
Top performance

With over a decade of experience in laser cutting and sheet metal bending, Laserlam constantly looks to new solutions to increase its productivity, such as Prima Power’s new 2D Laser Genius+.
Productivity doubled, advanced processes, high-level Industry 4.0 performance and compact in size, easy to install and service. This is the new 2D Laser Genius+ laser machine, designed and manufactured by Prima Power and now running at Laserlam S.r.l. The machine has just concluded a testing period agreed to by the two companies that aimed to evaluate its full functionality before officially being launched on the market. The test was conducted by the company from Orbassano (TO) because of its significant experience gained over more than a decade of manufacturing. Laserlam was founded in 2008 by its three founding partners, Carlo Ferraro, Bertrand Luchino and Giovanni Luca Davito Gara, professionals with extensive and consolidated experience in the sheet metal sector.
Evolving to keep up with market demands
From a pure contractor focused on laser cutting and bending, Laserlam increased its know-how to provide a complete service, from material selection to welding, and from mechanical processing to thermal treatments, becoming a leader in the market for its product quality. Today the company boasts around 30 employees, across four production areas, who analyze and develop requirements to create an affordable offering that is as accurate and competitive as possible. Production then follows, ending with the delivery of a complete product in short lead times, thanks to its very dynamic production model spread over numerous day shifts and with a number of machines and suppliers available for each individual process. As a result of its investment in research and development, together with partnerships forged over the years, the company from Turin is today able to meet the most varied requirements within the manufacturing sector, guaranteeing high quality products and services, also owing to the ISO 9001:2008 and ISO 14001:2004 certifications it obtained in 2010. “If in 2008 our aim was cutting and bending sheet metal, today our approach looks to cover the entire production cycle, receiving the customer’s design to create a finished product, complete with thermal treatments. We cater to a wide range of companies, from artisans to large automotive manufacturers, and with volumes ranging from a single piece, up to millions of items, averaging 25/30 pieces per order,” explained Giovanni Davito, Sales Manager of Laserlam S.r.l. “Our real strength is that we are able to provide a service that goes beyond the single item: anything that starts from sheet metal and that can be made with a laser and a bending machine is seamlessly managed within very tight deadlines.” This in response to a market that following the 2008/2009 financial crisis has changed face, with dynamics that are very different to those the manufacturing sector was accustomed to. Customers are increasingly demanding a complete service because they do not want to have to manage warehouses or deal with groups of suppliers, preferring a single company capable of providing turnkey solutions. “In this sense, today 80% of businesses provide us with project specs, but we take care of sourcing the materials, which we always have in stock so as to be responsive to the orders received. Keeping in mind that we currently produce around 2,000 new codes a month, it’s easy to appreciate the complexity of the logistics required, with substantial energy and resources dedicated to this,” he added. “In a more general sense, the entire production process is managed by software responsible for generating codes for new products, processing the initial material, nesting and machine operations, detecting production times from an Industry 4.0 point of view. In this way, we can trace every phase leading to the finished product, allowing us to track down all the information we need in the event of any issues.” From a production point of view, Laserlam has two latest generation laser cutting systems, two press brakes (a 40-ton electric press brake and a 250-ton hydraulic one) to which an hP 1630 from Prima Power will soon be added, and seven welding stations, in addition to a series of tooling machines for small contour processing, such as tapping, drilling, tumbling and washing of pieces, all used to complete the customer’s order without increasing delivery times. “To meet the changing needs of the sector, we needed to offer consistently high-quality products while lowering power, gas and compressed air costs, which with our CO2 laser were so high that they were becoming unsustainable. In addition, we needed a laser system to replace our current one that would increase performance thanks to fiber technology,” added Bertrand Luchino, Laserlam’s Production, Quality, Purchasing and Logistics Manager. “Since we had already installed a Platino Fiber laser system by Prima Power that we were very happy with, we decided to accept their offer as they needed to test their new Laser Genius+ within a business that worked very hard with various thicknesses and a wide range of materials.”
