
Bästa prestanda

Laserlam har över tio års erfarenhet av laserskärning och plåtbockning. Man arbetar ständigt med nya lösningar för att öka produktiviteten, till exempel Prima Powers nya 2D Laser Genius+.
Fördubblad produktivitet, avancerade processer, Industry 4.0-prestanda på hög nivå och kompakt storlek, enkel installation och service. Det här är den nya 2D-lasermaskinen Laser Genius+, som har utformats och tillverkats av Prima Power och den körs för närvarande hos Laserlam S.r.l. Maskinen har nyligen genomgått en testningsperiod som de två företagen kom överens om, i syfte att utvärdera de kompletta funktionerna innan den lanseras officiellt på marknaden. Testet utfördes av företaget från Orbassano (TO) på grund av dess betydande erfarenhet som kommer från att ha arbetat med tillverkning i över tio år. Laserlam startades 2008 av de tre grundarna Carlo Ferraro, Bertrand Luchino och Giovanni Luca Davito Gara, som var yrkespersoner med omfattande och samlad erfarenhet inom plåtsektorn.
Utveckling som håller jämna steg med marknadens krav
Laserlam har gått från att vara en ren underleverantör som fokuserat på laserskärning och bockning, till att öka sina kunskaper för att kunna tillhandahålla en komplett tjänst, från materialval till svetsning, och från mekanisk bearbetning till värmebehandlingar, för att bli ledande på marknaden tack vare sin produktkvalitet. Företaget har i dag cirka 30 medarbetare inom fyra produktionsområden, som analyserar och utvecklar krav för att ta fram ett prisvärt erbjudande som är så exakt och konkurrenskraftigt som möjligt. Därefter följer produktionen som slutar med leverans av en komplett produkt med korta ledtider, tack vare den mycket dynamiska produktionsmodellen som är utspridd över flera dagskift, där ett antal maskiner och leverantörer finns tillgängliga för varje enskild process. Tack vare sina investeringar i forskning och utveckling, kombinerat med samarbeten man har byggt upp genom åren, kan företaget från Turin nu uppfylla de mest varierande kraven inom tillverkningssektorn. Man säkerställer produkter och tjänster av hög kvalitet, till viss del tack vare de ISO 9001:2008- och ISO 14001:2004-certifieringar man fick 2010. ”Om vårt mål för 2008 var att skära och bocka plåt handlar vår metod i dag om att täcka hela produktionscykeln, från att ta emot kundens design till att skapa en färdig produkt, komplett med värmebehandlingar. Vi arbetar med många olika företag, från hantverkare till stora fordonstillverkare, och med volymer som sträcker sig från en enda enhet upp till miljontals artiklar, även om genomsnittet är 25–30 enheter per beställning”, förklarar Giovanni Davito, försäljningschef för Laserlam S.r.l. ”Vår verkliga styrka ligger i att vi kan tillhandahålla en tjänst som sträcker sig bortom den enskilda artikeln – allt som börjar med plåt och som kan framställas med laser och en bockningsmaskin hanteras smidigt inom mycket snäva tidsramar.” Detta var en reaktion på en marknad som förändrades efter finanskrisen 2008/2009 så att dynamiken blev helt annorlunda än det man var van vid inom tillverkningssektorn. Kunderna kräver i allt högre grad en komplett tjänst, eftersom de inte vill behöva hantera lagerlokaler eller flera olika leverantörer, utan föredrar att ha kontakt med ett enda företag som kan tillhandahålla färdiga lösningar. ”I dag förser 80 % av företagen oss med projektspecifikationer, men vi hanterar införskaffande av material, som vi alltid har i lager för att kunna reagera snabbt när en order kommer in. Med tanke på att vi för närvarande producerar omkring 2 000 nya koder per månad är det lätt att förstå vilken komplex logistik som krävs, och vi lägger mycket energi och resurser på detta”, tillägger han. ”I ett mer allmänt avseende hanteras hela produktionsprocessen av programvara som ansvarar för att generera koder till nya produkter, bearbeta det inledande materialet, nestning och maskindrift, och identifiera produktionstider med tanke på Industry 4.0. På så sätt kan vi följa alla faser som leder till den färdiga produkten, vilket gör att vi kan spåra all information vi behöver om det skulle uppstå problem.” Om man ser till produktionen har Laserlam två laserskärningssystem ur den senaste generationen, två kantpressar (en 40-tons elektrisk kantpress och en 250-tons hydraulisk kantpress) och man kommer snart lägga till en hP 1630 från Prima Power, samt sju svetsstationer. Dessutom har man en serie verktygsmaskiner för mindre bearbetning, som gängning, borrning, trumling och tvättning av delar, som används för att färdigställa kundens order utan att öka leveranstiderna. ”För att kunna uppfylla de förändrade behoven inom sektorn behövde vi erbjuda produkter av genomgående hög kvalitet, samtidigt som vi sänkte kostnaderna för el, gas och tryckluft, som var så höga med vår CO2-laser att det inte var hållbart. Dessutom behövde vi ett lasersystem att ersätta vårt nuvarande med som kunde öka prestandan med hjälp av fiberteknik”, tillägger Bertrand Luchino, Laserlams chef för produktion, kvalitet, inköp och logistik. ”Eftersom vi redan hade installerat ett Platino Fiber-lasersystem från Prima Power som vi var mycket nöjda med bestämde vi oss för att acceptera deras erbjudande, eftersom de behövde testa sin nya Laser Genius+ i ett företag som arbetade hårt med olika tjocklekar och många olika material.”
