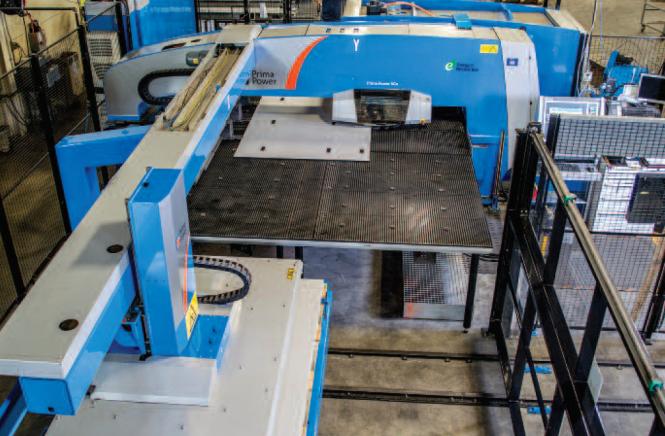
펀치-전단가공 복합기 - 인력 절감
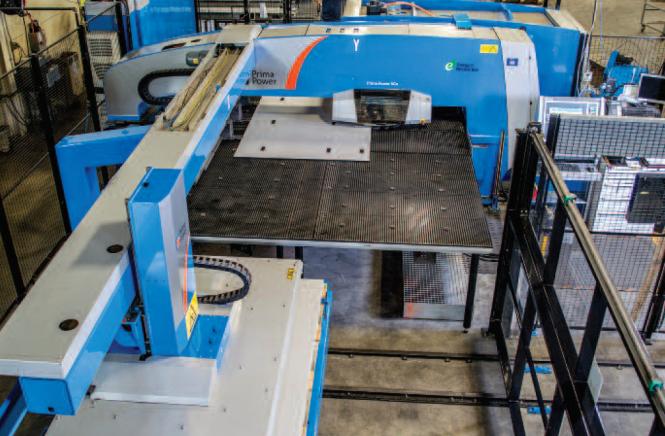
커스텀 도어 제조업체인 LaForce는 새로운 서보 일렉트릭 펀칭-전단가공 복합기를 이용해 판금 부속의 전단가공 및 펀칭 생산량을 세 배 이상 늘렸습니다
커스텀 도어 제조업체인 LaForce는 새로운 서보 일렉트릭 펀칭-전단가공 복합기를 이용해 판금 부속의 전단가공 및 펀칭 생산량을 세 배 이상 늘렸습니다
1954년 조 라포스 (Joe Laforce)는 위스콘신 주 그린 베이에서 평범한 철물점을 인수하며 사업을 시작했습니다. 지금 그의 회사 LaForce는 상업용 도어, 프레임, 철물 및 건물용 기재를 유통하는 미국 내 최대 규모의 기업 중 하나로 자리잡았습니다. LaForce의 제품은 다양한 사무용 건물, 의료보건 시설, 병원, 양로원, 의원, 학교, 소매시설, 스포츠 경기장 등에서 찾아볼 수 있습니다.
LaForce는 그린 베이 본사를 그대로 유지하고 있으며, 미국 내에서 11개 시설을 운영하며 맞춤형 도어와 프레임을 생산하고, 제품 설치, 설치 전 시험, 프리피니시, 보안시설 통합, 사양 작성, 방화문 점검, 주요 시스템 서비스 등을 제공하고 있습니다. 12개 시설에서 근무하는 직원의 수는 약 500여 명입니다.
LaForce는 초창기에는 주로 유통업체로 활동했습니다. 1969년 라포스 사장은 제품의 일정한 품질을 보장하고, 시간을 맞추어 납품하기 위해서는 자체적으로 도어와 프레임을 생산해야 할 필요가 있음을 느끼게 되었습니다. 이에 따라 제품의 제작 및 벤딩 가공을 진행하기 위해 두 대의 터렛 펀치 프레스와 두 대의 유압식 전단가공기, 일곱 대의 프레스 브레이크를 도입했습니다.
