
뛰어난 판금가공

오버외스터라이히주 헤어초그스도르프의 새로운 Biohort 생산공장 건설은 이제 1년 정도 진행된 상태입니다. 저장공간 솔루션 전문 기업인 Biohort는 노이펠든 본사에 추가로 2호 공장을 건립하며 최신 산업표준과 최적화된 공정 사이클을 바탕으로 하는 새로운 성장 자원을 창출했습니다.
그 결과 12,000 ㎡ 면적에 Prima Power의 최신 제조기술이 적용된 설비를 이용해 유럽에서 가장 발전된 형태의 판금가공 센터를 갖춘 공장이 만들어졌습니다.
오버외스터라이히주 노이펠든에 위치한 Biohort GmbH는 금속 저장 솔루션 분야에서 유럽 시장을 선도하는 기업 중 하나입니다. 제품 포트폴리오는 고품질 공구 저장고, 실용적인 실외용 보관 박스, 텃밭상자 (Raised bed)와 같은 유용한 원예용 솔루션 등으로 이루어져 있습니다.
1995년 요제프 프리글링어 (Josef Priglinger) 박사는 니더발트키르헨 (Niederwaldkirchen)에 위치한 전 표준강 제강공장의 금속 보관용 창고 생산 관리를 맡게 되었습니다. 2년 후에는 Biohort 표준강 지분의 100%를 인수했습니다. 이후로 이 회사는 프리글링어 가문이 소유 및 관리하고 있으며, 아버지와 이제 막 이 분야에 발을 들인 아들 막시밀리안 프리글링어가 공동으로 운영하고 있습니다. 막시밀리안 프리글링어 (Maximilian Priglinger)가 설명합니다. “우리 고객들이 지난 수십년 간 즐겨 찾았던 제품들은 정교한 설계와 인증된 공급자들을 통해 조달한 높은 품질의 자재를 바탕으로 오스트리아의 우수한 가공기준에 따라 만들어졌습니다. 때문에 우리가 20년 녹 보증을 적용할 수 있습니다.”
신록에 빠지다
지난 20년은 Biohort의 성공담으로 가득합니다. 매년 15-20%의 성장률을 기록했습니다. 그러나 이로 인해 노이펠든의 제조부문이 제조 능력과 같은 측면에서 한계를 드러내기 시작했습니다. 때문에 2016년 미래를 준비하기 위해 추가 생산 공장을 건립하기로 결정했습니다. 새 공장은 전체 생산 흐름을 충족하기 위해 미개발 전원지대에 건립될 예정입니다.
Biohort는 새 부지에 약 2000만 유로를 투자하면서 회사의 놀라운 성공담의 새로운 장을 열었습니다. 2017년 7월 헤어초그스도르프 공장의 기공식이 열렸습니다. 프리글링어 씨는 자부심 넘치는 목소리로 “우리는 오늘 투자의 결과를 마주하고 있습니다. 오스트리아에서 가장 현대적인 판금 가공 공장을 소유하고 있다고 말할 수 있게 되었습니다”라고 말했습니다.
생산공정의 재고
플랜트 설계는 단순히 새 건물을 설계하는 것과 완전히 다릅니다. 제조 공정을 처음부터 끝까지 재고해야 하며, 때로는 일정을 변경해야 하기도 합니다. 그 다음에야 생산 단계에 따라 건물을 짓게 됩니다. 다른 방법은 없습니다. 그렇게 처리량 수준을 적용한 결과 공정의 효율성이 극대화되었습니다.” 프로젝트를 시작부터 이끌었던 기술자 요하네스 자우너 (Johannes Zauner)가 설명했습니다.
지난 10월에는 라인이 가동되어 Biohort 레저용 보관 박스를 생산하기 시작했습니다. 생산제품의 다양성은 점차 확대될 예정입니다. 다음 단계로 LoungeBox, HighBoard 제품과 텃밭상자 제품의 생산지를 헤어초그스도르프로 이전할 예정입니다. 자우너 씨가 설명을 덧붙였습니다. “연간 1,600 톤의 판재를 가공해 약 50,000여 개 제품을 생산할 예정입니다.” 노이펠든 현장에서는 연간 7,600톤의 자재를 가공하고 있습니다.
