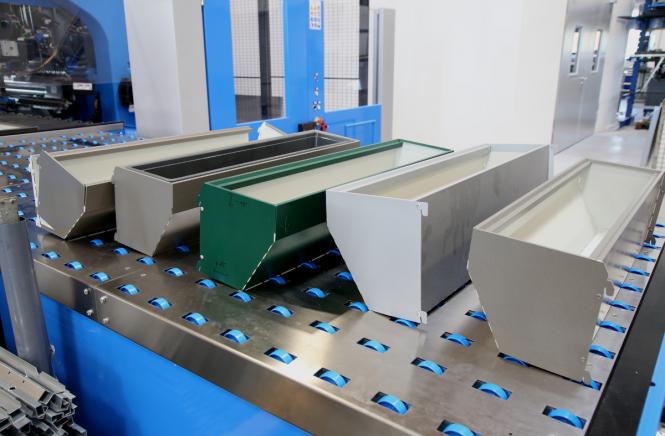
Lyxbearbetning av plåt
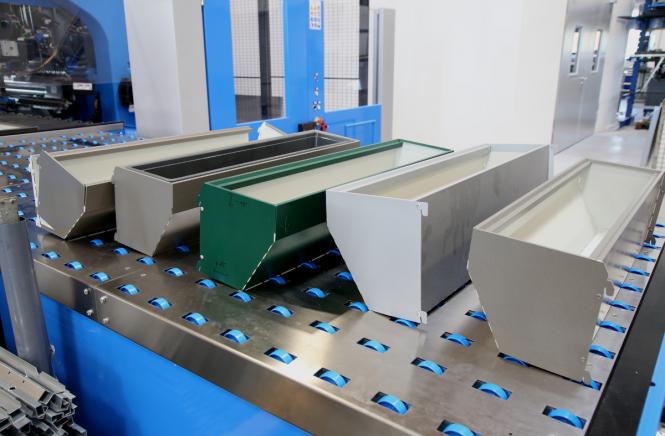
Byggfasen för Biohorts nya tillverkningsanläggning i Herzogsdorf (Oberösterreich) tog drygt ett år. Med banbrytande branschstandarder och optimerade processcykler skapade den här specialisten på lösningar för lagerutrymme nya resurser för ytterligare tillväxt med sin nya Anläggning 2, som är ett tillägg till huvudkontoret i Neufelden.
Resultatet var en anläggning på 12 000 kvadratmeter som har byggts med Prima Powers mest avancerade tillverkningstekniker, med målet att vara ett av Europas mest moderna plåtbearbetningscenter.
Biohort GmbH, med huvudkontor i Neufelden i Oberösterreich, är en av de främsta inom lagringslösningar för metall på den europeiska marknaden. I produktportföljen ingår högkvalitativa verktygsskjul, praktiska förvaringslådor för utomhusbruk och andra användbara detaljer för trädgårdar, som upphöjda odlingsbäddar.
Redan 1995 anförtroddes Dr. Josef Priglinger med att hantera produktionen av förvaringsskjul av metall på den tidigare standardstålanläggningen i Niederwaldkirchen. Två år senare tog han över 100 % av Biohorts andelar inom standardstål. Sedan dess har företaget styrts av Priglinger-familjen, nämligen i ett samarbete mellan far och son, ingenjören Maximilian Priglinger. ”De produkter som våra kunder kommer ha glädje av i årtionden har skapats tack vare sofistikerad design, material av hög kvalitet från certifierade leverantörer och förstklassiga österrikiska bearbetningsstandarder. Därför kan vi på ett ärligt sätt ge 20 års garanti mot korrosion”, förklarar Maximilian Priglinger.
Omgivet av grönska
De två senaste årtiondena har varit en verklig framgångshistoria för Biohort. Men en årlig tillväxt på 15 till 20 % ledde dock till att produktionsavdelningen i Neufelden stod inför ännu större utmaningar, nämligen tillverkningskapaciteten. Man ville förbereda sig inför framtiden och bestämde sig därför 2016 för att bygga en ytterligare produktionsanläggning så att man kunde uppfylla produktionsflödet fullt ut.
