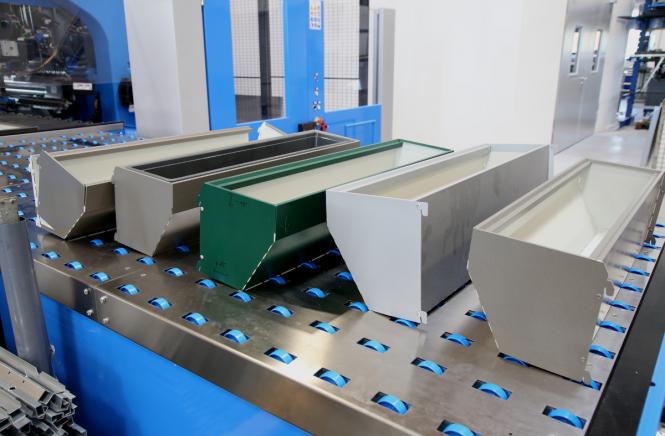
Luxe plaatbewerking
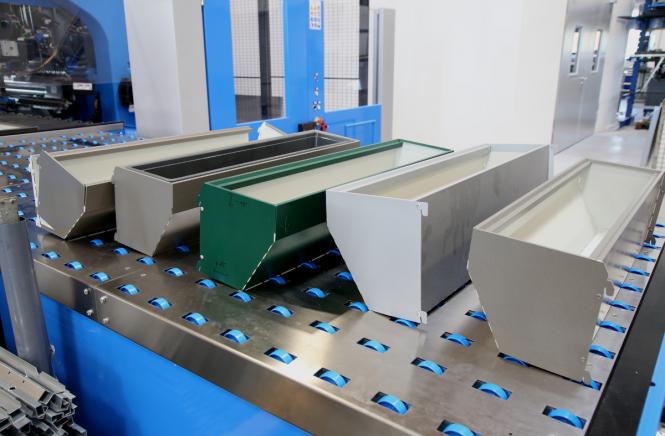
De bouw van de nieuwe Biohort fabriek in Herzogsdorf (Boven-Oostenrijk) duurde iets meer dan een jaar. Met vooruitstrevende industriële normen en geoptimaliseerde procescycli creëerde de specialist in opslagruimte-oplossingen nieuwe middelen voor verdere groei met de nieuwe Fabriek 2, een uitbreiding van zijn hoofdkantoor in Neufelden.
Het resultaat was een terrein van 12.000 vierkante meter dat gebouwd werd met de meest geavanceerde fabricagetechnologieën van Prima Power, om een van de modernste plaatbewerkingscentra van Europa te creëren.
Biohort GmbH, gebaseerd in Neufelden, Upper Austria, is één van de Europese marktleiders in metalen opslagsystemen. Het productassortiment omvat toolhokken van hoge kwaliteit, praktische opbergdozen voor buiten, en andere nuttige tuinaanvullingen zoals verhoogde bedden.
Al in 1995 kreeg Dr. Josef Priglinger de leiding over de productie van metalen opslagloodsen in de voormalige fabriek voor standaardstaal in Niederwaldkirchen. Twee jaar later nam hij de aandelen van Biohort standaardstaal voor 100% over. Sindsdien staat het bedrijf onder beheer van de familie Priglinger, namelijk gezamenlijk geleid door vader en zoon - afgestudeerd ingenieur Maximilian Priglinger. “De producten waarvan onze klanten tientallen jaren zullen genieten, ontstaan dankzij een uitgekiend ontwerp, hoogwaardige materialen van gecertificeerde leveranciers en Oostenrijkse premium verwerkingsnormen. Daarom bieden we, in alle oprechtheid, 20 jaar garantie tegen corrosie,” verklaart Maximilian Priglinger.
Ondergedompeld in groen
De afgelopen twee decennia waren een waar succesverhaal voor Biohort. 15 tot 20% jaarlijkse groei maakte echter dat de productieafdeling in Neufelden voor steeds grotere uitdagingen kwam te staan, ook wat de produktiecapaciteit. Om op de toekomst voorbereid te zijn, werd daarom in 2016 besloten een extra productiefabriek te bouwen op het groene platteland, om volledig aan de productiestromen te kunnen voldoen.
