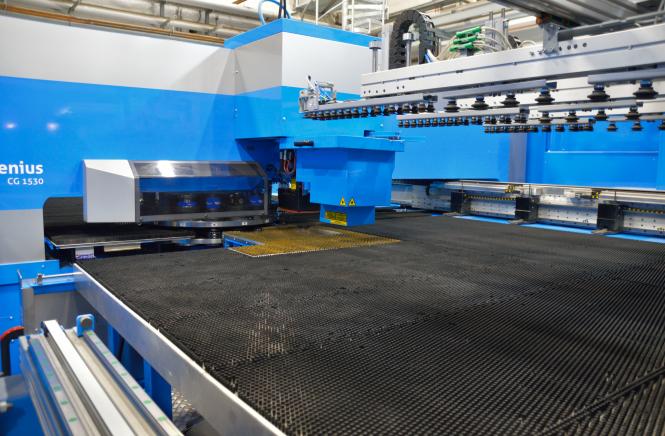
Budoucí montáž s novým kombinovaným strojem (laser+děrování)
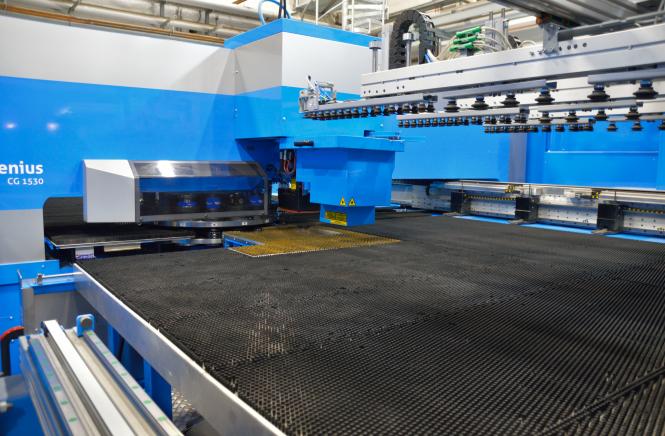
Společnost Eisenwerk Wittigsthal GmbH investuje do stroje, který kombinuje laser s děrováním, aby byla připravena na digitální budoucnost.
„Jsme spíše výrobcem produktů na míru než sériovým výrobcem,“ říká Jochen Browa, jednatel a spolu se svou ženou majitel společnosti Eisenwerk Wittigsthal GmbH v Johanngeorgenstadtu v Krušných horách. Společnost se zaměřuje na systémové vybavení pro instalace budov a v každém případě hodně zpracovává plechy, takže bylo logické rozšířit svou činnost o smluvní výrobu související s plechy. Za tímto účelem společnost Eisenwerk Wittigsthal v loňském roce investovala do systému Combi Genius od Prima Poewer, který kombinuje laser s děrováním.
Jméno Eisenwerk Wittigsthal mohou lidé ve východním Německu znát nejen proto, že společnost existuje již 366 let, ale také proto, že v 80. letech 20. století byla největším dodavatelem smaltovaných kotlů na dřevo. Kdo si chtěl v bývalém východním Německu dopřát teplou koupel, spoléhal na tyto kotle. V některých obdobích se vyrábělo až 250 000 kotlů ročně a celkem se prodalo více než 4 miliony kusů. Krátce před pádem Berlínské zdi se v továrně v Johanngeorgenstadtu připravovala výroba komponentů pro východoněmecký miniautomobil Trabant, ale nic z toho nebylo.
Po sjednocení Německa došlo k výraznému poklesu zakázek a společnost musela počkat až do roku 1992, kdy ji převzal podnikatel Winfried Friedrich a provedl její kompletní restrukturalizaci a reorganizaci. Společnost Eisenwerk Wittigsthal se vyvinula v dodavatele hotových systémových řešení pro budovy, jehož hlavní činností jsou měřicí, distribuční a řídicí systémy. Tyto měřicí systémy a rozváděče se instalují do plechových skříní pro povrchovou nebo zapuštěnou montáž. Když Winfried Friedrich v roce 2008 odešel do důchodu, převzal společnost Jochen Browa se svou ženou. Posílili svou činnost v oblasti ventilací a prosadili se v zakázkové výrobě z plechu. Vytvořili společnost, která dnes zaměstnává 60 lidí a dosahuje obratu přibližně 10 milionů eur ročně.