Biohort investerade cirka 20 miljoner euro i den nya anläggningen och påbörjade därmed ett nytt strålande kapitel i företagets framgångsberättelse. Det första spadtaget för byggnationen av anläggningen i Herzogsdorf skedde i juli 2017. ”I dag kan vi se resultatet och kan med rätta säga att vi äger den mest moderna anläggningen för plåtbearbetning i Österrike”, säger Priglinger stolt.
Nytänkande i produktionsprocesser
”Planering av anläggningen handlade inte bara om att bygga en ny hall. Tillverkningsprocesserna omarbetades från början till slut och planerades till viss del om. Sedan skapades byggnaden genom att dra nytta av produktionsstegen, i stället för tvärtom. Tack vare de genomströmningsnivåer som har implementerats är processerna extremt effektiva”, säger anläggningschefen Johannes Zauner, en ingenjör som har lett projektet från start.
I oktober förra året inleddes produktionen med Biohorts fritidsförvaringslådor. Planen är att utöka utbudet av produkter gradvis. I nästa steg kommer till exempel produktionen av LoungeBoxes, HighBoards och upphöjda odlingsbäddar att flyttas till Herzogsdorf. ”Vi förväntar oss en årlig bearbetningsvolym på cirka 1 600 ton plåt, vilket motsvarar cirka 50 000 artiklar”, säger Zauner. På anläggningen i Neufelden bearbetas totalt 7 600 ton per år.
Med vår nya produktionsanläggning i Herzogsdorf har vi den mest moderna anläggningen för plåtbearbetning i Österrike. Genom att välja Prima Power hade vi nöjet att hitta en systemleverantör som kan hjälpa oss att hantera ett så stort och utmanande projekt på ett lyckat sätt, och vi kan fortsätta lita på dem i framtiden.