Biohort investeerde ongeveer 20 miljoen euro in de nieuwe vestiging en opende daarmee beslist weer een schitterend hoofdstuk in het succesverhaal van de onderneming. De grondbrekende ceremonie voor de bouw van de fabriek in Herzogsdorf vond plaats in juli 2017. “Vandaag staan we oog in oog met het resultaat en kunnen we met recht zeggen dat we de modernste plaatbewerkingsfabriek in Oostenrijk bezitten,” zei Priglinger met terechte trots.
Heroverweging van productieprocessen
“Bij het plannen van de fabriek ging het niet alleen om het bouwen van een nieuwe hal. De fabricageprocessen werden van begin tot eind opnieuw doordacht en gedeeltelijk opnieuw gepland. Daarna werd het gebouw gebouwd door gebruik te maken van de productiestappen - niet andersom. Als gevolg van de ingevoerde doorvoerniveaus zijn de processen uiterst efficiënt,” meldde fabrieksmanager Johannes Zauner, een afgestudeerd ingenieur die het project vanaf het begin geleid heeft.
Vorig jaar oktober ging de lijnproductie van start met Biohort vrijetijdskisten voor opslag. Het is de bedoeling dat de verscheidenheid aan producten geleidelijk wordt uitgebreid. Als volgende stap zal bijvoorbeeld de productie van LoungeBoxes, HighBoards, en verhoogde bedden naar Herzogsdorf worden overgebracht.“We verwachten een jaarlijks verwerkingsvolume van ongeveer 1.600 ton plaatstaal, wat overeenkomt met ongeveer 50.000 stuks,” zei Zauner. In de vestiging in Neufelden wordt in totaal 7.600 ton per jaar verwerkt.
Met onze nieuwe productievestiging in Herzogsdorf hebben we de modernste plaatbewerkingsfabriek in Oostenrijk. Door Prima Power te kiezen zijn we blij dat we een systeemleverancier gekozen hebben met wie we zo’n groot, uitdagend project met succes konden aanpakken, en op wie we ook in de toekomst kunnen blijven rekenen.