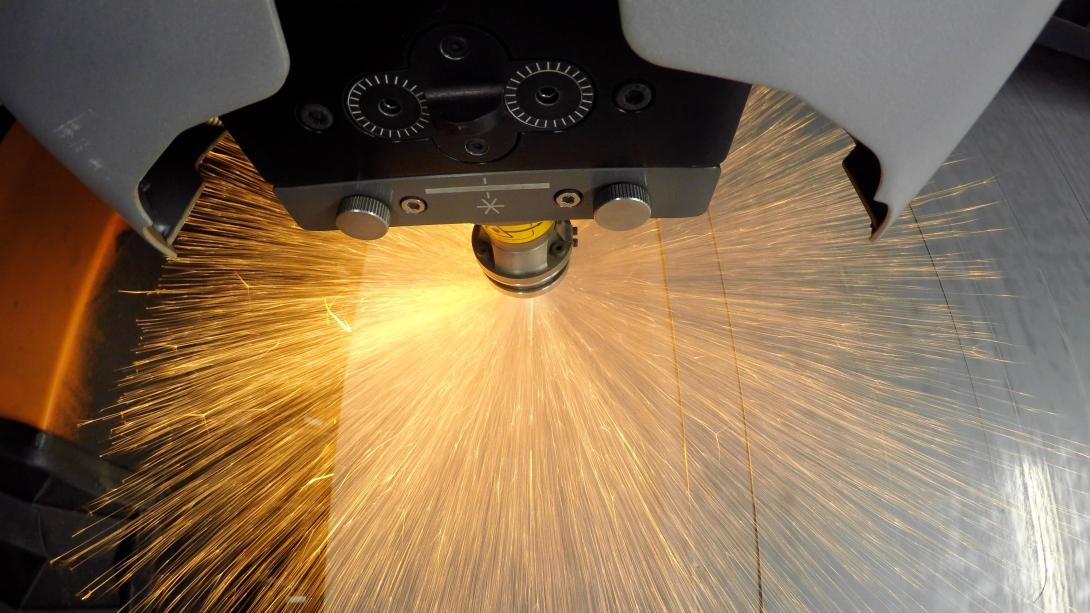
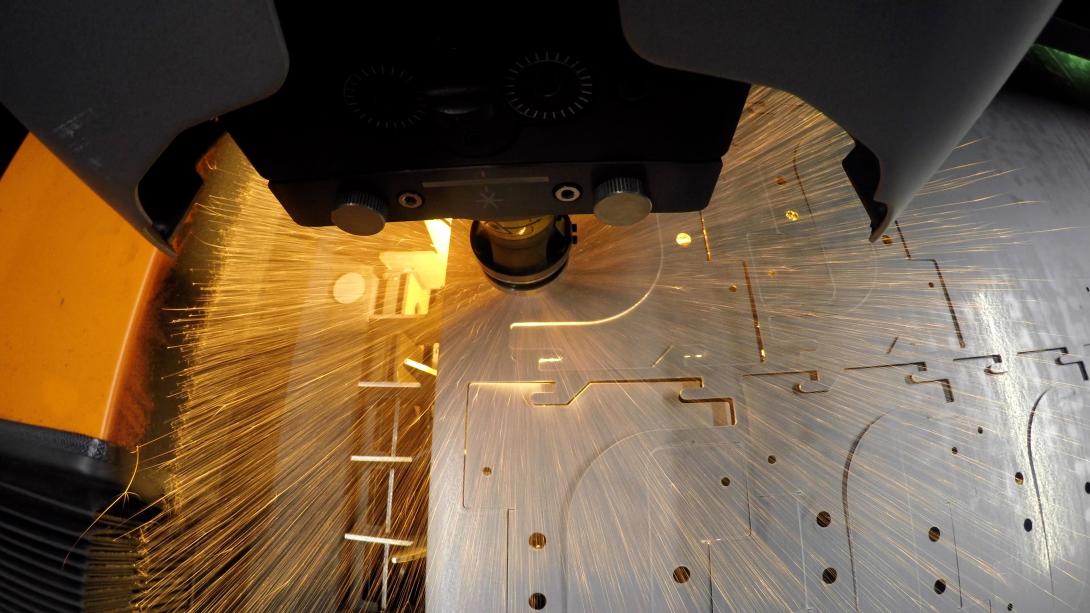
Ett lyckat samarbete
Prima Power, maskindivisionen inom Prima Industrie-koncernen, som specialiserar sig på industriella lasersystem och maskiner för plåtbearbetning, är en internationellt ledande aktör med ett av de största produktutbuden för skärning, klippning, bockning och automatisering. Man har anläggningar i Italien, Finland, USA och Kina samt ett försäljnings- och supportnätverk i över 80 länder, vilket gör företaget till en av de främsta aktörerna i 2D-lasersektorn. Man har ett brett utbud av maskiner för alla områden världen över, med utmärkt prestanda och effektivitet. ”Den nya Laser Genius+ från Prima Power som har en storlek på 1,5 × 3 meter (59 × 118 tum) och levererar 6 kW kan skryta med verkligt avancerad teknik. Några av de funktioner som imponerade mest på oss var systemets höga prestanda, vilket ger mycket mer avancerad skärförmåga än vi var vana vid”, fortsätter han. ”Den här maskinen har en annan dynamik som krävde att vi omstrukturerade vår produktion. Eftersom den arbetar betydligt fortare gjorde den nya Laser Genius+ att vi var tvungna att granska vår produktionsprocess för att kunna hålla jämna steg. Det innebar att vi för vissa delar till och med har fördubblat vår produktionskapacitet.” Systemet arbetar dygnet runt och en av de positiva aspekter som Lucino lyfter fram med Prima Powers nya produkt är den kompakta storleken. Den består i princip av två huvudenheter (maskinen och ett bord för in-/utmatning), vilket gör att allt från installation till vanligt underhåll och rengöring har visat sig gå fort. Tack vare den alternativa och innovativa teknik som används utgör det här systemet en utveckling inom Laser Genius-serien som Prima Power har valt att fokusera på inför framtiden. ”Maskinen är redo att ansluta och köra. Den kan installeras och börja producera på bara två dagar i vilken fabrik som helst”, förklarar Cristiano Porrati, Prima Power Countries Manager South Europe. ”Arkitekturen i Laser Genius+ är helt ny och alla detaljer har optimerats för att öka produktionshastigheten, minska underhållet och höja prestandan. Maskinen består av ett enda block som omfattar laserkällan, kylare, motorer, optik, elektromekaniskt skåp och skärområdet, samt ett andra block som består av in-/utmatningsbordet. När maskinen kommer till fabriken placeras de två blocken ut och man gör elektriska och pneumatiska anslutningar, så att maskinen på kort tid är redo för igångkörning och produktion.” Det innebär också att produktionen inte stoppas under någon längre tid i väntan på att det gamla systemet ska bytas ut mot det nya inom produktionsområden som blir