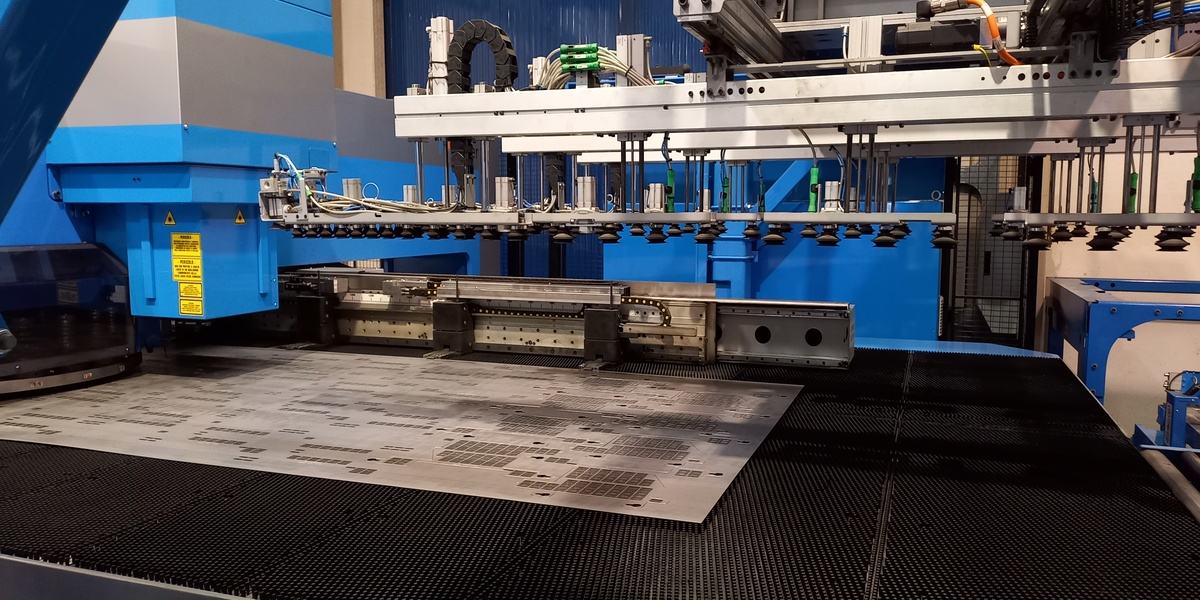
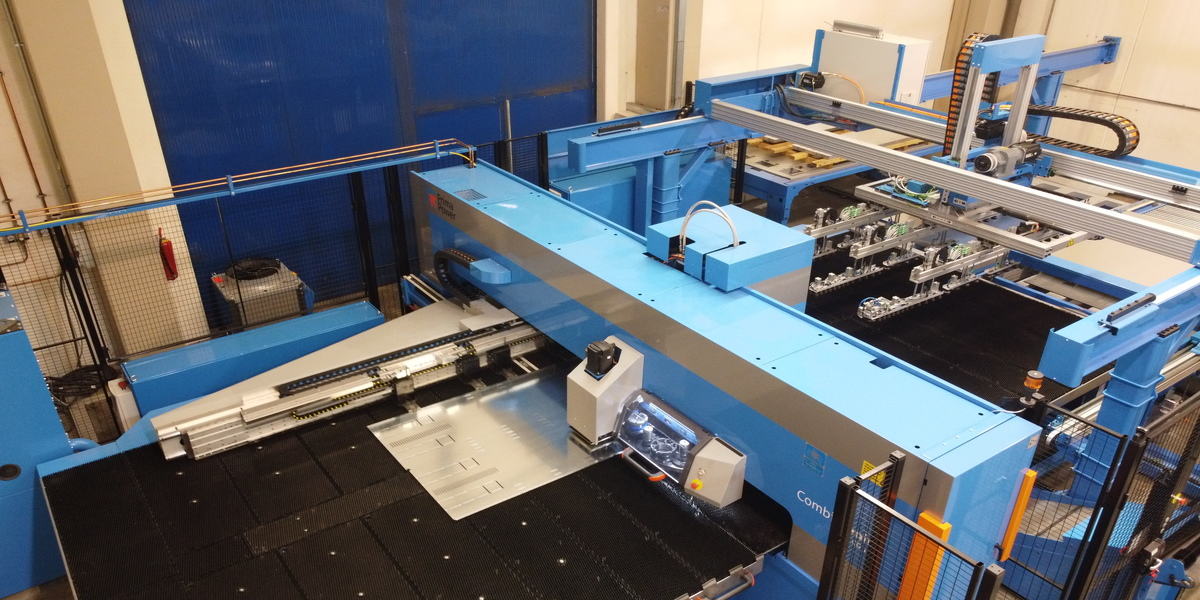
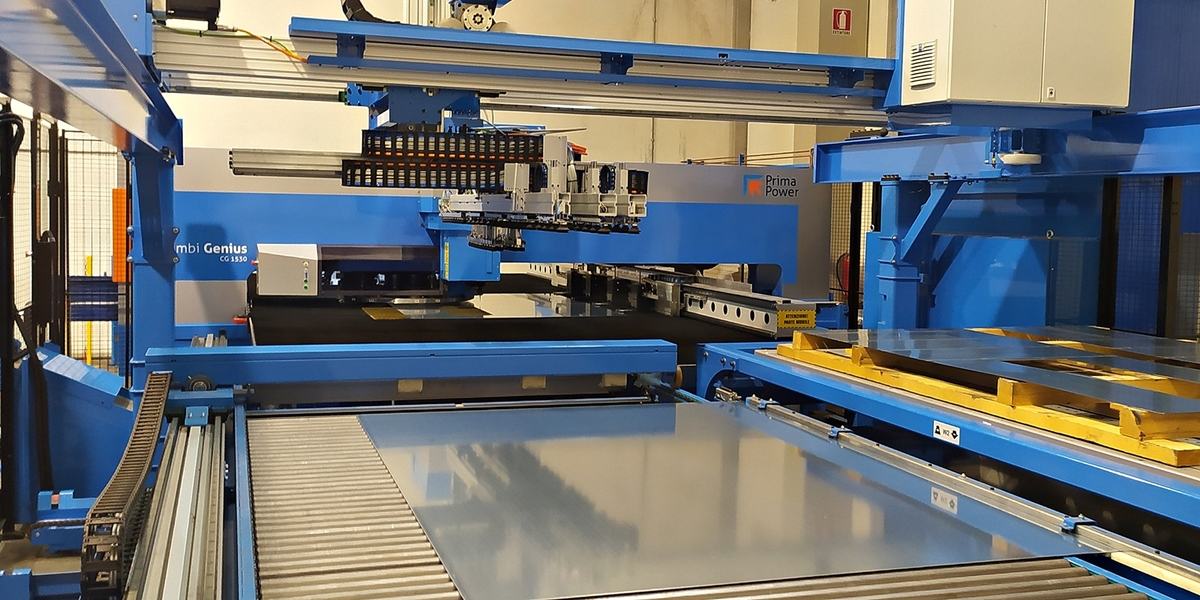
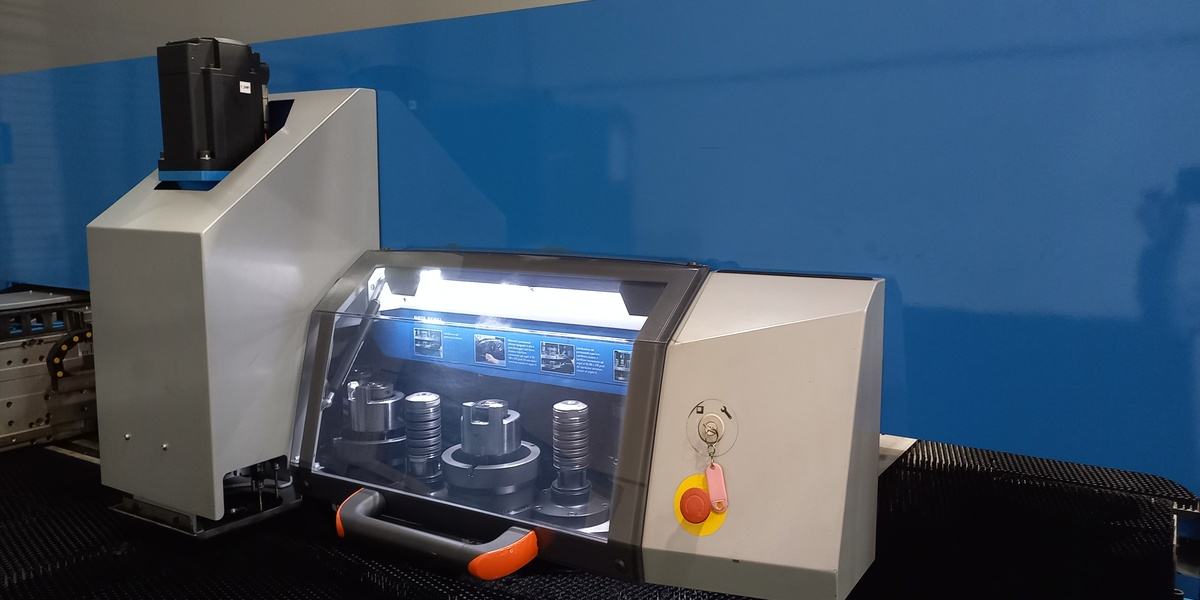
LES AVANTAGES DU COMBINÉ
.Le Combi Genius 1530 est en service depuis mai 2021 et au cours des derniers mois d'utilisation, il a apporté plusieurs avantages à DAV, à commencer par une forte augmentation de productivité par rapport au passé, lorsque ces processus nécessitaient un double passage sur deux machines (découpe laser et poinçonneuse).
" Un autre avantage est que nous avons pu « décharger » les machines laser d’une partie de l’usinage, étant donné que le combi Prima Power s'est également avéré être une excellente solution pour réaliser diverses