Eng. Maximilian Priglinger, Managing Director van Biohort GmbH
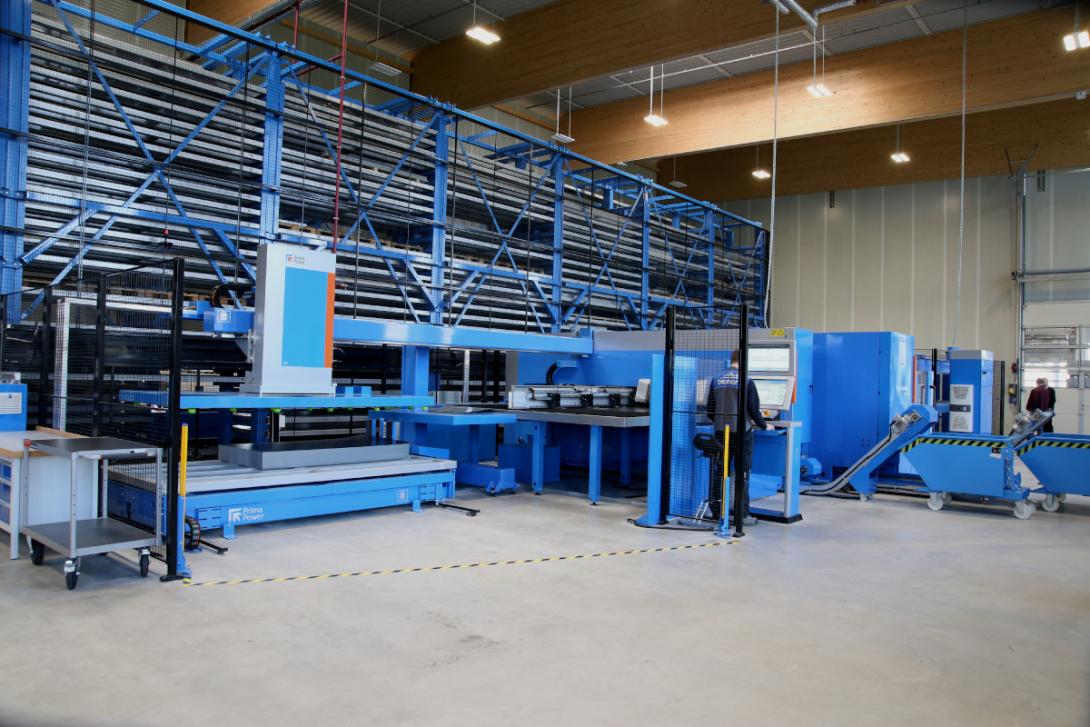
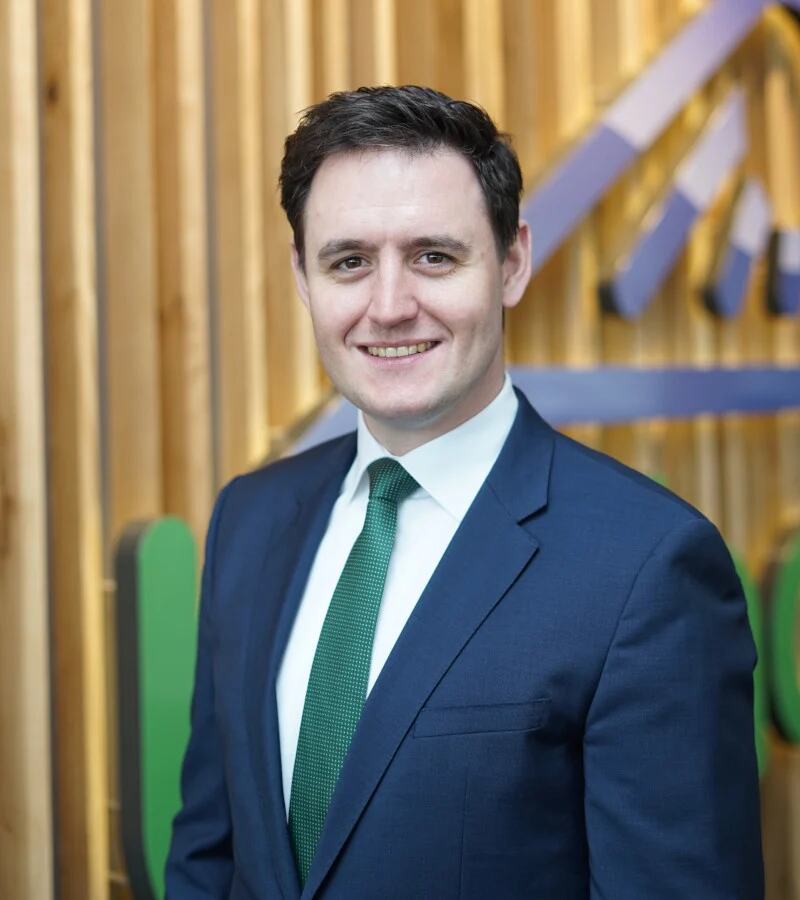
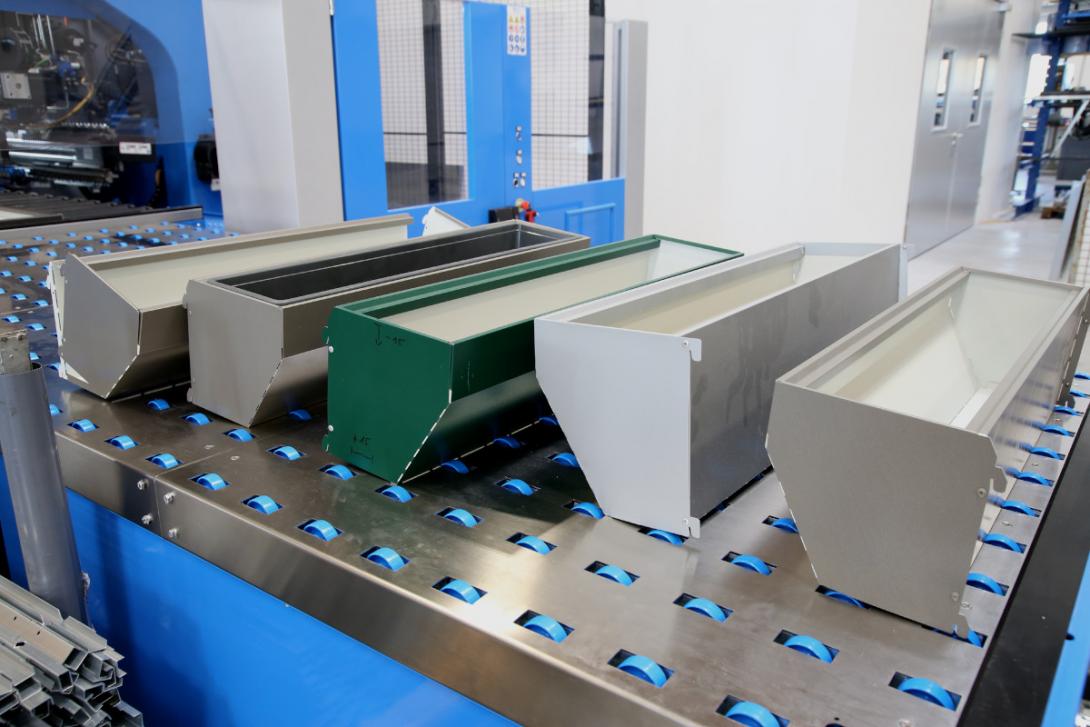
Indrukwekkende genetwerkte productietechnologieën
Eén ding was voor de verantwoordelijken vanaf het begin duidelijk: om het succes van Biohort op lange termijn te verzekeren, moest de nieuwe fabriek steunen op innovatie en de allernieuwste technologie. Na intensief vergelijken van leveranciers kwam Prima Power uiteindelijk als beste uit de bus van de lijst met een volledig genetwerkte productielijn bestaande uit een volautomatisch plaatmagazijn, een pons-schaar combinatie systeem, en een volautomatische buigmachine. “Bovendien heeft Prima Power ons in staat gesteld ook machines van derden in het systeem te integreren. Zo communiceert ons gerobotiseerd schaaraanvoersysteem ook met het plaatwerkmagazijn en wordt van materiaal voorzien,” verklaarde Zauner op tevreden toon.
Automatische materiaaltoevoer
Het productieproces begint met de automatische opslag van grondstoffen in het volautomatische metalen magazijn “Night Train Brilliance” door Prima Power. Deze installatie zorgt niet alleen voor een optimale opslag, maar is ook verbonden met de fabricagesystemen en brengt plaatwerkdelen over volgens een vooraf bepaald fabricageproces. De 50-meter lange Night Train heeft 560 opbergvakjes (elk met een capaciteit van vier ton) waar grondstoffen en afgewerkte stansblokken opgeslagen worden. Indien nodig kan het plaatwerkmagazijn in Herzogsdorf met nog eens 30 meter verlengd worden.