헤어초그스도르프에 새 생산시설을 확보하면서 오스트리아에서 가장 현대적인 판금 가공 공장을 보유하게 되었습니다. 이렇게 큰 규모의 까다로운 프로젝트가 성공할 수 있게 해 준 시스템 공급자, 미래에도 함께 할 공급자로 Prima Power를 선택하게 되어 대단히 만족스럽습니다.
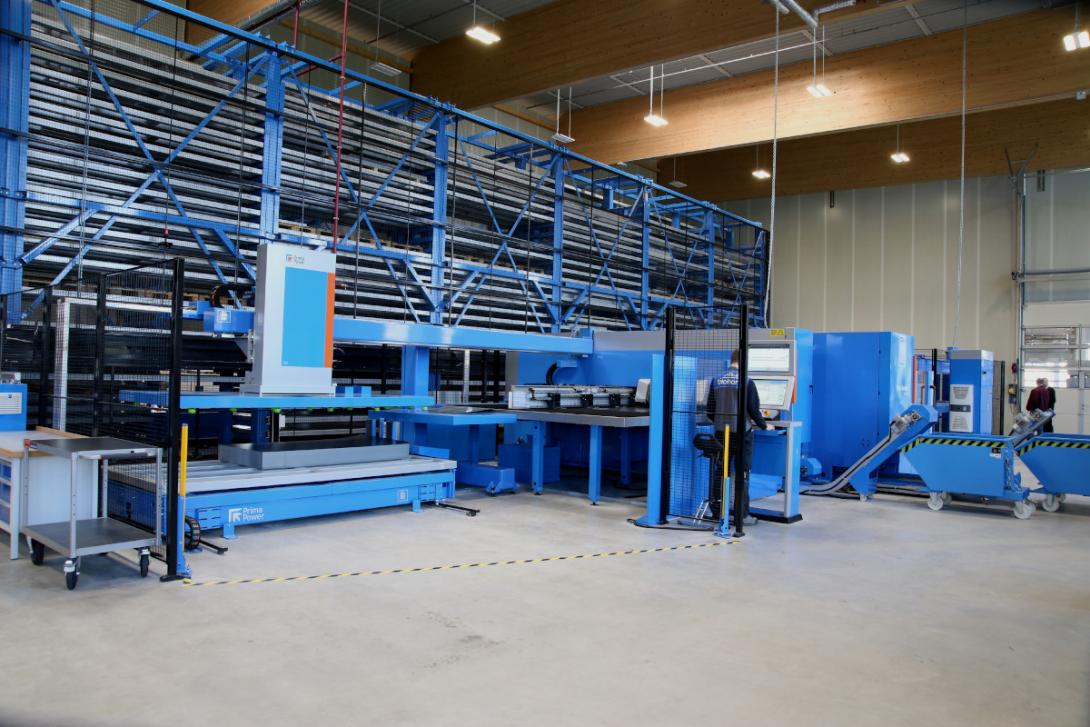
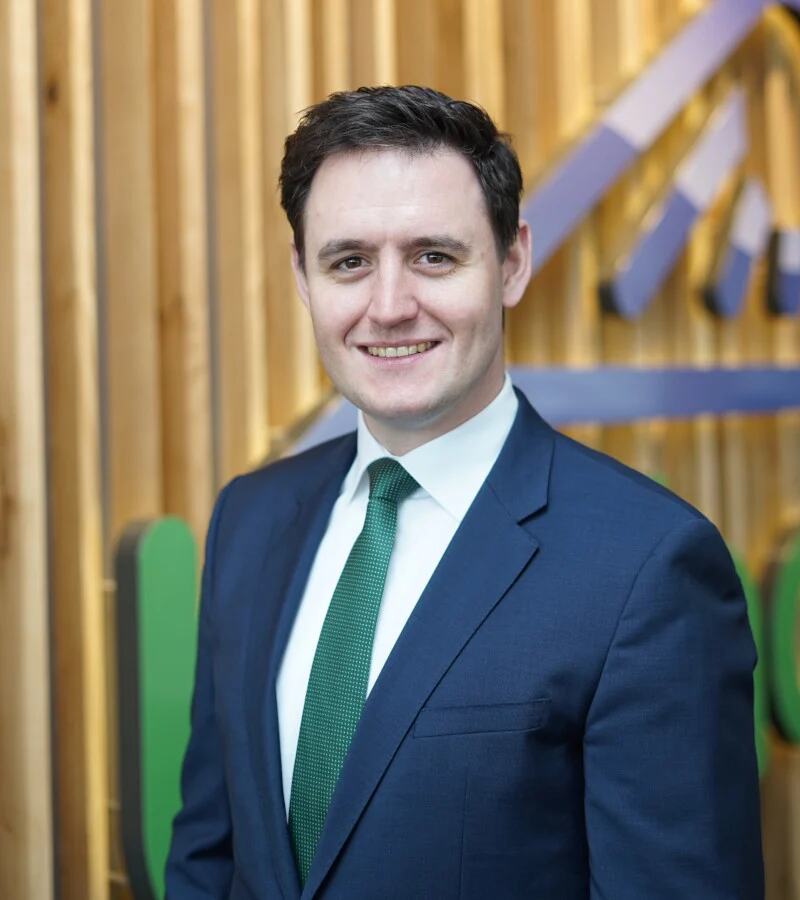
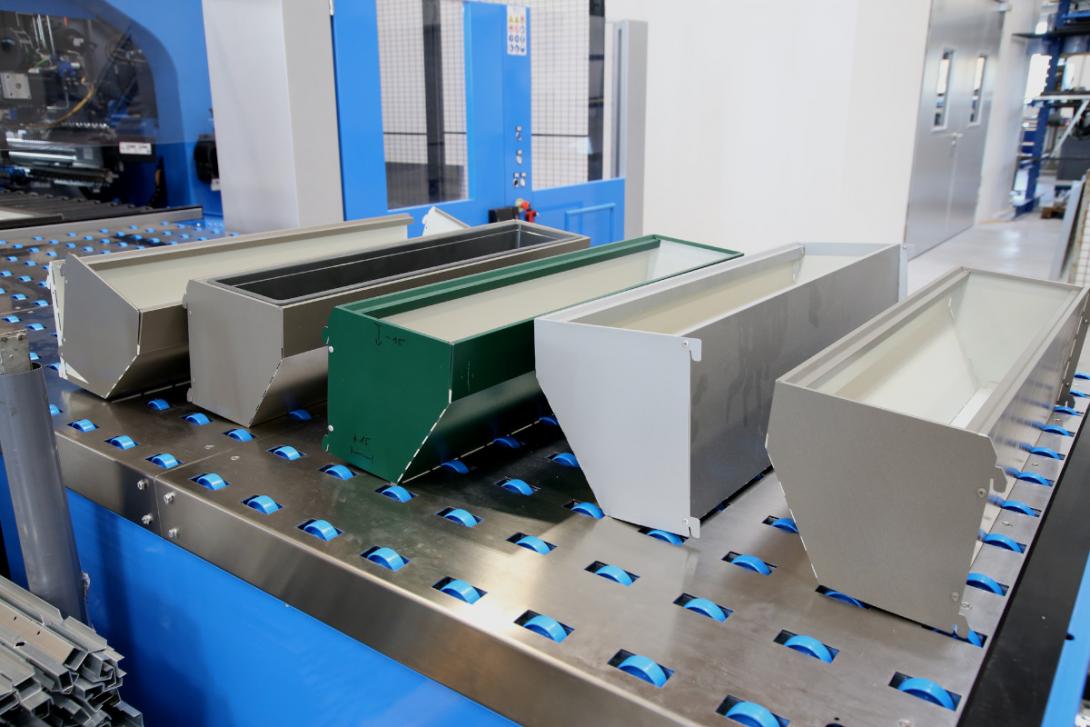
네트워크화된 생산기술의 강렬한 인상
프로젝트 책임자들은 Biohort가 장기적 성공을 거두기 위해서는 새로운 공장에 최신 혁신기술을 적용해야 한다는 사실을 처음부터 인지하고 있었습니다. 철저한 공급자 비교를 통해 완전 네트워크화된 생산 라인 공급자로 Prima Power가 선택되었습니다. 완전 자동화 판재 저장설비, 펀치-전단가공 결합형 시스템, 완전 자동화 벤딩기로 이루어진 생산라인을 공급할 수 있었기 때문입니다. “거기에 Prima Power가 시스템에 제3자 설비까지 통합할 수 있게 해 주었다는 점도 주효했습니다. 예를 들어, 우리가 현재 사용 중인 로봇 전단가공 피딩 시스템은 판재 저장설비와 통신하여 자재를 공급받습니다.” 자우너 씨가 만족스러운 목소리로 설명했습니다.