Stará a nová automatizace
Jochen Browa nám během naší prohlídky ukázal 55 000 m2 areálu. Naše první zastávka byla ve výrobním závodě kotlů na dřevo, který je automatizovaný s tehdejší technologií. Jednou nebo dvakrát ročně se lisy a smaltovací linka spustí asi na sedm týdnů, aby se vyrobilo 3 000 až 4 000 kotlů na vodu, po kterých je dodnes poptávka. Vždyť 10 % obratu společnosti pochází právě z této oblasti, což je sice malý, ale přesto významný podíl, protože 75 % obratu pochází z hardwaru pro stavební systémy. O zbývající obrat se dělí vzduchotechnika a zakázková výroba z plechů.
Speciální řešení a sériová výroba
„V našem ceníku máme asi 5 000 položek,“ říká s úsměvem Jochen Browa, „zákazníci si však často objednávají 5 000 komponent, které v něm nejsou. Naši zákazníci velmi oceňují, že od nás dostávají řešení na míru.“
Adaptace zahrnují jak čistě geometrické úpravy standardních katalogových řešení, tak zcela nové návrhy. To je důkazem odborné způsobilosti společnosti, která se uplatňuje i ve smluvní výrobě.
„Smluvní výrobu jsme prováděli dlouhou dobu, ale spíše v malém měřítku. Naše vybavení nás omezovalo na střední množství,“ vysvětluje Jochen Browa. K tomuto účelu byl použit systém děrování z 90. let 20. století od firmy Finn Power a relativně nová kombinace děrování a laseru od firmy Boschert bez automatizace. Lisy, které již mají, se však používají také pro zakázky z odvětví ventilace, které dosahují 400 000 až 500 000 vyrobených kusů ročně.
Dlouhodobý cíl: Průmysl 4.0
