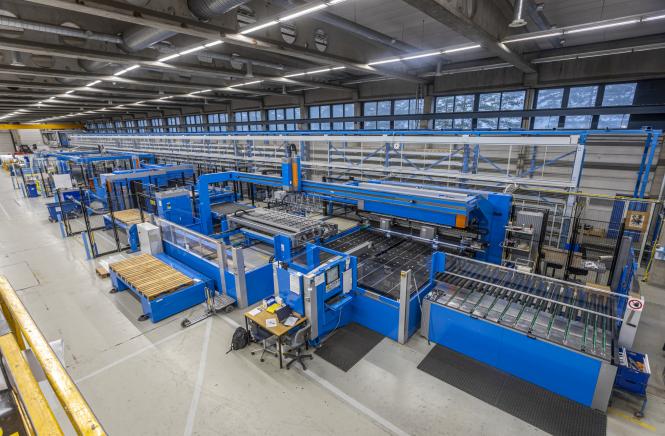
Nya investeringar skapar produktivitet på Haltons fabrik i Kausala
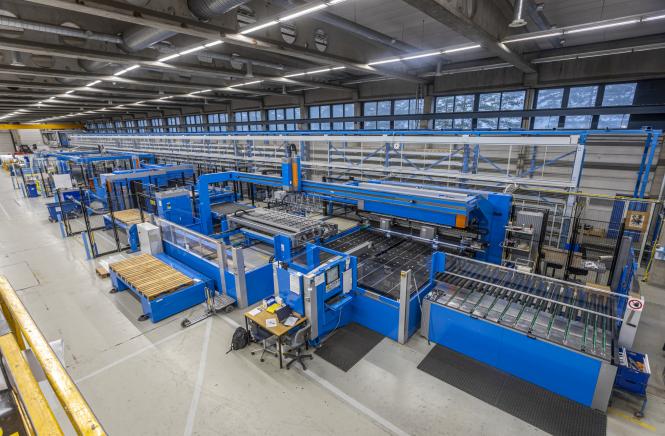
Halton-koncernen är världens främsta leverantör av lösningar för inomhusluft. Lösningar för inomhusluft är indelade i fyra segment: Marint, hälsa, livsmedel och byggnader
Halton-koncernen är världens främsta leverantör av lösningar för inomhusluft. Lösningar för inomhusluft är indelade i fyra segment: Marint, hälsa, livsmedel och byggnader
Halton-koncernen är världens främsta leverantör av lösningar för inomhusluft. Lösningar för inomhusluft är indelade i fyra segment: Marint, hälsa, livsmedel och byggnader. Företaget ägs av familjen Halttunen och har sitt huvudkontor i Helsingfors. Förutom i Finland har företaget för närvarande produktionsanläggningar i Frankrike, Tyskland, Storbritannien, USA, Kanada, Kina och Malaysia. I åtta av dessa länder har företaget också anläggningar för forskning och produktutveckling. Halton tillverkar även produkter under licens i Sydafrika, Mexiko, Nya Zeeland och Australien. Halton-koncernen har cirka 1 550 anställda i över 30 länder. Företagets omsättning år 2018 var cirka 218 miljoner euro. Halton har alltid hållit ett noggrant öga på företagets produktivitet, kostnader och det värde som produkterna ger kunderna. Man strävar efter tillväxt och en stor faktor för att uppnå detta är kostnadseffektiv plåtproduktion som kan skalas upp över hela världen vid behov. Företaget ville samarbeta med en global maskinleverantör som skulle kunna underlätta denna tillväxt.
I Finland har Prima Power länge varit Haltons partner på fabriken i Kausala.
”Vi investerade redan 2007 i det befintliga automatiserade lagersystemet, Night Train. Då ingick två stansmaskiner/vinkelsaxar och ett bockningscenter i systemet, och investeringen hade betalat sig inom 18 månader.”
Besparingar och effektivitet ur flera vinklar
Besparingarna uppnåddes genom att minimera förlusten av rullinjens längd och kapitalisera på inköpskostnaderna för rullmaterial jämfört med plåtmaterial. Dessutom innebar den effektiva vinkelsaxen att fler detaljer kunde föras till nestningen, plåtramens volym kunde minimeras och maskinbearbetningstiden för plåtar kan optimeras och förkortas. Dessutom förbättrades detaljernas kvalitet och prestanda under monteringen avsevärt, eftersom de märken som efterlämnas av revolverstansmaskinen försvann när vi införde vinkelsaxtekniken.
Svaret på frågan om det var värt att investera i automatisering och använda lagerautomatisering med Night Train och vinkelsaxar var självklart:
Vi är mycket nöjda med de fördelar vi fått från Night Train-lagringssystemet och vinkelsaxarna. Vi hade inte kunnat hålla jämna steg med våra nuvarande detaljvolymer utan dessa.
FLEXIBLA TILLVERKNINGSSYSTEM
KOMBINERADE STANS- OCH KLIPPMASKINER
FLEXIBLA TILLVERKNINGSSYSTEM
Expertis inom integration
Kundfokuserad strategi
Snabba, flexibla lösningar
© PRIMA INDUSTRIE S.p.A., single-member company | Via Torino-Pianezza, 36 - 10093 COLLEGNO (TO) ITALIA | Share Capital €26.208.185 | VAT 03736080015 - C.C.I.A.A. Torino 582421 | Reg. Impr. Torino n. 03736080015