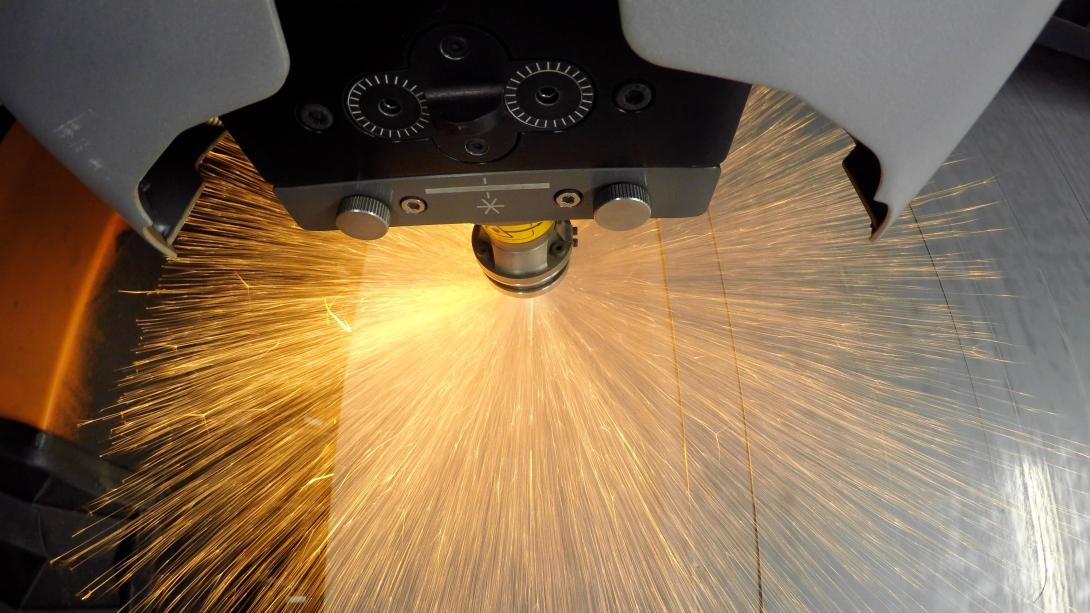
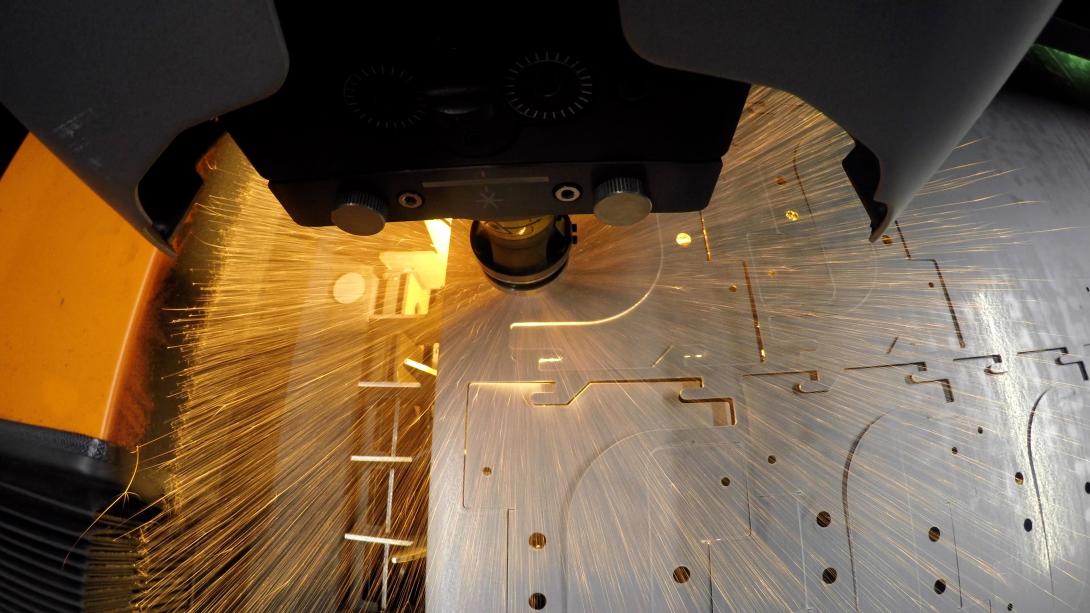
A successful partnership
Prima Power, the Machinery division of the Prima Industrie group, which specializes in industrial laser systems and sheet metal processing machinery, is an international leader with one of the widest offerings that includes cutting, punching, shearing, bending and automation. With plants operating in Italy, Finland, the USA and China, and a sales and support network in over 80 countries, today the company is among the main operators in the 2D laser sector. It offers a wide range of machinery for every field all across the world, with excellent performance and efficiency. “The new Laser Genius+ provided by Prima Power measuring 1.5 x 3 meters (59 x 118 inches) and delivering 6kW boasts truly advanced technology. Among the features that impressed us the most, was the high performance of the system, which offers much more advanced cutting capability than we were used to,” he continued. “The different dynamics of this machine required us to restructure our production. With its significantly reduced timings, the new Laser Genius+ forced us to review our production process to be able to keep up with it, which on certain elements, has even doubled our production capacity.” The system operates 24 hours a day and among the positive aspects highlighted by Luchino regarding Prima Power’s new product is its compact size, essentially consisting of two main units (the machine and a table for loading/unloading), thanks to which installation, as well as ordinary maintenance and cleaning have proved to be quick. Thanks to the alternative and innovative technology used, this system represents an evolution within the Laser Genius line that Prima Power has chosen to focus on going into the future. “The machine is plug&play. In just two days it can be installed and start producing in any factory,” explained Cristiano Porrati, Prima Power Countries Manager South Europe. “The Laser Genius+ architecture is completely new and every detail is optimized to speed up production, reduce maintenance and increase performance. The machine consists of a single block that includes the laser source, chiller, motors, optics, electromechanical cabinet and the cutting area and a second block consisting of the loading/unloading table. Once the machine enters the factory, the two blocks are positioned and the electrical and pneumatic connections made so that within a short space of time the machine is ready for start-up and production.” This also means that production is not stopped for very long while waiting for the old system to be replaced with the new one, within