découpes. Étant une machine entièrement électrique à faible consommation, Combi Genius était la solution idéale dans une période où les coûts de l'énergie et de l'azote montaient en flèche : ceci est confirmé par le fait que, bien que DAV ait augmenté son chiffre d'affaires, elle a réduit sa consommation d'électricité cette année.”
Après quelques semaines d'utilisation du Combi Genius, d'autres avantages sont également apparus, parmi lesquels se distingue la possibilité d'effectuer le marquage des pièces dans la même position.
" Chez DAV, nous devons marquer toutes les pièces avec une ficelle, une opération que nous effectuions auparavant à la main à l'aide de presses. Avec le Combi Genius nous pouvons le faire directement sur la machine grâce à certains outils spécifiques qui fonctionnent par impression ou gravure ."
Comme le Combi de Prima Power est une machine servo-électrique, il est particulièrement efficace dans ces opérations car vous avez le contrôle total de l'axe de poinçonnage, et vous pouvez décider de la pénétration et du relief pour le marquage. Il est important de souligner que, grâce au combiné de Prima Power, DAV a non seulement réussi à pénétrer de nouveaux marchés, mais a également élargi la gamme des opérations de formage qu'elle réalise, en exploitant les capacités du Combi Genius pour effectuer des opérations directement sur la machine qui nécessitaient auparavant l'utilisation de matrices.