allt mer begränsade. Maskinen kan ha ett komplett gränssnitt för automatisering tack vare att den levereras med system för förvaring, in-/utmatning och sortering av bearbetade detaljer. ”Det är den smartaste och mest sammankopplade maskin som Prima Power någonsin har tillverkat”, förklarar Giulio Amore, Prima Powers 2D Laser Product Manager, ”med nya givare på laserhuvudet och algoritmer för artificiell intelligens för avancerad övervakning och processtyrning.” Visualisering och realtidsrapportering för produktionsprocesserna garanterar fullständig kompatibilitet med Industry 4.0-kriterierna och den kan anslutas till valfritt analyshanteringssystem. ”Det kan man även se genom att den som standard levereras med två 24-tums HD-skärmar”, fortsätter Giulio Amore, ”där den första används för HMI-gränssnittet och den andra visar vad som händer i arbetsområdet. Jag vill även lyfta fram att Laser Genius+ har en symmetrisk och vändbar layout, vilket gör maskinen mer praktisk och flexibel och lättare att placera oavsett plats.”
”Den är smidig och effektiv även när det gäller teknisk support. Prima Power är fortfarande ett företag som i hög grad fokuserar på människor, så vi har ofta kontakt med den tekniker som senare kommer för att sköta underhållet. På så vis är vi säkra på att det finns en förståelse för problemet redan från början, innan arbetet utförs”, avslutar Bertrand Luchino. ”Eftersom alla högteknologiska maskinkomponenter utvecklas och tillverkas av Prima Power, som CNC, lasergenerator och mekanisk struktur, har vi bara kontakt med en enda part som säkerställer att vi har fullständig kontroll över laserprocessen och maximal tillförlitlighet. Redan från början kunde den professionalism och kompetens som kännetecknar ett företag som Prima Power vägleda oss i användningen av systemen. Vi var säkra på att vi alltid gjorde de val som passade våra behov bäst, med vetskapen om att vi alltid kan lita på ett stort utbud av högkvalitativa och konkurrenskraftiga produkter med hög prestanda. Just därför valde vi även Prima Power som leverantör för den nya kantpress som snart kommer ingå i vår maskinpark, närmare bestämt den hydrauliska kantpressen hP 1630, som ska hjälpa oss att bli mer konkurrenskraftiga även inom bockning.”
Den här maskinen har en annan dynamik som krävde att vi omstrukturerade vår produktion. Eftersom den arbetar betydligt fortare gjorde den nya Laser Genius+ att vi var tvungna att granska vår produktionsprocess för att kunna hålla jämna steg. Det innebar att vi för vissa delar till och med har fördubblat vår produktionskapacitet
Vill du ha en liknande lösning till ditt företag? Du hittar den här
Laser Genius+
2D-LASERSKÄRNINGSMASKINER