production areas that are becoming more and more restricted. The machine can be fully interfaced for automation since it comes with systems for storage, loading/unloading and sorting of the processed pieces. “It is the smartest and most interconnected machine Prima Power has ever manufactured,” explains Giulio Amore, Prima Power’s 2D Laser Product Manager, “with new sensors on the laser head and artificial intelligence algorithms for advanced monitoring and process control.” Visualization and real time reporting of its production processes guarantees total compatibility with Industry 4.0 criteria and it can be interconnected with any analytical management system. “This is also demonstrated by the fact that it comes standard with two 24” HD monitors,” continues Giulio Amore, “the first one used for the HMI interface and the second shows what is happening inside the working area. Furthermore, I’d like to highlight that Laser Genius+ has a symmetrical and reversible layout, which increases the practicality and flexibility of the machine for better placement in any location.”
“Even in terms of technical support, it is seamless and streamlined. Prima Power is still very much a people-focused company, so we often deal directly with the technician who will later come in for maintenance. In this way we are guaranteed that the problem is understood from the very beginning, before the work is done,” concluded Bertrand Luchino. “Furthermore, since all the high-tech machine components are developed and produced by Prima Power – the CNC, laser generator and mechanical structure – we deal with a single party, who ensures we have total control of the laser process and maximum reliability. Right from the start, the professionalism and skills that are the hallmark of a business like Prima Power guided us in using their systems, with the certainty of always making the right choice to best suit our needs, knowing that we can always count on a wide range of high-quality, competitive and high-performance products. It is exactly for these reasons that we have also chosen Prima Power to supply the new press brake that will soon become part of our machine park, more specifically, the hP 1630 hydraulic press brake, which will help us increase our competitiveness in bending too.”
The different dynamics of this machine required us to restructure our production. With its significantly reduced timings, the new Laser Genius+ forced us to review our production process to be able to keep up with it, which on certain elements, has even doubled our production capacity
Are you looking for a similar solution for your company? Find it here
Laser Genius+
2D LASER CUTTING MACHINES