Jochen Browa vidí potenciál pro expanzi v zakázkové výrobě větších sérií a běžných dílů. „K tomu však potřebujeme flexibilní a automatizované řešení, které je zároveň schopné pracovat v Průmyslu 4.0.“ Jochen Browa přišel s nápadem konfigurační aplikace, pomocí které si zákazník může na svém chytrém telefonu navrhnout vlastní jednotku a odeslat objednávku přímo do stroje. Odhaduje však, že realizace projektu bude trvat dalších 10 let. Zaprvé, implementace je pro středně velkou společnost spojena s obrovskými náklady a zadruhé, jeho „zákazníci pocházejí z poměrně konzervativního odvětví a neskočí na každý módní vůz, který projde kolem“.
Plán je však nyní stanoven a společnost Eisenwerk Wittigsthal GmbH investovala v loňském roce do tohoto cíle přibližně 2 miliony eur. Jednou z těchto investic je plně automatizovaný systém kombinující laser a děrování od společnosti Prima Power. „Nejprve jsme koupili pouze kombinovaný stroj laser/děrování, ale pak následovalo rozhraní do skladu a ohýbací centru.“ Plně automatizovaná linka pro ohýbání, děrování a laserové řezání bude zavedena, jakmile budou výrobky k dispozici.
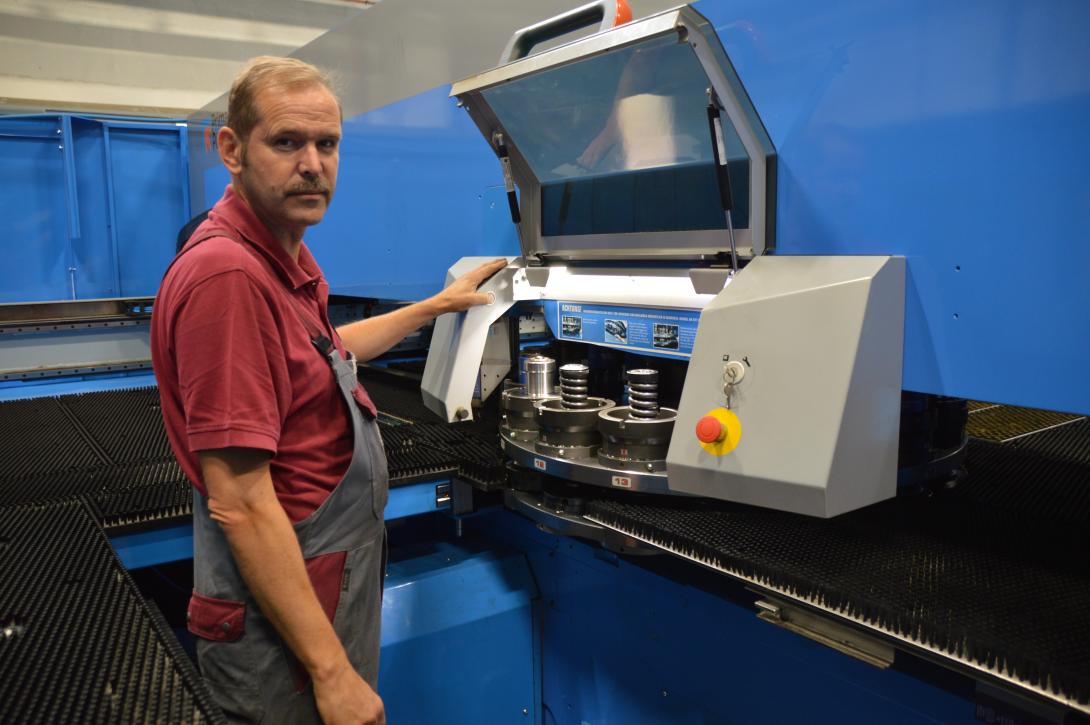
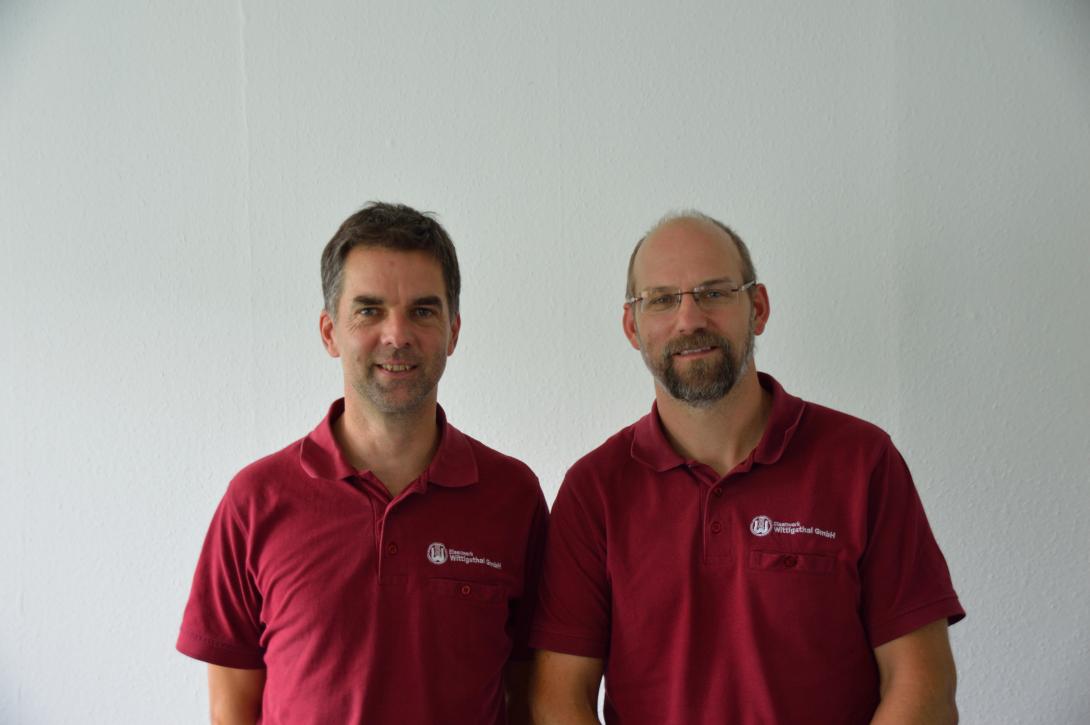
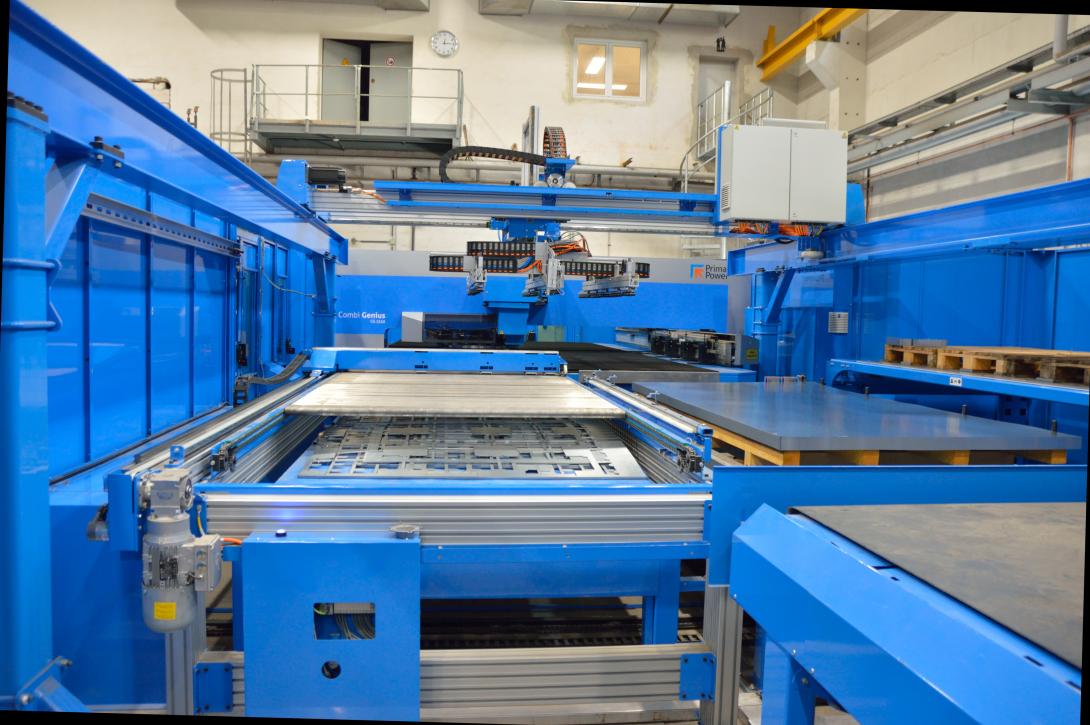

Roky dobrých zkušeností
Plánovaná nová továrna je také výsledkem dlouholeté spolupráce se společností Finn-Power, která je nyní součástí skupiny Prima Power. „S děrovacím strojem od společnosti Finn-Power pracujeme již více než 20 let. Z tohoto důvodu jsme se spojili se společností Prima Power. Se systémem jsme byli spokojeni a po 23 letech provozu jsme jej mohli dokonce dále prodat jako vhodný pro výrobu,“ říká Jochen Browa. Před rozhodnutím o investici jsme samozřejmě posoudili různé nabídky a svou roli hrála i cena. „Ale nakonec jsem si byl po dvou návštěvách společnosti Prima Power ve Finsku jistý, že automatizace bude fungovat tak, jak bylo nabídnuto.“
