
Stremet Oy and and the future in growth and partnerships

Stremet oy is a finnish sub-contracting company based in Salo, south-western Finland, with over 25 years of solid experience in its field.
Stremet’s customers include manufacturers of ventilation machines, metal furniture and sauna stoves, but the company also has a lot of seasonal custom productions for numerous and diversified clients. Such versatility is made possible by a wide range of machines, allowing Stremet to make a variety of sheet metal products with sheet thickness up to 20 mm. With the help of professional and skilled staff, the company is able to design and manufacture even more challenging objects. The goal is continuous development and growth, in keeping with corporate values: short delivery time, high reliability and good customer experience.
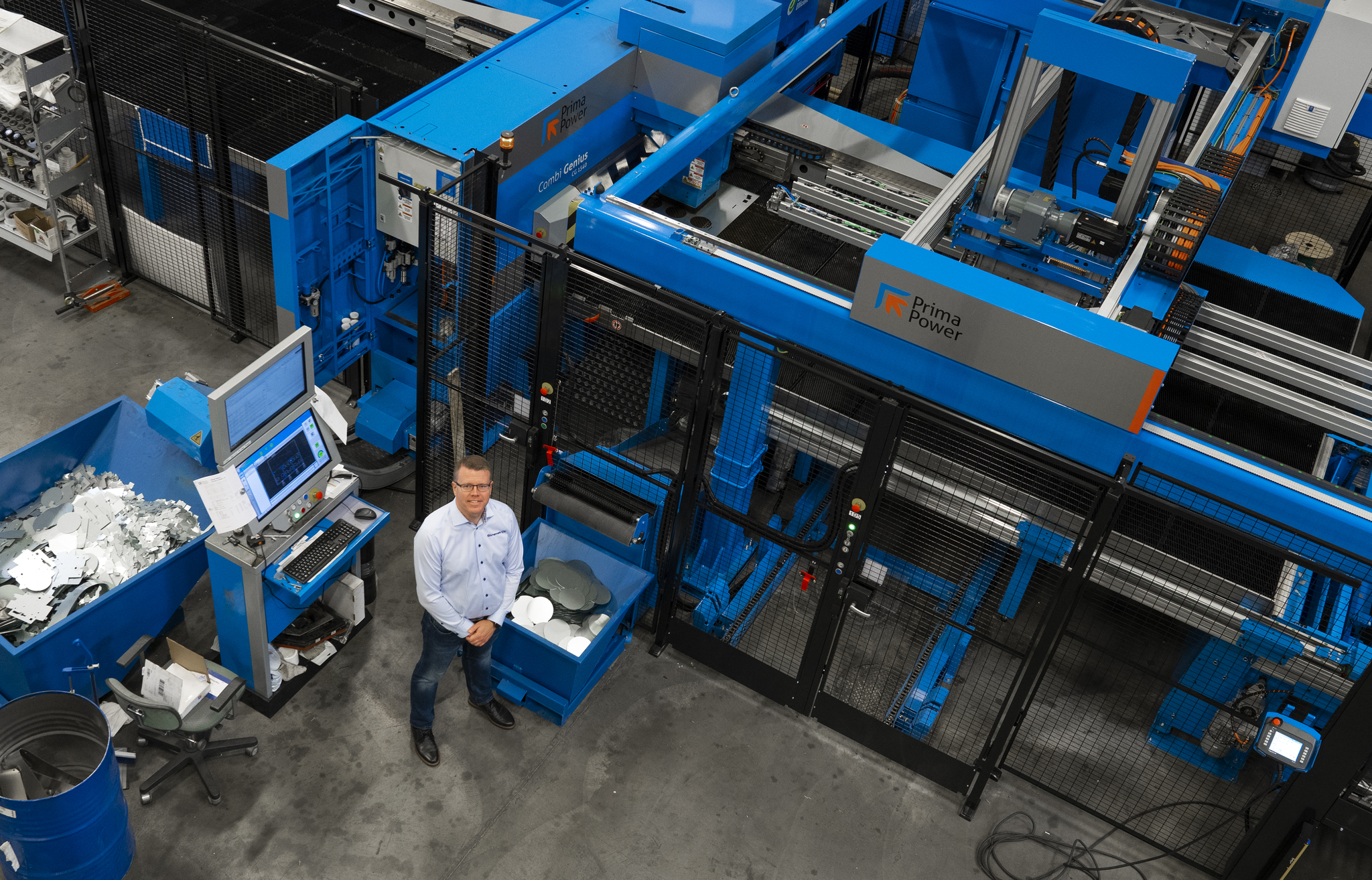
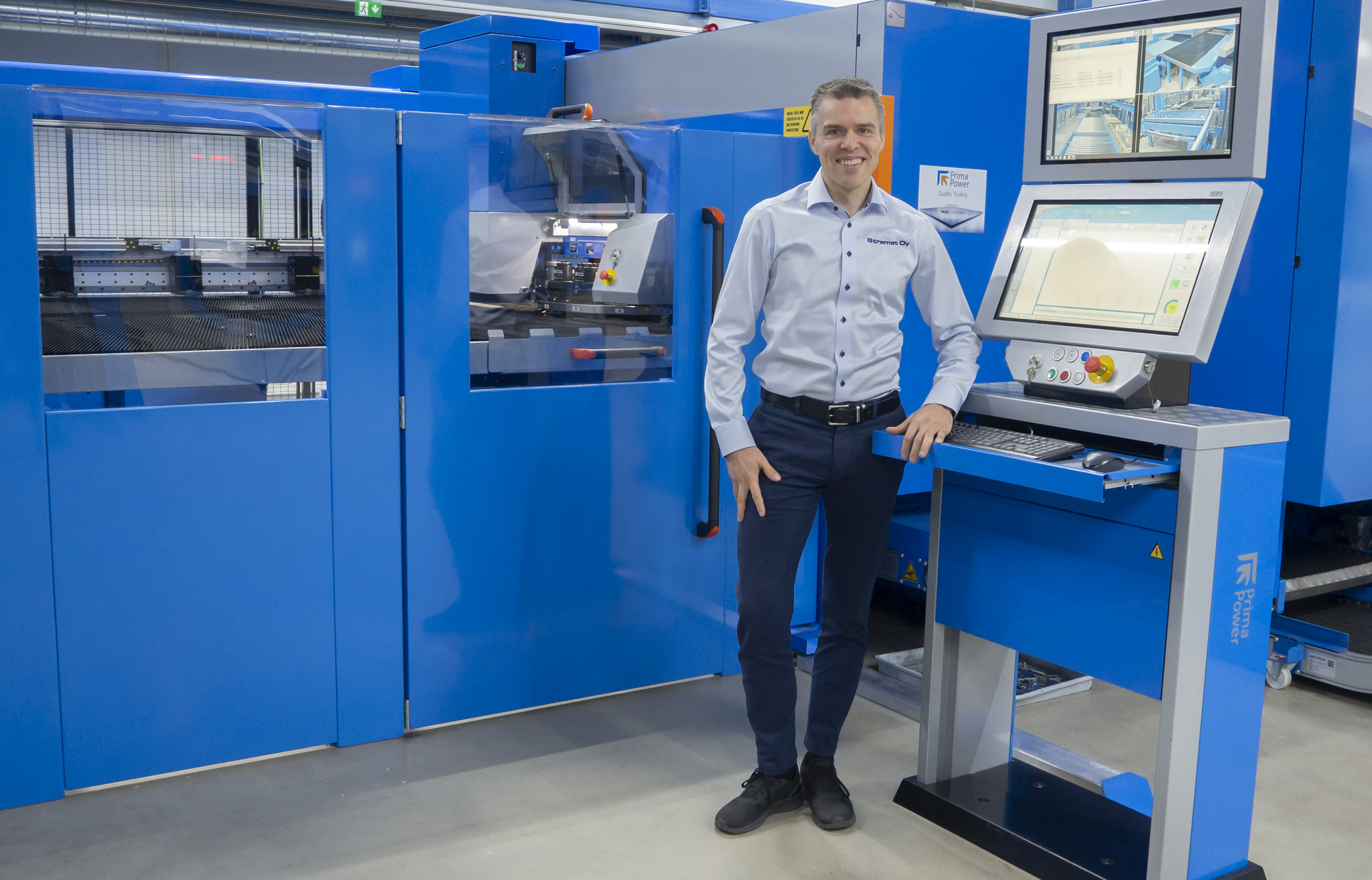
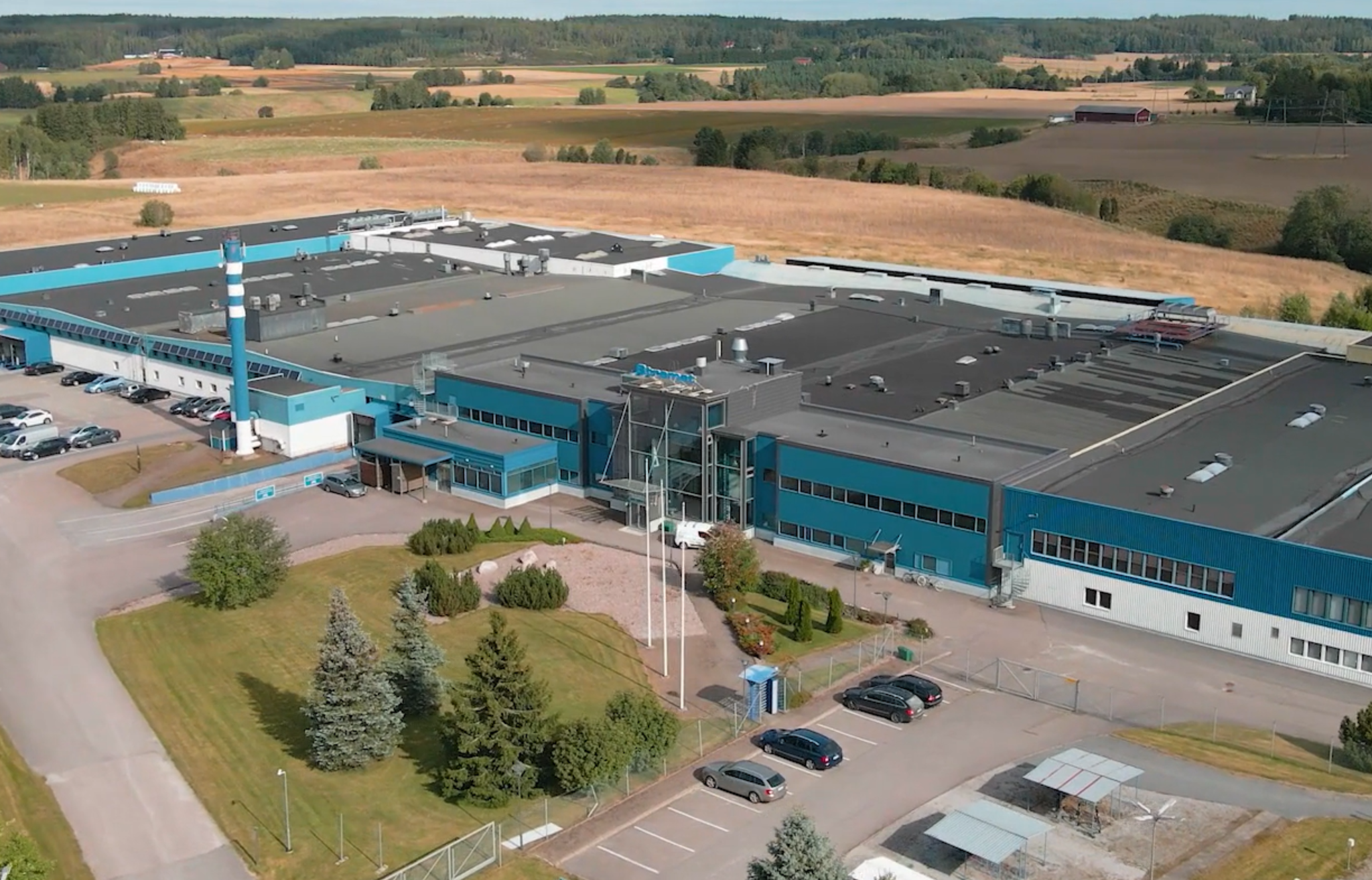
THE BENEFITS OF A LONG PARTNERSHIP