Om de vereiste delen te ponsen werd het Shear Genius pons-schaar combinatiesysteem van Prima Power gekozen. “Voor Biohort producten is een pons- en scheersysteem ideaal, omdat de meeste geproduceerde onderdelen een rechthoekige basisvorm hebben. Door deze onderdelen eerst te ponsen en dan in hetzelfde proces te splitsen met een geïntegreerde rechtshandige knipschaar, kan de grootste economische efficiëntie verkregen worden,” benadrukte Michael Pröll, Area Manager Oostenrijk bij Prima Power.
Krasvrij ponsen en opbergen
Verder, het Sheet Floating System van de machine voorkomt dat gevoelige oppervlakken bekrast worden. “In deze speciale ponsstand kunnen platen over de verhoogde borsteltafel glijden. Wij verwerken hoofdzakelijk thermisch verzinkte gegalvaniseerde, polyamide geëmailleerde steel sheets in finished kleur en zonder beschermfolie. Daarom is het bijzonder belangrijk dat de onderdelen zonder krassen in productie gaan,” zei Erich Dannerbauer, plaatsvervangend Technisch Manager bij Biohort.
De verzamel- en stapelrobot PSR gaat ook bij het lossen van de machine uiterst voorzichtig met de materialen om. De PSR automatiseert de terugkeer van gestanste stapels onderdelen in de Night Train. “Afhankelijk van het onderdeel en van de te verwachten bewerkingsstappen sorteert de stapelrobot de onderdelen nauwkeurig in de respectieve voorraaddozen, waardoor de stapelruimte optimaal benut wordt,” zei Dannerbauer.
Omdat bij Biohort in de hoofdfabriek in Neufelden verschillende ponsmachines van een andere fabrikant in gebruik zijn, werd voor het ponsen niet-propriëtaire programmeersoftware van Wicam gekozen. “Het gebruik van een uniform programmeersysteem voor alle ponsmachines zal in de toekomst zeker een grote vereenvoudiging betekenen,” zei Dannerbauer duidelijk.