Nyní instalovaný systém je stroj Combi Genius, kombinovaný systém děrování a laserového řezání s plně automatizovanou manipulací.
„Kombinovaný systém děrování a laseru se nejlépe hodí pro naše výrobky, který zahrnují tváření, ražení a závitování a často je v nich mnoho otvorů,“ vysvětluje Robert Wiegand, vedoucí výroby ve společnosti Eisenwerk Wittigsthal.
„Například v oblasti ventilace máme také díly s mnoha otvory, pro které někdy používáme devítiotvorové nástroje, tj. nástroje, které vyrazí devět otvorů najednou. V této aplikaci ani ten nejrychlejší 2D laserový systém nedokáže držet krok.“ Robert Wiegand má pro optimální využití systému jednoduchý návod: Otvory a vnitřní kontury se děrují, vnější kontury se řežou laserem.
Všestranný kombinovaný systém děrování a laseru
Systém Combi Genius ve Wittigsthalu využívá děrovací revolver s 16 indexovými pozicemi a laserovou hlavu včetně 3kW vláknového laseru. Všechny osy jsou poháněny servomotory a řízeny systémem CPC. Děrovací stanice stroje je vybavena inteligentním beranem včetně otočného tlačného čepu pro rychlou výměnu nástrojů.
Do revolveru lze uložit celkem až 384 jednoduchých nebo 128 otočných nástrojů. „K tomuto účelu můžeme nadále používat všechny nástroje ze starého systému, včetně nákladných lisovacích nástrojů,“ vysvětluje Robert Wiegand. K dispozici je další speciální nářadí a multifunkční nástroje. Lze použít jak staré multifunkční nástroje, tak otočné multifunkční nástroje. Pro děrování je k dispozici síla 300 kN. Válečky, žebra a podobné tvary lze tvarovat až do výšky 15 mm.
