Prima Power announces the product introduction and availability of the LASERDYNE® 811 - designed to address the next generation of laser processing challenges. The LASERDYNE 811 machine employs the most current hardware and software components for flexible precision laser processing in an affordable compact platform. This combination of workstation, controller, and laser means; cost-effective, high speed, and reliable manufacturing machines for low and high throughput and takes full advantage of fiber laser technology.
The machine has the necessary flexibility and precision to perform optimized laser processing on welding, drilling, cutting, and DED additive manufacturing applications for small to medium-size workpieces. The working envelope is 1100 x 800 x 600 mm (41.5 x 31.5 x 24 inches) for the X, Y, and Z axes, respectively. Each axis has greater than 50 m/min velocity and acceleration of 1.2 g and is optimized for industry-leading floor space efficiency for the work envelope.
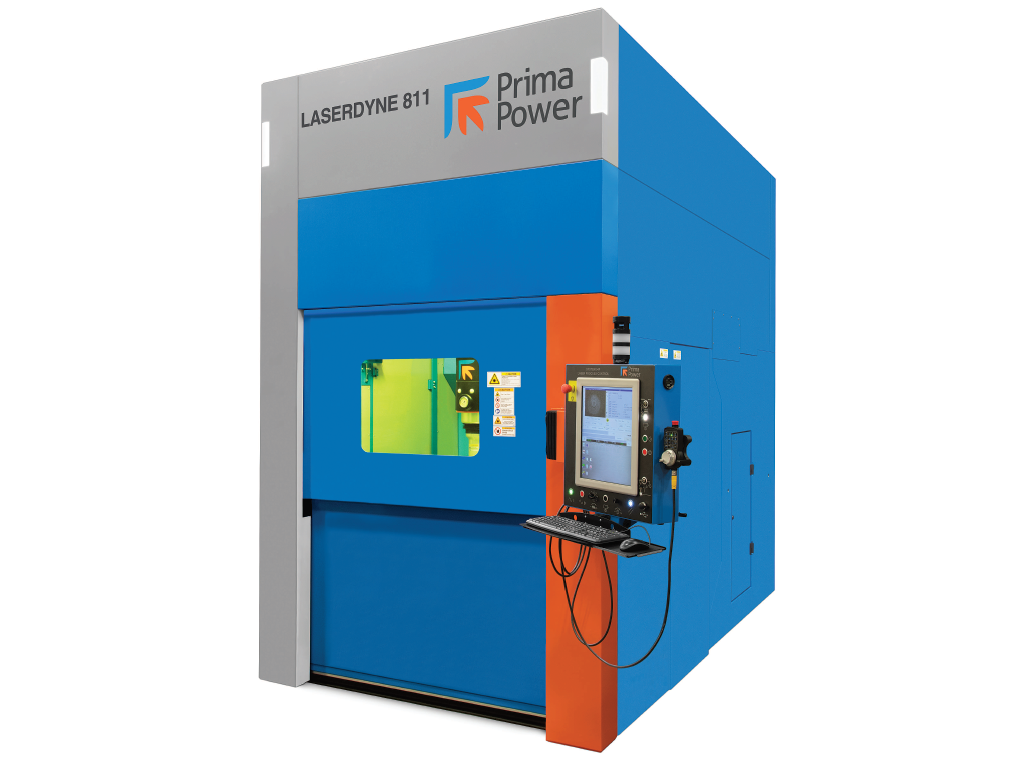
The machine is designed to take full advantage of the BeamDirector®. The additional two axes of motion (C and D) provides access to hard-to-reach places in the workpiece, precise beam placement, and the greatest flexibility in a 5-axis laser system. The BeamDirector has 90 rpm rotational speed and control repeatability of 15 arcsecs. In addition, the BeamDirector supports laser processing from 90° (normal to the surface) to 10° off the surface of a part all the way along the axis of travel.
The S94P CNC provides unprecedented control over the motion system and most importantly, the processing parameters to maximize process quality while providing the most efficient laser processing in the industry. The S94P controller has the ability to provide real-time pulse by pulse control, including, when required, a unique shape for each individual laser pulse. The S94P controller supports seven axes of simultaneous motion and additional axis as required by automation. This means easy integration with a variety of automation solutions for workpiece handling, loading and unloading of components, and other created subassemblies. As with every Prima Power Laserdyne machine, the LASERDYNE 811 has the latest standard software and supports Windows version 10. This includes the full suite of SmartTechniques to optimize the laser process, shorten cycle times while improving the process quality and consistency. As always, software updates are provided without charge.