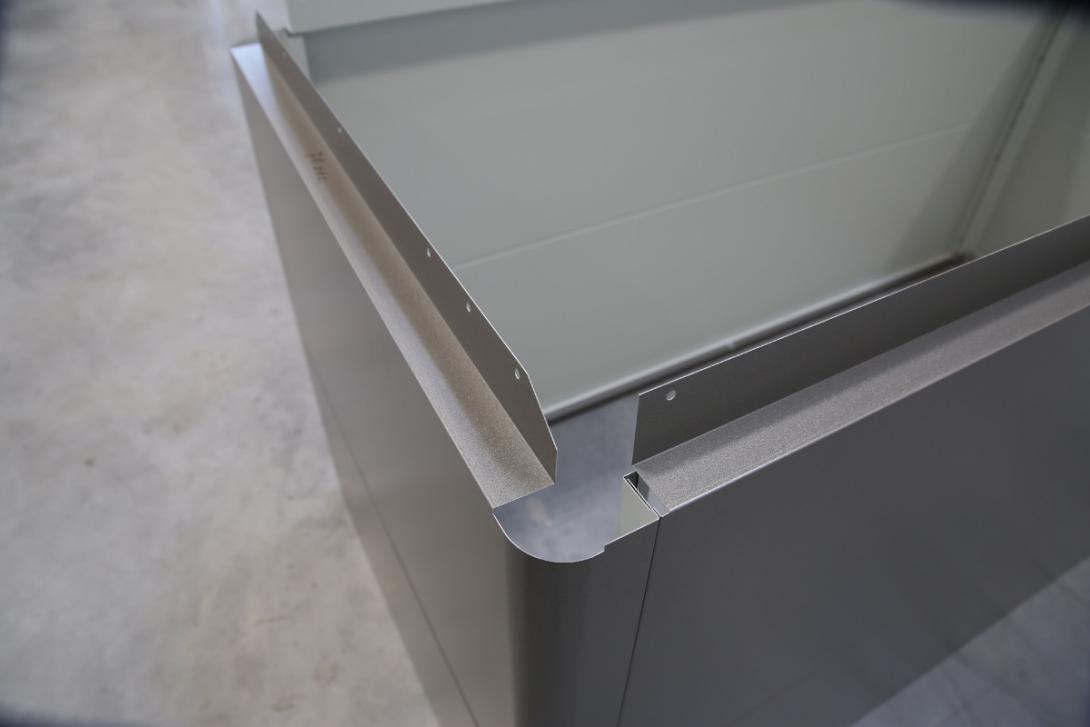
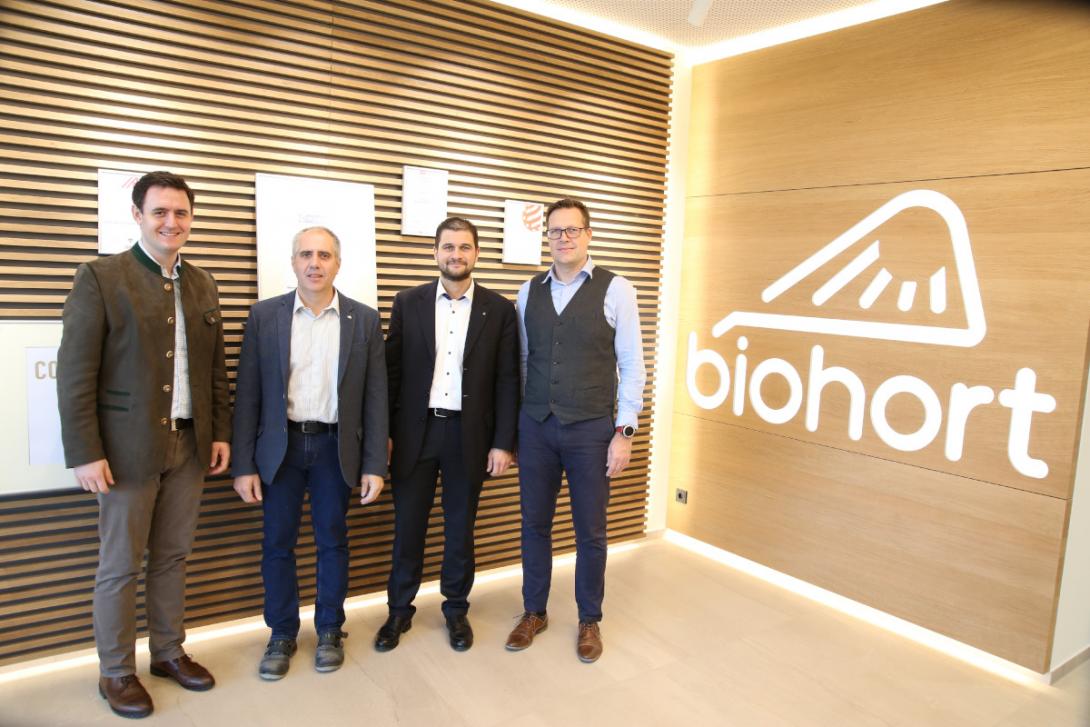
Volautomatisch buigen
Aan de andere kant van de Night Train, naast de opslagstations voor grondstoffen, het robotschaar-voersysteem en een mechanische afkantpers, is er de EBe 5.3, een volautomatische buigmachine van Prima Power. Het is vanzelfsprekend rechtstreeks verbonden met de Night Train, en de machine is ook aangedreven door een PSR pick- en stapelrobot met al geponste plaatblanco’s.