Jak je u děrovacích laserových systémů standardem, je plech během zpracování držen upínkami a posouván po kartáčových stolech. Děrovací a laserové řezací hlavy zůstávají v pevné poloze. Kartáčové stoly jsou určeny pro plechy o hmotnosti 250 kg. Programem řízené kartáčové segmenty před děrovací věží a uvnitř ní zajišťují dodatečnou ochranu povrchu plechu. Tři upínky drží plech a systém CPC nastavuje polohu podle pracovního postupu, takže je možné optimální využití plechu bez nutnosti změny polohy.
Rychlý a bezúdržbový vláknový laser
Použitý laserový systém je systém s CF rezonátorem o výkonu 3 kW od společnosti Prima Power. Optimalizovaná řezná hlava, kolimátor, vedení paprsku a parametry řezu zajišťují vysokou kvalitu a rychlost řezání. Obsluhu laserového systému usnadňují různá zařízení. Patří mezi ně ochranné sklo LPW, které zabraňuje usazování řezného prachu a nečistot na objektivu, a monitor laserového plazmatu LPM, který sleduje proces řezání a v případě potřeby automaticky restartuje systém. Snímač navíc monitoruje čočku a její kvalitu.
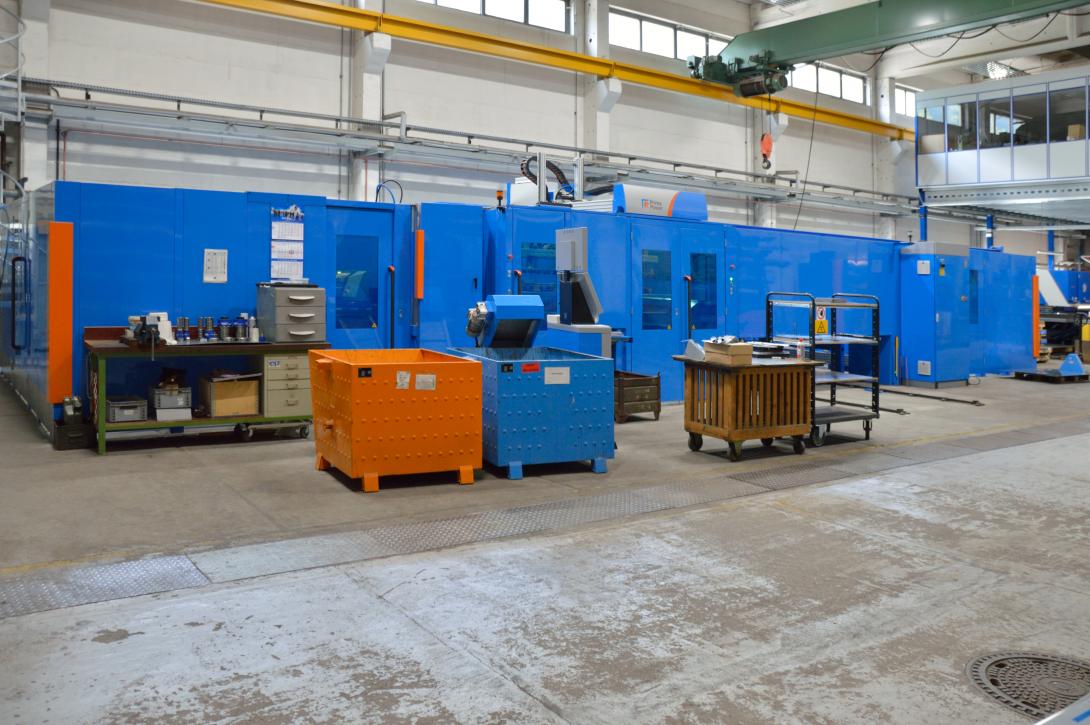
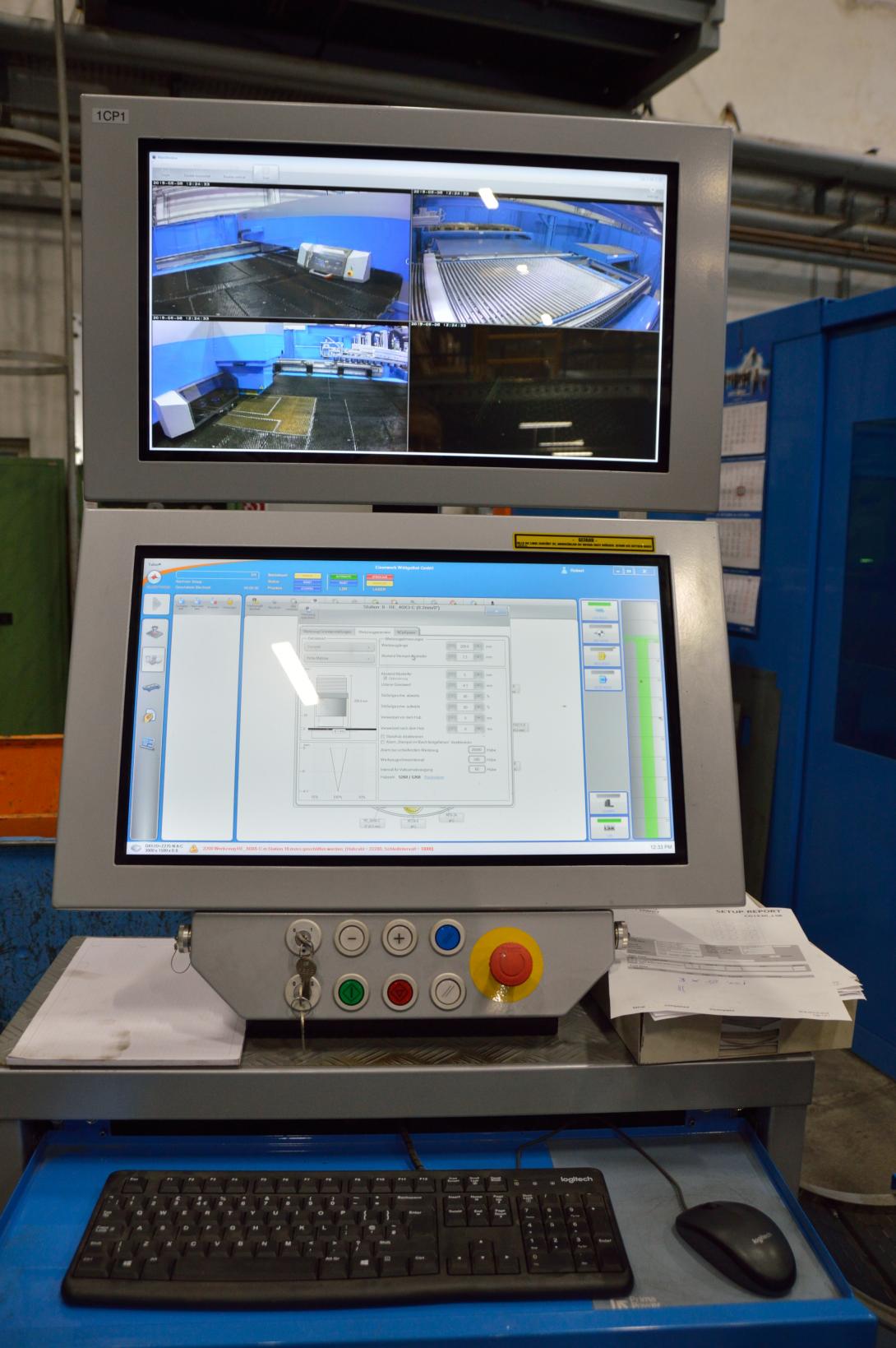
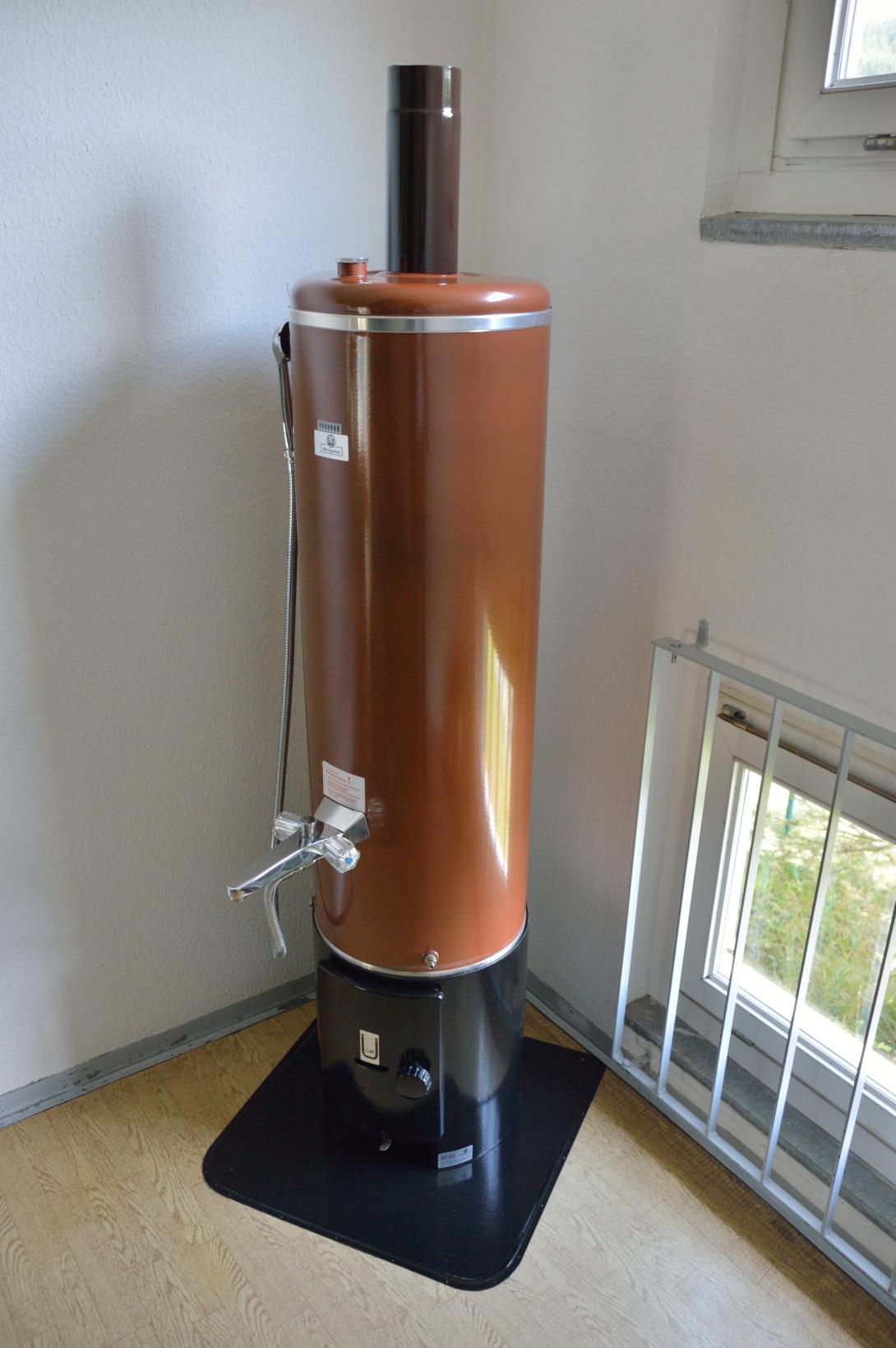
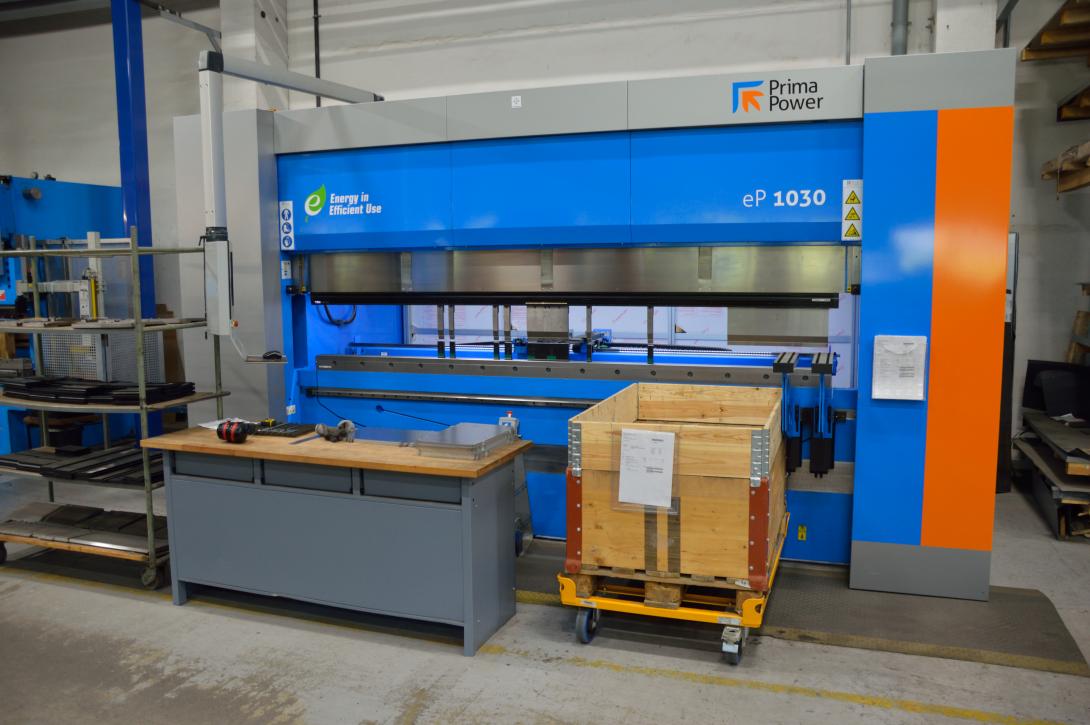
Nakládací a vykládací systém
Děrované díly se vykládají přes klapku na díly o rozměrech 500 x 500 mm. Pro laserové díly jsou k dispozici dvě klapky o rozměrech 300 x 400 mm pro rychlé třídění a 800 x 800 mm pro větší díly. Většinu dílů však nakládá a vykládá lineární robot s vysoce flexibilním systémem přísavek.