Ing. Maximilian Priglinger, vd för Biohort GmbH
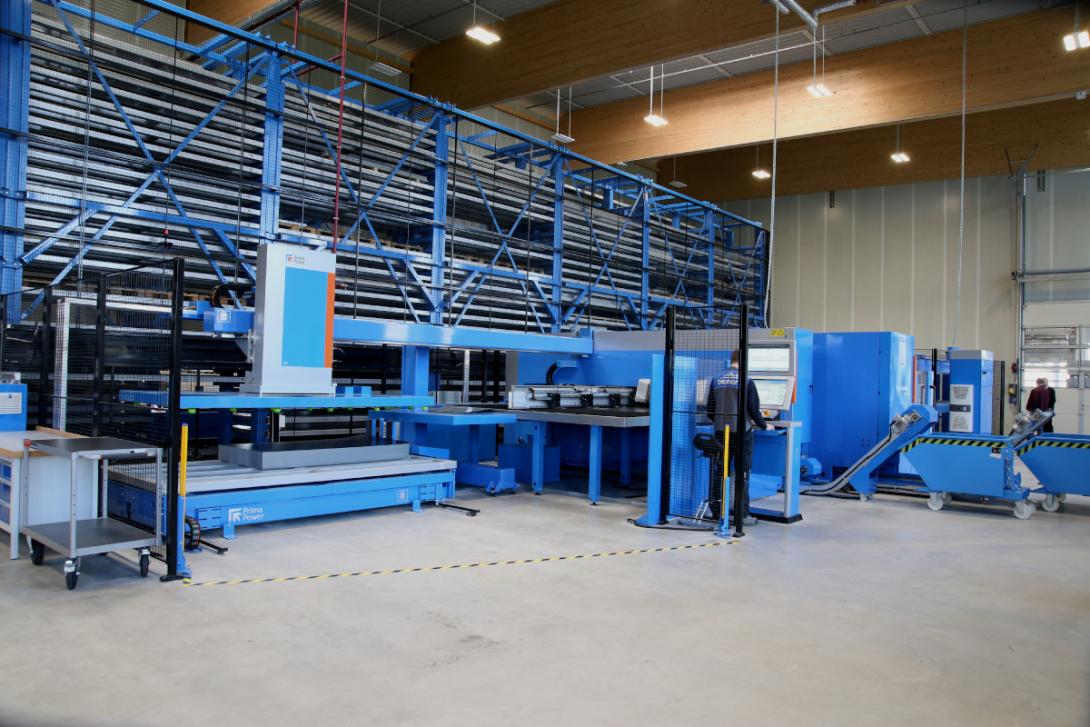
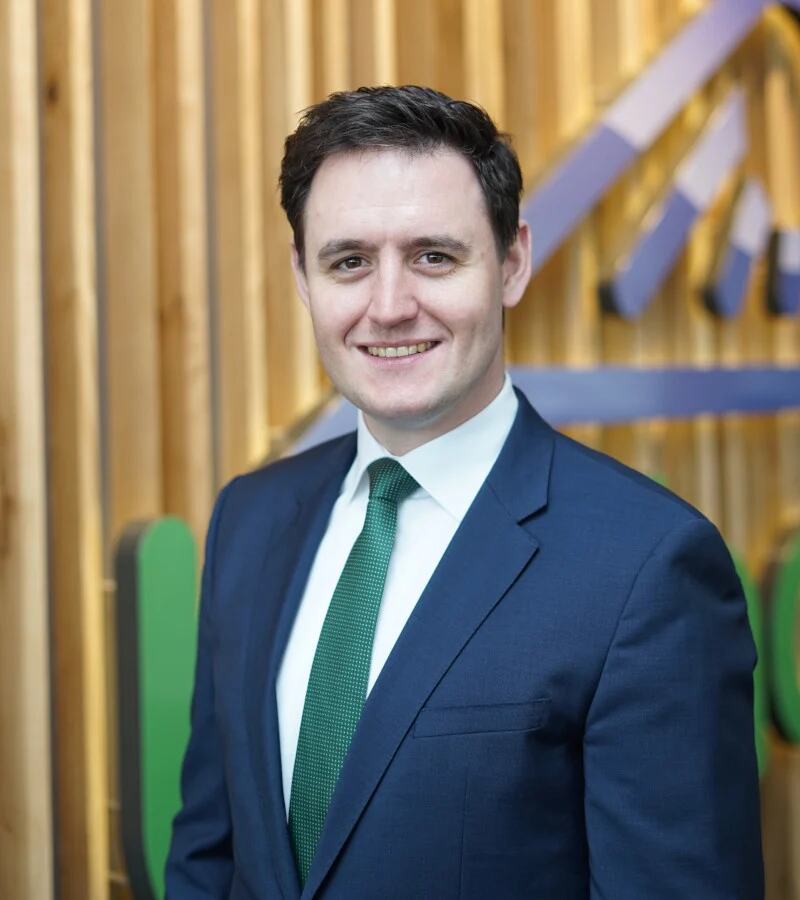
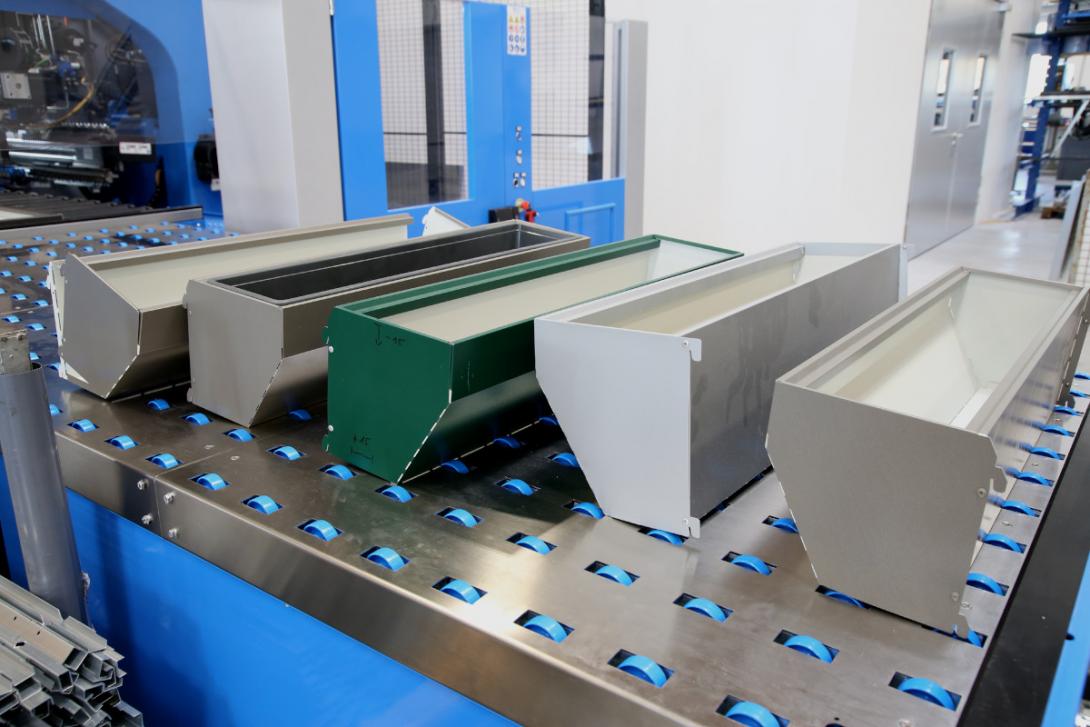
Imponerande teknik för nätverksansluten produktion
En sak var tydlig för de ansvariga redan från början: för att vara säkra på att Biohort skulle lyckas på lång sikt behövde den nya anläggningen förlita sig på innovation och den senaste tekniken. Man genomförde en noggrann jämförelse av leverantörer och efter den låg Prima Power överst på listan tack vare sin helt nätverksanslutna produktionslinje som består av ett helautomatiskt plåtlager, ett kombinerat system för stansning/klippning och en helautomatisk bockningsmaskin. ”Dessutom har Prima Power gjort det möjligt för oss att även integrera tredjepartsmaskiner i systemet. Till exempel kommunicerar vårt robotsystem för klippmatning också med plåtlagret och förses med material”, förklarar Zauner nöjt.
Automatisk materialleverans
Produktionsprocessen börjar med automatisk lagring av råmaterial i det helautomatiska metallagret ”Night Train Brilliance” från Prima Power. Den här anläggningen garanterar inte bara optimal lagring, utan är även kopplad till tillverkningssystemet och överför plåtdelar enligt en fördefinierad tillverkningsprocess. Den 50 meter långa Night Train har 560 platser för förvaringslådor (var och en med en kapacitet på fyra ton) där råmaterial och färdiga råämnen kan lagras. Vid behov kan plåtlagret i Herzogsdorf utökas med ytterligare 30 meter.