The cooperation with Prima Power began in 1995 when Stremet was founded, and the company bought its first Finn-Power turret punch press. Since then, the company has already purchased about ten more, with six F5 and A5 punching machines still in active operation. The machinery fleet has also been complemented by a Prima Power Shear Brilliance punching and shearing combi machine and BCe Smart automatic panel bender. Since there was a lot of demand among customers for thicker parts as well, the company decided to also invest in a laser machine with automation. The new technology further increased demand, so much that the company made another similar investment shortly after the first one. Thus, the Platino laser machine with automatic storage was soon followed by a Laser Genius, also equipped with automatic storage. In addition, two eP1336 press brakes for the edging of thicker and longer cuts were purchased. In the autumn of 2021, the company invested again in Prima Power’s technology with the purchase of a second semi-automatic BCe Smart bending machine and a Combi Genius machine, which combines punching and laser cutting, as well as two eP press brakes now with a bending width of 2 m. Now the company is able to better meet the demand for diverse parts where manual steps were previously needed. Press brakes were acquired to patch up the bottleneck that had been observed in bending.
Prima Power has been a good and reliable partner for Stremet. “We are fully satisfied with the service received. We have always been offered a solution that is the most suitable for our needs out of many options. Often going above and beyond the technology we had first thought of ourselves,” says Mikko Fiskaali, the CEO and partner of the company. “Over the years, Prima Power has actively suggested to us the best solutions with which we could meet the needs of our customers and develop our production,” confirms Janne Männistö, business director and partner at Stremet Oy.