The LASERDYNE 811 supports Industry 4.0 through the use of MTConnectTM real-time parameter and data streaming along with Prima Power Laserdyne developed SPC process data reporting and storage capability.
FastTrim and Fast Suite II CAD/CAM software support full six-axis interpolation and are options available with the LASERDYNE 811. The CAD/CAM option with the DED Additive manufacturing machine is AMExpress and CAM manufacturing software to produce part programs.
With the BeamDirector and the wide variety of easy-to-use LASERDYNE nozzles, transitions from welding to cutting to drilling and vice versa are performed in a matter of seconds, providing the ultimate solution in machine flexibility.
The LASERDYNE 811 is the most advanced laser processing tool available for 2D and 3D welding, drilling, cutting, and DED additive manufacturing.
Below is information on the four major laser processing categories.
Welding Applications
Welding has always been regarded as a highly-skilled and labor-intensive activity and in many respects it is. An experienced welder knows, one cannot judge the quality of a weld by appearance. The quality of the weld is determined by material and gas interactions during the molten phase and the bonding of the materials during the cooling phase.
LASERDYNE® machines help ensure the delivery of a highly controlled beam and therefore energy to the workpiece. Gas management is critical to the end result and LASERDYNE provides a great variety of nozzle designs, flow control hardware, and software enabling complex geometries to be welded both with and without filler material. This translates to repeatable welding processes and high-quality parts without critical labor skills.
With the growing use of specialty alloys (e.g. boron steel, high strength nickel alloys, chromium alloys, and titanium alloys) new challenges arise because the processing parameter window for these materials may be narrow. With optimal fiber laser parameters, the welding process can be very tightly controlled and previously difficult to weld materials are now routinely welded in manufacturing settings.
The ability to control pulse characteristics and shape the beam has made it possible to weld previously difficult to impossible applications. As an example very thin aluminum, copper, cast iron, high carbon steels, and many other alloys which were considered not weldable using traditional methods. This evolution in welding technology has led to the LASERDYNE Applications Group™ publishing Welding 101 and Welding 102 PDFs that capture the changes in this important process.
Drilling Applications
With the combination of BeamDirector technology a precise laser beam is delivered to the workpiece at angles previously not possible. This precision enables the laser, properly controlled, to the very quickly produce holes in a workpiece through percussion drilling or trepanning. Many Nd:YAG laser and EDM processes have been converted to fiber laser drilling with astonishing results in terms of throughput and quality. Example applications are effusion cooling holes, filtration components, diffusers, and nozzles for land-based and aerospace turbine engines.
Cutting Applications
LASERDYNE machine have provided manufacturing and development engineers with increased design flexibility, often reducing the number of parts and improve the overall quality of the final product. Product designers are familiar with traditional 2D laser part cutting from sheet stock, but were not always familiar with 3D laser processing. Designers are free to use tubes, metal spinning, hydroformed, and deep drawn parts to create better and more cost-effective solutions when using a multi-axis system to trim the part or cut complex shapes that pose a challenge for conventional tooling. Rather than having a complex assembly, designers can consider forming and trimming processes to provide a single more cost-effective part and reduce the secondary operations. Automotive and general manufacturing operations are using laser cutting processes to shorten process cycle times. The combination of reduced tooling costs and flexibility in materials is leading to the rapidly increased use of laser cutting.
DED Additive Manufacturing Applications
The Prima Additive DED manufacturing systems are built based on the process capability and precision of the LASERDYNE platform. The precise and real-time control over the powder deposition, laser power, and shield gas delivery enables the powder to be fused into a wide variety of custom parts or to rebuild metal surfaces, which are then machined to the OEM dimensions and specifications. Worn tools and components can now be rebuilt to extend their service life. Examples of DED additive manufacturing are often parts not easily made by conventional manufacturing processes or parts that are not cost-effectively built using conventional methods. Examples are shaft rebuilds, worn surfaces rebuilds, turbine blade repair, and custom shaped housing/shields.
The LASERDYNE 811 serves as a replacement machine for the discontinued and obsolete LASERDYNE® 780. The LASERDYNE 811 has improved dynamics, accuracy, process control, up-to-date operating systems, and supports a variety of automation options