För stansning av de detaljer som krävs valde man det kombinerade systemet Shear Genius för stansning/klippning från Prima Power. ”För Biohorts produkter är ett system för stansning och klippning perfekt, eftersom de flesta av de tillverkade komponenterna har en rektangulär grundform. Genom att först stansa och sedan dela upp dessa detaljer i samma process med en integrerad vinkelsax kan vi uppnå den största ekonomiska effektiviteten”, betonar Michael Pröll, Austria Area Manager hos Prima Power.
Repfri stansning och lagring
Dessutom förhindrar maskinens flytande system för plåtar att känsliga ytor repas. ”I det här särskilda stansläget kan plåtarna glida över det upphöjda borstbordet. Vi bearbetar främst varmförzinkade, polyamidemaljerade plåtar med färdig färg och utan skyddsfolie. Därför är det särskilt viktigt att detaljerna går in i produktionen utan några repor”, säger Erich Dannerbauer, vice teknisk chef hos Biohort.
Plock- och staplingsroboten PSR hanterar även materialet extremt försiktigt vid utmatning av maskinen. PSR automatiserar retur av staplar med stansade detaljer till Night Train. ”Beroende på detaljen och de bearbetningssteg som förväntas följa sorterar staplingsroboten detaljerna på ett exakt sätt i respektive förvaringslådor och använder staplingsområdet optimalt”, säger Dannerbauer.
Eftersom flera stansmaskiner från en annan tillverkare används hos Biohort på den stora anläggningen i Neufelden valde Wicam en ej egenutvecklad programvara för stansning. ”Att använda ett enhetligt programmeringssystem för alla stansmaskiner kommer definitivt innebära stora förenklingar i framtiden”, säger Dannerbauer med säkerhet.