We have always been offered a solution that is the most suitable for our needs out of many options. Often going above and beyond the technology we had first thought of ourselves.
THE FACTORY OF THE FUTURE
Fiskaali sees the operation of a future factory as a straightforward process in which work stages have been refined into an optimal supply chain using an ERP system. The process starts with the incoming order and ends with invoicing. In the office, digitizing and automating order and image processing as far as possible is an advantage. When physical placement and internal logistics are efficient, the waste of time in production is also minimized by limiting the precious minutes spent on moving parts or searching for tools at the workstation, for example. Workstations should be as close to each other as possible and preferably so that the goods come from one end of the factory and leave from the other end. This way the factory can achieve a good flow efficiency, operations run smoothly and cost efficiency increases. In addition, automating operations such as loading, unloading, sorting and stacking makes things infinitely easier. At Stremet, automation is used in all work steps as much as possible, within the limits allowed by the batch size.
Eliminating waste increases sustainability, workflow and safety at work: features that all customers value more and more.
“I see the factory of the future as a streamlined process with as little time and material waste as possible. Furthermore, eliminating waste using LEAN methods increases sustainability, workflow and safety at work. These three factors are features that all customers value more and more. When production waste is minimal, flow efficiency high, work smooth, operation sustainable and occupational safety at high level, the subcontracting company that controls these processes will likely place orders with high delivery reliability, good customer satisfaction and a strong overall result. This is a process we develop at Stremet with improvements every day,” says Fiskaali.
In the future, more and more versatility will be required from subcontractors.
Today, customers want the strongest possible capabilities under one roof. In the future, more and more versatility will be required from subcontractors. Stremet’s goal is therefore to develop the 22,000-m2 property to be as diversified as possible. “We are already thinking about moving the paint shop to the same property, as well as finding a tube laser company, a welding company and a design agency as tenants. The goal is to have a so-called smart hub in Salo: a subcontracting factory that provides everything that can be manufactured and processed from metal,” Fiskaali adds.