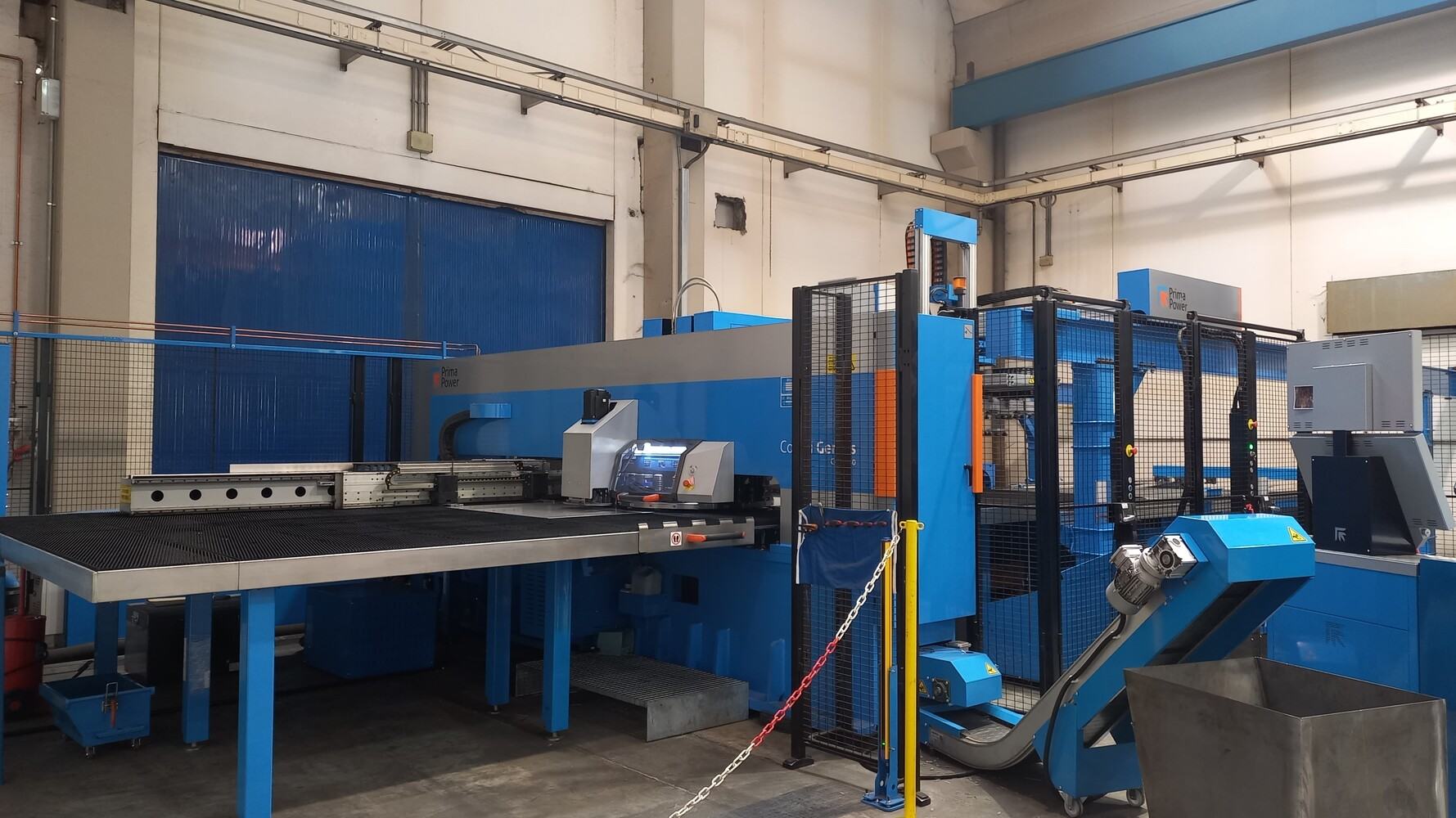
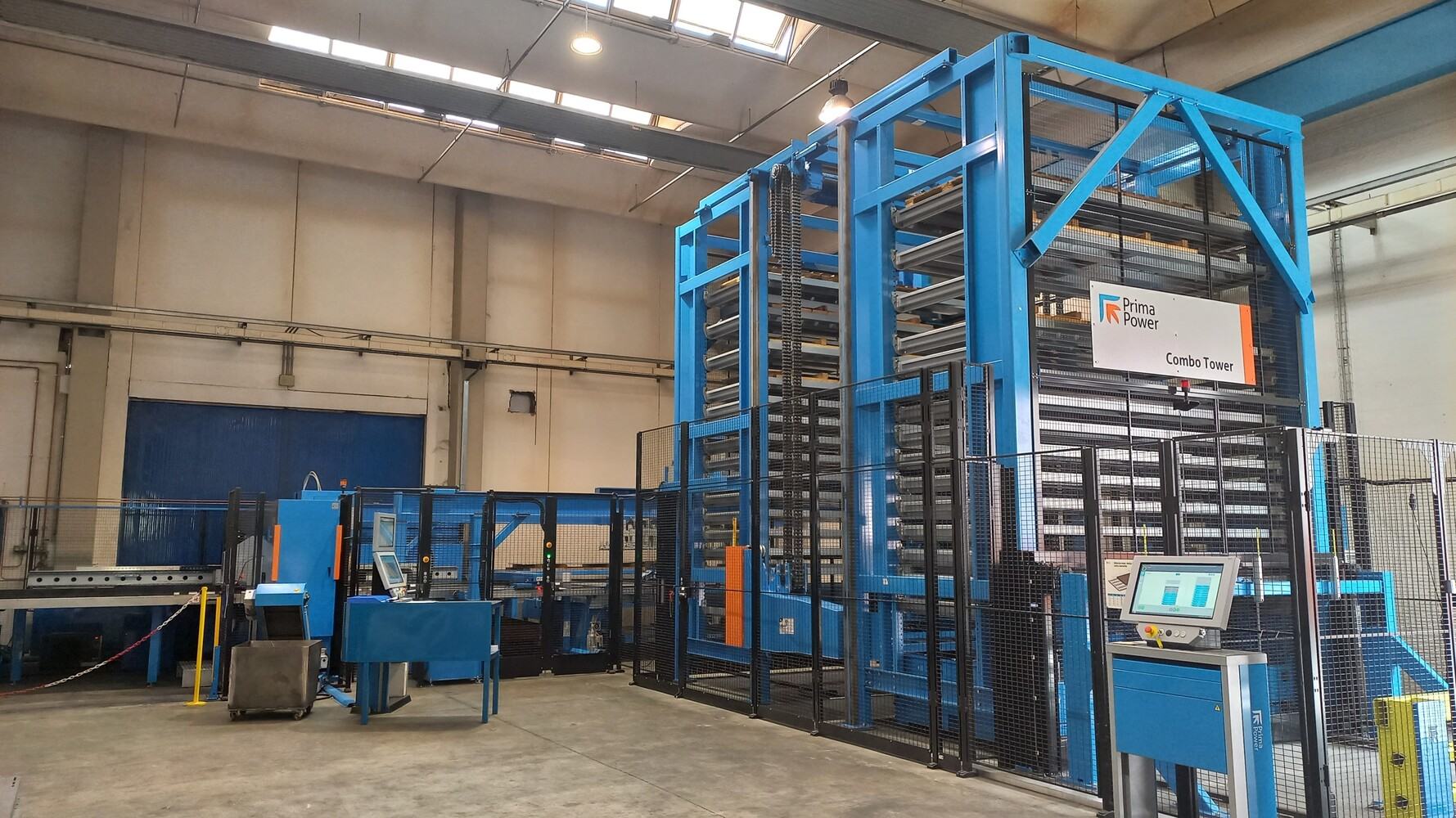
AUTOMATISER... DANS PETIT ESPACE !
En regardant l'impact du Combi Genius installé chez DAV, nous constatons que la machine combinée est toujours en mesure de livrer une pièce finie et propre.
"Je suis convaincu que pour réduire les temps d’usinage, il est plus important d’automatiser la partie chargement et déchargement plutôt que d'augmenter la puissance de la source – confirme Stefano Vavassori.
" En effet, dès le début nous avions demandé la présence du robot LSR. (acronyme de " Loading and Stacking Robot") pour charger et décharger les pièces afin d'éviter toute intervention manuelle à la fois pour une plus grande sécurité de l'opérateur et pour éviter d'endommager les pièces usinées". A noter que pour augmenter la fiabilité du processus de prélèvement des pièces découpées au laser, la technologie RALC (Robot Assisted Last Cut) a été prévue sur le robot LSR. Lors de la dernière coupe, la machine et le robot effectuent des mouvements simultanés et synchronisés des axes assurant un prélèvement sûr et fiable des pièces.