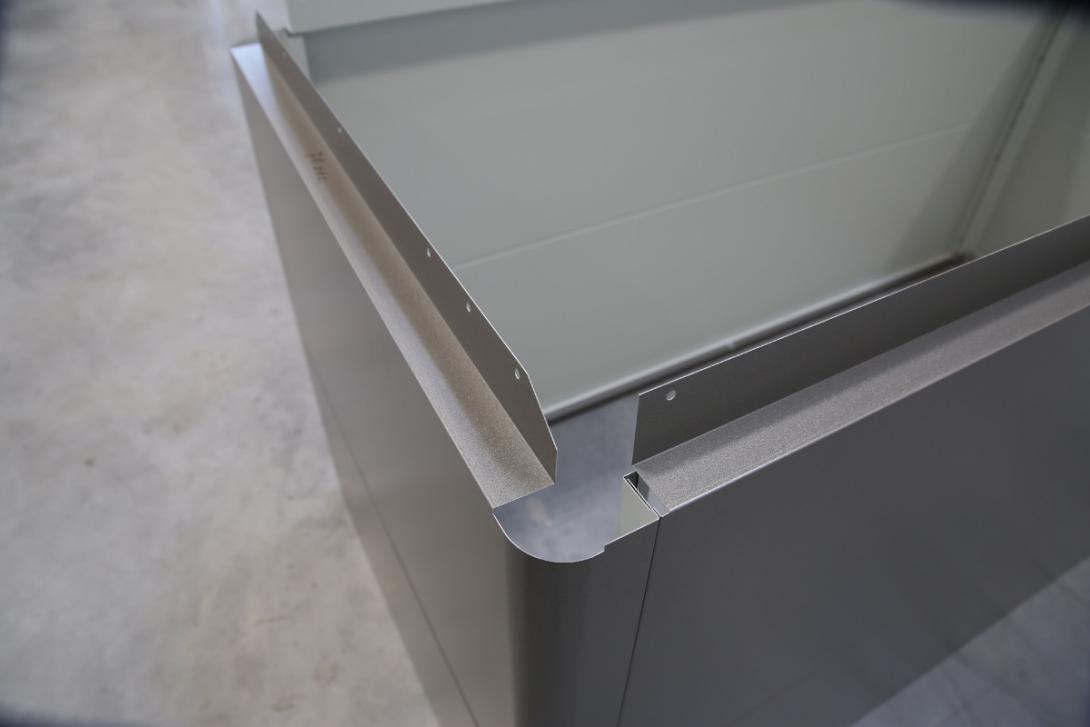
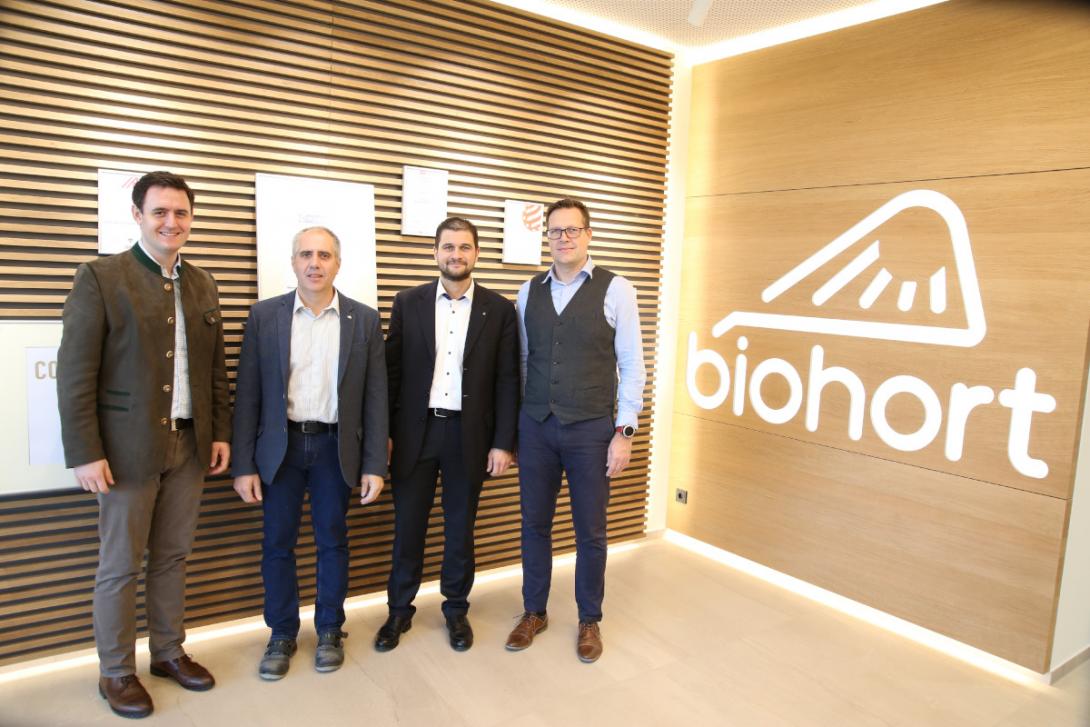
Helautomatisk bockning
På andra sidan av Night Train, bredvid lagringsstationerna för råmaterial, robotmatningssystemet för klippning och en mekanisk kantpress, finns EBe 5.3, en helautomatisk bockningsmaskin från Prima Power. Eftersom den är direkt ansluten till Night Train stöds maskinen även av en PSR-robot för plockning och stapling av råämnen som redan har stansats.