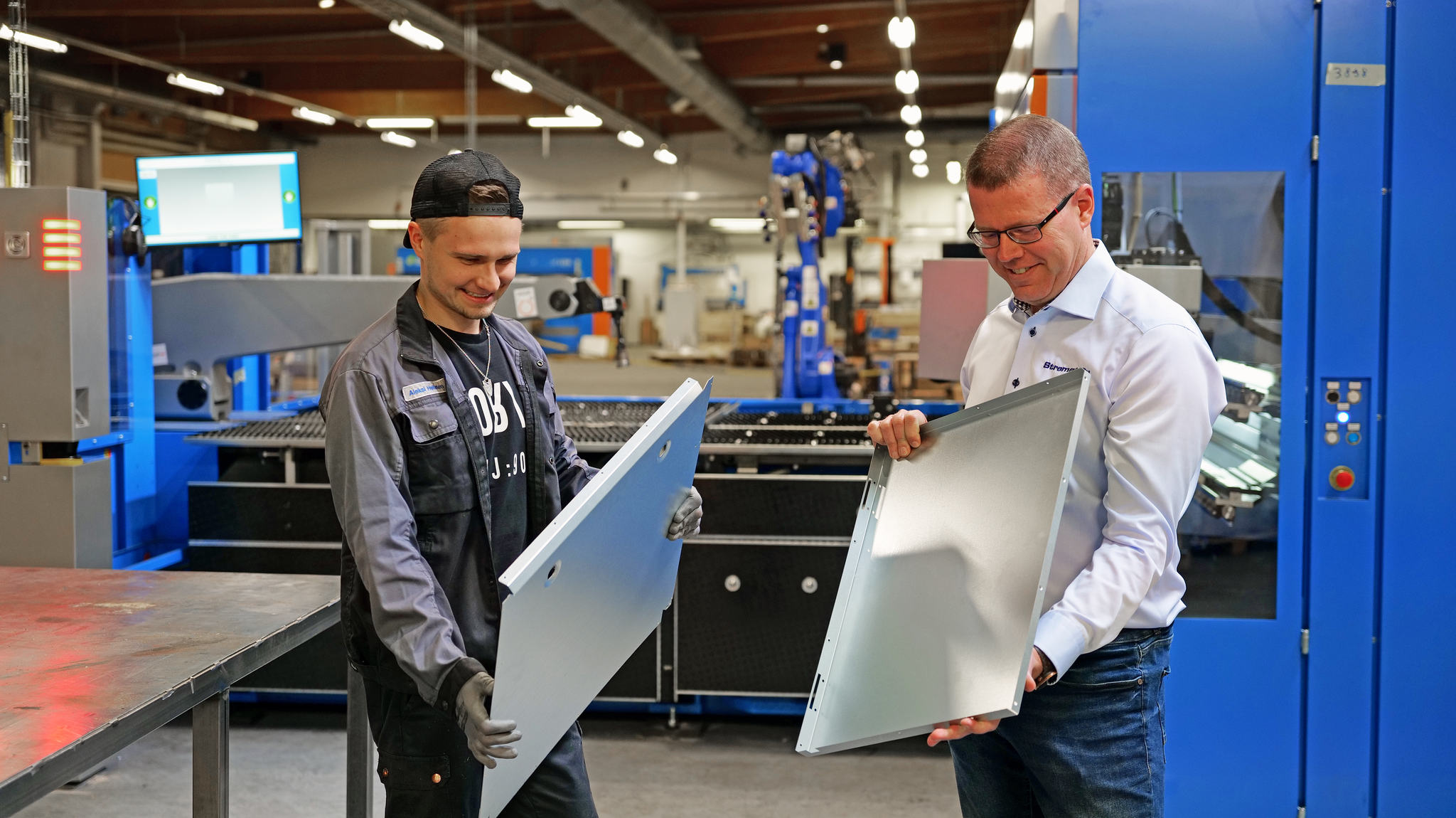
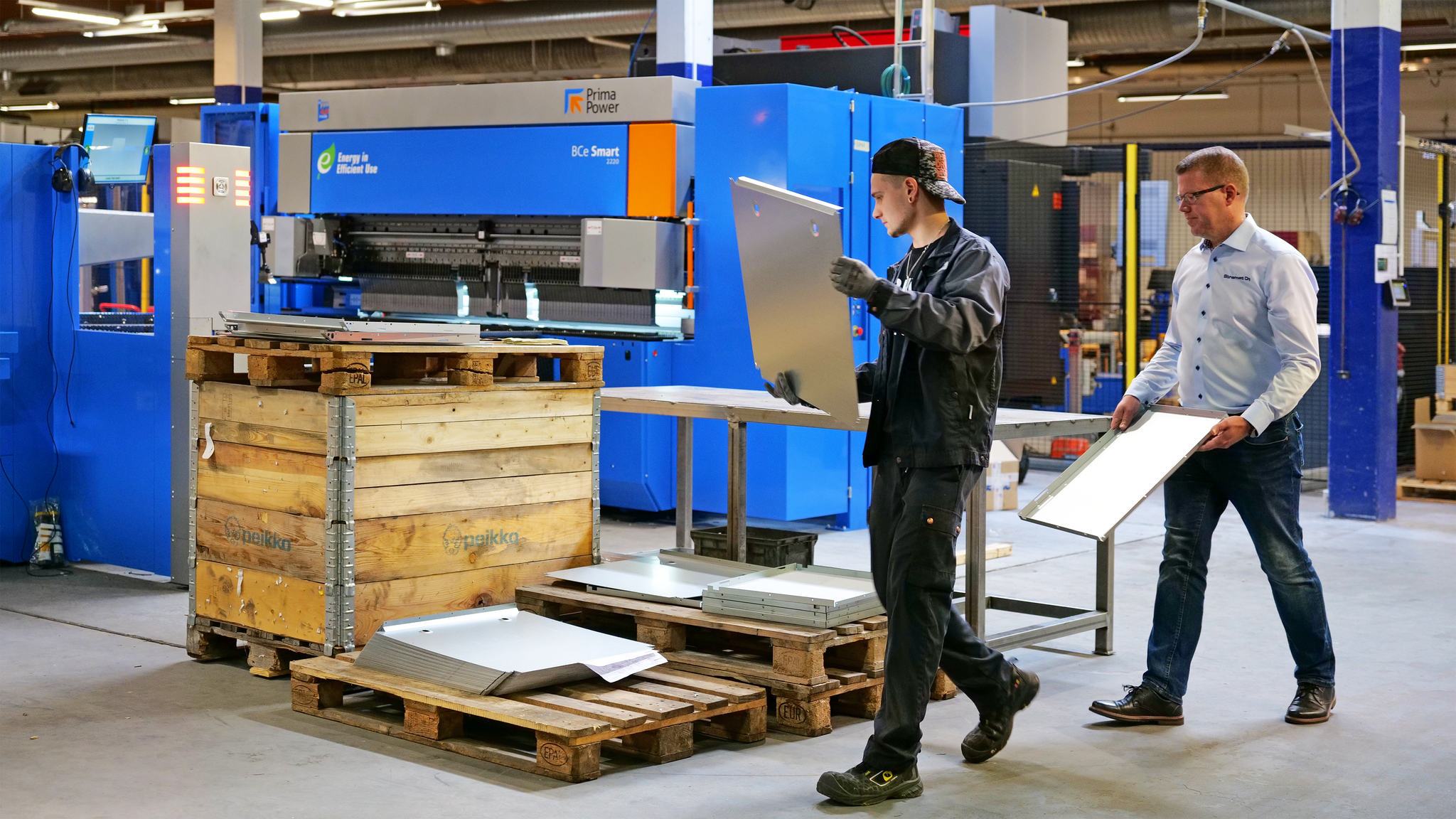
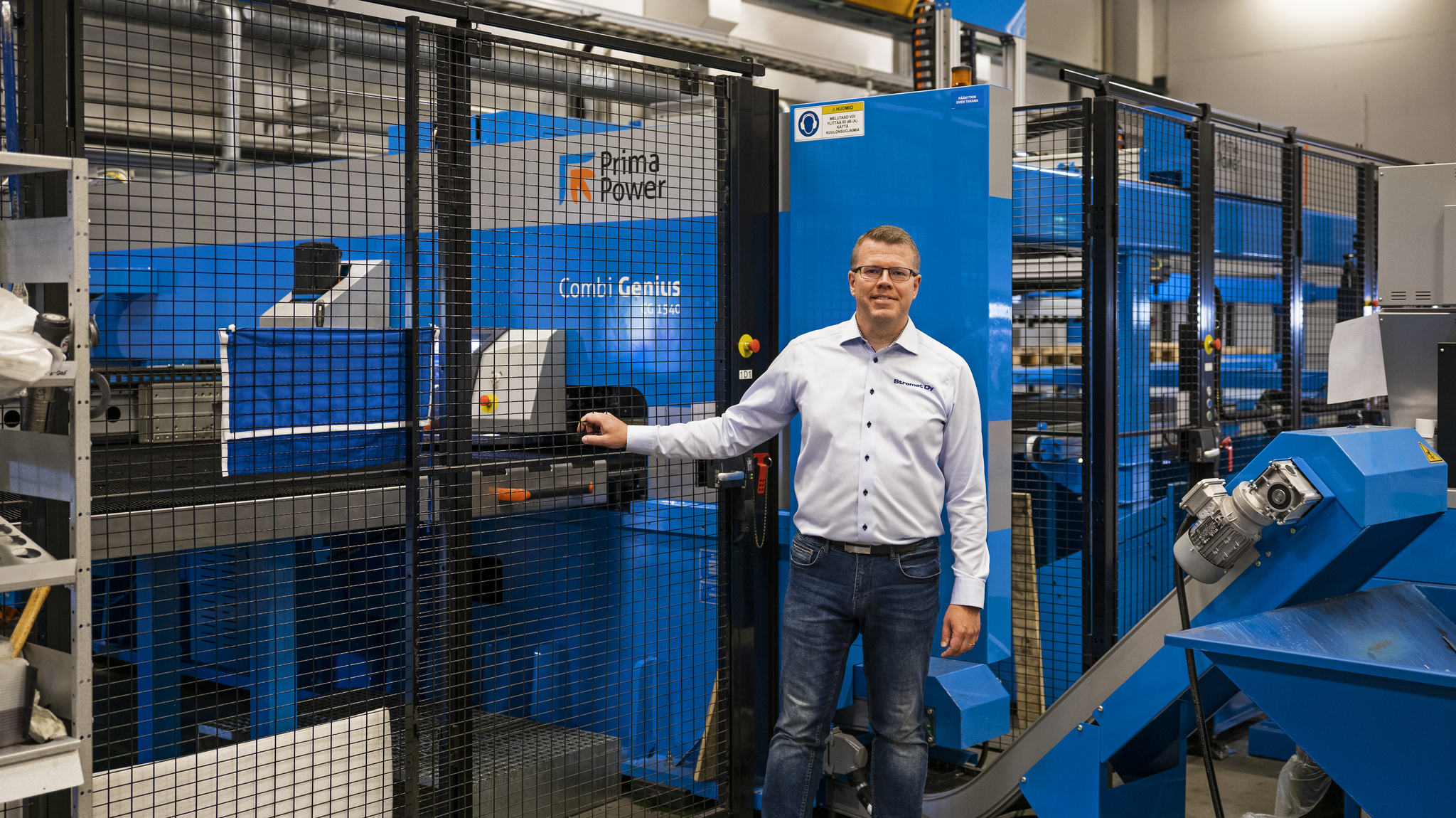
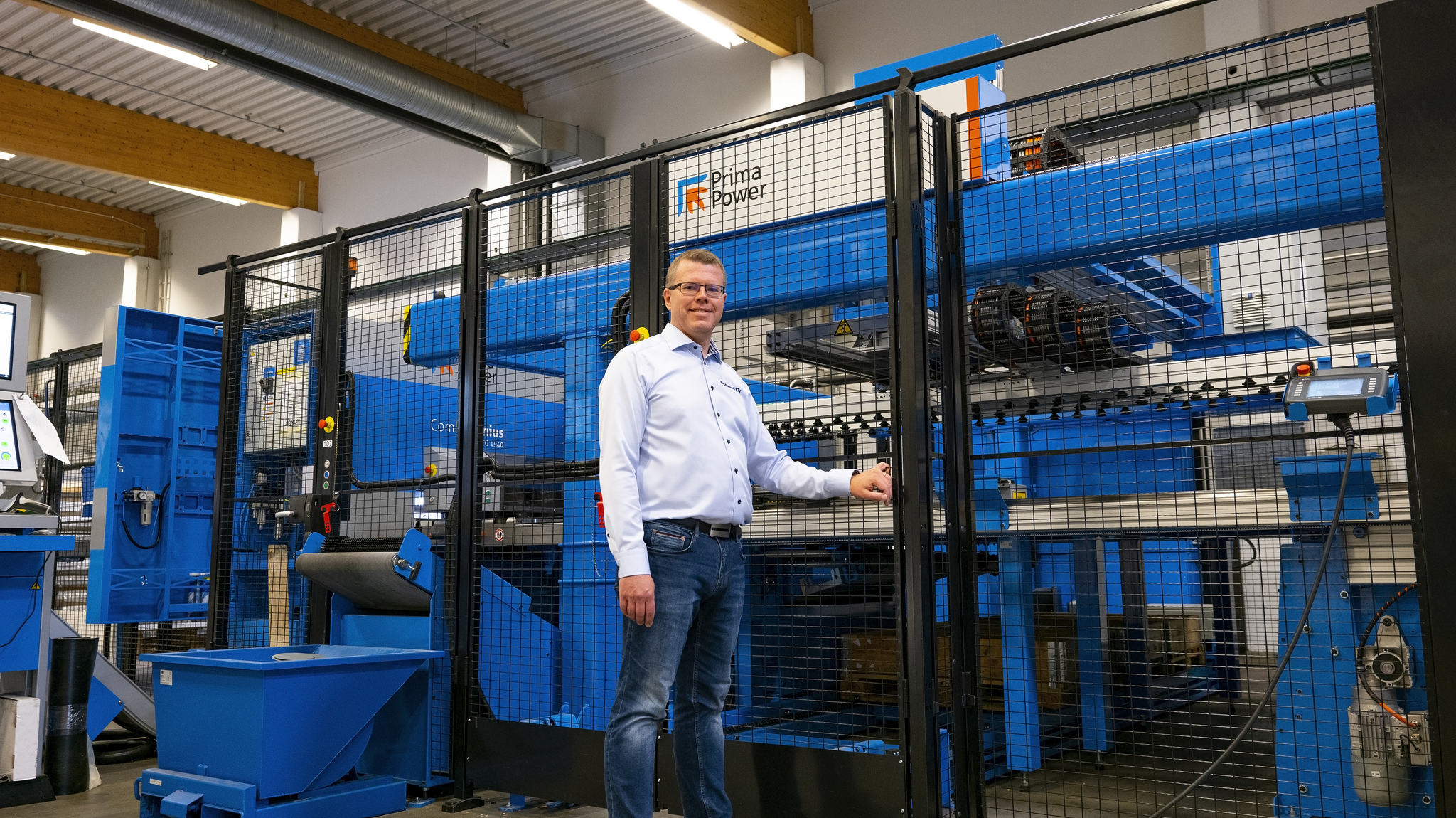
THE FUTURE IS SUSTAINABLE
Sustainable development is an important value that is growing in relevance all the time. It is not only a crucial issue in and of itself, but also an argument with measurable economic impacts. On top of this, people are becoming more aware of sustainability and are demanding companies make an effort in this direction. Stremet wants to be involved in areas that tackle climate change and invest in environmentally friendly energy production as well as in lowcarbon construction. These are the megatrends of the moment, and the lifeblood of the future.