Vooral bij de doosjesfabricage, zoals bij Biohort het geval is, kan de buigcel zijn sterke kanten echt bewijzen. “Behalve korte insteltijden, een groot voordeel is dat je elke vorm kunt maken - niet alleen eenvoudige afschuiningen, maar ook, bijvoorbeeld, buigradii. En dat met slechts één toolset. Bovendien kan hij snel aan verschillende productafmetingen aangepast worden,” zei Dannerbauer, onder de indruk van de doeltreffendheid van de EBe machine. Ook voor toekomstige producten is alles al voorbereid: zoals voor speciale vormen of, bijvoorbeeld, om visplaten te buigen, zijn ook niet-roterende tools beschikbaar.
Opmerkelijk zijn de besparingen bij de productie van onderdelen ten opzichte van conventionele mechanische kantpersen: “Voor complexere onderdelen zijn we drie tot vier keer sneller met de buigmachine. In dit geval is geen tijdrovende toolwissel nodig zoals bij mechanische kantpersen,” benadrukte hij. Met de nieuwe buigoplossing, is er nu een groot potentieel beschikbaar dat vooral voor nieuwe producten gebruikt kan worden. Er zijn interessante nieuwe mogelijkheden voor productontwikkeling, ook wat vormgeving betreft.
Geoptimaliseerde productiestroom
Het absolute hoogtepunt van deze ultramoderne plaatbewerkingslijn is, om het rechtuit te zeggen, de continue productiestroom die, na goederenontvangst, meestal volledig geautomatiseerd is. De metalen plaat wordt automatisch gevraagd door het pons-en-scheer combinatie systeem en, na door een robot bewerkt te zijn, wordt het op de materiaalbak gelegd en als blanco weer in het platenmagazijn opgeslagen. Daarna hebben zowel de buigmachine als het bijkomend aangesloten schuiftoevoersysteem de nodige onderdelen uit het magazijn nodig, die dan automatisch worden klaargelegd.
Van daaruit bereiken de afgewerkte onderdelen de assemblage- of verpakkingslijnen en dan het magazijn voor afgewerkte goederen met behulp van containerwagens. Afgezien daarvan worden tijdens het hele fabricageproces geen transportactiviteiten zoals die van een vorkheftruck uitgevoerd. “We kunnen inderdaad garanderen dat materialen krasvrij in de productie worden gebracht, niet in de laatste plaats vanwege de geringe handling-inspanning die voor afgewerkte onderdelen nodig is. Dat was een grote uitdaging voor onze eigen hoge kwaliteitsnormen,” gaf Erich Dannerbauer toe. En algemeen directeur Maximilian Priglinger besloot: “Door Prima Power te kiezen zijn we blij dat we een systeemleverancier gekozen hebben met wie we zo’n groot, uitdagend project met succes konden aanpakken, en op wie we ook in de toekomst kunnen blijven rekenen.”
Met onze nieuwe productievestiging in Herzogsdorf hebben we de modernste plaatbewerkingsfabriek in Oostenrijk. Door Prima Power te kiezen zijn we blij dat we een systeemleverancier gekozen hebben met wie we zo’n groot, uitdagend project met succes konden aanpakken, en op wie we ook in de toekomst kunnen blijven rekenen.
Ben je op zoek naar een soortgelijke oplossing voor je bedrijf? Hier kun je het vinden
Night Train FMS®
FLEXIBELE PRODUCTIESYSTEMEN
Toonaangevende technologische opslagoplossing in geautomatiseerde flexibele productiesystemen
Shear Genius
PONS- EN SCHEERMACHINES GECOMBINEERD