Bockningscellen kan verkligen visa sin styrka, särskilt vid tillverkning av lådor, som hos Biohort. ”Utöver korta ställtider är det även en stor fördel att man kan tillverka alla former, inte bara enkla avfasningar, utan även exempelvis böjda radier. Dessutom går det att göra med bara en verktygsuppsättning. Den kan även snabbt anpassas till olika produktstorlekar”, säger Dannerbauer, som är imponerad av hur effektiv EBe-maskinen är. Allt är även redan förberett för framtida produkter, eftersom det för specialformer, till exempel bockning av laskar, även finns icke-roterande verktyg tillgängliga.
De besparingar som kan uppnås vid detaljtillverkning i förhållande till konventionella mekaniska kantpressar är också värda att notera: ”För mer komplexa detaljer arbetar vi tre till fyra gånger snabbare med bockningsmaskinen. I det här fallet krävs inga tidsödande verktygsbyten, som är fallet med mekaniska kantpressar”, betonar han. Med den nya bockningslösningen finns nu stor potential som kan användas särskilt för nya produkter. Det finns intressanta nya möjligheter för produktutveckling även när det gäller utformning.
Optimerat produktionsflöde
Den verkliga höjdpunkten för denna toppmoderna plåtbearbetningslinje är verkligen det kontinuerliga produktionsflödet, som efter varumottagningen till största delen är helt automatiserat. Metallplåten begärs automatiskt av det kombinerade systemet för stansning och klippning, och när den har bearbetats av en robot placeras den i materiallådan och förvaras i lagret som ett råämne. Därefter begär både bockningsmaskinen och det extra anslutna klippmatningssystemet nödvändiga detaljer från lagret, som sedan förbereds automatiskt.
Därifrån når de färdiga detaljerna monterings- eller paketeringslinjerna och sedan lagret för färdiga varor via behållarvagnar. Utöver detta utförs inga transportaktiviteter, t.ex. sådana som görs av en gaffeltruck, under hela tillverkningsprocessen. ”Vi kan verkligen garantera att material förs in i produktionen utan repor, inte minst tack vare att det krävs så lite hantering för färdiga komponenter. Det var en stor utmaning för våra egna höga kvalitetsstandarder”, medger Erich Dannerbauer. Verkställande direktör Maximilian Priglinger avslutar: ”Genom att välja Prima Power hade vi nöjet att hitta en systemleverantör som kan hjälpa oss att hantera ett så stort och utmanande projekt på ett lyckat sätt, och vi kan fortsätta lita på dem i framtiden.”
Med vår nya produktionsanläggning i Herzogsdorf har vi den mest moderna anläggningen för plåtbearbetning i Österrike. Genom att välja Prima Power hade vi nöjet att hitta en systemleverantör som kan hjälpa oss att hantera ett så stort och utmanande projekt på ett lyckat sätt, och vi kan fortsätta lita på dem i framtiden.
Vill du ha en liknande lösning till ditt företag? Du hittar den här
Night Train FMS®
FLEXIBLA TILLVERKNINGSSYSTEM
Ledande tekniklagerlösning i automatiserade flexibla tillverkningssystem
PSBB
FLEXIBLA TILLVERKNINGSSYSTEM
Ett flexibelt tillverkningssystem
Shear Genius
KOMBINERADE STANS- OCH KLIPPMASKINER