" Pour nous – poursuivent les propriétaires de DAV – il était également particulièrement important que Prima Power fournisse deux trappes sur cette machine afin de permettre de nombreuses méthodes de déchargement : directement dans la trappe pour les petites pièces mais aussi individuellement sur des palettes externes. L'automatisation du déchargement est fondamentale pour nous, nous connectons déjà des machines laser aux entrepôts depuis des années et nous connaissons les avantages qui en découlent". C'est précisément pour cette raison qu'il a été décidé de connecter un système de stockage automatique au Combi Genius 1530, transformant ainsi le système en une véritable cellule d’usinage.
" Je suis convaincu que l'avenir passe par des cellules automatisées en production, peut-être en parallèle, qui réalisent les différents processus avec une flexibilité maximale. Dans ce scénario, il est essentiel de prévoir également des interconnexions avec des entrepôts automatisés".
" Pour le Combi Genius, DAV a choisi d'investir dans un double système de stockage Combo Tower, la solution Prima Power pour un stockage flexible et l’automatisation du flux de matériaux à ses différents stades : brut, semi-fini et chute. Combo Tower met en effet à disposition différents matériaux, dès qu'ils sont nécessaires, automatiquement et sans délai ; elle peut également servir de tampon ou de stockage intermédiaire pour les composants finis.
" Dès les premiers aménagements, nous nous sommes orientés vers une solution à deux tours qui augmentait considérablement l'autonomie de la cellule avec une augmentation minimale de la taille."
La question de l'empreinte au sol de l'usine était, comme c'est souvent le cas pour les entreprises italiennes, un véritable défi : trouver de l'espace dans l'entrepôt n'était pas facile.
" La compacité et la structure modulaire qui caractérisent les solutions Prima Power nous ont beaucoup aidés – explique Vavassori -, de plus, grâce au robot LSR, la manipulation des pièces ne prend guère plus de place qu'une machine autonome ."