자동화 자재 공급
생산공정의 시작은 Prima Power의 완전 자동화 금속 저장설비 “Night Train Brilliance”에 원자재를 자동 저장하는 것에서 시작됩니다. 이 시설은 자재 저장을 최적화할뿐만 아니라 제조 시스템과 연계하여 사전에 지정된 제조공정에 따라 판금 부속을 이송하는 역할까지 맡습니다. 50 m 길이의 Night Train은 총 560개 저장용 박스 위치로 구성되며 각각의 박스에 원자재와 완성된 스탬프 블랭크를 최대 4톤까지 보관할 수 있습니다. 헤어초그스도르프의 판재 저장설비는 필요하다면 추가로 30 m 더 연장할 수 있습니다.
필요한 부속을 펀칭 가공하기 위한 설비로는 Prima Power의 펀치-전단가공 결합 시스템인 Shear Genius를 선택했습니다. “Biohort의 제품은 대부분이 직사각형의 기본적인 형태로 생산되는 관계로 펀칭 및 전단가공 시스템을 사용하는 것이 적절했습니다. 1차 펀칭 이후 통합된 오른편의 커팅 전단가공기로 동일한 공정을 진행하며 세 개의 부속으로 분리하면서 경제적 효율성이 극대화됩니다.” Prima Power의 오스트리아 지역 매니저 미하일 프뢸 (Michael Pr?l)이 강조했습니다.
긁힘 없는 펀칭 및 저장
나아가 설비의 시트 플로팅 시스템 덕분에 중요한 표면에 긁힘이 발생하는 것을 예방할 수 있습니다. “이 특수 펀칭 모드에서는 판재가 브러시 테이블 위에서 움직입니다. 주로 용융아연도금 판재, 도색 마감된 폴리아미드 에나멜 강판재를 보호 포일 없이 가공합니다. 때문에 생산 공정이 진행되는 과정에 부속에 긁힌 곳이 없어야 합니다.” Biohort의 기술매니저 대리 에리히 다너바우어 (Erich Dannerbauer)가 말했습니다.
피킹 및 스태킹 로봇 PSR도 기기 언로딩 시 자재를 대단히 부드럽게 다룹니다. PSR은 펀칭 가공이 끝난 부속을 다시 Night Train에 저장하기 위해 이송하는 부분도 담당합니다. 다너바우어는 이에 대해 “부속과 부속이 거칠 공정 단계에 따라 스태킹 로봇이 부속을 정확하게 각각의 저장 박스로 분류해 저장하는 방식으로 스태킹 영역 활용도를 극대화한다”고 설명했습니다.
Biohort의 노이펠든 주 공장에서 다른 제조사의 펀칭기 여러 대가 가동되고 있는 관계로, 펀칭 가공에 사용할 소프트웨어로는 Wicam 비독점 프로그래밍 소프트웨어를 사용합니다. “모든 펀칭기에 동일한 프로그래밍 체계를 적용하면 미래에 단순화를 이룰 수 있습니다.” 다너바우어 씨가 강조했습니다.