2013년이 되어 LaForce는 310,000 ft2 면적의 본사 시설에서 제품을 더욱 효율적이고 생산적인 방식으로 제작하기 위한 방안을 탐구하기 시작했습니다.
산업기사? 겸 지속발전 코디네이터로 근무하는 브래드 존슨 (Brad Johnson)이 설명합니다. “이전까지는 블랭크를 제작하기 위해서 판재를 전단가공한 후, 블랭크를 펀칭 가공하여 부속을 생산했습니다. 때문에 자재 취급과 생산성과 무관한 노동에 낭비되는 시간을 줄일 방안을 찾아야 했습니다.”
LaForce는 오랜 시간 연구한 끝에 서보 일렉트릭 펀치-전단가공 복합기를 도입하기로 했습니다 (Prima Power Shear Genius SGe, 2013년 말 도입)
판재의 변환
펀치-전단가공 개념을 사용해 풀 사이즈의 판재를 완성 부품으로 변환할 수 있는 설비를 공급하는 것이 목표입니다. 만들어진 부속은 최종 생산 단계로 넘어가 최종 제품 조립 과정에 바로 투입할 수 있습니다.
LaForce에서 운용하는 Shear Genius SGe의 심장은 최대 분당 1,000회 펀칭 가공을 수행할 수 있으며, 인덱스 속도 250 rpm, 최대 시트 위치조정 속도 분당 150 m에 달하는 서보 일렉트릭 30톤 펀칭기입니다. 설비의 직각 전단가공 기능은 신속한 전단 움직임을 가능케 하며, 완전히 CNC로 제어되는 서보 일렉트릭 구동 시스템으로 가동됩니다. 최대 5 ㎜ 두께의 알루미늄 판재, 최대 4 ㎜ 두께의 연강, 3 ㎜ 두께의 스테인리스강을 전단 가공할 수 있습니다.
설비에는 자동화 판재 로딩 기능과 프로그래밍 가능한 자동화 부속 제거 및 분류 기능이 탑재되어 있습니다. 여기에 존슨 씨는 모든 자동화 기능의 설정 및 준비 시간이 대단히 짧고, 야간에도 무인으로 가동할 수 있어 완제품을 만드는 과정에 인력 투입이나 폐기물의 발새잉 크게 줄어들었다고 설명했습니다.
LaForce는 또한 펀치-전단가공 복합기를 이용하면 부속 테두리를 니블링 가공하는 대신 전단가공하게 되어 가공 후 폐기물이나 비용 부담이 큰 디버링과 같은 2차 작업이 불필요하게 된다는 점도 알게 되었습니다. 설비가 가동되는 동안에는 사람의 개입 없이도 자동으로 판재가 로딩되며, 위치도 조정됩니다. 그리고 펀칭 가공 중 시트를 고정하는 클램프가 전단가공 중에도 그대로 시트를 고정합니다. 독립형 터렛 펀치 프레스에 비해 SGe 설비는 평균적으로 제조에 소요되는 전체 시간을 약 60% 줄였습니다.
존슨 씨가 설명했습니다. “2013년에는 주 평균 2209개의 부속을 생산했습니다 (3개의 개별 설비를 이용하여 135인시를 들여 전단가공/펀칭 가공으로 생산한 부속). 현재는 부속 생산에 SGe만 투입하여 평균적으로 1주일에 48인시를 들여 2630개의 부속을 생산하고 있습니다. 우리 부속을 생산하는 데에 사용되는 전단가공 및 펀칭 가공의 생산성이 인시당 부속 16개에서 인시당 부속 55개로 늘어난 것입니다. 생산성이 145% 향상된 것과 동등합니다.”