Balíky plechů jsou během výroby přiváděny do pracovního prostoru stroje. Lineární robot pak plně zvládá nakládání a vykládání. Vezme plechy jeden po druhém, vyrovná je a přesune na stůl děrovací laserové jednotky. Souběžně s nakládáním se z pracovního prostoru odstraní zbývající plechová mřížka a uloží se pod stoh nezpracovaného plechu.
V režimu řezání lineární robot odebírá hotové součásti bezprostředně po posledním řezu a ukládá je na hromádky na předem definovaných souřadnicích. K dispozici jsou dva stoly pro stohování. Teoreticky by bylo možné do stroje ručně vkládat až 5 m dlouhé plechy.
„Přesvědčilo nás také jednoduché ovládání systému,“ říká Robert Wiegand. „To platí jak pro přímou obsluhu stroje, tak pro programování. Na systém si zvyknete poměrně rychle i bez větších znalostí. Pokud znáte principy děrování, laserového řezání a základy CAD, je to navzdory složitosti systému překvapivě jednoduché.“
Systém Combi Genius se ovládá pomocí dotykového ovládacího panelu. Obsluha může kontrolovat nastavení stroje i seznamy úloh. Čtyři kamery kontrolují vnitřní prostor systému a sledují proces stroje. Obsluha má jasný výhled na nástrojovou hlavu se všemi používanými nástroji i na nastavení laserové hlavy. K dispozici je také systém správy nástrojů, který například zaznamenává počet provedených úderů a zobrazuje příslušné pokyny pro údržbu.
Operační systém a programovací systém NC Express e3 spolu bez problémů spolupracují. Zakázky vytvořené pomocí NC Express e3 můžete do seznamu zakázek zadat buď pomocí čtečky čárových kódů, nebo je Task loader automaticky vybere z databáze a vloží do seznamu zakázek se všemi požadovanými doplňujícími informacemi, jako je NC program, nástroj nebo materiál.
„Uvažovali jsme o použití programovacího systému, který by nám umožnil naprogramovat všechny stroje,“ vzpomíná Jochen Browa, „rozhodli jsme se však použít systém Prima Power kvůli jeho spolehlivému časování.“
Robert Wiegand dodává, že je stále znovu překvapen, jak přesně časy vypočítané během programování odpovídají skutečnému výrobnímu času na stroji, a to i u složitých dílů. „To má obrovský význam pro velkosériovou výrobu, kde často rozhoduje cent nebo zlomky centu.“ A protože právě pro takové případy je stabilní automatický provoz zásadní, dodává: „Stroj pracuje převážně automaticky bez zásahů. Pokud jsou NC programy správně nastaveny a otestovány, může stroj pracovat až do vyčerpání zásoby plechů ve stroji, aniž by bylo nutné provádět větší kontrolu.“
Skutečnost, že systém Combi Genius lze ovládat také prostřednictvím chytrého telefonu, je dalším důkazem, že společnost Eisenwerk Wittigsthal GmbH směřuje k digitalizaci výroby a průmyslu 4.0. Jochen Browa rozhodně uvažuje o rozšíření na plně propojenou linku na ohýbání, děrování a laserové řezání.
V našem ceníku máme přibližně 5 000 položek, ale zákazníci si často objednávají 5 000 komponent, které v něm nejsou. Naši zákazníci velmi oceňují, že od nás dostávají řešení na míru
Hledáte pro svou společnost podobné řešení? Najdete ho zde
Combi Genius
DĚROVACÍ A LASEROVÉ ŘEZACÍ STROJE KOMBINOVANÉ