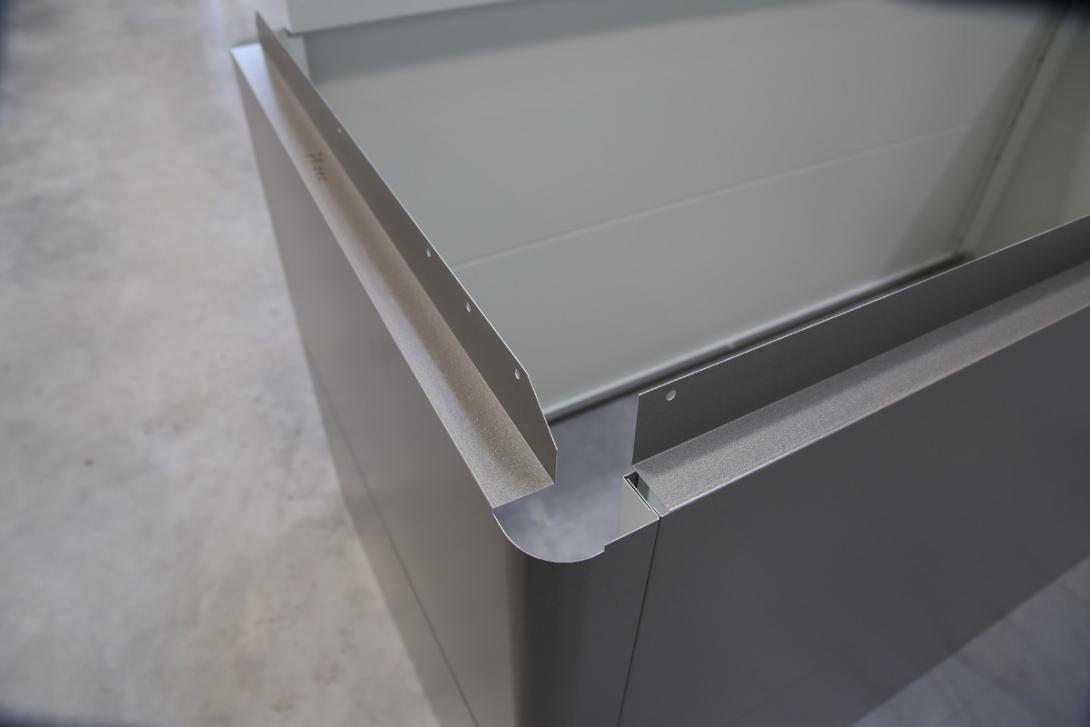
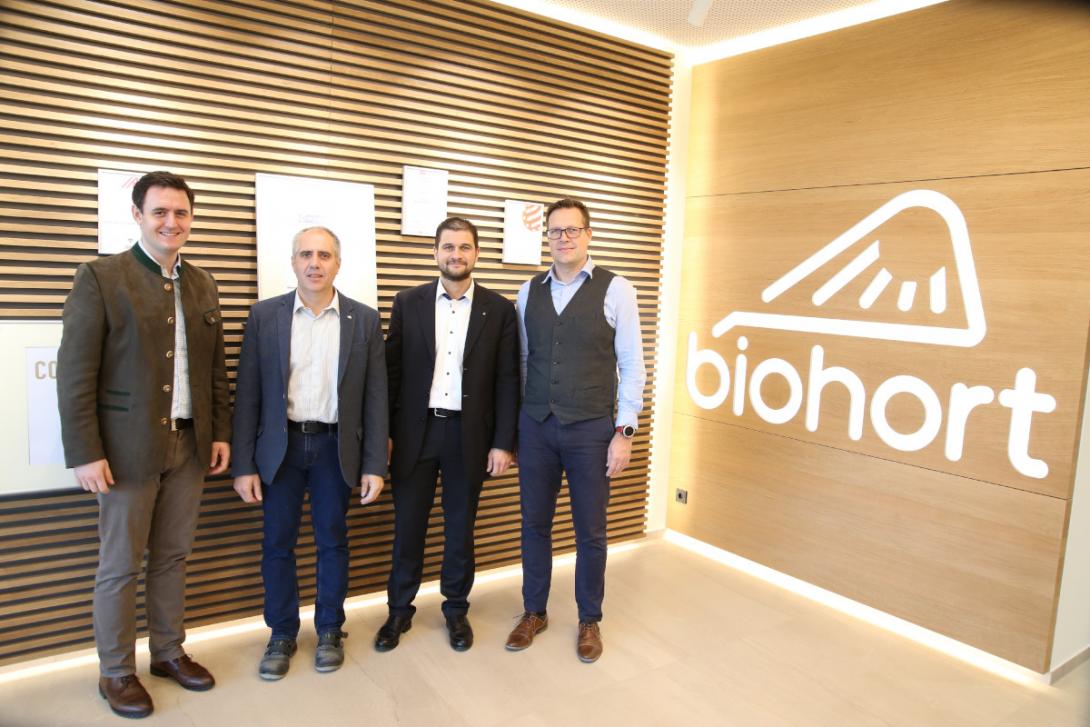
완전 자동화 벤딩
Night Train의 반대편, 원자재 저장 스테이션의 옆에는 로봇 전단가공 피딩 시스템과 기계식 프레스 브레이크가 설치되어 있습니다. 바로 Prima Power의 완전 자동화 벤딩기, EBe 5.3입니다. 이 설비는 물론 Night Train과 직결되어 있으며, PSR 피킹 및 스태킹 로봇이 펀칭 가공이 끝난 강판 블랭크를 공급하면 이를 가공하는 역할을 합니다.