펀치-전단가공기는 LaForce 제품의 품질도 크게 개선했습니다. 존슨 씨가 이에 대해 설명했습니다. “이전에는 블랭크 전단가공 후 터렛 펀칭으로 가공하는 과정에 부속별 편차가 발생해 품질 문제를 겪을 때가 있었습니다. SGe를 도입한 이후에는 부속의 품질과 수치가 정확하고 균일하게 유지되면서 품질 문제도 사라졌습니다. 설비 정확성이 높은 덕분에 Sge의 높은 수치 정확성을 바탕으로 프레스 브레이크 가공 시 준비 시간이 짧아졌고, 용접 과정에도 부속 가접이 더욱 쉬워지면서 다른 공정에서도 시간과 노동력을 절약할 수 있게 되었습니다.”
지켜지는 약속
존슨 사장이 말합니다. “SGe는 우리가 기대했던 바를 충실하게 수행하고 있습니다. 우리는 이 설비를 도입하기 전 면밀한 검토와 조사를 여러 차례 진행했습니다. 처음에는 레이저 커팅 설비를 도입하려 했고, 때문에 많은 사람들이 파이버 레이저 설비가 우리에게 필요하다고 설득하려 시도했습니다.” 존슨 사장이 설명을 이었습니다. “하지만 우리가 생산하는 부속은 주로 긴 직사각형 형태였습니다. 곡선이나 원형은 없었지요. 별도의 블랭킹 공정 단계를 없애고 판재 전체를 공유선 커팅 (Common-line cutting) 방식으로 가공할 수 있는 솔루션을 찾고 싶었습니다. 그리고 펀치-전단가공 설비가 가장 적절한 설비였습니다.”
“결과적으로 원래 보유하고 있던 터렛 펀치 프레스와 전단가공기 중 각각 한 대씩을 매각했습니다. 나머지 터렛 프레스와 전단가공기는 만약을 대비한 예비 설비로 보유한 상태입니다. 도입한 설비는 우리가 해결할 문제 중 부속의 전단가공과 펀칭 가공 문제를 해결했습니다. 다음 단계는 성형 및 스팟 용접 공정을 검토하는 것입니다.”
펀칭-전단가공 복합기는 불필요한 노동력을 절감하고 수치 공차를 개선할 수 있습니다. 동시에 판금 제작 생산성을 향상시키기 위한 다양한 특성도 보유하고 있습니다.
이러한 특성 중 대표적인 것은 다음과 같습니다.
툴 홀더 유연성—독립혁 툴 홀더를 통해 제작자가 터렛에 툴 스테이션을 결합하는 대신 자체 터렛 레이아웃을 설계할 수 있도록 합니다.
자동 인덱싱—펀칭기와 다이가 툴 홀더 내에서 프로그래밍 가능한 0.001도 단위로 회전하며, 360도 이상의 각도로 회전할 수 있어 프로그램된 각도로 신속하게 이동할 수 있습니다.
상향 성형—상향 성형은 16 ㎜까지 정확한 성형이 가능하도록 합니다. 또한 모든 다이가 같은 높이에 위치하여 소재가 손상될 위험을 최소화하고 설비의 가동시간을 극대화합니다.
In 2013, we averaged 2209 parts per week utilizing three different machines and 135 manhours. Today, just using the SGe we produce an average of 2630 parts per week using just 48 manhours. The process went from 16 parts/man-hour to 55 parts/man-hour: that’s a 145% improvement!
통합 전문성
고객 중심 접근 방식
고속의 유연한 솔루션
지속가능개발을 위한 우리 회사의 접근법입니다. 지구에 끼치는 우리의 영향을 줄이는 것 또한 경제적 효과가 있습니다. 더 알아보기
우리 회사는 전 세계에서 활동합니다. 가장 가까운 Prima Power 사무실을 찾아 연락해보십시오.
© PRIMA INDUSTRIE S.p.A., single-member company | Via Torino-Pianezza, 36 - 10093 COLLEGNO (TO) ITALIA | Share Capital €26.208.185 | VAT 03736080015 - C.C.I.A.A. Torino 582421 | Reg. Impr. Torino n. 03736080015