Furthermore, the company is well aware that impact must be assessed in financial and environmental as well as in social terms. After all, the factory’s most valuable asset are its employees and, in a context of intense competition to hire the most skilled workers, Stremet wants to hold on to competent people. “We strive to make Stremet a nice company where work is enjoyable. We invest in our corporate image and hope that it will also influence people. We want to make tasks as pleasant as possible, for example by eliminating heavy work stages through automation and robotics, as well as implementing work rotation and training staff. Every employee is genuinely valuable and that is reflected in our corporate culture,” Fiskaali says.
Within this framework of sustainability, the company is able to set for itself strong and strategic goals for development and growth: the revenue growth target is 20% for next year, with a long-term aim to double the current turnover of around €12 M. “Our goal is to increase the company’s recognition: in the long term, we want to be Finland’s most sought-after subcontracting partner in the sheet metal industry,” concludes Fiskaali.
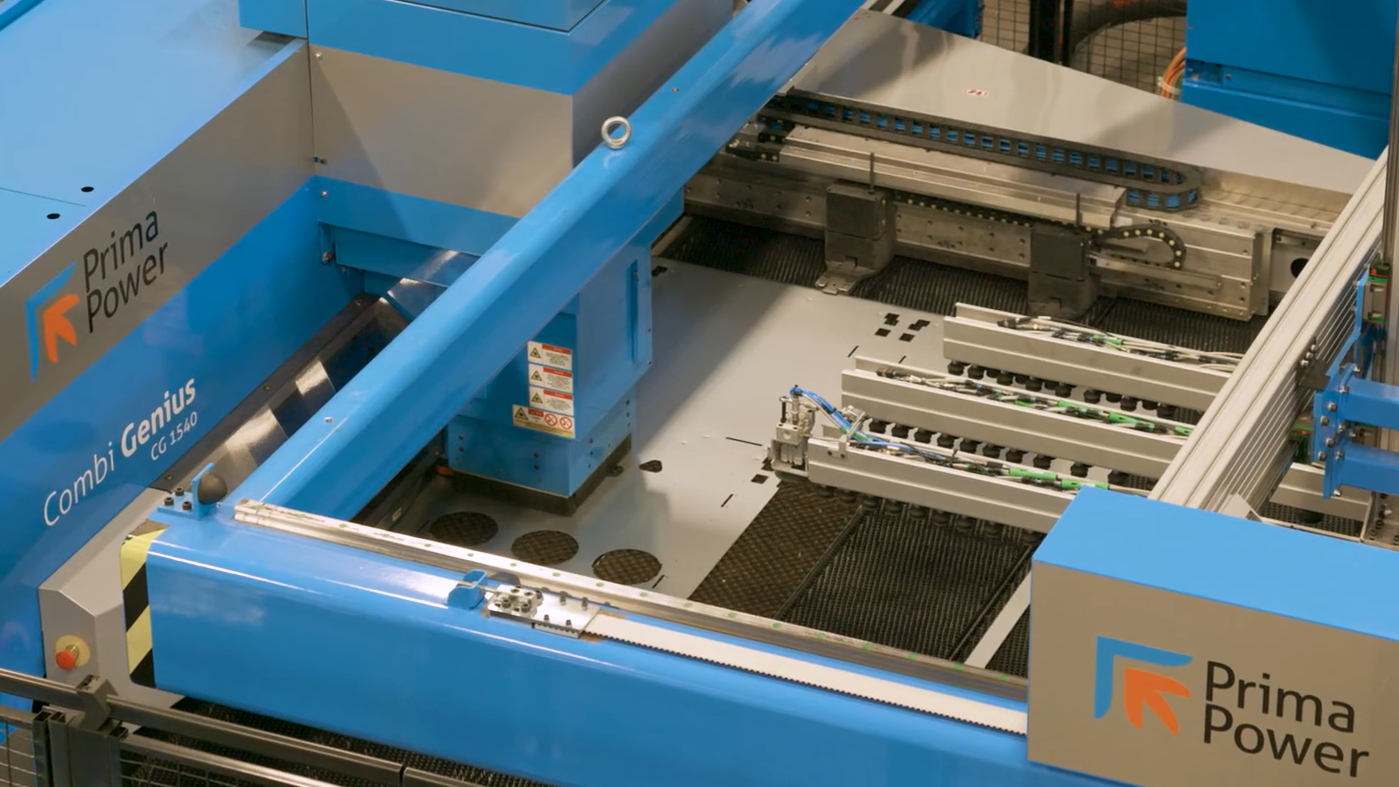
Sustainable development is an important value that is growing in relevance all the time. It is not only a crucial issue in and of itself, but also an argument with measurable economic impacts.
Read this and many other stories on the last issue of our Power Line magazine.
We are fully satisfied with the service received. We have always been offered a solution that is the most suitable for our needs out of many options. Often going above and beyond the technology we had first thought of ourselves.