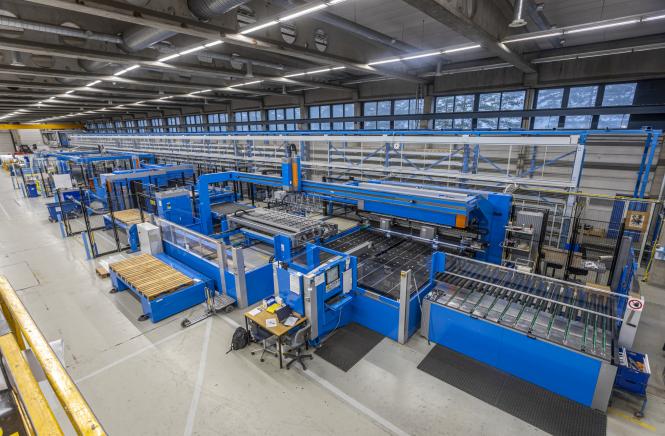
Neue Investitionen schaffen Produktivität in der Halton-Fabrik Kausala
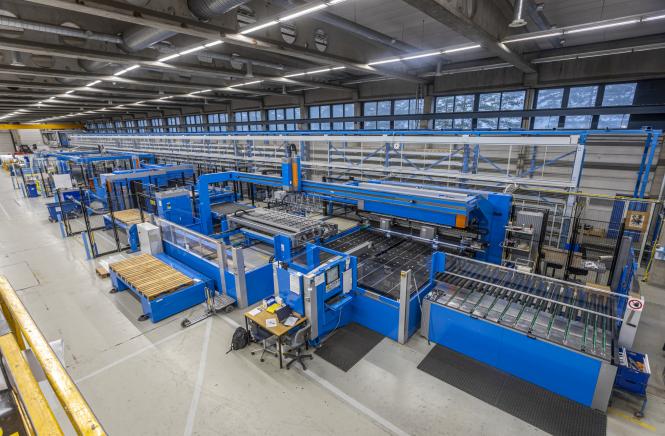
Die Halton Group ist der weltweit führende Anbieter von Raumluftlösungen. Raumluftlösungen sind in vier Segmente unterteilt: Marine, Gesundheit, Lebensmittel und Gebäude.
Die Halton Group ist der weltweit führende Anbieter von Raumluftlösungen. Raumluftlösungen sind in vier Segmente unterteilt: Marine, Gesundheit, Lebensmittel und Gebäude.
Das Unternehmen ist im Besitz der Familie Halttunen und hat seinen Hauptsitz in Helsinki. Neben Finnland verfügt das Unternehmen derzeit über Produktionsstätten in Frankreich, Deutschland, Großbritannien, den Vereinigten Staaten, Kanada, China und Malaysia. In acht dieser Länder unterhält das Unternehmen auch Einrichtungen für Forschung und Produktentwicklung. Halton stellt auch Produkte unter Lizenz in Südafrika, Mexiko, Neuseeland und Australien her. Die Halton Group beschäftigt rund 1.550 Mitarbeiter in über 30 Ländern. Der Umsatz des Unternehmens lag 2018 bei rund 218 Millionen Euro. Halton hat die Produktivität des Unternehmens, die Kosten und den Wert seiner Produkte für die Kunden immer genau überwacht. Das Unternehmen hat Wachstum im Visier, und ein wichtiger Faktor für Wachstum ist eine kosteneffiziente Blechfertigung, die bei Bedarf weltweit skaliert werden kann. Das Unternehmen wollte eine Partnerschaft mit einem globalen Maschinenlieferanten eingehen, der dieses Wachstum ermöglichen konnte.
In Finnland ist Prima Power schon seit langem Haltons Partner im Werk Kausala.
„Wir hatten bereits 2007 in das aktuelle automatische Lagersystem Night Train investiert. Damals wurden zwei Stanzmaschinen/Winkelscheren und ein Biegezentrum in das System integriert, und die Investition hat sich innerhalb von 18 Monaten amortisiert.“
Einsparungen und Effizienz aus mehreren Blickwinkeln
Die Einsparungen wurden durch die Minimierung des Längenverlusts der Coil-Linie und die Ausnutzung der Einkaufspreise von Coil-Material im Vergleich zu Blechmaterial erzielt. Darüber hinaus bedeutete die Effizienz der Winkelschere, dass mehr Teile verschachtelt werden konnten, das Volumen des Blechrahmens minimiert und die Bearbeitungszeit der Maschine für Bleche optimiert und verkürzt werden konnte. Auch die Qualität der Teile und ihre Leistung bei der Montage verbesserten sich deutlich, da die von der Revolverstanze hinterlassenen Späneabdrücke verschwanden, als wir die Winkelschertechnologie einführten.
Die Antwort auf die Frage, ob es sich lohnt, in die Automatisierung zu investieren und Night Train Lagerautomation und Winkelscheren einzusetzen, lag auf der Hand:
„Das war es definitiv. Bei unserer derzeitigen Kapazität bräuchten wir wahrscheinlich fünf eigenständige Maschinen und für jede von ihnen separate Bediener für jede Schicht, um unsere beiden Winkelscheren zu ersetzen. Daher würden wir insgesamt 15 Arbeiter benötigen, um fünf Maschinen in drei Schichten zu bedienen. Außerdem bräuchten wir für jede der Schichten einen Gabelstaplerfahrer, um die Bleche von einem Ort zum anderen zu transportieren. Fünf eigenständige Maschinen würden auch einzelne Werkzeuge erfordern, was bedeutet, dass die Werkzeugkosten im Vergleich zu unserer aktuellen Situation enorm wären. Wir hätten weder unser heutiges Niveau der Lagerplatzeinsparung erreicht, noch hätten wir die erforderlichen Bestände vorrätig. Die Bleche und Teile bleiben im Lager, und wir kennen jederzeit ihren genauen Bestand. Außerdem wird unser Rohmaterial in den Lagerregalen nicht beschädigt, und unsere Produktionsstätten werden sauber gehalten. Wir sind mit den Vorteilen des Night Train Lagersystems und der Winkelscheren sehr zufrieden. Ohne sie könnten wir unsere aktuellen Teilemengen nicht bewältigen“, sagt Kari Virkki, Leiter der Produktionstechnik.
Wir sind mit den Vorteilen des Night Train Lagersystems und der Winkelschere sehr zufrieden. Ohne sie könnten wir unser aktuelles Teilevolumen nicht mehr bewältigen.
KOMBINIERTE MASCHINEN ZUM STANZEN UND SCHEREN
FLEXIBLE FERTIGUNGSSYSTEME
Kompetenz in Integration
Kundenorientierter Ansatz
Flexible
Hochgeschwindig
keitslösungen
Ein integriertes und pragmatisches Engagement.
Wir sind auf der ganzen Welt tätig: Finden Sie die Prima Power Vertriebs- und Serviceniederlassung in Ihrer Nähe und kontaktieren Sie uns.
© PRIMA INDUSTRIE S.p.A., single-member company | Via Torino-Pianezza, 36 - 10093 COLLEGNO (TO) ITALIA | Share Capital €26.208.185 | VAT 03736080015 - C.C.I.A.A. Torino 582421 | Reg. Impr. Torino n. 03736080015