특히 Biohort처럼 박스를 주로 생산할 때에는 벤딩 셀이 그 장점을 가장 잘 발휘할 수 있습니다. “준비시간이 짧은 것에 더해 간단한 챔퍼에서 벤딩 반경까지 모든 형태를 만들 수 있다는 큰 장점이 있습니다. 툴세트 하나면 충분합니다. 다른 크기의 제품을 생산할 때에도 빠르게 대응할 수 있다는 점도 있습니다.” EBe 설비의 효과가 인상깊었다며 다너바우어 씨가 말했습니다. 미래에 생산하게 될 제품에 대한 대비도 이미 끝난 상태입니다. 특수한 형태나 이음판 등을 생산하기 위해 비회전 툴 또한 준비되어 있습니다.
부속 생산 시 기존 기계식 프레스 브레이크에 비해 절약할 수 있는 부분이 많다는 점도 중요합니다. “우리는 복잡한 부속을 생산할 때를 기준으로 벤딩기를 이용해 3-4배 정도 더 빠르게 공정을 마무리할 수 있습니다. 기계식 프레스 브레이크를 쓸 때와는 달리 시간을 들여 툴 교체를 진행할 필요도 없습니다.” 그가 강조했습니다. 새로운 벤딩 솔루션을 이용하게 되면서 신제품에도 적용할 수 있는 막대한 잠재력이 생겨났습니다. 설계 측면에서도 독특한 제품을 개발할 수 있을 정도로 제품개발의 유연성이 크게 높아졌다는 점도 중요합니다.
최적화된 제품 흐름
이 최신 판금 가공 라인의 가장 중요한 특징은 제품 흐름이 끊임없이 이어진다는 점입니다. 즉 생산 공정 대부분을 완전 자동화할 수 있습니다. 펀칭-전단가공 시스템이 판재를 요청하면 로봇이 이를 가공한 후 자재 상자에 보관하거나, 블랭크로 가공하여 판재 블랭크 저장설비로 이송 및 보관합니다. 이후에는 벤딩기와 연결된 전단가공 피딩 시스템이 보관된 부속 중 필요한 것을 요청하며, 이를 자동으로 준비 및 이송하여 투입합니다.
이후 완성된 부속은 조립 라인이나 포장 라인으로 이송되며, 조립이나 포장을 거쳐 완성된 상품은 컨테이너 트롤리로 이송하여 보관합니다. 전체 제조 공정이 진행되는 동안 지게차 등 사람이 직접 제품을 수송하는 과정은 존재하지 않습니다. “완제품 취급 필요성이 낮아 생산 과정에 자재에 긁힘이 발생하지 않음을 보장할 수 있습니다. 우리 회사에서 정한 높은 품질기준을 달성하는 과정에 가장 까다로운 부분이었지요.” 에리히 다너바우어 씨가 인정했습니다. 이어서 막시밀리안 프리글링어 이사가 마무리했습니다. “이렇게 큰 규모의 까다로운 프로젝트가 성공할 수 있게 해 준 시스템 공급자, 미래에도 함께 할 공급자로 Prima Power를 선택하게 되어 대단히 만족스럽습니다.”
With our new production site in Herzogsdorf, we have the most modern sheet metal processing plant in Austria. By selecting Prima Power we are pleased to have chosen a system supplier with whom we were able to successfully handle such a large, challenging project, and who we can continue to rely on in the future.