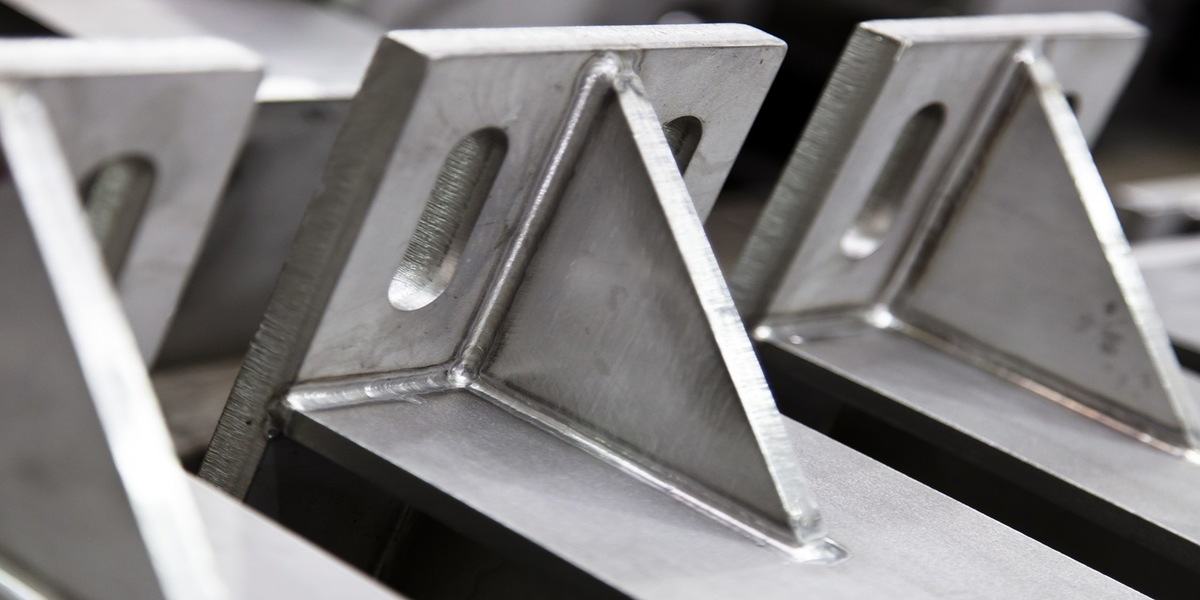
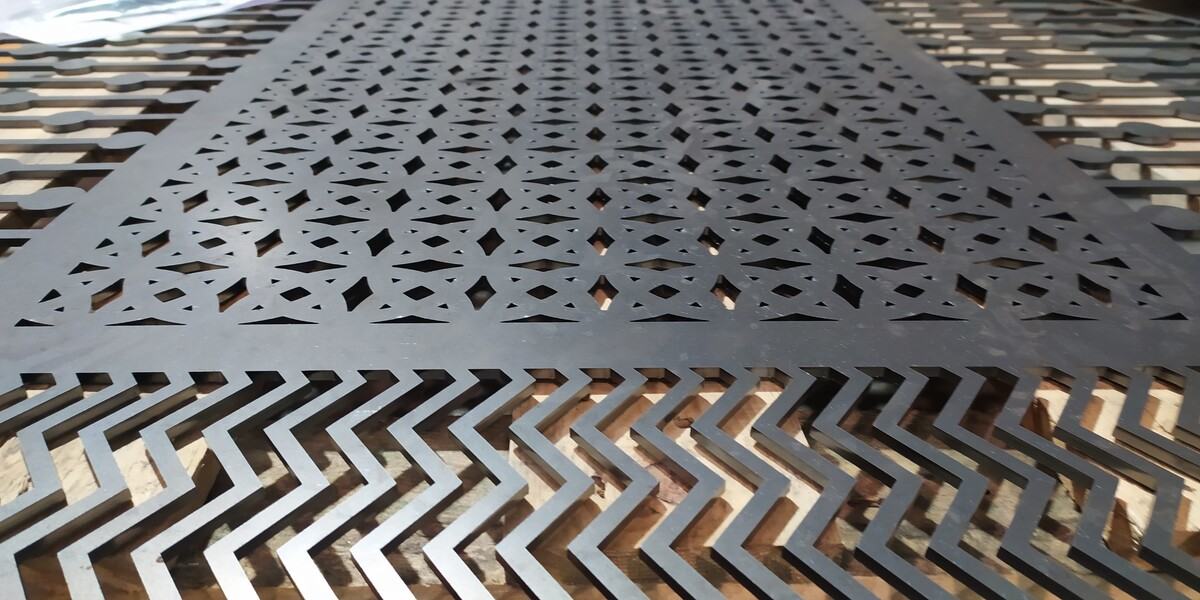
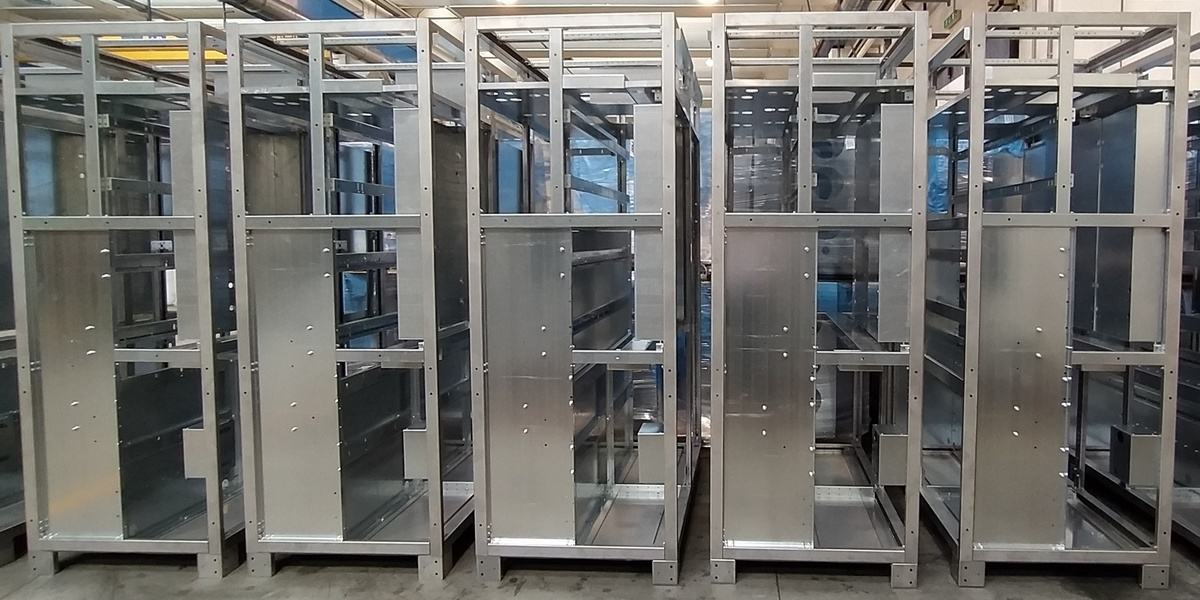
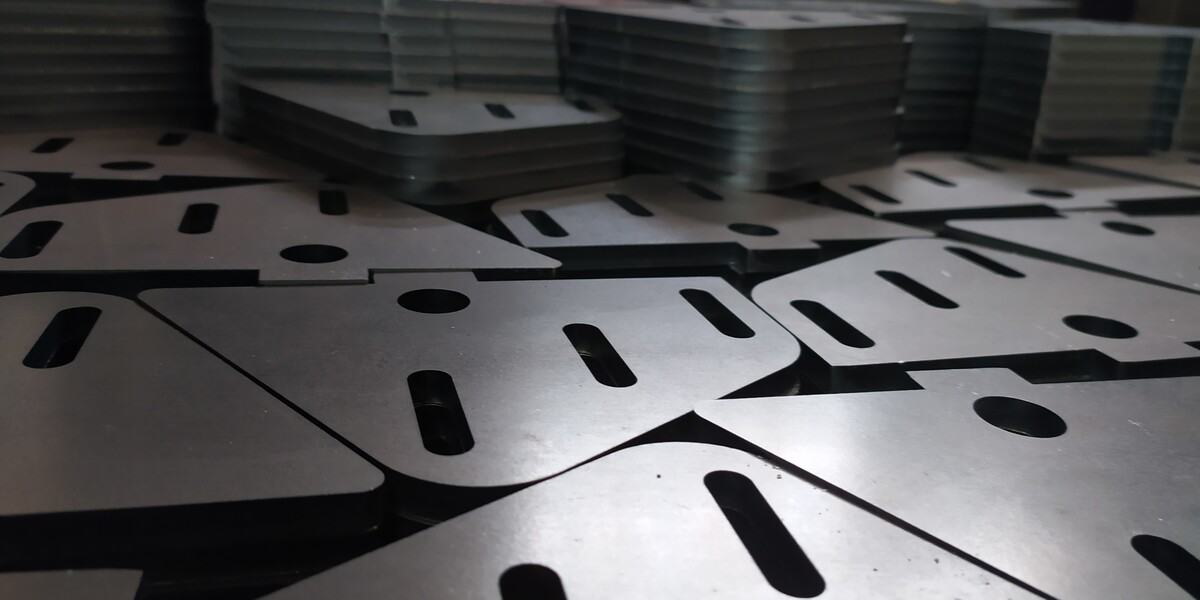
Avec Prima Power, nous avons non seulement visité des entreprises qui utilisaient déjà le Combi Genius, mais nous avons également effectué une série de tests dans leurs usines pour produire certains types de pièces. Le résultat a été surprenant : quand j'ai vu les vidéos et les rapports de production, nous avons compris que c'était exactement la bonne machine étant donné qu'elle permettait de réduire le temps de production de plus de 60%.
Vous cherchez une solution similaire pour votre entreprise ? Découvrez-la ici
Combi Genius
MACHINES COMBINÉES DE POINÇONNAGE ET DE DÉCOUPE LASER
Poinçonnage + Découpe laser = Économie de fabrication supérieure
1+1>2
Loading and stacking robot (LSR)
MANUTENTION DES MATÉRIAUX